Your brake system has powerful allies and equally powerful adversaries. Its worst enemy is moisture, while the air dryer is its best friend.
Water is always forming inside your air brake system. The water vapor in outside air turns to liquid because of the pressure (90-120 psi). There’s also oil from the air compressor. The brake system uses the engine’s oil for lubrication, and some of that lube oil goes by the compressor’s piston rings and into the air headed for the wet air storage tank.
Unless separated from the air stream, the water lays in the air brake system tanks and piping and combines with the oil to form a light brown emulsion. Fred Hoffman, engineering manager for air dryers at Bendix Commercial Vehicle Systems, says, “The system is designed for air and not liquid. The air dryer protects the whole system. ABS valves, relay valves and suspension leveling valves – anything that’s lubricated is especially vulnerable.” Leslie Kern, heavy-duty product manager at Chicago Rawhide, agrees, saying, “ABS valves will not function properly if there is moisture present. So air dryer maintenance is more important now than it was before the advent of ABS.”
The emulsion can clog and corrode those brake system valves or even air lines, leading to expensive maintenance, even a serious brake problem while you’re driving. In winter, it can also freeze – usually in the small orifices of a relay or ABS valve or at a bend or low point in an air line.
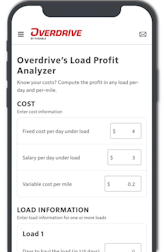
Installing and maintaining a good air dryer prevents such trouble because it gets the moisture and oil out of the air stream before it reaches any of the working parts.
Routine maintenance
The dryer’s internal workings could last forever if oil contamination didn’t eventually work its way though the separator and keep the beads from grabbing water the way they should. The desiccant bed and oil separator have a limited life – normally about one to three years, though in ideal applications it may be longer. Because of this, both are assembled into the dryer together as a replaceable cartridge. The most important single part of dryer maintenance is replacing that cartridge at the right time. As with almost everything in trucking, the duty cycle of the truck greatly affects cartridge life. Brake air system maintenance also plays a big role because leaks mean the compressor handles more air, meaning more water for the dryer to take out.
The most basic air dryer maintenance is to drain the wet tank and primary and secondary storage tanks periodically. This, says Larry Donaldson of the Bendix Tech Team, serves as a check of dryer function and should be done at least every 25,000 miles, 400 hours or three months, whichever comes first. Jon Canale, a senior project engineer at MeritorWABCO, says it’s smart to do this as often as once a week.
If the dryer is the right one for the application and the air system is in reasonable condition, a lot of moisture in the tank (normally mixed with some oil) means it’s time to replace the cartridge. “It’s normal to see a tan-colored goo in the air stream that some describe as ‘mayonnaise,'” Canale says. “Some is normal, but you should not have much if the dryer is working properly. You’ll just see a little mix in the initial blast of air.” In ideal applications, there won’t be any.
When you drain air tanks, you don’t have to empty them. “Just pull the cord and hold open for a few seconds so you can see what comes out,” Canale says. Completely draining the tanks interferes with dryer performance, putting some water downstream till things stabilize.
You should examine the cartridge if you see oil accumulating around the purge valve and just below the exhaust port, Canale says. Heavy evidence of oil there can be a sign of an incorrect dryer installation that has allowed heat to build up. The Meritor WABCO tape “System Saver Series Single Cartridge Air Dryers” says you may actually find the turbo cutoff valve to have a hole burned right through the center. The dryer purge valve may also
fail, and the valve failures will often be accompanied by oil downstream of the dryer as well as frequent cycling of the air compressor. Check the length of the air line from compressor to dryer “to make sure it’s cooling the air properly,” says Canale. The length with newer, cooler running compressors can be as short as 6 feet, but on older trucks, especially in vocational applications, it should be longer – as long as 12 feet. Check the manual for the correct specification, and make sure the line is neither too short nor too long. Also inspect carefully for “dips or loops,” which are bad news and need to be straightened out. There should be a continuous, gentle downhill slope so moisture and freezing won’t block the line.
If there is also oil in the air tanks and bottom of the dryer, your cartridge definitely isn’t working the way it should be. The cartridge is saturated with oil, and it’s passing right through. If the problem crops up after months of satisfactory operation, change the cartridge.
Leslie Kern says CR air dryers should have the cartridge replaced every three years in linehaul service, two years in inner city and every year in refuse and off-highway applications, where air usage is highest. CR sells its cartridges as part of service kits that also include the turbo cutoff valve and purge valve and recommends you replace all three at once.
Replacing the cartridge
Replacing the cartridge is normally straightforward, but the actual procedure varies widely with the construction of the dryer. Regardless, the first step is to drain all air from the system so it will be safe to begin disassembling parts that normally hold pressure. On the Bendix AD-9 air dryer, one of the workhorses of the industry, you must remove eight bolts (two of which fasten the unit in place) so the outer shell can be lifted off the base. Then unscrew the cartridge with a strap wrench, change its two O-rings and reassemble the unit. On the Bendix AD-IP, removing a through-bolt from underneath the dryer base allows the cartridge (which slightly resembles a spin-on oil filter) to be simply lifted off. On the MeritorWABCO System Saver 1200 and the CR Turbo-2000 and Turbo-3000 air dryers, the cartridge is almost exactly like a spin-on oil filter and is spun off and on similarly. In the case of the CR units, an O-ring needs to be replaced, too.
On all units, also wipe out any accumulated oil and moisture (a few units have an integral sump to help collect them).
Look up manuals on the Web or see your dealer or distributor for printed copies.
In the case of cartridges, you might want to forgo cheaper aftermarket designs for OEM parts, Canale says. Though the aftermarket parts are less expensive than the $30-40 OEM parts, the makers may substitute plastic for the metal used in all the ArvinMeritor cartridges designed for U.S. applications. Canale says this material isn’t strong enough to withstand the normal limits on air dryer heat and can fail, allowing beads to clog your system – a mess that’s difficult and costly to cure.
If you’ve had good service in the past, but more recently are having to replace the cartridge often due to oil fouling, it’s probably time to replace the air compressor. If it’s worn, you’ll probably also hear it running more of the time even though the brake system is relatively free of air leaks.
MeritorWABCO 1200P and 1800P air dryers use their own external purge air tank so air won’t be bled out of the brake system during the purge cycle. If you find you’re not getting the obvious air blast when the air compressor cycles off and the dryer should be going into the purge cycle, check the line between dryer and tank. Look for kinks, internal clogging from the goo that forms in the brake system, and any other blockage.
Leslie Kern mentioned a different situation – heavy brake system use. This is often the case in vocations like dump operations where the driver is constantly accelerating and braking. CR recently introduced a special oil separator that can easily be retrofitted for trucks in these high duty cycle applications to prolong desiccant life. The separator would also be helpful if your air compressor is starting to show signs of wear (some oil blowby), but still keeps the brake system pressurized. She says it is ideal for equipment equipped with ABS systems, as the “pristine” air helps keep contamination from “preventing the system from functioning properly.”
The CR separator can easily be inserted under the desiccant cartridge after de-pressurizing the brake system, removing the eight attaching bolts and then pulling off the bolt-on cap. It requires no maintenance.
For most trucks that are well maintained and have the right unit, properly installed, replacing the cartridge at the right time will keep your dryer working right and your brake system protected from moisture.
How Air Dryers Work
Air dryers contain a cartridge filled with something called a “desiccant” in the form of small beads. The beads are made of a material that attracts moisture very strongly. Air flows through the dryer on its trip from the compressor to the wet tank during the on cycle of the compressor.
Oil is first separated by a simple, mechanical separator – a strainer made of beads. It drips off the oil separator and settles in a sump below. Then, as the air passes through and over the desiccant bed, moisture clings to the outside surfaces of the beads in this attraction process, called “adsorption.” This leaves the air so dry that any remaining moisture stays completely vaporized.
The desiccant beads hold only a few ounces of moisture. But the adsorption process is almost completely reversible. Get the moisture back off, and they can be used over and over again. So, to keep the dryer working continuously, it goes through a “purge cycle” each time the air compressor shuts off.
The dryer also holds some compressed air in spaces called the “purge volume.” The air compressor is periodically shut off by the air pressure governor, which is operated by the air pressure in the system. When shutoff occurs, the air pressure opens a device called a purge valve. Then the pressurized air from the purge volume flows backward through the desiccant and oil separator and out through the purge valve at the bottom of the dryer. As the pressure drops to what is normal outside, the water is evaporated off the beads, and they are left dry. The oil is also blown out of the sump. This is the blast of air you hear each time the air compressor cycles off.
Many air compressors are fed turbocharged air right out of the intake manifold. This air has been slightly compressed by the turbo and has gone through the charge air cooler, so this makes the compressor more powerful and efficient. Because of air compressor turbocharging, the purge valve has another function. It incorporates a turbo cutoff piston that closes off the supply port through which air normally flows from the compressor into the dryer. This keeps this air from escaping through the dryer and out the exhaust port while the compressor is off. It also eliminates the chugging sound that would come out of the exhaust port even with normally aspirated compressors when the compressor is off.
Listen Carefully
Listening for a regular purge cycle can alert you to air dryer problems, says Canale. If the purge cycle occurs too frequently, “that noise may be a symptom of another problem. Do deeper troubleshooting,” says Kern.
Air system leaks, including leaks within the dryer itself, can cause the compressor to cycle more frequently. Leakage causes the unit to come on after less off time and stay on longer. If the leak is big enough, it will stay on all the time. In this case, says Kern, “Figure out where the leak is. It could be in the dryer or anywhere in the system.”
To find the leak, run the engine to charge the system to the point where the governor cuts out. Then listen to the purge of air from the dryer. There will be “a significant initial blast,” indicating that the dryer is purging freely, Canale says. Listen, but don’t feel for this because you could get injured by debris. But once the blast slows down, put your hand under the exhaust port. You should feel a slight flow for 15-30 seconds, after which it will shut off. If flow continues, the most likely cause is a failed turbo cutoff valve, assuming the air compressor is turbocharged. You can quickly determine you have this type system by tracing the inlet line to the air compressor. If it comes from the engine intake manifold, you have a turbocharged compressor. If it comes from upstream of the turbocharger (for example between the air cleaner and the turbocharger), and the turbo valve has failed, you’ll hear a chugging noise. In a few cases, leakage during the off cycle can result from a failed check valve on the dryer discharge line leading to the brake system.
Next have someone dump system pressure by fanning the brakes. Soon you’ll hear the compressor cut in. After the system charges back up to nearly the cutoff pressure, shut the engine off. Now feel for air escaping from the purge valve’s exhaust port. If there is leakage from the port, the problem is a failed purge valve. Leakage elsewhere in the brake system, for example in tank drain valve O-rings, will tax the compressor and dryer and should be fixed. Leaks can be located by coating every connection with soapy water, which will bubble from the leak.
Another common cause of too-frequent purge cycles is a failing air compressor governor or “unloader” as it’s sometimes called. Kern explains that it’s supposed to cycle the compressor off and send a signal to the dryer to exhaust at 120 psi. After that, the brake system uses the air in the tanks till the pressure has dropped to 90 psi. Then it cuts back in. The governor “is a likely item to fail, but low cost. It can begin to send the signal too often as it wears, causing frequent cycling.” Even though the air gauge on the dash is normally connected to the secondary air storage tank, and the governor to the primary one, you will likely notice the indication moving up and down less if this is the trouble.