Once a novelty, inverters are now mainstream over-the-road equipment.
On any given evening in America, truck stop parking lots are filled with truckers enjoying the comforts of modern domesticity, their many household appliances quietly nursing on the undulating AC current of power inverters.
Once a novelty, inverters are now mainstream over-the-road equipment. Fleets use them to recruit and retain good drivers. Truck makers offer them as factory-installed options. Anti-idling laws and the new hours-of-service rule have made them more practical.
Their appeal can be summed up in two words: convenience, economy. For many truckers, the choice is not whether to buy an inverter, but which model to choose. AC-driven appliances in all the latest colors can be found at any discount retailer, whereas their less powerful and more expensive DC counterparts generally are sold only through camping outlets and Army surplus stores.
There are two basic types of inverters: pure sine wave and modified (or quasi) sine wave. The former delivers an electric waveform as good as, and sometimes better than, the output of a utility company. The latter is less expensive but produces a waveform unsuitable for certain devices, such as microwave ovens, laser printers, some digital clocks and cordless tool chargers.
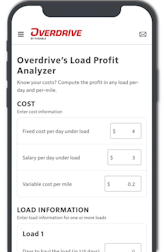
Most people base their buying decisions on power and price. The range in both categories is from 75 watts and roughly $25 to 3,000 watts and $1,000 or more. Unfortunately for many people, this simplistic approach to purchasing often leads to disappointment and frustration, usually because they undervalue quality or underestimate their AC loads.
“We’ve found that insufficient size is the biggest reason our products are returned,” says Brian Lawrence, OEM sales manager for Xantrex Technology in Arlington, Wash. “People will buy a 150-watt inverter but actually need one that’s three or four times as powerful. People commonly think that smaller electrical appliances don’t use much power. That’s not the case.”
Xantrex builds a full line of inverters and is one of the few companies offering a heavy-duty inverter-charger combination. It’s also the only approved supplier for factory-installed units. Lawrence says this segment of the business has grown steadily and rapidly since 2000, when Freightliner became the first truck maker to offer the units as options. Volvo and International soon followed suit.
Factory installs have a couple of advantages, Lawrence says. First, the inverter is covered under the truck’s bumper-to-bumper warranty. Also, the “fit and finish” is usually superior to aftermarket jobs.
“There’s nothing better than running the wires through the walls before the interior panels are mounted,” he says. “Plus, manufacturers do a good job of clearly identifying the wiring,” reducing the chance of mechanics later slicing into the system’s harness.
The number of new trucks spec’d with inverters is still relatively small, meaning that most truckers do the installation themselves. Following are the steps for mounting and connecting an inverter. This information should be used in tandem with the product-specific instructions provided by each manufacturer. The need for safety cannot be overstated in these jobs because they involve a truck’s batteries, which emit explosive gases and contain enough electrical force to instantly toast any metal they encounter, including tools and jewelry.
THE FIX
- MAP OUT THE JOB. Unpack the inverter, its cables and other parts. Figure out where to mount the unit and auxiliary switches or outlets, if they’re included. Inverters should be mounted in an area that’s well-ventilated, dry and accessible, but away from heavy objects that might slide during cornering or hard braking. The location’s distance from the truck’s battery box is also important. Closer is always better. Determine the path for routing cables between the inverter and batteries. Check under (or behind) the panels where holes will be bored, to ensure no submerged wiring or framework is damaged in the process.
- BORE CABLE HOLES. Following the manufacturer’s instructions, use appropriately sized hole saws to cut openings, if necessary, for the inverter’s cables and wiring. Then line each of these holes with a rubber grommet, which will protect the cable from chafing on the metal. Grommets are included with some installation kits. They’re also widely available at hardware, plumbing or auto parts stores.
Not all holes require grommets. Xantrex, for example, uses a “pass-through” plate to route its cables from inside the cab to the great outdoors. The 4-inch weather-tight plate is designed to mount over a 31/2-inch opening. Remove carpeting, padding or rubber mats covering the mounting area before boring this hole. Later, cut the material to accommodate the plate and cables. When you’re ready to secure the plate, apply a healthy dose of silicone sealer or similar product on the mating surfaces to reduce the chance of corrosion between joined dissimilar metals.
- ROUTE CABLES. An inverter’s DC (battery) cables carry a considerable amount of current, so it’s important that the ends be professionally installed, either by the inverter manufacturer or a shop that has the proper crimping equipment. Thread the assembled cables, ground straps and other required wires through your freshly cut holes, leaving them loose and unattached for the moment. Fit cable ends with protective rubber boots. These are normally included in the installation kits.
- MOUNT FUSE BLOCK. Every inverter should be protected with an inline fuse on the positive DC cable, even if the manufacturer claims its products are protected with “internal safety systems.” Better installation kits will include a fuse and holder, which should be mounted inside the battery box. Should you need to buy these pieces separately, choose components that can handle the current load of your inverter model. In most cases, this means something greater than 100 amps. When mounting the holder, allow plenty of room for the cables that will be connected later. Disconnect the batteries’ existing (main) cables, negative first.
- MOUNT INVERTER. Remove carpeting, padding or rubber mats from the inverter’s mounting area to ensure adequate ventilation. Use a template (either homemade or from the kit) to drill the necessary holes. In some instances, you can use the inverter as a template, holding it in place with one hand while using the other to mark the screw-hole locations. Attach all cables and wires to the inverter, then secure it with corrosion-resistant screws. For cargo box installations, it’s wise to protect the inverter with a solidly mounted shield. A piece of sturdy aluminum or stainless steel, custom-bent for your specific application, will prevent damage from sliding heavy objects. Leave plenty of space around the unit for air movement.
- MOUNT AND CONNECT SHORE POWER RECEPTACLE. (Applies only to inverters with shore power hookups.) Find an easily accessible spot to mount the shore power receptacle – ideally, out of the path of wheel spray and reachable from the ground. Follow the manufacturer’s instructions for installing your part. Find the correct cable leading to the inverter and route it to the receptacle, then tightly connect the color-coded wires to the receptacle’s terminals (green to ground, black or red to hot, white to neutral). Coat these connections with a good electrical sealant.
- MOUNT AND CONNECT REMOTE SWITCH. (Applies only to inverters so equipped.) The level of effort needed to mount the remote switch depends largely on its distance from the inverter and the number of upholstery panels that must be removed to route the wiring. Since the switch is intended for convenience, it should probably be located in the area that you’re most likely to inhabit while using the inverter: the sleeper. Often, a sleeper’s own control panel will have enough available space for the switch. It’s a good idea to wrap submerged wires with split-poly loom to prevent chafing against any nearby metal.
- MOUNT INTERNAL AC RECEPTACLE. (Applies only to inverters so equipped.) The wiring issues in Step 7 apply here, too. Beyond that, one of the biggest considerations in mounting an AC receptacle is convenience. It should be located near most of the appliances needing power. This will reduce the number of cords strung across the sleeper compartment. The mounting surface should be reasonably solid, such as a wood or metal framework, to eliminate the chance of ripping the receptacle loose while unplugging something.
- CONNECT AND SECURE ALL CABLES AND WIRES. Follow the manufacturer’s instructions for connecting any remaining wires. The battery should be hooked up last, starting with the positive cable. Use split-poly loom on all wiring and cables that might rub on nearby surfaces, then secure the entire system with plastic wire ties.
- TEST UNIT. Switch on the inverter and make sure all its indicator lights and dials (if applicable) are functioning properly. Plug in a shop light or other low-load AC device and turn it on. Next, connect an extension cord to the shore power outlet to test the inverter’s charger (if applicable). Lacking any unpleasant surprises, the job is done. Regular cleaning is the only maintenance required for most inverters.
TOOLBOX
Combination wrenches
Half-inch socket set
Assorted screwdrivers
Power drill
Drill bits
Hole saw (or similar device)
Ball-peen hammers
Tape measure
Silicone (or similar) sealers
Utility knife
Tape measure
Plastic wire ties
Poly loom
RESOURCES
Cobra Electronics
www.cobra.com
(773) 889-8870Coleman
www.coleman.com
(800) 835-3278Exeltech
www.exeltech.com
(800) 886-4683Samlex America
www.samlexamerica.com
(800) 561-5885Vector Mfg.
www.vectormfg.com
(866) 584-5504Xantrex Technology
www.xantrex.com
(800) 282-8776