Designed to haul standardized containers, the experimental Bison Bullet was developed by General Motors in 1964. It featured electronic loading and unloading equipment, so during a pickup, the driver could avoid lumpers and instead just sign autographs.
Amid all the other news stories of October 2005, you may have missed the outcome of the DARPA Grand Challenge, an off-road race in the Nevada desert sponsored by the Pentagon’s Defense Advanced Research Projects Agency.
TerraMax, a modified military vehicle built by Oshkosh Truck, was one of only five entries in a field of 23 to complete the grueling 132-mile course. Its time was less than 13 hours. Not too shabby, considering no one was driving it.
The Grand Challenge is for robot vehicles only. After its route coordinates were programmed in, TerraMax was left to fend for itself among the scorpions, rattlers and coyotes, making its own decisions about how best to get around rocks and gullies and maneuver its 8-foot-wide frame through Beer Bottle Pass with inches to spare.
One might be tempted to call TerraMax “the truck of the future,” but we’ve heard that before. The truck you’re driving today once was a truck of the future, its fuel economy, horsepower, cab comfort and electronic sophistication the stuff of a 1950s trucker’s Buck Rogers dreams.
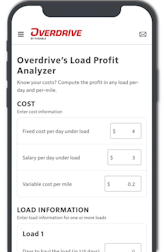
But plenty of other trucks of the future fell by the wayside long ago, some because they were ahead of their time, others because their time was entirely in some other dimension.
Return with us now to what the trucking future once looked like. In the words of a promotional film for the 1950s General Motors Futurliner: “It’s an atmosphere of magic and miracles, but actually it’s all wonderfully real!”
ONE OWNER-OPERATOR’S AERODYNAMIC DREAM: THE PAYMASTER
“I didn’t set out to design a truck,” says Dean Hobbensiefken. “But when you’re a truck driver, you have a lot of time to think.”
Hobbensiefken had one truck in 1962 when he launched his owner-operator trucking business in Lyons, Ore. Soon he was running six trucks, hauling forest products and doing his own maintenance.
“You spent most all your Saturdays maintaining and servicing trucks,” he says. “I needed fewer things to grease, fewer things to check.” He also needed better fuel economy.
For the initial sketch of his dream truck, he placed the steer axle and the rear trailer axle 41 feet apart, as required in Oregon in those days, then tried different two-axle tractor designs and payload configurations. The ideal arrangement, he decided, was a 135-inch wheelbase with a 62-inch fifth-wheel offset.
“That’s a really weird-looking configuration,” he says, “but I saw that if I had a tractor like this, I could haul as much as a four-axle tractor with only a two-axle.'”
He told his idea to one OEM he prefers not to name. “They told me, ‘That can’t be done. We tried that one time.’ Having heard someone say it couldn’t be done, of course I went home and told my wife, ‘I don’t care what it takes. I’m gonna build this thing.’ After all, a truck is nothing more than a big car. I had built several cars from scratch as a kid, just modified hot rods.”
Hobbensiefken drew up blueprints, had a fabricator produce the frame parts, then did the welding and assembly himself.
“I’d get home after a 12-hour day at the trucking company, eat some dinner, then go to the garage and work on the truck until 3 in the morning. My wife was a wonderful, supportive, very patient trucker’s wife.”
The super-efficient truck that resulted had air suspension, a removable power module independent of the axles, single tires instead of duals, and other features designed with the do-it-yourselfer in mind.
“You could grease all the fittings from the driver’s side door,” Hobbensiefken says. “You didn’t even have to get under the truck.”
It also looked funny, as its design was dictated by airflow, not aesthetics. “In aerodynamics,” Hobbensiefken says, “a cabover is the worst case, and a conventional is right behind.”
In finding a name, he drew upon his military experience. “In the Army, the paymaster is the guy who hands you money every month. I thought, this truck is going to hand its owner money every month. I’ll call it the Paymaster.”
In July 1971, he installed the same 534-cubic-inch Ford gasoline engine he was using in his C-Series Ford cabovers for the Paymaster’s debut at the Pacific Logging Congress. “Some of those truck engineers not only came by once but several times, and brought their friends. It was quite gratifying.”
The chief engineer at Hayes, a then-prominent Canadian truck maker, told him, “If you’re getting 4 mpg with a gas engine, this truck will get 7 mpg with a diesel.” Hobbensiefken popped in a Caterpillar 1160 and got 7 mpg, loaded.
In the wake of the 1973 Arab oil embargo, Hobbensiefken signed an agreement with the 49,000-truck Ryder fleet, which then contracted with Hendrickson to build test models.
Hobbensiefken had to persuade the engineers that an 18,000-pound payload on the steering axle was a good idea. Sure enough, the fully loaded Paymaster was able to handle 60 mph blowouts without losing control. Wind-tunnel tests showed the Paymaster had 40 percent less wind resistance than a standard truck, but Hobbensiefken already knew that, thanks to homemade tests devised by a friend at Boeing who had helped Wernher Von Braun build U-2 rockets for the Nazis.
“It’s all about reducing the horsepower demand on the engine at cruise speed,” Hobbensiefken says. “That truck was getting down the highway at 135 hp, and the typical truck of the day was running 220 at the same payload and the same speed. Ryder was convinced this thing would sell. They had a thousand sets of truck parts ordered for the thousand Paymasters.”
However, those plans were scrapped in 1975 due to a deep recession and Ryder’s commitment to buying thousands of traditional trucks on long-term contracts. Hobbensiefken refused to give up.
“I sacrificed some mpg to market the truck, to try to make it more acceptable to the buyer. I added a sleeper cab and conventional tires. Still the OEMs kept telling me, ‘This truck is too far ahead to market yet.’ One OEM told me in 1975, ‘We don’t see ourselves building an aerodynamic truck of any kind until the 1990s,’ and that’s just about when they did it, too.”
In 1980, Hobbensiefken laid out a three-year plan to build Paymasters one at a time himself as a cottage industry, but he gave up when he realized the bank loan, in those inflationary days, would cost him 22 percent interest.
Only 14 Paymasters were built; some are in museums, but others are still working. Owner-operators Richard and Mary Heater put 2 million miles on their 1980 Paymaster. They hauled 80,000-pound flatbed loads at an average 7 mpg for 17 years.
A SPORTS CAR BENEATH A TRAILER: THE STRICK CAB-UNDER
Truck manufacturers have put the cab behind the engine, over the engine, even beside the engine. But it took a trailer manufacturer to put the cab in front of the engine – and under the trailer.
The extraordinary Strick “Cab-Under” was the brainchild of engineer Ronald Zubko, now retired in Farragut, Tenn. “To me, a truck is a tool,” he says. “It’s not something that has to fit a certain aesthetic mold or configuration. It can be whatever it needs to be to get the job done.”
The Cab-Under began as “one of those back-of-the-envelope daydreaming things,” Zubko says. In the mid-1970s, customers were clamoring for ways to get more cubic feet of capacity into trailers without violating strict federal length requirements of 55 feet in the East and 65 feet in the West.
“So I sketched one of these things that showed the driver sitting underneath the trailer,” Zubko says, “and my boss said, ‘That’ll never work.'” For one thing, the boss argued, it would be terribly uncomfortable for the driver.
Shortly thereafter, the boss turned 50, and his wife gave him a 46-inch-high Maserati sports car. “He came in saying, ‘This is the most comfortable thing I ever drove. Let’s look at that design again.'”
Then Zubko and two assistants spent a year dismantling a new International cabover and radically rebuilding it on a special frame. “It was like having a hobby and getting paid for it,” Zubko says.
The result was a heavy truck that wasn’t just a flatbed but a flat everything. The tractor stood only 48 inches high, with 81/2 to 9 inches of ground clearance. The cab was ahead of the front axle, and the Cummins V2 903 engine rode in a low-slung “possum belly” in the middle. The trailer rode on top.
“We could pull standard 27-foot doubles, and the 55-foot overall length limit was nearly all storage,” Zubko says. “That was a lot more cubic content, exactly what our customers were clamoring for, and the economics were quite significant.”
In eight months, Strick calculated, the additional freight hauled per run – especially light cargo – would pay for the cost of the truck. Fuel economy, 7 mpg, was good because the design “cut down on all the drag of a traditional tractor-trailer,” Zubko says.
The first interested customer was a maker of bubble wrap. “Sealed Air toured the company with our Cab-Under,” Zubko says, “and it generated a lot of attention, especially from the police.” At every stop, the driver had to show the paperwork to prove that yes, officer, it is a legal vehicle.
Strick ran exhaustive tests on such things as the truck’s braking ability and the line of sight from the driver’s seat, Zubko says. “You’re basically sitting in a semi-reclining position, like you’re in a sports car. If you’re sitting in the Cab-Under, and you drive up alongside a Corvette Stingray, you’re in exactly the same position.”
For safety, the Cab-Under driver was encased in what Zubko calls “a NASCAR-like roll cage, a half-inch of solid steel,” but that was not enough to keep from running afoul of politics. U.S. Sen. Ted Kennedy denounced the Cab-Under as unsafe. Future Public Citizen leader Joan Claybrook, then head of the National Highway Traffic Safety Administration, was not impressed when Strick brought the Cab-Under to Capitol Hill for a demonstration.
“The driver had driven it for six months cross country,” Zubko says. “He said it was one of the safest and most comfortable vehicles he’d ever driven.”
The Teamsters took the Cab-Under to the Transportation Research Institute at the University of Michigan, which confirmed everything Zubko knew to be true. “It was a stable vehicle,” Zubko says. “It couldn’t jackknife because there was no kingpin. In a rollover, the driver would be better off than in an articulated vehicle.”
The report also noted downsides. “An impact against a low, rigid barrier such as a retaining wall would be a problem, and in very bad weather, the splash and spray from the road surface would be a visibility problem,” Zubko says. “That was a valid criticism.”
There was talk of using the Cab-Under design in dump applications, or as a ladder platform in emergency vehicles, but Strick ultimately decided to remain a trailer manufacturer, not a truck manufacturer, Zubko says.
Only two Cab-Unders were built. The improved second model, which had an 84,000-pound hauling capacity, was sold to a German who used it to haul flatbed building materials in Europe; it’s now in a German museum. The original is in Zubko’s garage.
“It’s a relic of a bygone era,” he says. “You don’t have a chance to do something like that very often. People are very resistant to change.”
DRIVING GM’s FUTURLINER INTO THE 21ST CENTURY
The hit of this summer’s Antique Truck Historical Society convention in Auburn, Ind., was a beautifully restored General Motors Futurliner No. 10, one of a small fleet that toured the country during the Eisenhower administration in a promotion called the Parade of Progress.
In its debut, the restored Futurliner was attention-getting not just for its gleaming red-and-white paint scheme. It’s 33 feet long, 8 feet wide and more than 11 feet tall, with a 248-inch wheelbase. It looks sort of like a truck-bus hybrid, but mostly like nothing seen on the highway in 50 years.
The 25-member restoration team, all retirees in green caps and khaki shirts, happily worked the convention crowd, selling Futurliner T-shirts, posters, DVDs and refrigerator magnets.
The retirees have gotten together every Tuesday since fall 1998, with summers off, to work on the Futurliner in the barn of restoration leader Don Mayton of Michigan. “It was only supposed to be a part-time project,” Mayton says, laughing. “I’m supposed to be retired.”
Also on hand were some of the original “Paraders,” the drivers and support personnel who traveled with the Futurliners. Jim Gentzel, for example, helped launch the tour in April 1953. He traveled with the Parade of Progress to 110 cities in 38 states and Canada. His last stop was Janesville, Wis., in September 1955. The 12 Futurliners traveled in a 30-vehicle convoy that included ordinary big rigs pulling 40-foot trailers loaded with equipment and supplies.
Futurliner innovations included air conditioning, power steering and curved, tinted windshields. All the engineering news wasn’t good, however – an 8-foot-wide, 121/2-ton vehicle was a poor fit for the two-lane roads of the day.
“They were under-powered, under-braked,” Gentzel says. “They were kind of hard to steer. From the driver’s seat, you couldn’t see anything within 20 feet. The top speed was 40 mph.”
The Futurliners always had surprisingly small engines. The restored No. 10 is powered by a single GMC 6-cylinder gasoline engine. “They hired young guys just out of college to drive these things,” says restorer Ed DeVries, “and they didn’t want to give them too much power.”
In each town, the Paraders circled the Futurliners and opened their cargo bays to reveal science and technology exhibits. The Paraders also erected a tent that seated 1,200 people. The stage show was science demonstrations of wonders such as fax machines.
“We fried an egg in a Dixie cup on a cold stove with a microwave, then had a kid come up and eat it. Lots of Mr. Wizard stuff.” Gentzel says, referring to the classic kids’ TV science show of the 1950s.
After Gentzel left the Parade for a career in GM’s financial office, the Futurliners visited 36 more cities, finally wrapping up the tour in June 1956. “When it was over, all the equipment went back to Pontiac, Mich., and no one seemed to care,” Gentzel says.
GM sold the Futurliners to anyone interested in a promotional vehicle. Evangelist Oral Roberts used one, dubbed the Cathedral Cruiser, in his crusades. Futurliner No. 10 was sold to a brewery. By the time collector Joe Bortz donated No. 10 to the National Automotive and Truck Museum decades later, it was a rusted hulk.
“These are such unique vehicles, and all the ones we could find were in an absolute state of disrepair,” Mayton says. “It was such a shame, and we were determined to save one of them.”
All the parts and systems, from the Art Deco letters to the wiring harness, had to be redesigned and rebuilt. GM no longer even had the schematics. Money and expertise arrived from around the country. The specially designed one-piece windshield alone cost $10,000.
Visitors to the restoration website, www.futurliner.com, can find a wealth of historical information and support the effort by buying memorabilia including a documentary DVD, which records the thrilling moment when the engine cranked on the first try.
A real lightweight
This 1934 Fageol at the Pacific Northwest Truck Museum is remarkable not for its looks but for its way-ahead-of-its-time construction. One of 10 commissioned by Leland James of Consolidated Freightways in Portland, Ore., it’s all-aluminum: frame, cab, hood, fenders, radiator. So resistant were OEMs of the day to the notion of lightweight aluminum trucks that James vowed to build them himself. The result was Freightways Manufacturing Co., known since 1942 as Freightliner.
Double trouble
This one-of-a-kind 1957 Diamond T was radically modified in the 1960s by its owner, grain hauler Frank Gripp of Annawan, Ill., who tired of Frank Jr.’s complaints that every truck on the road was passing them. The elder Gripp said he couldn’t afford a faster truck, so he mounted a second engine, a 300-cubic-inch Buick V8, and ran the driveline through the radiator. On the highway, the driver could run one or both engines and shift between them. It’s now owned by Diamond T collector Delbert DeYoung of Friesland, Wis. “We call it Pinocchio,” he says.
Amazing Amalgam
The Kenworth Bruck, half bus and half truck, was made in 1951 for the Great Northern Railway. The front held 21 passengers, the back 7 tons of freight.
For 20 years, the Bruck made daily round trips between the Montana towns of Whitefish and Kalispell. Fully restored, it’s now on display at the Stumptown Historical Museum in Whitefish.
Where no man had gone…
Four years before men walked on the moon, General Motors built this 8-ton mobile laboratory for NASA. Today’s mobile labs on Mars are 5 feet long, weigh less than 400 pounds and are remote-controlled from Earth.
Half a cab will do
The most experimental half-cab design in the Pacific Northwest Truck Museum is this 25-foot flatbed straight truck built by Murty Brothers of Portland, Ore. The rear 10 feet of decking lifts to reveal a fifth wheel. Georgia Pacific used these to haul lumber from the West Coast in three-truck convoys. For the backhaul, one truck would haul the other two on the trailer. “The insurance companies killed that idea,” says museum President Terry Dovre. “There were several wrecks with all three trucks in the ditch.”
Nice visibility
“This is just like flying a plane!” said one excited driver of the Kenworth cab-beside-engine, introduced in 1953. Designed for ideal driver visibility, the cab-beside also was 1,000 pounds lighter than a standard truck. This 1955 model, owned by Don Krogh of Mauston, Wis., was on display at this summer’s American Truck Historical Society convention.”I drove a lot of these bastards,” said Dick Beaudette of Blane, Minn. Gerald Osborn of Kansas City, Mo., recalled one harrowing ride with a trainee. “It’s so hard in a cab-beside to judge the other side of the cab,” Osborn said. “That guy must have hit seven or eight cars. They went right up on the sidewalk.”
Top of the world
One of several industry attempts to introduce a gas-turbine engine, the prototype Chevrolet Turbo Titan III, like the Unisphere, was a popular attraction at the 1964-65 New York World’s Fair.