A Norcal Waste Systems truck is refueled with liquid natural gas. LNG also can be used in medium-duty trucks, though less exotic spark ignition technology is normally used in place of high-pressure gas injection.
You’re used to filling up with good old diesel No. 2 derived from mineral crude oil, but some surprising new fuels could end up being available to you, especially if your truck comes home to roost every night near a big city.
Fuels that are in gaseous form pose challenges for use in a diesel engine, but many of those challenges have been dealt with. New technology such as high-pressure gas injection with a pilot shot of diesel fuel is an effective approach in heavy-duty engines. In medium-duty engines, necessary changes may include such departures from diesel design as putting spark plugs in the engine and lowering the compression ratio.
A common theme – and what might prove to be the Achilles’ heel for the emergence of some promising new fuels – is the need for centralized fueling. This may be necessary to tap city gas mains or equipment that liquefies natural gas, or to allow bulk purchase of a liquid fuel custom-blended by a local distributor.
Biofuels such as biodiesel and diesel-ethanol blends are compatible with present engines, though the latter need careful handling for safety reasons.
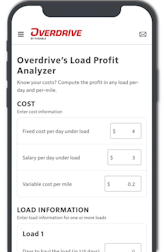
Biodiesel
The National Biodiesel Board estimates that biodiesel consumption rose from 250 million gallons in 2006 to 450 million gallons in 2007. That’s well under 1 percent of the 170 billion gallons of gasoline and diesel fuel that Americans use annually.
Minnesota has required nearly all diesel fuel sold in that state had to be a 2 percent biodiesel blend since Sept. 29, 2005, though the requirement has been suspended for brief periods due to jelling problems during cold weather. The state of Washington will require sale of a 2 percent blend as of Dec. 1, 2008, or earlier if certain local availability
triggers are met. Iowa requires that 25 percent of sales at larger retailers be ethanol or biodiesel by 2010. Other mandates for use in state vehicles, tax incentives, or other goals have been legislated.
However, with demand for gasoline and diesel projected to double by 2025, pressure will continue to rise for use of any suitable alternative fuels.
Biodiesel reduces the carbon footprint of a diesel engine, which means that the CO2 it emits will be turned back into oxygen and sugars during later growing seasons. It also emits significantly less particulate. Its use has become politically and economically desirable because of its ability to reduce the consumption of foreign petroleum and stimulate agriculture and new refining activity in the United States.
Engine makers have been testing biodiesel in their products for years and have taken steps toward accommodating its use, most obviously via their biodiesel specifications. With consultation and a reliable supplier, you should be able to operate on blends ranging from 5 percent to 20 percent, depending on the engine manufacturer. Both Caterpillar and Cummins allow quality B20 that meets the American Society for Testing Materials standard, though Caterpillar recommends using oil analysis, as change intervals may need to be slightly tightened.
The decision to use a biodiesel blend will not automatically void your warranty, says Mike Powers, Caterpillar’s product development manager. On the other hand, realize that no problem caused by any fuel, including regular diesel, is covered by any engine maker’s warranty. The best policy is to understand the engine maker’s specifications and discuss all the facts with your dealer and service people before running it. Some experts believe that simply installing fuel heating equipment for winter, desirable even with regular diesel fuel, will greatly reduce cold weather trouble.
Caterpillar believes that clean diesel fuel, not biodiesel, “will be the preferred fuel for the future,” says Charissa Ebbert, the company’s product information manager. One reason is the complexity of the 2007 emissions system.
Caterpillar does not recommend biodiesel in 2007 engines because of the U.S. Environmental Protection Agency’s mandated maintenance intervals for the diesel particulate filter, Powers says. The Caterpillar Regeneration System has a small injection nozzle that needs periodic cleaning with a fuel additive, a procedure done at the same time as DPF ash cleaning. Biodiesel can cause the nozzle to clog too early, Powers says.
Caterpillar and all the engine companies generally support biodiesel in earlier engines, however, because it reduces trucks’ carbon footprint by effectively recycling carbon dioxide, Powers says.
“Our biggest concern is that there is not enough consistency across the country,” he says. “At present, the states don’t have the regulators in place, the weights and measures people who verify that normal diesel fuel meets the ASTM D975 specification.”
The Engine Manufacturers Association is working on a “more robust” and complete specification than the present one, Powers says. In the meantime, biodiesel may not be worth the risk “unless you know your supplier can deliver the specification consistently,” he says.
The National Biodiesel Board is attempting to get as many refiners as possible to achieve BQ-9000 certification, which guarantees consistent refining to the ASTM standard and verification through constant testing.
Natural gas
A surprising alternate fuel for diesels is natural gas, made up mainly of methane. Whereas diesel is about one-third carbon – meaning that diesel engines, even when yielding perfect combustion, produce a substantial amount of CO2 – methane is only one-fifth carbon. Its simple, gaseous structure makes it burn relatively cleanly and with almost no soot. Its high hydrogen-to-carbon ratio means inherently lower greenhouse-gas emissions.
Powers says Caterpillar does not see natural gas as a viable truck fuel. The ideal natural-gas application is a fleet with vehicles that return regularly to a home base within reach of city gas mains.
However, Cummins-Westport, a joint venture of Cummins and Westport Power Inc., has been producing liquid natural gas ISX engines for years, and the ports of Los Angeles and Long Beach plan to spend $1.6 billion on Kenworth T800s equipped with these engines as part of its Clean Truck’s Program. Pacific Gas and Electric in San Francisco also has purchased some of these vehicles and is the nation’s first utility to operate Kenworth T800 LNG-powered vehicles.
These are basic Cummins designs with altered fuel injection. Medium-duty Cummins natural gas engines include a spark ignition system and a different combustion chamber.
Because natural gas cannot be liquefied by pressure alone, such trucks require heavily insulated tanks – designed like thermos bottles – that keep the gas liquiefied at about minus 250 degrees Fahrenheit. LNG supplier Clean Energy runs fueling stations around major cities in various areas, including Southern California and Texas. Fueling is fast. Both saddle tanks can be filled with a single connection on one side of the truck.
The well-insulated tanks retain the fuel without a significant pressure increase, although if the truck sits for seven to 10 days in warm weather, the tank may vent a small amount of gas.
Testing has confirmed the integrity of the tank even when dropped eight stories. How about a severe, T-bone crash that could rupture a tank? Because the gas is lighter than air, it would rapidly escape skyward, making an explosion unlikely, says Jonathan Burke, a Westport Power vice president.
The Westport HPDI (high pressure direct injection) system on the ISX closely resembles a diesel injection system. Its biggest advantage: it allows the engine to run without an air throttle, similar to a diesel, and with normal torque, which can be limited by knock in other natural gas engines. It has a special injector that handles both diesel and natural gas, but uses the same piston and combustion chamber as a standard ISX, giving the same compression ratio.
Someone running a Westport LNG truck couldn’t abandon diesel entirely. The system relies on diesel fuel for ignition because natural gas has an extremely low cetane rating and would not ignite under normal compression. No more than 7 percent of the total fuel used – and 5 percent on average – is diesel, however, and you have to refuel the small diesel tank only about every week to 10 days, Burke says.
The gaseous fuel is injected at 4,500 psi at a point in the cycle typical of a diesel, beginning after compression is almost complete. It is this unusual feature that allows the engine to run with normal diesel torque and efficiency. Maximum U.S. ratings for these engines are 450 hp with 1,550 lb.-ft. to 1,750 lb.-ft. in a multi-torque arrangement. An Australian version produces 580 hp and 1,850 lb.-ft.
Compared with a pre-2007 diesel, Westport’s LNG engine reduces NOx by 40 percent to 50 percent and particulate by 80 percent. Greenhouse gases are reduced by 20 percent to 25 percent. The 2007 version marketed today is certified to meet the current EPA rule, complete with a diesel particulate filter and the standard levels of cooled exhaust gas recirculation.
Because natural gas burns so cleanly, extended oil changes may be approved as the company accumulates more experience and does oil analysis, Burke says. Since the gas costs 30 percent to 40 percent less than diesel fuel based on energy content, the engine provides a significant fuel cost savings, he says.
So far, this engine has been sold only to fleets. A program to offer the unusual engine to owner-operators running Class 8 rigs will begin early next year, when Kenworth starts production of trucks equipped with the ISX natural gas engine at its plant in Renton, Washington, says Kenworth spokesman Jeff Parietti. At present, the engines are modified for natural gas elsewhere.
Owner-operators using these vehicles will need to operate close to one of the Clean Energy LNG refueling stations, most of which are near large ports or airports. The ports of Los Angeles and Long Beach will offer subsidies to help finance new vehicles to encourage use of low-emissions, alternative-fuel trucks.
Cummins-Westport also is producing a smaller, 8.9-liter natural-gas engine called the ISL G. It’s classed as medium duty, with up to 320 hp and 1,000 lb.-ft. of torque – more torque than hauled some Class 8 loads in the ’70s. It runs like a car engine, using spark ignition and “stoichiometric” combustion, which means that all the oxygen in the air is used up by the burning fuel. High levels of cooled EGR help lower NOx, but the engine also uses an automotive-style three-way catalyst that reduces hydrocarbons, carbon monoxide and NOx. This engine already meets 2010 diesel standards.
Natural gas provides dollar savings in these engines, too, though their lower efficiency makes the savings less dramatic than in the ISX.
Other biofuels
While Volvo Trucks North America neither produces nor markets alternative-fuel engines, the parent company staged an interesting demonstration in Brussels in September. It rolled out seven heavy-duty trucks, each of which used a different renewable biofuel, including biodiesel, biogas, dimethyl ether, synthetic diesel, hydrogen gas and ethanol/methanol.
The point was that Class 8 trucks clearly can run on everything from fermented sugar cane to sewage gas; the problem is that petroleum refining and distribution systems are not designed to provide us with these boutique biofuels.
At the Washington International Renewable Fuels Conference held in early March, Volvo detailed the engine modifications needed for some of the fuels such as ethanol and dimethyl ether. Ethanol and methanol require a cetane improver, jacket water charge air cooling in place of air-to-air, and a 24:1 compression ratio. Dimethyl ether needs a low pressure, common-rail injection system and slightly pressurized tank, but the engine produces more torque than with standard diesel fuel. Mack Trucks showed off a dump truck equipped with a hybrid system powered by a flywheel generator and turbine-generator. The system saves fuel by helping with acceleration and powering the engine accessories more efficiently.
“The technology exists, but we need the fuels,” said Leif Johansson, chief executive officer of the Volvo Group, at the Washington event.
Any of these fuels could prove to be useful in heavy trucks, in Volvo’s view, but their widespread acceptance will depend largely on political and economic decisions affecting their availability.
Hybrids
Various kinds of hybrid technology are being rapidly developed, and a few even are finding their way into medium-duty trucks used in urban service.
Research by Eaton Corp. has shown that a hybrid drive consisting of a large bank of batteries and a motor-generator mounted at the flywheel can prove quite useful even in an over-the-road Class 8 operation. When drivers cruise down level interstates, they often brake and then accelerate. Hybrid systems could recover this energy rather than throwing it away.
The technology also can be used to greatly reduce clutch wear by using the powerful motor-generator for initial starts, especially when on a steep hill. It may even be adapted to provide power for the sleeper while the truck is shut down overnight, supplementing or even eliminating the need for an APU.
Biofuel benefits still hotly debated
Critics of the biofuel craze have argued that producing a gallon of some biofuels actually consumes more than a gallon of fossil fuels, due to the associated costs, including refining and crop production.
The National Biodiesel Board argues on its website (www.biodiesel.org) that this is not true of U.S. biodiesel, production of which gains 3.2 units of energy for every unit of fossil energy put in. “Biodiesel reduces net carbon-monoxide emissions by 78 percent compared to petroleum diesel,” the board says.
A paper published in National Resources Research claims “that biodiesel production requires 27 percent more fossil energy than is present in biodiesel.” A paper called “Biodiesel Energy Balance” by two University of Idaho researchers says the NRR paper has seriously flawed methodology and “leads to an absurd result.”
A 2006 study published by the National Academy of Sciences found that switching from petroleum diesel to soy-based biodiesel reduces greenhouse gases 41 percent, versus only a 12 percent reduction for corn-based ethanol – but that neither can replace much petroleum without seriously cutting into the U.S. food supply. If every ear of corn and soybean in the United States were turned into biofuel and poured into our engines, the study said, it would replace only 12 percent of U.S. gasoline demand and 6 percent of U.S. diesel demand.
‘The right thing to do’
Here are a few of the fleets, large and small, that are on the cutting edge of testing alternative fuels’ suitability for trucking.
STATES LOGISTICS SERVICES of Buena Park, Calif., decided to fuel its Class 8 trucks, all Internationals with ISM engines, with B99 – 99 percent biodiesel to 1 percent petroleum diesel. “Reduced emissions was the key motivation in our decision,” says Matt Montford, sales manager. “Our drivers report that the engines are quieter, are smoother to operate, and there’s no black smoke.” The move also “sets us apart as a forward-looking business,” Montford says. “We believe it’s the right thing to do.”
EASTMAN CHEMICAL of Kingsport, Tenn., upgraded 200 trucks to 30 percent biodiesel after two years of successfully running on B20. “It was an excellent opportunity to do something beneficial for the community and the environment at the same time,” says Darren Curtis, an Eastman staff engineer. Drivers love the performance and decreased odor and smoke.
SAFEWAY converted its entire fleet of more than 1,000 trucks to biodiesel fuel, and every truck now sports a green sticker with a soybean leaf and the words, “Powered by Biodiesel: Clean, Renewable, Domestic.” The grocery chain says this change, in terms of pollution, is the equivalent of taking almost 7,500 cars off the road.
UPS ordered 167 compressed-natural-gas delivery trucks for operations in Atlanta, Dallas, and the California cities of Fresno, Los Angeles, Ontario and San Ramon, beginning in 2009. They will feature Cummins-Westport engines on Freightliner custom chassis and are expected to yield 20 percent fewer emissions and 10 percent better fuel economy than 2007 diesels.
The company’s global alternate-fuel fleet totals 1,629 vehicles, including CNG, propane, electric and hybrid electric, says UPS spokesman Ralph Caldwell. Also, biodiesel will be adopted for ground support vehicles at the company’s Worldport air hub in Louisville, Ky.
CHRISTIANSEN BROTHERS, a heavy hauler based in Spanish Fork, Utah, converted to fuel refined by Better Biodiesel. The reasons include lower emissions and maintenance costs, longer life for equipment and the allure of renewable energy, says CEO Lew Christiansen.
SMITHTOWN, N.Y, requires the independent contractors who collect the town’s garbage to use compressed natural gas, rather than diesel fuel, saying that diesel costs too much and pollutes too much. To make it easier for the contractors, Smithtown and fuel supplier Clean Energy have agreed to set the prices at $2.33 per diesel gallon through 2008, with yearly increases up to $2.94 DGE (diesel gallon equivalent) in 2013. Four contractors, all on seven-year contracts, will use a federal alternative-vehicle tax credit to offset up to 80 percent of the cost of the new trucks.
DECKER TRUCK LINE of Fort Dodge, Iowa, is testing B20 biodiesel in 10 trucks in a two-year study in partnership with the Iowa Central Community College, the National Biodiesel Board and the U.S. Department of Agriculture. So far, the biodiesel trucks average a tenth of a mile per gallon less in fuel economy, but that difference could be the result of driving techniques, says Donald Heck, the college’s director of biotechnology.
Diesel’s other cocktails: ethanol – or even water
For quick and easy ignition, diesel engines need a fuel with a high cetane level, meaning it’s easily fractured by heat. The fuel also needs to be a heavy liquid with a high lubricity. For this reason, most automotive engineers believe that ethanol may be a fine fuel for cars but is unsuited for a diesel. O2Diesel, a Delaware company, has bucked the conventional wisdom by developing a diesel-ethanol blend anyhow.
The trick to making this blend work in either a medium or heavy truck engine is additives. O2Diesel’s blend consists of 7.7 percent ethanol, 91.7 percent diesel fuel and 0.6 percent additives. The additives keep the ethanol, which is much lighter than diesel fuel, fully mixed, and ensure that the cetane rating is at least as high as the base diesel fuel, while adding lubricity to bring the level to 40 percent above the base fuel.
The company also offers O2-B20, which substitutes for the 91.7 percent diesel fuel a blend of 20 percent biodiesel and 71.7 percent petroleum diesel.
The company says its test of O2Diesel in a 1991 Series 60 Detroit Diesel engine reveals 4.3 percent less carbon monoxide, 0.9 percent less NOx and 20 percent less particulate compared to ultra-low-sulfur diesel.
Moreover, less soot produced in combustion means less soot in the oil, which means longer change intervals, the company says. It also could reduce a fleet’s carbon footprint significantly since the fuel contains less carbon than straight diesel, and the carbon the ethanol adds to the exhaust will effectively be recycled into the next crop, the company says.
Fleets with as few as seven vehicles are now using the fuel, but their drivers would need to do their own fueling at a central location, says Mark Jorgensen, O2- Diesel sales development manager. The product is blended by certified petroleum jobbers who supply it to the fleets’ tanks.
O2Diesel costs slightly more than straight diesel right now, but as the cost of straight diesel goes up, there soon may be parity between the costs of the two fuels, Jorgensen says. The fuel also “appears to resist jelling better than regular diesel” and easily can be kept winter-ready with standard anti-gel additives, Jorgensen says.
About the only inherent disadvantage is that the blend has a lower flashpoint than diesel fuel and thus must be handled with the same precautions as gasoline.
An even more unusual fuel blend is Purinox, a combination of 80 percent petroleum diesel and 20 percent purified water. Water in the fuel tank normally would give one pause, as it could ruin the engine. But not with the co-solvents developed by the Lubrizol Corp. The company claims they keep the water fully dissolved in the fuel so that it doesn’t separate or settle out even when left in the tank for a month.
It sounds counter-intuitive that water would make diesel fuel burn better, but the basic idea has been around for a long time. Large power stations frequently use high-pressure steam to atomize heavy oils, and combustion is much better with steam than when using fuel pressure alone. But Purinox flopped in the United States and now is sold only in Europe.