RESOURCES
Bandag
www.bandag.com
(563) 262-1400
Bridgestone-Firestone
www.bridgestone-firestone.com
(615) 231-3367
Goodyear Tire and Rubber
www.goodyear.com
(330) 796-2121
Michelin North America
www.michelin.com
(864) 458-5000
Tire Retread Information Bureau
www.retread.org
(888) 473-8732
Industry surveys have found most on-road tire remains were caused by failed casings, both from new tires and retreads, normally due to overload or low air pressure.
You’ve heard horror stories about retreads that failed. These stories are normally told without an understanding of what makes tires, including new tires, come apart. They also often reflect a lack of knowledge about how good retreading technology actually is these days.
Tread will last, at most, about 350,000 miles, says Al Cohn, Goodyear’s manager of strategic initiatives for commercial tires. However, a properly maintained casing is designed to last as long as 750,000 miles, he says, and that’s why a careful retreading program has the potential to save money.
Consequently, “Retreading is the solution to maximizing the investment that a fleet has made in the casing itself,” says Randy Clark, vice president of marketing for Michelin America Truck Tires.
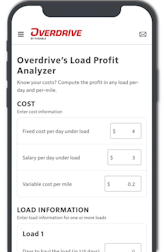
“No major truck tire manufacturer would dream of bringing a truck tire to market that has not been designed for multiple lives,” says Harvey Brodsky, managing director of the Tire Retread Information Bureau. “If manufacturers did, no one would buy it because it would not be cost-effective.”
Cohn estimates that nearly 85 percent of large fleets retread their tires.
“You can’t afford to put new tires on everything,” says Dorothy Maddox, vice president of Nick and Dees Trucking, a small fleet in Hereford, Texas. “You can’t afford to go any other way, because you can’t even sell the casings.” Her fleet’s experience with retreads has been spotty. On rare occasions, tread has peeled off, without a casing failure, and damaged their equipment. “Heat has a lot to do with the problems we’ve had,” she says, particularly during summer operations in the Southwest.
She says the fleet’s present experience, with Michelin retreads, has been the best. They’ve had much better experience with retreading done by local dealers than with buying retreads on the road.
Maddox says casing preparation has proved to be a key to successful retreads, and experts agree that casing maintenance is the most important step for a retreading program. Because air is part of the structure of the tire, running underinflated will destroy a casing because it will flex more than it’s designed to, creating heat that weakens it.
Don Schauer, manager of fleet communications at Bandag, reports that 75 percent of on-road failures are the result of too little pressure for the load. Be careful about loading properly and, using pre-trip and on-road checks, keep tire pressures as close as possible to the maximum recommended pressure when fully loaded. Use a calibrated pressure gauge, not one that’s been bouncing around in the glovebox. Note tire damage likely to cause leakage and get repairs quickly.
The next step is to avoid abuse. Round corners carefully so tires don’t run over curbs. Avoid hitting objects on the road.
Correct repairs will preserve a good casing, while poor ones mean a death sentence. Bandag recommends having repairs done only by a technician certified by the Tire Industry Association. Be aware that tires must be removed and installed with proper tools to avoid bead damage. (The old blow-it-onto-the-rim-with-ether trick is strictly taboo.) Unless punctures are sealed from inside the casing after removing the tire from the rim, tire cords will rust, rendering the casing useless.
Vocation also affects casing life. Pickup and delivery fleets may retread a number of times because treadwear is high; total miles on the casing will be less, however.
Schauer says it’s critical to track the age of the casing because rubber will eventually oxidize and deteriorate. Many smart fleets put a five-year limit on a casing’s life to help guarantee its health until retired. Clark says trailer tires with relatively few miles may last a lot longer.
Even a quality retread needs to have the right tread pattern for the application, says Cohn. Consult a good tire expert who can help you pick the appropriate one.
Most linehaul fleets use good casings being retreaded for the first time (termed virgin casings) as drive tires. Cohn says a common pattern with Goodyears is to run a new tire 350,000 miles on a drive axle and then retread it for about 250,000 miles as a drive during the second life. A third life in the range of 100,000 to 150,000 can then be had on the trailer. Some casings, though, get terminally damaged and can’t be reused each retreading cycle.
Visiting the retreader’s shop can help you know the quality of the work. The shop should have sophisticated, non-destructive inspection equipment that allows the technician to see inside the casing. Retreaders who warrant their work and have a reputation for backing it up (including paying for road calls) deserve your business.
You can buy retreaded tires, but the long-term savings are greater if you preserve your investment in your own casings and have them retreaded. Industry sources estimate the cost of retreading your tire to be 30 percent or more of a new tire’s cost. If you have a good tire maintenance program, your casings will perform more reliably than the average one you might buy from a dealer, and you’ll maximize the benefits you can get from a retreading program.
THE ART OF RETREADING
The retread process starts with careful examination of the casing. If an X-ray or other technology determines it is defect-free, it is buffed down to ensure an even diameter. This also produces a smooth surface for tight bonding of the new rubber. After inspection, the casing receives any repairs required to ensure that it has no defects caused by tread damage.
Finally, the job of restoring the tread begins. There are two basic methods:
MOLD CURE. Uncured, soft-tread rubber is applied to the casing. The casing is inserted into a large mold, or enclave, which contains the tread pattern. The casing and raw rubber are subjected to heat and pressure, which cures the rubber. Few retreads are done this way because a different mold is needed for each tread pattern and tire size.
PRE-CURE. Pre-cured retreading, which accounts for 80 percent of retreading, bonds a strip of finished tread to the casing with less heat than is required for a mold cure. Advocates of this process argue that subjecting the casing to less heat means less risk of damage or deterioration. Pre-curing is done at 210 to 250 degrees, while mold curing is done at 295 to 310 degrees.
A cushion gum layer of uncured rubber is uniformly applied to the casing. A strip of tread with the desired pattern is then fitted around the casing, with its ends butting up against one another. The tire is put in a flexible envelope and pressure is applied inside an enclave to keep the tread firmly in place during the process. One size enclave does all sizes of tires. Heat, pressure and time cure the cushion gum and bond the tread to the tire.
Goodyear has a special form of pre-cure tread that has no seam across the tire, says Tim Sawdey, manager of retread policy and supply. Called Unicircle, the tread is molded in a continuous ring rather than a strip. The tread is snapped onto the casing and is designed to hug the sidewall for better adhesion.
Once retreading is completed, another careful inspection must be performed. If the application of the new tread is not perfect, the job must be redone.