Don’t let failing wiper blades, arms or motors put you in danger.
A great fastball pitcher will tell you his secret is “they can’t hit what they can’t see.”
But in a truck you can hit what you can’t see. And it can hit you.
A clean windshield is critical in any weather but more so in wet and stormy weather when you need a clear view of the road even more than usual. But you can’t keep your windshield clean if your wiper blades, arms and motor aren’t in good working order.
We visited Kenworth of Pennsylvania in Kutztown, Pa., to get the advice and help of service manager Terry Meitzler. He showed us the simple process of wiper blade and arm replacement, jobs most truckers could perform easily. He also demonstrated wiper motor replacement on a 2004 Kenworth W900L, a job well within the capabilities of most truckers with a little experience in doing mechanical work. (We have used this model as an example. Work on your model may be different. Consult your owner’s manual or a mechanic.)
The location of the wiper mechanism high on the cowl of the truck demands a solid place to stand when you work. Use a good stepladder and follow sensible safety rules as you work.
Using the ladder is much safer than trying to stand on the frame rails or engine parts. Always use the ladder to get up and then check to make sure your footing is secure before stepping off the ladder.
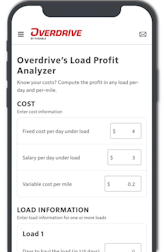
Replacing the blades
Wiper blades are made of soft rubber, and truckers know that soft rubber quickly gets brittle and may crack. The result is pools of water on the glass that block your view.
Fortunately, if still new, poor performance may be caused only by accumulated grit along their edges. This keeps the soft but sharp rubber edge from contacting the glass the way it should. A careful wiping with a wet paper towel is often all that’s needed to restore performance. If grit is determined to stay, you may need to use mild detergent and water to get them clean. In this case, rinse them thoroughly to keep the windshield from developing a soap film.
Indications of worn wiper blades include a loss of pliability. This hardness may show up as edges that are permanently bent over, meaning they clear effectively only in one direction, especially after a long dry spell. Other symptoms include worn, uneven, feathered edges that produce streaks of water on the glass.
Fortunately, once the blades have lost their pliability or sharp, even edges, they are easy to replace.
The wiper arms should allow you to easily pull and retain the wipers off the windshield for service. Just gently pull them away from the windshield, and then insert a 1/8-inch drill bit into the hole in the side of the arm. When you release the arm, it will be locked 6-8 inches away from the windshield.
The blade itself consists of a flat, rubber insert with metal edges on either side incorporating a locking mechanism at the outboard end. To remove the insert, just use a pair of needle-nose pliers to squeeze together the metal edges at the indentations on the outer end. This will unlock the blade, allowing you to slide it out of the claws that hold it in several locations across the blade retainer. Slide the new blade insert into the outboard retaining claw with the insert turned so the locking grooves will go in last. Feed it carefully into each of the retaining claws across the blade retainer and then slide it in until the indentations at the outer end lock on the outboard claw. Pull the arm outward slightly and remove the drill bit, then release it.
Arm replacement
Wiper arms can sometimes get bent due to various kinds of road abuse, requiring replacement. They may also exhibit limited spring tension, causing the blade to fail to ride consistently against the glass. Also, wiper arms are sometimes replaced in order to use a different type of wiper blade and retainer.
Arm replacement is simple, but you have to be careful to restore the original alignment.
- Run a piece of chalk or crayon along the upper edge of the blade where it rests on the windshield.
- Pull the arm away from the windshield and install a 1/8-inch drill bit into the hole to lock the arm away from the windshield. Then install a socket wrench onto the acorn nut. Hold the arm with your other hand to prevent all the torque from being transmitted to the wiper linkage, and loosen the nut. Finally, remove the nut and washer.
- Carefully slide the arm off the splines and remove it.
- Install the drill bit to lock the new arm in the withdrawn position.
- If necessary, transfer the old blade and retainer to the new arm.
- Slide the end of the arm just over the end of the linkage driveshaft and then rotate the arm to align the blade properly with the mark on the windshield. Once it looks like it’s at the right angle, slide the arm onto the driveshaft splines. Remove the drill bit to release the arm and then check alignment. If necessary, reinstall the drill bit; then pull the arm off and turn it in either direction, and reinstall it to get the alignment right.
- Install the washer and then start the acorn nut onto the linkage driveshaft. Tighten the nut with a socket wrench while holding the arm against the torque with your other hand. Remove the drill bit.
Wiper motor replacement
After many miles, a wiper motor may fail, sometimes on only the speed you have used the most. But, before replacing a motor, make sure that’s actually the problem, as a failed fuse, switch or wiring could also stop it. A bad switch or certain wiring problems could also make the motor stop on only one speed. If the motor won’t work at all, always check for a blown fuse first and replace the one for the wiper circuit if it’s open before going further.
If you’re adept at electrical troubleshooting, you could test with a voltmeter for voltage on the appropriate prong of the motor electrical connector at each motor speed position of the switch. The best way to do this is with a factory wiring diagram showing which prong should be hot in each switch position. If you have voltage there, make sure any ground wires or ground connections on the motor are also in good condition before condemning the motor itself.
Since wiring on modern trucks with multi-speed wiper motors can be exotic, you may want to just take the truck to a dealer or repair shop and have them test the system to make sure you have a bad motor. This shouldn’t cost you a lot of money.
Unlike troubleshooting, replacing the motor is fairly straightforward for anyone who can use simple tools. You’ll need a secure stepladder, a set of Phillips head and regular screwdrivers, and a set of small socket wrenches. It would be ideal to have a small, inch-pound torque wrench to make sure you have the fasteners tightened just right, though this isn’t absolutely necessary. When replacing the motor on the W900L, the factory recommends Loctite 242 to hold some of the fasteners. Use a quality thread-locking compound like this to help motor mounting fasteners stay tight.
The W900L is a single wiper motor mounted near the passenger side of the truck, just under the windshield and forward of the cowl. The motor operates both wipers through a complex linkage that needs to be disconnected, but not removed, to replace it. The motor is mounted to its own bracket, which is attached to a bracket mounting the linkage to the cowl.
- Release and open the hood. Place your stepladder close to the cowl on the right (passenger) side of the truck.
- If the wiper motor will turn in any speed, turn on the ignition and operate it to put the wipers in the parked position. This will make it easier to align the motor’s crank, which needs to be moved from the old motor to the new one. Turn the ignition back off.
- There is a black cowl shield, actually a water collection tray, located along the front of the cowl at the top. Unplug the two windshield washer hose connections where they run through this.
- Remove the five Phillips head screws and two bolts that fasten this shield to the top of the cowl, and remove it.
- Disconnect the two wiring connectors leading to the motor under where the shield was mounted.
- There is a black, metal crossbar running across the cowl below the windshield. Both the motor bracket and the linkage are mounted to this. Disconnect the motor bracket from the crossbar by removing the two bolts attaching it to the front surface, located to the left (driver’s side) of the wiper shaft, and the one bolt attaching it to the outboard surface of the crossbar, all the way on the right (passenger side) of the vehicle. The motor and bracket will now sit on top of the linkage it drives.
- Carefully remove the C-clip that fastens the linkage to the shaft on the end of the motor crank. The clip sits in a groove in the end of this shaft, which drives the linkage. Don’t just start prying on the clip, or you will be likely to drop it. Carefully hold onto the clip with the thumb and finger of one hand while carefully prying it off the shaft with a screwdriver held in the other hand. Place the clip in a secure place, like the lid of a jar, so you won’t lose it. Now remove the bellow-type grease seal (noting which direction it faces in) and washer from the shaft and place them with the clip.
- Slide the linkage off the motor shaft, moving the motor slightly toward the cowl as necessary. Remove the remaining washer and grease seal (noting direction) from the shaft and place them with the C-clip and other parts.
- Remove the bolt located below the windshield, which holds the left (passenger) side of the crossbar to that section of the cowl. Then, using a socket wrench and long extension, loosen the one remaining bolt holding the crossbar to the inner surface of the cowl. Leave the bolt attached by a couple of threads and remove the socket. Now reach in and turn and remove the bolt.
- The crossbar can now be gently forced down for clearance to remove the motor and bracket. Do this and then pull the motor and bracket out.
- The new motor has been run and put in the park position before shipping. Carefully note and mark the position of the crank on the old motor and bracket.
- The illustration shows the old and new motors. The old motor is still attached to the bracket by its three mounting bolts. The new motor is on the right, and you can see the three mounting holes. Note the exact angle of the crank lever on the old motor and mark this angle on the new motor. Note the installation angle of the motor in the bracket, too, so you can install it in the same position.
- Remove the nut from the end of the crank lever, and slide it off the motor shaft. Remove the three mounting bolts from the bracket, and remove the motor.
- With the Loctite 242 or a similar thread-locking compound, coat the threads of the new bolts supplied with the new motor. Then position the motor at the same angle as the first one was in the bracket and install the bolts. If you have an inch-pound torque wrench, torque the bolts to 60-70 inch-pounds.
- You’ll note that the angle of the shaft on the new motor is marked with green paint to show the parked position. Now install the crank lever over the splines at the same angle as on the other motor. Then install the flanged locknut onto the motor shaft. Hold the crank lever in position so it won’t turn while torquing the nut to 200 inch-pounds. If the crank arm is installed at the same angle, it will be aligned with the link connecting the motor and linkage when installed.
- Gently force the crossbar down for clearance, and then maneuver the motor and bracket in above it, under the windshield so it can be mounted to the crossbar.
- Before mounting the motor and bracket, you’ll need to reconnect the linkage to the crank arm. Install the bellow-type grease seal (in the right direction) first and then the washer. Then place the hole in the end of the connecting link over the shaft on the crank arm and force the shaft through it. This will require maneuvering the motor and bracket first toward the cowl as you center the hole over the shaft and then back toward you as you slide the link onto the shaft. Once the link is on, install the second spacer, the outer grease bellow and the clip. Position the clip in the groove in the shaft. Hold it in position with the fingers of one hand while forcing it on with pliers held in the other hand. Position one of the plier jaws on the opposite side of the shaft to get enough force to make the clip go on.
- Install the bolt (and washer) that fastens the crossbar directly under the windshield. Position the crossbar so the holes line up, and install the bolt and washer and tighten it. Next, install the bolt (with its washer) that fastens the crossbar to the cowl, in underneath. If you can’t reach in with the bolt in your fingers to start the threads, you may be able to install it this way: Push the bolt head all the way into the socket, holding the socket at an upward angle so the bolt won’t fall out, then maneuver the bolt into position, holding onto the socket extension. Once the threads are started, tighten the bolt all the way.
- Put the motor bracket in its final position, aligning the holes in it with those in the front and side of the crossbar. Install and tighten the two mounting bolts on the front and the one on the side.
- Reconnect the two wiring connectors. Turn on the ignition switch and test the motor to make sure it works in every speed position.
- Align the rubber gaskets just behind the cowl metal, and reinstall the cowl shield with its five Phillips head mounting screws and one bolt at either end.
- Pass the windshield washer hoses through this shield, and reconnect them. Your installation is now complete.
For further information, contact:
Kenworth Truck Co.
(425) 828-5000
www.kenworth.com
Kenworth of Pennsylvania
(610) 285-6516
www.kwofpa.com
Loctite
(800) 562-8483
www.loctite.com