Innovative approaches to drivetrain design promise more efficient highway cruising.
Volvo recently shook up the standard view of how a drivetrain should behave.
The truck maker introduced the XE13 option, a system combining a Volvo I-shift automated 12-speed overdrive transmission with axle ratios in the range of 2.64-2.69:1. This gives a 65-mph cruise rpm of 1,150 rpm, a little more than 200 rpm lower than most trucks built today, even when they have conservative gearing.
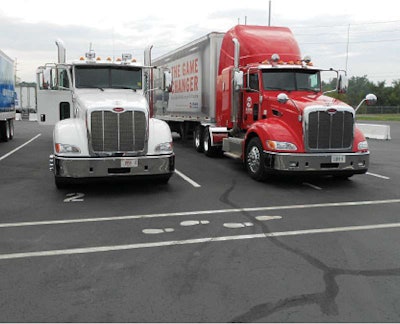
Volvo calls the concept “engine downspeeding.” It’s among new developments from drivetrain manufacturers aimed at using less fuel to maintain desired highway speeds.
The XE13, equipped with a 425-hp engine producing 1,750 lb.-ft. of torque, incorporates “modified software.” What this means is the XE13 drivetrain produces good performance by downshifting at a higher road speed when climbing a grade, says Ed Saxman, marketing manager for Volvo Drivetrain. It downshifts at a speed that is adapted to fast gearing – typically, he says, at about 58 mph when geared for the most fuel-efficient 65 mph cruise.
Long-haul drivers tend to prefer manual drivetrains that will pull hills without frequent downshifts. Give the engine enough torque, the right torque curve and the right rear axle, and the truck will climb most hills even when staying in top gear. Thus, trucks are normally geared for a cruise rpm that represents a compromise between efficient steady-state cruising and the ability to climb hills without a shift.
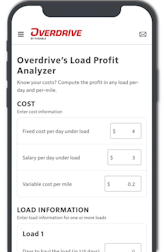
A truck geared for 65 mph cruise at 1,370 rpm can normally drop down at least to 1,100 rpm before the driver needs to shift. With a typical 10-speed transmission geared for 1,370 rpm at 65 mph, the driver would not have to downshift until reaching about 52 mph, or 1,096 rpm.
Part of the recipe for making the standard drivetrain a pleasure to drive is the significant difference between the cruise speed and the first downshift point. Another part of it is the relatively high horsepower produced by compromise gearing, typically a rear axle around 3.40:1. This results from the additional 220 rpm versus the cruise rpm of Volvo’s XE13, for instance.
Allison Transmissions this year will introduce an exotic 10-speed, twin-countershaft automatic that incorporates a similar drivetrain concept, with a couple of interesting tweaks. Allison’s TC10 TS will get its 10 speeds by combining a five-speed main box with a two-speed range box, just as standard 10-speed manual transmissions do. It will, however, use a torque converter in place of a clutch, and shift between gears with the hydraulically actuated clutches of other Allison automatics. The torque converter will lock up at about 4 mph and then behave like a standard engaged clutch to save fuel.
The TC10’s torque converter will multiply the engine’s output torque by 1.76, allowing a powerful start while the transmission’s gearing provides a 7.4:1 first gear, significantly faster than the equivalent gear in standard 10-speeds. They normally have a first gear in the range of 11:1 if top gear is an overdrive. (The first gear in the overdrive versions of Volvo’s I-shift is 11.73:1.) This means the gearbox can have closer steps than other 10-speeds without having more gears.
Also, the 8-9 and 9-10 shifts in the TC10 will have narrower steps than the lower gears. The Volvo 12-speed I-shift has consistent steps of about 28 percent, while the Allison’s 9-10 step is 17 percent and its 8-9 step is 24 percent.
This means that the Allison will cruise in 10th gear at the chosen cruise speed, say 65 mph, but can downshift to 9th without a drop in vehicle speed if the driver demands more power for acceleration or hill climbing with a significant increase in throttle. With such narrow steps, this occurs without revving the engine enough to get the rpm above the sweet spot. The result is that while steady-state, level road cruise will occur at an unusually low rpm, the drivetrain remains quite capable of delivering normal, or even superior, responsiveness.
Todd Dygert, Allison’s TC10 specialist, estimates the rear axle ratio the transmission will use in over-the-road, linehaul applications at about 2.64:1 with the transmission’s 0.86:1 overdrive. The I-shift, Saxman says, uses 2.64-2.69:1 rear axles with its 0.78:1 top gear, depending on whether the truck is a 6×4 or a 4×2 single-drive-axle tractor.
To hold cruise speeds pulling hills with an automated drivetrain that incorporates engine downspeeding, the transmission must be able either to downshift as soon as power is demanded, as the Allison does, or earlier than a standard 10-speed would when shifted manually. In the second case, the engine must also deliver full torque down to a lower rpm. Because the I-Shift has 12 speeds, it has narrower steps than a 10-speed, which helps keep the engine in the sweet spot.
Saxman says the Volvo XE13’s 425-hp rating hides the fact that the engine produces constant torque until it’s turning more than 1,500 rpm, behaving like the Volvo engine’s maximum rating where the truck cruises and holding that torque down to a lower rpm.
So an automated drivetrain with an ultra-fast rear axle is practical because of more frequent downshifts and, best of all, the operator doesn’t have to do that shifting.
Addressing low rpm’s torsional vibration
One potential problem with chugging along at lower rpms is torsional vibration in the transmission gears or elsewhere. This can create noise or even accelerated wear. The problem arises because of differing vibration frequencies — the drivetrain equivalent of the opera singer holding a certain note to make a glass shatter.
Eaton has taken a further step, Shane Groner says, to adapt the clutch dampening system to the new conditions. “Our clutch designs will have larger springs because the peak of torsional vibration passes right through the sweet spot under cruise conditions,” he says.
When it comes to vibration problems, Volvo’s Ed Saxman says, “Our engine has a stiff bottom end, which helps. And we have a viscous damper on the camshaft. This reduces the stress on all the components from vibration transmitted from the engine. ”
The “input damper” on Allison’s TC10, says Todd Dygert, “was specifically designed based on our plan to run at very low engine speeds.”
Cummins anticipates no problem with torsional vibration, says Cummins’ Bill Kendrick. However, “engine mounts and torsional dampers are designed to limit vibrations within specific frequency ranges and lower engine speeds may reduce the effectiveness of these components. In light of that, Cummins is working with powertrain suppliers and vehicle manufacturers to ensure the entire system is well designed. Different components may be required for a specific vehicle.”
With Detroit Diesel, “Significant measurable fuel efficiency benefits are available” from configurations already tested, says Brad Williamson, director of engine and component marketing for Detroit owner Daimler Trucks North America. Detroit is “evaluating the correct driveline specifications for even more significant downspeeding,” he adds.
Another concern is the possibility that running at low rpm could cause problems with combustion and create deposits or higher emissions. But Dygert notes that the “‘on again, off again, on again’ transient cycles dictated by the power-interrupting shifts” of transmission systems in prevalent use today keep the typical turbocharged diesel from operating optimally. “Allison powershifting keeps the engine under a relatively constant load,” he notes, suggesting a boon to emissions reduction.
Kendrick says Cummins designs engines to operate at lower speeds. “When operated as designed, these engines will be fully emissions compliant. We do not anticipate any reduction in reliability or durability as a result of lower speed operation.”
Detroit Diesel is too early in its test process “to tell what effects this type of set-up will have on deposits, etc.,” says Williamson. “But we can say our engines do perform well in a set-up of this nature and continue to meet/exceed emissions standards, maintain good combustion and deliver leading fuel economy.
“Simply lowering the engine cruise rpm on existing products does bring an efficiency advantage, but to perform correctly and get the most benefit a system approach is needed. Only when the system is optimized are other tradeoffs like driving performance, durability, and reliability avoided. We currently do not see any issues when the system and its shift points are managed correctly.”
Ed Saxman says Volvo’s engine, which already has low soot, should eliminate any potentially adverse effect of downspeeding. “With ultra-high pressure fuel injection, we can burn all the fuel, and it is difficult to measure the soot in engine exhaust,” even before the diesel particulate filter, he adds. “There should be no soot issues relating to cruising at a low rpm.”
‘Downspeeding’ speeds up
Will drivetrains incorporating “engine downspeeding” become a trend? For Eaton Corp., the answer is a resounding, “Yes.”
The company’s automated transmissions already depart from the traditional single cruising gear concept, says Shane Groner, Eaton’s manager of development and product planning. Its Ultrashift and Ultrashift Plus II products have included a “kickdown” feature for acceleration since 2005. They respond to driver demand by dropping down from top gear at highway speeds, as acceleration becomes more important to the operator than efficient cruising. Groner refers to this as “modulating capability,” meaning the transmission can shift up and down in an orderly manner in response to changing throttle demand.
“We’ll be seeing new products incorporating engine downspeeding technology within a year,” Groner says. “They will provide new, small gear steps in the range of 17 percent, giving a change in rpm after a shift in the range of 250-300 rpm or even less. We have a number of ratios in our arsenal that we can use to accomplish this and already have the required modulating capability in our boxes. The idea is to squeeze more miles out of the fuel.
“We can provide several designs to meet different applications, including both overdrives and direct drive units, and both 10-speeds and multi-speed, small-step units.” Groner notes, “There’s no putting one design into every application.”
Multi-speed units are the 13-and 18-speed boxes with splitters. Such units are intelligent enough to split the gears to keep the engine in the sweet spot during subtle changes in highway cruise conditions, yet shift full gears for faster acceleration when the truck is getting up to highway speeds, Groner says. Such units are in field testing with Paccar and Detroit Diesel.
Fuel economy and torque output improve when running at 1,150 rpm rather than 1,375, says Volvo’s Ed Saxman. “This means the engine puts out more power from each ounce of fuel, so customers gain about a 1.5 percent fuel efficiency improvement for every 100 rpm of ‘downspeeding.’ So fleets that spec XE13 can expect up to a 3 percent improvement when compared to another overdrive transmission in a similar operation.”
About Allison’s TC10, Todd Dygert notes that it’s “been shown to offer better fuel economy than automated manual transmissions in customer trials using real-world duty cycles.” Fuel economy improvements in fleet tests ranged from 3.3 percent to 11 percent.
Allison contends the powershift concept — the avoidance of de-throttling the engine during shifting — saves fuel by eliminating the dead period during shifts when the engine and drivetrain turn over but produce no power. The lower cruise rpm is a large contributor to these savings, however.
Fuel economy gains at lower speeds are a “result of reduction in parasitic losses,” notes Bill Kendrick, Cummins’ assistant chief engineer for vehicle performance. This refers to the reduced energy required to turn the engine over and operate the oil pump, water pump and other accessories.
Sweet spot vs. speed range
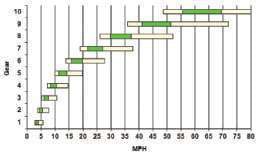
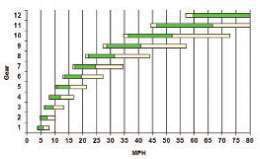