What’s below the deck of your trailer can let you down if you ignore it.
While tractors are complex pieces of equipment that come in a variety of shapes, sizes and colors, trailers all tend to look alike to the inexpert eye. And that means they can become an afterthought if you’re careless.
While the upper parts of a trailer are usually similar, it’s what’s underneath that makes the difference; not only between trailers, but also in whether they stay in good enough shape to keep you productively – and safely – on the road.
Sliders, suspensions, landing gear and wheel bearings don’t just keep on keeping on like the battery bunny, they need constant inspection and maintenance if you are to rely on them to keep you rolling.
We spoke with experts in factory service positions and dealer service shops, and we referred to several technical manuals to help you with trailer maintenance.
Why a slider?
Weight distribution is one of the most critical issues for truckers. The weight on each axle must be correct, or roadside inspectors or scale operators will ticket you. Also, the axles need to be far enough apart to satisfy bridge formula requirements. With the ability to move the rear tandems, a trucker can compensate for where his load sits in the trailer. That’s why trailers often have “sliders,” which are movable trailer tandem axle suspension systems. Instead of the springs and hangers or brackets being attached directly to the trailer’s main frame, they are fastened to a sliding subframe that constitutes a complete, movable suspension system.
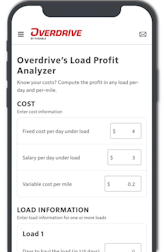
You can shift weight onto the rear tandems by moving the slider forward; or shift it onto the drive tandem by moving the slider backward. The most critical issue with sliders is, of course, locking them in place once the driver has shifted them to the desired position. Proper operation is absolutely critical, but maintenance and inspection are also vital for trailer operating safety.
The typical slider frame has at least four pins that slide through holes in its rails. Rails with numerous holes in them are attached to the trailer body. These locking pins are retracted to move the slider and then extended through corresponding holes in the body rails to lock it in place.
Slider inspection
- Check the slider locking pins, pull bar mechanism and wear pads for signs of wear or binding. Repair or replace parts as needed. Mechanism replacement is normally simple, involving knocking retaining pins out to remove and installing new pins to fasten the new mechanism in place. Greasing all the wear surfaces frequently helps extend life.
- The slider has a wear pad on top of the rail on either side. It is made of a soft material to protect the slider frame and trailer body frames from wear. If you detect cracks or breaks in the material, the trailer should be lifted off the slider and the wear pads replaced.
- Inspect all fasteners for looseness or breakage. This should be done annually. Re-torque, repair or replace as needed. Check the four hold-down clips and fasteners to make sure clips are not bent or cracked and that bolts are secure. If someone should try to move the trailer without all the locking pins securely locked, these would at least keep the slider from coming out from under the trailer body rails. These are torqued to 85 pounds-feet on many Meritor sliders. Check the value for your component.
- Inspect the frame rails for damage. Any cracking or significant damage such as that which can occur when slamming the unit hard against its stops is not only dangerous but will also result in an out-of-service order if the vehicle is inspected. Also, inadequate welded repairs are often weak points subject to corrosion. They will also result in an out-of-service order.
- Inspect spring hangers carefully. Developing stress cracks are often revealed by paint peeling along a line. Some shops try to repair hangers with wear pads of various kinds, but the only durable and safe repair is to replace the entire hanger. Interestingly, misaligned axles cause the springs to develop a lot of side force against the hangers, often shortening their life drastically.
- Look at spring saddles – a light coating of rust due to worn paint may indicate they are moving around because the U-bolts are not properly torqued. If the bolts are in good condition, check their torque, but in proper order and using rated torques. For example, on the Hutch 4-spring suspension shown, 7/8-inch U-bolts bolts must be torqued in a diagonal pattern to 470 pounds-feet dry and 3/4-inch. U-bolts must be torqued diagonally to 420 pounds-feet.
- Other bolts, such as the radius rod attaching bolts and rocker bolts must also be torqued to specification. The radius rod runs from the forward spring hanger to the spring saddle to control fore and aft motion. The rocker bolts are at the hinge point of the equalizer in the center spring hanger. Annual torquing of all bolts to specification will help guarantee long life and safe operation.
- With air suspensions, bushings are a critical wear item. Look for ragged or loose pieces protruding from the area around the connection. Pry gently up and down with a 2-foot prybar to check for looseness. Vertical play allowed on this Meritor air suspension is .062-inch If a radius rod is off center in its mounting, this may indicate a bushing problem.
- Inspect air springs for cuts and abrasions, and replaced if damaged. Check for anything rubbing the air spring and, if necessary, relocate air lines or other parts that might cause abrasion using ties.
- Listen for leaks and replace any leaking air springs or air lines or connectors.
- Shocks are especially critical to help control the motion of air suspensions. This improves the stability of the trailer on the road, and reduces tire wear, too. Inspect shocks for worn bushings in their ends, enlarged mounting holes and dents. Also grab each shock at the center and make sure it cannot be rattled back and forth along its vertical axis. Shocks that are working will be warm after a long run, while defective shocks will be at outside temperature. Trailers with good shocks will have minimal, visible bounce after hitting a bump. Replace worn or damaged shocks.
- The height control valves are working if the trailer maintains consistent height at both axles whether loaded or empty. If, as the trailer is loaded, it first drops slightly and then comes back to normal height, and it rides level, they are working.
Greasing
All the wearing parts of the slider locking mechanism, especially the pin surfaces, should be greased regularly. Another critical greased part is the camshaft that operates each brake. It has bushings at both ends that should be greased regularly with multipurpose chassis grease. Grease should be pumped in just until fresh grease appears. Over-greasing of the inner cam bushing can result in lube on the linings and failed roadside inspections.
Also, grease automatic slack adjusters with the special grease recommended by the manufacturer. Proper greasing of automatic slacks, especially, helps ensure long life and reliable performance.
Alignment
Axle alignment is one of the most important issues in the maintenance of trailer suspension systems. It’s simple to do, but a special alignment rack is necessary to do the job right.
A trailer’s axles should be aligned whenever it appears to be dog-tracking down the road. You may be able to detect dog-tracking in your mirrors. If you can see more of the trailer on one side than the other even though you are steering straight ahead, the trailer axles need to be aligned.
Alignment pays for itself in increased tire life and reduced fuel consumption many times over. It only takes a good technician a short time to align axles unless there are mechanical problems like bad wheel bearings or bent suspension components that need to be repaired. If misalignment is severe enough, it can ruin a set of tires in a single trip!
On the Hutch spring ride, alignment is adjustable via an adjustable radius rod on one side. The technician just loosens the lockbolts at either end and then rotates the center section of the rod to move that side of the axle forward or backward as necessary.
On the Hendrickson Intraax, there is an egg-shaped eccentric on either side. The technician just loosens the lockbolt and then uses a socket bar in the square hole to rotate the eccentric and move that end of the axle in the right direction. Adjustments are provided on both sides so that the distance between axles can be adjusted as well as the angle of each axle in relation to the trailer frame. Both axles must be adjusted on both sides during an alignment operation.
The landing gear
Landing gear uses a high speed gear ratio to raise and lower legs to the ground when the trailer is hooked up, and a low gear to raise and lower the trailer once the legs are supporting it. The No. 1 abuse of this system is dropping the trailer when the legs are not yet resting solidly on the ground.
When lowering the legs, once they touch the ground, the low gear should be engaged and the legs extended another inch or two to ensure they are adequately supporting the trailer.
The number one maintenance issue is greasing. There are typically grease points on the gearbox, as well as on the body, in order to cover the entire mechanism. The leg itself, where it slides up and down inside the body of the unit, should also be greased to prevent abrasive wear.
No. 2 issue is bolt torque. Torque all bolts to specifications periodically. Also, inspect all brackets carefully and replace if cracked.
You can tell when the landing gear’s internal gearing has worn and the mechanism needs replacement. You’ll feel the gears strip as you turn the crank instead of getting a steady lowering or raising of the legs.
Wheel bearing lubrication
Many wheels use oil in their bearings. With oil-lubed bearings, it’s easy to check the level and replenish. But you have to keep after them because even a small defect in a seal means the oil will quickly leak out. So keep your eyes pealed for any sign of oil leakage and also check the fill level frequently. Leakage means the hub must be disassembled and the oil seals replaced, a precision operation.
Any sign of oil leakage onto the brakes puts the trailer out of service.
Lube level can be easily seen through the sight glass. You can add fluid by either removing the small filler plug in the top of the housing (after rolling the wheel until it’s at the top), or by removing the red plug in the center. You can see the rings that indicate that the unit is full or that level has dropped to the point where it is essential to add oil. Check your owner’s manual for the correct viscosity and other specifications.
Total capacity is about 1 1/4 pints. After adding oil, spin the wheel a few revolutions and then recheck the level to make sure it is still correct. Add more oil, if necessary.
Many wheel bearings use grease rather than oil because, if a seal should fail, leakage will occur only very slowly. The downside of grease is that bearing must be disassembled and repacked carefully periodically and whenever the bearing and seals are serviced.
With greased bearings, routine maintenance means a regular inspection for any grease leakage. Remember, leakage onto brake linings means you’re out of service. Check your owner’s manual for the interval at which these bearings need to be disassembled, packed with fresh grease, and properly reassembled with new seals. These are precision operations that challenge even an experienced technician.
Here (see next page) is the axle spindle that forms the inner bearing surfaces, and the inner and outer bearings, for one type of greased wheel bearing system.
Our experts pointed out that there are a number of long-life greased wheel bearing systems on the market. Check your owner’s manual for maintenance intervals by type of bearing and seal system. With the long-life systems, an inspection for leakage and bearing play may be all that is required on a regular basis until you reach very high miles.
For all these bearing systems, however, maintenance by the book is critical because a failure can mean a wheel off, a trucker’s worst nightmare.
For further information, please contact the following:
Doonan Trailer Corp.
www.doonan.com
(620) 792-6222
East Manufacturing Corp.
www.eastmfg.com
(888) 405-3278
Great Dane Trailers, Inc.
www.greatdanetrailers.com
(912) 644-2100
Hale Trailer Brake & Wheel
www.haletrailer.com
(610) 395-0371
Ravens and Fontaine Trailers
www.fontainetrailer.com
(800) 821-6535
Rogers Brothers Trailers
www.rogerstrailers.com
(800) 441-9880
Transcraft Trailers
www.transcraft.com
(800) 950-2995
Utility Trailer Manufacturing
www.utilitytrailer.com
(626) 965-1541
Wabash National Corp.
www.wabashnational.com
(765) 771-5300