Attention to electrical system maintenance will prevent a no-start or sudden loss of power — and extend alternator life.
The alternator connects the engine and the electrical system. It converts rotating power from the crankshaft to 14-volt current to charge the batteries and operate all lighting, gauges, the engine ECM and the electronic portion of the injection system. The starter plays the reverse role, converting the battery’s stored electricity into cranking power.
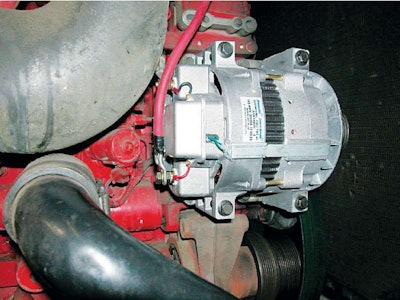
While the alternator is fairly trouble-free, its function and long life depend on battery maintenance and the maintenance of all the wiring and ground systems that ensure low-resistance electrical circuits. A certain electrical system symptom can signal a problem in one or more areas, so maintenance and troubleshooting should not be restricted to one or two components.
Battery maintenance
Alternator maintenance is more about maintaining the batteries than the alternator itself. A good alternator lasts almost forever, but only if it doesn’t overheat. One good way to prevent such overheating is to keep the batteries working efficiently.
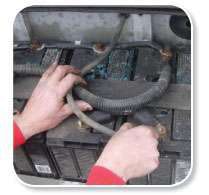
The alternator’s main job is to handle the vehicle’s electrical load, calling on 75 percent or more of its output. New batteries and good wiring reduce battery charging needs, making life a breeze for the alternator. As batteries and cables develop resistance, the alternator works harder and longer to replace what’s used for starting or supplying overnight shutdown loads.
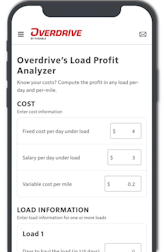
Testing batteries once a year, preferably just before the weather gets cold, is critical.
Testing reliable start power
1. Disconnect the cables to isolate the batteries.
2. Use a carbon pile load tester – a big electrical resistance – to put half the rated load on each.
3. Check the output voltage for 20 seconds of continuous loading with a voltmeter. If the voltage stays at or above 9.5 volts for more than 20 seconds, the battery will get you started.
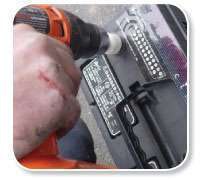
Voltage on a battery that is close to failing will fall off by the end of 20 seconds. If any battery fails this test, replace the entire set to ensure long life. You can inexpensively have this test done at a dealer or repair shop if you can’t do it yourself.
While this test will help ensure reliable starts, it’s harder to determine whether batteries are gradually starting to tax the alternator by losing their reserve capacity, notes Bruce Purkey, president of Purkey’s Fleet Electric. He suggests two ways you can check on this:
Testing reserve capacity
1. Establish a baseline for good batteries by testing them when new.
• Turn off the engine. Measure battery voltage.
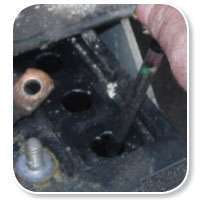
• Turn on headlights and let them drain the batteries for 30 minutes. Retest the output voltage and record the reading.
• After a year or two, you can repeat the test. After 30 minutes, if voltage drops more than when new, it shows a reduction in reserve capacity.
2 Carefully monitor battery performance while shut down overnight if you have an inverter with a low-voltage cutoff. If your typical overnight load is fairly constant, note how long it takes to get a low-voltage warning or cutoff. When that interval becomes significantly shorter, it’s time to replace the batteries.
Conventional batteries require regular addition of distilled water. Keep the cells filled for maximum performance and life, doing so once a month. When doing your monthly check of electrolyte level, carefully wipe off the top of every battery. Do this for maintenance-free batteries, too. Keeping batteries clean reduces the loss of charge during shutdowns.
Conventional batteries have the advantage that the density of the electrolyte liquid in the cells can easily be tested with a hydrometer. Remove the cap from each cell, draw a sample of electrolyte into the hydrometer, and watch what the indicator balls do. If they rise to the top of the fluid, the cell is charged. If they sink, the cell is bad, and the battery should be replaced. Always return the electrolyte to the cell once tested. Testing every six months is an excellent way to anticipate battery trouble.
Maintenance-free batteries have an indicator that changes color when they deteriorate. Check your owner’s manual for a description of how the indicator should look. When its color changes, have the battery checked and, if necessary, replaced.
More battery PM tips
• Clean and tighten connections. Twice a year, disconnect all the battery connectors and use a powered brush to clean both the inside diameter of each connector and the post. Reconnect all connections securely and then protect them with di-electric grease or a spray protectant. Note that typical, soft lead connectors continually stretch. Tighten the fastening bolts once a month to ensure maximum conductivity, or get plated brass connectors that are much harder.
• Beware cold temps. Cold weather affects a battery’s ability to give up stored power and to allow recharging. “A battery will lose 35 percent of its cold cranking amps at 0 degrees Fahrenheit,” Purkey says, “so you need a full battery charge to ensure reliable starting. Also keep in mind that a jumpstart may not be enough to get the truck ready for a shutdown even a few hours later. At cold temperatures, it can take as long as two days for batteries to become fully charged.”
This means connecting the truck to a battery charger is the best way to get the truck back to reliable operation, says Tim Ruth of Warehouse Battery Outlet. “To bring a discharged battery to its full 12.6-volt charge, charge it at a low rate for 18-24 hours, not just 2 or 3 hours,” he says.
Wiring maintenance
Purkey says many a battery cable has been the real culprit when truck owners believe they have a charging or battery problem. So when checking your batteries before cold weather, inspect the cables, as well. The Technology and Maintenance Council’s Recommended Practice 129 calls for a voltage drop of 0.5 volts or less at 500 amps of current flow. If the voltage drop is greater than this, the cable needs to be replaced.
However, you can’t tell much by just putting a voltmeter on connections because resistance doesn’t show up until there is high current. So Purkey recommends having a professional test each cable with a special instrument that uses electronics to measure resistance. In four seconds a technician can tell whether a cable needs replacement.
Alternators and heat
As the wiring inside the alternator heats up, resistance increases, reducing the unit’s output. The windings inside have insulation and soldered connections that are sensitive to heat. As loads increase beyond what the unit was designed for, it can fail. An unusual load can have the same effect as inefficient batteries, producing a snowballing effect that means long hours at maximum loads, overtaxing the alternator.
You could also do this yourself. Measure voltage at the starter positive connector while the engine is being cranked by someone else. Then take a similar measurement at the battery positive terminal and subtract the first reading from the second. “It makes a lot more sense to replace a $4 battery cable than an $80 battery when the cable is actually the problem,” Purkey says.
He also recommends checking wiring quarterly, or whenever you see corrosion starting to develop. “If you can see green, there is more of it from corrosion that is still invisible,” he says.
More wiring PM tips
• Starter and alternator positive and ground connections and any ground wires on the chassis need to be checked to ensure connections are clean and tight. Inspect and, as necessary, clean any wiring connections, whether voltage or ground. You can clean the contacting surfaces with an abrasive like sand paper. Then reinstall fasteners tightly, replacing them if corroded.
• Inspect all wiring for cracked or frayed insulation or rubbing against other parts. Repair bad wiring and protect it by using ties to keep it away from surrounding surfaces.
Alternator cooling system and belt maintenance
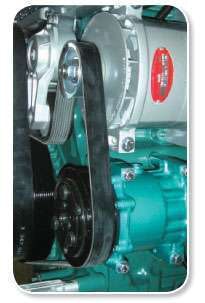
Your alternator has a cooling system – a fan that forces air through passages in the windings. This airflow keeps resistance low enough for good output, and protects perishable insulation and internal connections unless threatened by dirty fan blades or clogged passages, Purkey says. The problem with the alternator’s location is that small oil leaks are common in the engine compartment. The dust sticks to the layer of oil, eventually coating the fan blades and possibly clogging the cooling passages.
If you see oil on the alternator, trace it back to the source and fix the leak. Then carefully clean the fan blades and air inlets in the body of the alternator with a clean rag to restore airflow.
Since the diesel is the truck’s ultimate source of power, it’s important to keep the belt system that spins the alternator in tip-top condition. Since belts depend on tension for the friction that makes them effective, check the tensioning mechanism and the alternator’s mounting system.
Testing belts and mounting system
1. Put a wrench on each alternator mounting bolt and on any adjustable bolts that allow belt tension to be adjusted to make sure every bolt is snug. Also, look at the alignment of the pulleys to make sure the alternator and any tensioner or crankshaft pulley grooves are straight across from one another. If the back of the belt bends sideways in either direction as it comes out of the pulley groove, either the accessory itself or some other part of the system is loose or has a bent bracket or one of incorrect design. Distorted or incorrect brackets need to be replaced, as do missing bolts.
2. Inspect each belt, looking for cracks on either the outside band or inside where the belt rides in the groove. Look carefully at the friction surface on either side of the V-shaped area. If there is any sign of cracks, or if these two surfaces are smooth from slippage, known as “glazing,” the belt should be replaced. Where serpentine belts that run around several accessories are used, check for the same kinds of cracks and glazing, plus for fraying that starts at the outside edges and works its way toward the center. Also, check to see the belt is clean and dry. If it is oil-soaked, replace it and fix the oil leak. Replace pulleys that are so old they have grooves in them where the belts ride.
3. Test the tension of all belts that are manually adjustable with a tension gauge. You can look up required tension in your owner’s manual. Experienced do-it-yourself technicians can test tension with a thumb. You should be able to depress the belt a half-inch to three-quarters of an inch for each 10-inch span between pulleys. The belt should be snug, but slightly springy – not rock solid. Adjust the tension if necessary by loosening mounting and adjusting bolts, rotating the accessory with a socket drive to get the right tension, then retightening the bolts.
4. If the accessories are driven by a serpentine belt, the system will have an automatic tensioner. Check to make sure the tensioner’s indicator line sits between the two lines nearby on the block. If the indicator is outside the other two lines, then either the tensioner is weak or the wrong-size belt has been installed. Either condition makes it impossible for the tensioner to do its job. If there is some tension on the belt but the indicator is not where it should be, replace the belt with one of the correct length.
5. To check the tensioner itself, turn it away from the belt with a socket drive to remove tension, then disconnect the belt. Now use the drive to slowly rotate the tensioner from its neutral position all the way inward. If you feel any roughness or excessive friction, the tensioner’s damper is worn and the unit should be replaced. Replace the belt and start the engine. If the tensioner is working properly, the belt will operate smoothly. If the belt vibrates and the tensioner does not remain in a relatively stable position, this is another sign the tensioner’s damper is worn and should be replaced.