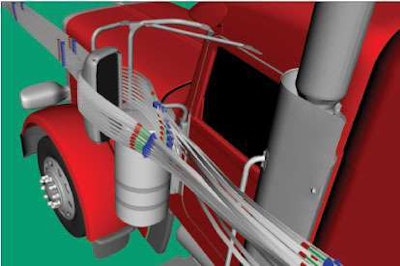
If you want to know whether aerodynamic devices help fuel economy, ask Greg Decker, an owner-operator based in Calgary, Alberta. He’s installed aerodynamic equipment on his 2008 Volvo 780 tractor and 2002 Utility 3000R refrigerated trailer.
Decker, who has meticulously tracked his fuel performance after every tankful for seven years, says his commitment has made a difference. From Aug. 4 to Sept. 30, 2008, he got 6.05 miles per gallon. During the same period this year, his mpg was 6.81. He credits the Windyne Flex Fairings he had installed on his trailer this past summer.
Decker, leased to Caneda Transport, says he previously added aerodynamic mud flaps and airflow tabs to improve handling and curtail road spray, as well as get better fuel economy. “If there were other ways to improve, I would try,” he says.
A combination of higher fuel prices and equipment-altering regulations has the potential of changing how and where truckers will operate. Regulations planned by the California Air Resources Board will eventually require aerodynamic technologies, as well as low-rolling resistance tires, for all trailers that run in the state. All of this stands to change the intensity of owner-operators’ focus on their rigs’ aerodynamics.
Truck aerodynamics got little notice until the oil embargo in the early 1970s led to shortages and sharply higher fuel prices. In 1974 a federally funded study examined wind drag on a cabover with a 45-foot trailer and five add-on devices. Interest waned, however, as oil prices declined.
Beginning in the mid-1980s, truck manufacturers introduced more aerodynamically styled models. Most owner-operators, however, remained loyal to their boxy-hooded vehicles as fuel prices stayed low. More aerodynamic truck models emerged in the 1990s and the first of the trailer components designed to redirect airflow soon followed.
But cheap fuel kept demand weak for the trailer devices, at least until the 2008 summer. “At $1.25 fuel, who wants to save a percent or two [on fuel economy] and spend a couple thousand dollars and have maintenance issues of these things getting banged up?” says Bob Tichelman, president and CEO of Windyne, the maker of sliding trailer fairings used by Decker. “With fuel hitting $5, everybody woke up to the fact that 2 percent of $5 fuel is something.”
Tractor tactics
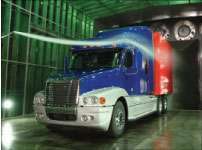
To take advantage of the heightened aerodynamic engineering of the past decade or so, your best move is spec’ing an aerodynamically styled model when you buy new or finding a used aero model.
In designing an aerodynamic model, the primary goal is to reduce air drag around the front, through the radiator and along the sides and roof. Likewise, engineers strive to provide air a smooth transition to the trailer, says Keith Harrington, product marketing manager for Freightliner.
“When you make changes to parts of the truck, it affects the rest of the truck downstream,” says Andy Zehnder, on-highway marketing manager at Kenworth. “When you tweak a bumper or change a headlight, how the air interacts with that component can change the overall interaction.”
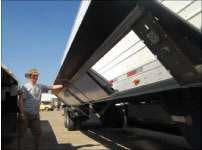
As for retrofit items, at the top of the list are full roof fairings and cab side extenders. Jerry Warmkessel, Mack highway products marketing manager, estimates an aerodynamic package of roof fairings and cab extenders on the tractor could generate a fuel mileage improvement of 8percent to 10 percent and cost about $2,500 to $3,500.
Chassis side fairings can cost up to $2,400 and yield a 2 percent fuel saving.
Rick Mihelic, Peterbilt Motors’ engineering systems manager, cautions that if you start adding aerodynamic items one at a time, you may or may not get the performance gain advertised, because the individual pieces are designed to work in concert with each other.
Peterbilt recently introduced a fuel efficiency package with features such as a rooftop air shield and sleeper side extenders to improve aerodynamics by up to 20 percent, which translates to 10 percent better fuel economy.
“That saving can be $4,000 and over annually, depending on fuel prices,” says Landon Sproull, chief engineer. Mihelic says, “Our design goal is to keep payback within one to two years.”
A critical area is the real estate between cab and trailer. “What you’re doing is putting an aerodynamic vehicle in front of a brick,” Mihalic says. “You can completely negate the benefit of the tractor if you run too long a gap.”
Frank Bio, product marketing manager for Volvo Trucks North America, says you can gain 1 percentage point of fuel savings for each 10 inches you decrease the tractor-trailer gap. For many operators, this will require little monetary investment, if any. Sproull suggests a distance of 46 inches or less, as long as trailer movement doesn’t interfere with the cab.
Trailer devices
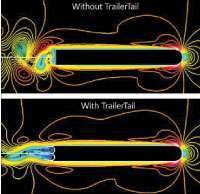
Warmkessel points to the trailer as the “next area of opportunity” for aerodynamic advances. Many fleets and owner-operators are already chasing that opportunity, though the weak economy is blunting business in the aftermarket.
The product that presents the potential for the greatest fuel savings, while typically being the most expensive, is trailer skirting. The idea is to deflect side winds, control airflow beneath the trailer and limit the air turmoil that exists at the back of the trailer on the road. “Without skirts, air gets under the trailer, it creates all kinds of frictional drag,” says Brian Layfield, president of Laydon Composites, a Canadian maker of truck and trailer aero components.
Advertised fuel savings vary from 4 percent to 7 percent. Skirting costs from around $1,500 to $4,000 and up. The more you use your trailer and the higher fuel costs rise, the faster your payback will be. Many of the manufacturers provide calculators on their websites for figuring the savings.
Larry Olson of Camp Douglas, Wis., running under his own authority, began using the AeroFlex last summer. After 20,000 miles, “I was averaging 7 mpg, which is pretty good, but you always want more,” he says. “Since I put on the unit, I’m averaging 7.5 mpg. I’m saving $300 a month in fuel, so payback will be in nine to ten months.”
Windyne’s three-panel Flex-Fairing trailer skirting can be extended from 24 to 35 feet and one of the panels can be flipped up for access to chains, belly boxes, ramp and landing gear. It’s also one of the lowest off the ground, at 6 inches, which increases the surface area for deflecting air. “Extensive testing has been going on because many fleets are dubious of advertised test results,” Tichelman says. “Next year will be a banner year for us because we have concluded our tests with big fleets.”
Silver Eagle Manufacturing takes a parallel-wall approach to its trailer skirting. Since it positions its skirt 18 inches off the ground to avoid banging into curbs, docks and other structures, it installs a second skirt 14 inches in from the outer skirt. “That wall catches air that gets inside the first wall and creates a vortex between the two walls, keeping air from getting beneath the trailer,” says Mark Jurman, sales and marketing vice president. “Wind blows across the tires and out the back of the trailer.”
ATDynamics offers a package of Transtex skirts and a TrailerTail at the back door that achieves fuel savings of 9.5 to 11.5 percent, says Andrew Smith, president and CEO. The package costs $5,000. Smith says the tail helps calm the turbulent airflow at the trailer’s back end and also reduces spray.
Mind the gap
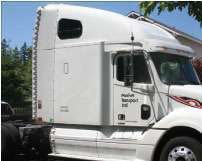
The trailer’s back end and the tractor-trailer gap are aerodynamic hotspots for Airtab LLC. The company designs and makes wishbone-shaped “vortex generators” aimed at minimizing aerodynamic drag when attached vertically at the back of the trailer next to the doors or the sides of the tractor cab. “Each Airtab creates two counter-rotating vortices – like when you pull the plug on your bathtub and the swirl that’s created by water rushing down the drain,” says Jack Latimer, managing member. “We’re basically changing the vertical eddy that rolls down the truck into a horizontal airflow.”
Latimer says the stick-on devices – $2.75 apiece – are popular with owner-operators because they help stabilize the vehicle against crosswinds and provide better side mirror visibility. “Fuel savings is icing on the cake,” he says. “We advertise 2 to 4 percent. One driver we know is right around 4 to 5 percent.”
The trailer front has attracted less competition among manufacturers, in part because aerodynamic tractors and reduced gaps tend to minimize savings that can be achieved. Nonetheless, with a trailer nose cone, an owner-operator can achieve fuel savings of 3.5 percent for a tractor with a full-height roof fairing to more than 7 percent with a mid-roof tractor, says Kathy Rose, vice president sales and marketing for Nose Cone Manufacturing. The cost of $1,100 for an installed cone or $1,500 for a cone and side panels can be recouped within months.
Greg Decker thinks operator attitudes about aerodynamics are changing. “At first a lot of other drivers thought I was nuts when I put on the fairings,” he says. “With the price of fuel going up, I’m now getting calls about what I’m doing.” n
California’s aero mandates for trailers
Impending California regulations could affect how and when trailer owners enhance their equipment aerodynamically. Here’s a summary of the aero-related requirements planned by the California Air Resources Board:
• All 2011 and newer dry van trailers must be U.S. EPA SmartWay certified trailers or equipped with SmartWay-approved aero technologies and low-rolling resistance tires that achieve at least 5 percent fuel savings
• All 2011 and newer reefers must be SmartWay certified trailers or use SmartWay-approved aero technologies and low resistance tires that combine for a minimum 4 percent fuel savings.
• All older dry vans and reefers must meet the same tire and aero technology requirements applied to new models by Jan. 1, 2013, or a phased-in schedule for fleets that ranges between the end of 2010 and 2019.
‘Texas fly swatter’ replaces mudflaps
Aerodynamic benefits can come in the most mundane places. Barry Andersen found fuel savings by replacing mud flaps on tractors and trailers with his Eco-flaps.
The product produces an average annual savings of $1,500 per truck, based on a 3.5 percent mpg improvement and a fuel cost of $2.20 a gallon, Anderson says.
A former owner-operator, Andersen wanted to solve the problem of rain spraying from rigs on the highway. He came up with a quarter-inch-thick flap made of Dupont high-grade nylon that lets water and air through – a design some customers have called a “Texas fly swatter.”
“When the air goes through, that’s how you achieve the savings,” he says. “Every mud flap mounted at the bottom of the trailer is wasting fuel. It’s creating drag.”
Flaps come in two sizes – 24-by-24-in. and 24-by-30-in. Andersen says the key is to allow as much space as possible above the flap for airflow.
Savings with SmartWay
In recent years, the involvement of the U.S. Environmental Protection Agency with its SmartWay program has also refocused attention on aerodynamics and other strategies to improve fuel economy. To learn more about SmartWay commercial partners and potential cost savings, visit www.epa.gov/smartway
Aerodynamic device websites
Airman: www.airmansystems.com
Air Tab LLC: www.airtab.com
Andersen Flaps: www.ecoflaps.com
ATDynamics: www.atdynamics.com
Freight Wing: www.freightwing.com
Laydon Composites: www.laydoncomp.com
Nose Cone Manufacturing: www.nosecone.com
Silver Eagle Manufacturing: www.silvereaglemfg.com
Windyne: www.windyne.com
Smoothing airflow under the trailer
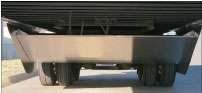
Learning how to redirect air under the trailer became such an obsession with Bob Henderson that he went to Oregon State University and graduated with an engineering physics degree in 2001.
Henderson’s approach is the AirWedge, an aluminum device attached beneath the trailer in front of the axles. Instead of air swirling in back of the trailer and rain spray splashing out the sides, the product moves it out the back. “It rechannels the air underneath the trailer, does a little compression on it and squirts it under the trailer axles out the back and directs it toward the road,” he says.
Henderson hatched the idea while driving a truck in the 1970s and started a company, Airman Inc., to make the product. He runs the company after hours from his day job as an engineer for a metals company.
Tom Severn, an owner-operator from Medford, Ore., had the AirWedge installed on the 53-foot reefer trailer he and his wife pull for Lund Trucking of Chehalis, Wash. Lund owns the trailer, but Severn paid for the device to improve the fuel economy of his 2005 Peterbilt 379.
“Before I put the unit on, I was averaging a solid 5.9 mpg,” Severn says. “Even with this truck, I’ve picked up two to three tenths, depending on the weather and load. I paid $2,500 for it and it paid for itself in six months.
If you can’t get a return on investment between six months and a year, it’s difficult to rationalize spending the money.” He says the device also reduces spray and improves the trailer’s handling by calming down the wind at the back of the trailer.