It takes more than flipping an on/off switch to get the most from your engine retarder.
Without an engine brake, diesels don’t produce much braking compared with car engines because they lack a throttle – the biggest source of engine braking in a car. Truck diesels are also small for the weight of the vehicle, which is one reason trucks sometimes run away on steep downgrades.
Clessie Cummins, who invented the Cummins diesel, also invented the Jacobs Engine Brake, commonly known as the “Jake Brake.” The Jake Brake and its competitors use hydraulics powered by the engine’s existing valvetrain parts to convert your truck diesel into a retarder that stops almost as hard as the engine pulls under power.
The engine brake adds little to engine wear. Its biggest advantage is that it works by compressing and releasing air, eliminating the friction between dry parts of a service brake system, so it will never overheat. Having an engine brake not only will help you descend steep grades safely, it will significantly cut your maintenance costs because it will save your service brakes.
Proper operating
An on/off switch allows you to turn the engine brake off altogether or allow it to operate when the throttle and clutch pedals are fully released (your feet are off).
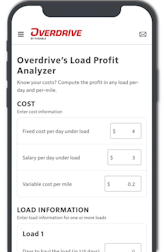
The brake is also controlled by a “Low/High” or Low/Medium/ High”dashboard switch with two or three positions, so you can match the power of the brake to road conditions. With a two-position switch, you get braking action on either all six cylinders or three of them, giving either full power or half power. With three positions, the switch settings engage six, four or two of the engine’s cylinders, giving full braking power, two-thirds or one-third power.
There is also an accelerator pedal switch. If the main power switch is on, the switch turns the brake on when the driver releases the throttle but cuts it off as soon as he applies power.
A few vehicles also have a brake pedal switch, so the engine brake can never be used alone – only after the service brakes are applied.
Follow this procedure to operate your engine brake:
- The engine brake depends on a free flow of oil, so always wait until the engine reaches normal operating temperature before switching it on. Always turn the engine brake switch off when shutting the engine down so it will not operate with the engine cold.
- The most critical factor in operating an engine brake safely is understanding the effect of road and load conditions. Unless your tractor or truck has a front drive axle that is engaged, the engine brake retards only the drive wheels, creating potential for a jackknife if the road is wet or icy. This problem is worse with a single-axle tractor, so never operate an engine brake when running bobtail, or with an empty trailer on a slippery road.
- When driving loaded under conditions that are just slightly slippery (for example, in the rain), first observe whether or not the truck remains stable when backing out of the throttle. If it does, then turn the brake switch to the lowest setting. Make sure there is plenty of room on both sides and in front in case you need to recover. Next, activate the brake cautiously, ready to turn it right off or declutch if the tractor’s rear wheels begin to turn out.
Remember to turn the engine brake back off or declutch right away if the tractor starts to skid, fishtail or even jackknife. Advance to a higher setting only if the rig remains quite stable; do this with the same caution used initially. If the rig starts to jackknife, recover as above.
- Under dry road conditions, use the maximum power setting for abrupt stops, as in traffic. When descending long, gradual grades, start at the lowest power setting and increase it, as necessary, to hold your speed where you want it. You will often be able to alternate between two power settings to keep the truck at the right speed, using the more powerful of the two settings to drop a few miles per hour, then switching to the other to bring the truck back up to your desired speed of descent.
- Descending a long, steep grade always requires using a lower gear and descending slowly. Always activate the engine brake before reaching the downgrade to check that it is working. With an engine brake, you can use a higher gear and still get enough engine braking to minimize use of the service brakes. The lower the gear you use, the greater the retarding ability of the engine brake and the cooler your service brakes will remain. The Jacobs manual estimates that, depending on load, you can descend a 6 percent grade at 25 mph using your Jake brake. The ideal is to find the “control speed,” which is the speed and gear that cause the brake to maintain the constant speed you want with little or no use of the service brakes. Remember that using too high a gear can cause overheating of your service brakes even with a good engine brake.
- The engine brake’s power also increases rapidly with an increase in engine RPM. Any time you need maximum braking power, you should downshift until the engine is between 1,800 RPM and the maximum speed allowed for engine brake operation (usually 2,100-2,300 RPM). Look in your owner’s manual to find out what that allowable RPM is. Then observe it very carefully, as bent valve-train parts will typically be the result of over-speeding the engine. This is abuse, not covered under the engine warranty.
- The truck gains speed during the shift on a steep downgrade, which means you need to downshift at a lower RPM. When downshifting on a downgrade, always make sure you have plenty of RPM to make the shift. If your governed speed is 1,800 RPM, you should not downshift much above 1,200-1,300 RPM. If you can’t make the shift, go right back into the next higher gear.
- When shifting with the clutch, the engine brake is inactivated. But many drivers shift without the clutch and leave the switch energized to speed the shift (sometimes called “Jake shifting”). This is risky because the powerful engine brake slows the engine crankshaft very fast. This can subject the drivetrain to extreme torque.
- On trucks with an electronic engine, the brake is de-activated at about 1,000 RPM. Some engines with traditional, hydro-mechanical injection have switches to cut off the brake at low RPM, too. But if your vehicle doesn’t, always remember to switch off the brake when running down low because the retarding force becomes alarmingly potent. This will also prevent stalling and rough operation.
Making adjustments
An engine tune-up involves not only adjusting the engine’s overheads – the valves and injectors – but the engine brake itself. In fact, you need to remove the engine brake housings in order to access the valves and injectors for adjustment.
We received the help and advice of Jacobs regional Manager Bob Hillen and technician Bill Lattemann at Penn Detroit Diesel in Fleetwood, Pa.
“Doing this is not something anyone should be afraid of,” Hillen says. “But, since you are dealing with overheads, it’s essential that all adjustments be to specification and that all torque values are observed.”
The normal price for setting the overheads on a Series 60 is $355. Although they inform us that they normally don’t charge extra for engines with Jake brakes, it’s obvious that a trucker can save himself some money by getting the feeler gauges, injector setting tool, and socket and torque wrenches and doing this job himself.
Before starting, make sure the engine is cool – with oil temperature of 140 degrees F or less.
This procedure is for the Model 765 Jake brake used on Detroit Diesel Series 60s up until about four years ago.
- In order to access the overheads, the Jake housings must be removed. To do this, disconnect the electrical connector on each of the three housings. Then remove the two capscrews on one side and the single one on the other, and lift them off.
- Set the valves and injectors according to instructions in the Detroit Diesel manual.
- Once the valves and injectors have been set, make sure there is no oil in the boltholes. Blow them out with clean compressed air, if necessary.
- Lubricate the threads of all the capscrews with clean engine oil. Position each housing with the two capscrew holes on the exhaust valve side of the engine, and start the capscrews. Once each housing is in place and capscrews started, slide the housings around on the head to center their positions. This will help ensure that the brake will be perfectly aligned with the valve adjusters.
- Using a torque wrench only, torque the fasteners one by one to 40 pounds-feet. Then torque them to the required 90 pounds-feet. Reconnect the electrical connector on each.
- To adjust each cylinder, its exhaust valves must be on the base circle of the cam. Bar the engine over by the front crankshaft pulley to reposition it as necessary.
You can use the engine positioning guidelines Detroit Diesel supplies for setting each cylinder’s exhaust valves to make the related Jake setting. Or you can turn the engine over until the exhaust rocker’s roller, the one on the left on each cylinder, is on the base circle of the camshaft and completely off the cam lobe before adjusting the Jake parts for the valves of each cylinder. - Work on the exhaust side of the engine. Adjust the “blind side” adjuster, via the slave piston on top of the housing. This is the adjuster on the left side that has no adjusting screw on top. Start by loosening the slave piston’s adjusting locknut and then turning the screw outward. Then slide the required feeler gauge (0.026 inch) between the exhaust valve adjusting screw and the Jake actuator. Turn the adjusting screw back and forth with a screwdriver until there is a very slight pull as the gauge is slid between the parts.
Once the adjustment is correct, hold the screw with the screwdriver and gently tighten the locknut. Then torque the locknut with a torque wrench to 25 pounds-feet. It’s important to torque properly, as the screw is hollow and may be distorted by overtorquing, which would impact brake operation. - Now adjust the bridge that runs between the two valves by setting the adjustment on the other valve. This is done the same way, but right above the valve. Loosen the locknut, loosen up the bridge adjusting screw and slip the same 0.026-inch gauge between the valve adjusting screw and the bridge. Set the lash exactly as you did on the other side. Tighten and then torque the locknut in the same way.
- This basic procedure must be performed on the exhaust valves for each cylinder, making sure each rocker is in the right position before starting.
- Reconnect the electrical connectors. Then with the cam cover still off, start the engine and run it until the oil begins to warm up. Depress the armature, which is in the center of the top of the solenoid valve, to activate each several times and fill the housing with oil.
Note that every Jacobs engine brake has a label on it that gives the lash setting. The latest Jake for Detroit Diesels is the Model 790/795 (depending on the particular engine).
It uses two housings, each with six slave pistons rather than three. Each valve has its own slave piston, eliminating the bridge. Each slave piston is adjusted individually but in the same way as on the 765.
Jake brakes for other brands of engines are adjusted similarly. Jacobs will supply manuals giving specific torques and describe the slight individual variations in each adjustment procedure.
Tune-up
It’s best to have a tune-up performed on an engine brake every 300,000 miles or 9,000 hours in typical highway service. In this procedure, critical parts are cleaned and inspected, and some perishable springs and control valves, and various related parts, are replaced. It’s a complicated job best performed by a technician. At Penn Detroit Diesel, an engine brake tune-up costs about $200 for parts and $344 for labor, or $544.
Aftermarket installation
Installing an engine brake on an existing engine may seem quite basic. It bolts on the same way as the overhead adjustment. But most truckers use the services of a professional technician in getting an engine brake, because dealing with the wiring and switches can be a complicated job.
Because of the complicated electricals, Penn Detroit Diesel normally charges for about eight hours of labor for the job, or $688. The brake itself lists for $2,500.
After installation, the engine’s ECM needs to be reprogrammed (or “reburned”) so it will properly coordinate the operation of the brake with the engine rpm, pedal positions and ABS. This will cost another hour of labor ($86), and Detroit Diesel normally charges $400 for the electronic download; however, the download charge is often waived if the brake is purchased at the Detroit Diesel outlet where you are having the work done. The net cost, depending on labor rates where you are dealing, would normally be in the neighborhood of $3,200.
That’s expensive, but it’s necessary to consider what you are getting, in addition to a device that could save your life on a long downhill grade. Tractor and trailer brake jobs are expensive and mean downtime; using an engine brake properly could reduce their frequency by at least 40 percent. Plus, you’ll get some of your money back when you trade or sell your vehicle.
For further information, please contact the following:
Jacobs Vehicle Systems
www.jacobsvehiclesystems.com
(860) 243-1441
Pacbrake
www.pacbrake.com
(800) 663-0096
Tecbrake
www.tecbrake.com
(800) 766-2251
Penn Detroit Diesel-Allison
Fleetwood, PA
www.penndda.com
(610) 944-6657