Checking the transmission fluid requires getting underneath and pulling a plug. But, unless seals are defective, leakage is negligible, and all you’ll need to do is pull the plug for a second to see that the level is satisfactory.
Today’s axles and transmissions are beasts of burden: Smaller than their predecessors, these components have higher power densities but with less lubrication capacity than earlier models. At the same time, engine torque through the driveline is higher
and higher, says Jack Zakarian, consulting engineer with Chevron Corp. In other words, “The stress on oil has gone up,” he says.
That’s why these workhorse components need lubes tough enough to handle the rigors of over-the-road operation. There are two basic types of lubricants available for axles and transmissions: mineral lubes, which are distilled, or separated, out of crude oil with heat and solvents, and synthetic lubes, made through a process that enhances the most basic hydrocarbon molecules.
That process produces a more pure lubricant that offers improved performance and longer component life and that remains stable for longer periods, says AmSoil’s Ed Newman. For these reasons, component makers have authorized transmission and axle fluid change intervals up to five times longer than with mineral lubes. Longer change intervals mean lower overall cost because you’ll use less lube over the life of the component and have less downtime. Yet, despite these advantages, only about half of owner-operators use synthetic lubricants in their transmissions and axles, according to an Overdrive survey.
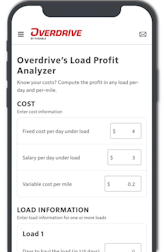
That’s too bad, experts say, because synthetics do a superior job at tackling the two biggest challenges transmission and axle lubes face: heat and friction. Today’s transmissions carry more and more torque and power with the same size gears in the same case, Zakarian says. “Many transmission coolers today dump their heat into the engine cooling system, which in many vehicles raises transmission temperatures even more,” he says. The problem is compounded by aerodynamics, which minimizes airflow around the transmission, meaning almost all the heat has to be carried away by the cooler. The result is a high concentration of heat there.
Truck drive axles, on the other hand, use gears that have many advantages, including strength, but which create a lot of sliding friction. Although the total amount of heat created is less than in the transmission, the fluid still must work very hard – much harder than in the past. The loads on the teeth are more concentrated than in the transmission. There is also less cooling air passing around the axles than in the past.
For these reasons, axle lubes need EP (extreme pressure) additives, which create a surface coating on the gearteeth that’s “almost a solid under load,” says Zakarian, and which prevents welding and seizure. The coating enables those hypoid gears to slide over one another without scoring, while helping resist “much higher loads as well as the shock loading,” says Alex Bulkhovsky, a technical adviser with ExxonMobil.
When it comes to dealing with heat, synthetics can run at high temperatures without getting too thin because their viscosity is more stable than mineral lubes. “My shop people tell me that heat destroys components,” says Harold Mast, owner of BRT Transport in Parkesburg, Pa., which has used synthetics in transmissions and axles since 1996. With synthetics, “we believe the units run cooler and will last longer,” he says.
In fact, synthetics can endure thousands of hours at high temperatures without forming deposits that interfere with cooling. A synthetic will degrade less in 500,000 miles than a mineral lube will in 50,000 miles, Bulkhovsky says. Deposits result when heat attacks the lube and converts it from oil into sludge and varnish. “There is a lot of heat generated in the transmission and axle,” says Bulkhovsky. “That heat needs to dissipate or the lubricant degrades.”
Deposits and sludge slow heat transfer. Heat is trapped, and there can even be a spiraling cycle in which the extra heat then speeds up the rate at which the deposits are formed.
In the end, partly because of heat-related expansion and partly because of the space they occupy, the deposits “change the clearances in the geartrain,” says Bulkhovsky. “The clearances get tighter, and the equipment works harder,” because the moving surfaces are clamped closer together and there is more friction. “This happens because the lubricant can’t get between the working parts,” he says.
The ability of synthetics to run at high temperatures hour after hour without either getting too thin or forming deposits enables them to solve these wear-causing problems.
Synthetic lubricants also save fuel, as much as 3 percent over mineral lubes, experts say. “Because of the purity, the molecules are all the same size,” Bulkhovsky says. “It’s like running over multiple ball bearings. It’s smoother than mineral lube.” Citgo Petroleum Corp.’s Mark Betner describes this as a “lower coefficient of friction.” In other words, synthetics’ superior “slipperiness” reduces the amount of power required to turn the gears and bearings so the engine uses less fuel.
Another factor contributing to fuel savings is that synthetics maintain their viscosity – even at low temperatures. “Synthetics flow better at a low temperature because they do not crystallize when cold,” Zakarian says. This means they “allow quick lubrication of critical parts upon start-up in extremely cold climates,” says Reggie Dias, director of commercial products for ConocoPhillips Lubricants.
Better fuel economy, enhanced component life, reduced maintenance costs and longer warranty terms are just a few reasons why using synthetic lubes could be a good choice for your business. “We feel like we are saving a lot by reducing downtime and extending our warranties,” BRT Transport’s Mast says.
All lubes qualified for extended use and warranty, whether full synthetics or not, offer superior performance in over-the-road applications. However, if you run off-road or in other unusual circumstances where there is a problem with fluid contamination – from dust, dirt and moisture – you’re probably smart to stick with traditional mineral lubes and shorter change intervals.
MUCH OF THE BANG FOR FEWER BUCKS
Still worried about the high price of synthetics? You can get most of the benefits of synthetic lubes at a lower cost with products from makers including Citgo, Chevron and Shell. These highly refined mineral lubricants cost more than regular mineral oils and are not as widely sold.
Called Group II and Group III base stocks, they meet component manufacturer’s extended warranty and change requirements. However, that could be changing. Rick Muth of Roadranger field marketing, which handles service for both Fuller transmissions and Dana Corp.’s rear axles, says that the qualification test for extended changes and warranty will be toughened “to include better performance in low temperature operation and better gear wear and scoring protection.”
Refiners create these “super” mineral lubes using very high temperatures and pressures and special chemical treatments to produce mineral base stocks that are “actually chemically reacted, and altered or modified,” says Chevron Corp’s Jack Zakarian. “It’s a synthetic process,” and even though the final product isn’t built from basic molecules, as is a synthetic oil, it still has a much more uniform structure. As a result, the difference between the two is “a subtle distinction.”
As long as the “super” lube you are considering meets the performance and warranty requirements outlined by your axle and transmission maker, there’s no reason you can’t use it, experts say. Lube makers put these lubricants through extensive field testing in order to have them included on component suppliers’ approved lists. For example, to receive warranty approval from Dana Corp. and Arvin Meritor, Shell put its “super” lube through rigorous lab testing, as well as more than 50 million miles of on-road fleet trials, says Greg Raley of Shell Global Solutions.
There are some very good semi-synthetic lubes for automatic transmissions, though they have been tested only in autos, not commercial trucks, where the lube runs hotter, says Dwight Kramer, OEM development manager at Castrol, a brand of BP Lubricants. He recommends fully synthetic lubes, such as Castrol’s TranSynd, for auto trannies.
THE PRICE OF CHANGE
Even though synthetic lubes cost more than mineral lubes, the longevity of synthetics yields a modest savings of $200 or $300 over mineral lubes over 500,000 miles for do-it-yourself changes. The real economy, though, comes by eliminating the downtime and inconvenience of more frequent changes. Over 500,000 miles, a synthetic might save four changes for axles, seven changes for the transmission. Actual costs and drain intervals vary by application, brand, component capacities and other factors.