Penray Fill-For-Life 2-way test strips are dipped in the coolant and then compared with the scales on this chart. The upper scale determines coolant concentration while the lower scale determines nitrite (SCA) concentration.
If you can’t stand the heat in your engine, get out of the cab – and check your radiator.
Getting the heat out of the engine block requires a good water pump and clean coolant, but that is only half the battle. The other half is throwing all that heat off to the outside air. This is the job of the radiator, and EGR engines and the aerodynamic, sloped noses of many late-model trucks are making that job tougher and tougher.
The radiator consists of upper and lower tanks linked by dozens of thin-walled, narrow metal tubes with coolant flowing down through them. This exposes the coolant to metal in contact with outside air so it can get rid of heat (radiate) from the engine.
There isn’t much room for the radiator in an aerodynamic truck so the tubes have flat sides to help put the maximum amount of metal into a small space. Their narrow shape also keeps the coolant moving very fast inside the tubes, throwing heat off more efficiently. Closely spaced metal fins run between the tubes. This increases the total metal surface in contact with air, throwing off still more heat. But packing all this metal into a small space makes the outside of the radiator subject to clogging with debris.
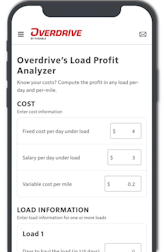
Having wet cylinder liners in direct contact with the coolant in a diesel improves performance, but it makes the cooling system a high-maintenance item. Trace amounts of exhaust gas leak around the liner seals and make the coolant corrosive. The result can be cooling system deposits and clogging in the radiator. Because the radiator tubes are so narrow, the deposits can easily clog those tubes shut.
The radiator operates under pressure produced by the radiator cap. The cap holds the coolant in until the pressure exceeds 7 psi to 15 psi and then relieves the pressure to avoid bursting any system parts.
The pressure raises the boiling point of the coolant well past the normal level of 212 degrees Fahrenheit. The higher boiling point enables the radiator to throw off a lot more heat than it could without pressure. The pressure also helps keep the block and cylinder liners cool by keeping steam bubbles, which interfere with cooling, from forming.
Air Flow
The radiator can’t do its job without lots of outside air flowing through it. Larry Erickson, field service manager at Peterbilt Motors, says the narrow openings between fins and tubes will definitely pick up some “road debris that will restrict airflow.”
Gary Falendysz, senior principal engineer in the truck division of Modine Manufacturing, says periodic cleaning of the air side of the radiator, charge air cooler, condenser and other heat exchangers is essential. “In order for these heat exchangers to work properly they need airflow,” Falendysz says. “Leaves, bugs and other road debris can foul them, restrict the airflow and reduce performance.”
The outsides of tubes and fins should be cleaned at least twice a year unless you operate in very dusty areas – then it should be done more often. Falendysz suggests doing this whenever the vehicle is washed.
The Mack maintenance manual says, “Using compressed air or water spray, clean insects, leaves and other foreign matter from radiator core openings as required. Always clean the radiator core from the engine side. Never use a wire or a screwdriver” to pry out leaves or dirt.
Erickson says the best, safest way to clean the fins and tubes is with a pressure washer that you can regulate, using warm water. “If you use 200 psi, it will bend the fins,” Erikson says.
On many trucks air shields direct air through the radiator. These shields should be checked regularly for cracks. Keep the belts that drive your fan in good condition and at proper tension. Also investigate and fix any problems with the clutch fan to help keep the radiator functioning when you’re operating in traffic or climbing hills.
Deposits, or “scale,” that come from cooling system neglect work as an insulator, holding heat in the radiator tubes – exactly what you don’t want. Even a very thin layer will mean the coolant’s temperature will drop less as it flows through, reducing radiator capacity. Deposits also slow down flow and can easily reach the point where they fully clog the thin passages inside the tubes.
This will soon result in a high operating temperature and, eventually, engine shutdown by the ECM. Another consequence: “The pump pulls the coolant through. It’s not a problem till the radiator tubes really get stopped up,” Erikson says. “With flows in the range of seven gallons per minute, the restriction will mean the water pump will start to pull in air because the seals in the cooling system are designed to keep coolant in, not air out.”
There are two low-maintenance ways to keep your cooling system clean inside to prevent this kind of trouble. Easy maintenance of both systems depends critically on adding only the right coolant. The worst thing is to add coolant designed for a car, not heavy-duty trucks, which will quickly leave the system unprotected against corrosion and may even foul it with silicates, an additive designed for the aluminum parts used in car cooling systems.
Darrell Hicks, the national truck OEM manager of Penray’s Power Fleet Division, says it can be difficult to get the proper coolant on the road, even at some truckstops. Keeping leaks to a minimum greatly increases the chances of making sure you’ll be able to top up with the right stuff. When you don’t have much leakage you’ll likely be able to carry enough of the right stuff with you.
The first step here, says Hicks, is simply to refill the system properly. Most trucks today use an overflow tank that allows you to see the coolant level right through it. The tank contains the coolant but without a pressure cap, so as soon as the level rises too high, it is lost. Often, drivers will fill the tank to the top. “Then,” says Hicks, “In only 25 miles, the coolant in the system expands and the fresh coolant is pushed out.” They keep filling the tank with any coolant they can get their hands on and soon the system has a significant amount of the wrong coolant in it.
“Fill the tank only to the level line,” Hicks say. “If you’ve overfilled it, and it’s pushed some coolant out, don’t refill it.”
If the truck uses a conventional radiator with only a top tank, fill it only to the correct level as specified in the owner’s manual – usually a couple inches below the cap opening even when warm.
Whenever you’re adding coolant repeatedly, “Find the leak,” Hicks says. “Why are you losing the fluid?”
The first thing to check is the radiator cap. You could be pushing fluid out through the cap, Erickson says. “The rubber seal can be so deteriorated a 7-pound cap will no longer be a 7-pound cap at all,” he says.
Remove the cap and inspect the seal. If it’s obviously cracked or grooved, replace the cap. Even if not, install a pressure tester, pump it up to the rating of the cap, and then watch to make sure the pressure is retained for two full minutes. If not, replace the cap. Erickson suggests replacing it every year or 120,000 miles. Check the rating carefully when replacing.
A good radiator cap will not only cure a common type of coolant leak, it will help keep coolant from boiling along the cylinder liner outside walls, helping to minimize cavitation erosion – a destructive acne-like pitting away of the cylinder liner. Erickson adds that keeping leakage to a minimum so the radiator stays full will also help minimize hot spots in the engine that can cause head gasket failure or even cracked cylinder heads.
Radiator repairs
“It shouldn’t be necessary to check for loose bolts in a modern cooling system,” Gary Falendysz of Modine says. “Most often, these fasteners have a self-locking feature that keeps them tight throughout the life of the product.” Erickson agrees such mounts have been made about as maintenance-free as they can be with a life of 300,000 to 400,000 miles.
But the high temperatures under the hood (often exceeding 275 degrees Fahrenheit) age rubber components over time. “Hoses, belts and rubber isolators can become dry and crack due to this heat,” Falendysz says. “Ozone also attacks these rubber components. Belts, hoses and rubber isolators should be replaced if they become hard or cracked.”
Erickson recommends checking isolators out, especially on an older or used truck. Isolators suspend radiators on a bed of soft rubber so chassis vibration will never reach them. If they get hard, vibration will pass right through. If they “get loose in the sockets,” says Erickson, the radiator may even bounce around. This can cause deterioration of internal seals and relatively delicate brazed joints in the unit, resulting in leaks and the need for repairs. Also, check the bolts mounting the brackets to the engine – vibration can occasionally cause them to fail, leaving the radiator vulnerable.
Radius rods, often used to anchor the radiator at the top, also deserve a close look. If loose or misadjusted, they may allow wind pressure to push the core back into the fan as the correct clearance may be less than an inch. Make sure all mounting bolts are tight and any bushings are in good condition. Make sure the radiator is vertical or at the correct angle to ensure adequate clearance between the core and fan. Erickson says this is a critical maintenance area as fan blades can fail catastrophically when rubbing occurs.
Falendysz points out that modern trucks have “cooling modules” that often consist of a metal frame that surrounds and supports not only the radiator, but also the charge air cooler and air conditioner condenser. Maintaining the mounts for the radiator will also often help prevent expensive repairs of these other devices.
“Most radiators have lightweight aluminum cores with plastic tanks,” Falendysz says. “A rubber seal between the core and plastic tank prevents coolant leaks. Minor damage of the core can be repaired by brazing, welding or with epoxy, but most of the time it makes more sense to simply replace the radiator with a new one.”
Erickson says different rules apply with the “tougher, all metal” units, like those used in the Peterbilt 379. Each tube is welded into a corresponding hole in a flat “header plate” located at top and bottom of the radiator core. The header plate holes serve as rigid mounting points for the tubes. The upper and lower tanks, made of stainless steel, are bolted onto the header plates and sealed with rubber gaskets. Radiators in other brands of trucks of traditional design may be similar.
If you develop a leak between the upper tank and header plate, you can easily drain the system, unbolt the tank and replace the gasket. But Erickson warns against attempting to remove the radiator on your own to replace the lower gasket, or for the other repairs a radiator shop might perform on a damaged unit. The unit is so heavy – about 200 pounds – that a large A-frame must be used to support it during removal and replacement. Without such equipment, it’s easy to “mash fins,” says Erickson.
Clogged radiators
You’ll know a radiator is clogged, Erickson says, by cautiously feeling the temperature of the core just after shutting down the engine. Areas of the radiator where tubes are stopped up will be much cooler to the touch. If the radiator isn’t too badly clogged, it may be possible to clean it right on the truck.
Allow the engine to cool and then remove the radiator cap and peer down into the tank to check for clogging. You may see corrosion around the ends of the tubes. This often takes the form of “solder bloom,” where the solder used to seal the tubes into the tank expands when it corrodes, fully or partially blocking off the end of the tube. On systems with a pressurized overflow tank and no cap on the radiator, you may be able to get a look inside the tank by partially draining the system and then disconnecting the upper hose.
If only partly clogged, it may be possible to clean the system by using an “on-line” cleaner that works while you drive. You simply drain some coolant, add the cleaner, which consists of one gallon of liquid, and then drive 25,000 miles. The cleaner includes corrosion resistors to protect the system during the process. After the mileage has elapsed, you drain, flush and refill the system with fresh antifreeze.
More aggressive chemical cleaner can be used while the engine is running but the truck is sitting. One example is Penray’s 2025 Twin Pack. One pack consists of the very acidic cleaner and the other of a neutralizer needed to flush the system after cleaning so the acid won’t damage system metals.
If these do-it-yourself efforts fail, you may still be able to save the clogged radiator core, which Erickson says can cost more than $1,000 to replace. Radiator specialty shops can do the most aggressive and effective cleaning with the unit off the truck, Falendysz says.
Of course, the key to preventing such drastic repairs and cleaning is careful maintenance of the supplemental coolant additives or oxalic acid system that combats system corrosion. “Preventive maintenance by regular interval system flush and refill is the best way to prevent internal clogging from becoming a problem,” Falendysz says.
Doing all these things will help guarantee that you’ll be able to climb long hills with confidence even on the hottest days of the summer.
A jug of the Texaco Extended Life Coolant, also marketed by Caterpillar and Shell. It uses carboxylates to give stable, long-term protection, but must always be replaced with the identical formula or protection will be lost.
Do the Coolant Two-Step
Know how to choose the right blend and then keep it working for you
You have two choices when it comes to easy-to-maintain systems for heavy truck coolant.
The first option is to use only fully-formulated coolant, a blend that protects the system right out of the bottle, together with a “need-release” filter supplying supplemental coolant additives (mostly nitrites) as needed. You make sure the system is clean, refill with this antifreeze and then install an SCA-control filter. Controlling how the SCAs flow into the system not only saves the trucker a lot of maintenance, it prevents the SCAs from accumulating as solids in the system, which would require a coolant change much sooner.
Darrell Hicks of Penray, which makes a need-release filter, says the filter has a cake of SCAs in it that looks like “a puck of toilet bowl cleaner.” The secret to the filter’s ability to control system SCAs is a membrane that separates this “puck” from the coolant flowing through the filter. To the molecules in the cake of SCAs, the membrane is like a screen door with tiny holes in it. The membrane allows the SCAs to pass through, but only if “the relative corrosiveness of the coolant” reaches a certain level, says Hicks. As you drive and the chemical effect of the SCAs in the coolant starts to drop, that’s when the filter adds SCAs automatically. The filter also removes debris from the coolant to help keep other dissolved solids from shortening its life.
There are various brands of need-release type filters with varying change intervals, but they all last much longer than the traditional maintenance type filters. The Penray need-release unit is normally replaced at 15 months and 150,000 miles. Once the system is working, all you really have to do is make checks so you can be sure only the right coolant has been added.
Your second option is extended life coolant. One example is the ChevronTexaco/Caterpillar extended life coolant (ELC), also marketed under the Shell Rotella and DDC Power Cool Plus brands. This coolant uses carbolic acid, which breaks down much more slowly than SCAs, providing long-term protection with almost no maintenance. All you do is add a bottle of extender at 300,000 miles and then change the coolant at 600,000 with most brands of engines (check the manufacturer’s specific recommendation).
Cummins Fleetguard markets a hybrid carbolic acid coolant called ES Compleat that adds a few SCAs to the system and uses a need-release type filter to do so.
After you have chosen your coolant, the only difficult part of maintaining these systems is being sure to add only the proper coolant, either fully-formulated or ELC depending on which system you are using.
Keep the system tight and free of leaks. Key moves in this process include checking and tightening hoses or screw-type clamps or replacing band-type clamps as needed.
If you are not sure about the state of your coolant, Hicks suggests using a refractometer to check it. Refractometers generally run about $69. “These are pricey but accurate,” he says. “The reading tells you when the system has been invaded with either water or antifreeze.” How? You place some antifreeze on the refractometer’s glass, close the cover, point the glass toward a light and peer through the lens. The mix of antifreeze and water bends the light, creating a shadow that runs across a scale and reveals the exact freeze point of the mix. Since drivers typically add a little too much water or antifreeze, you’ll immediately notice a telltale change in the reading.
If you are still not certain, Hicks recommends checking antifreeze concentration and protection every time you change your oil. You can use test strips like the ones Penray supplies called “Fill for Life 2-Way.” You dip one test strip into the radiator or overflow tank for two seconds, then pull it out and watch what happens to the colors of two little pads. After 45 seconds, you compare the color of the pad near the end of the strip with a percent glycol scale and the color of the other with a nitrite percentage scale. You may have to adjust SCA level by adding small packets of the stuff.
If you’re using ELC, adding the wrong coolant will defeat the protection of the carboxylates, but you could then just add and maintain SCAs in order to avoid an immediate change of coolant. ELC, too, can be tested with special test strips for depletion of its protection.
Erickson recommends that you avoid using any kind of water filter with ELC because of the chance of installing one that adds SCAs by mistake.
A visual inspection is also in order because if the coolant is brown or full of sediment, it’s severely contaminated, meaning the system will have to be flushed and the coolant replaced. But even if coolant is clean, that’s no guarantee it is working. If you don’t know, check it because only the test strips can tell you if you have adequate protection.
For further information contact:
Shell Oil
(800) 782-7852
www.shell-lubricants.com
The Penray Companies
(800) 322-2143
www.penray.com
ChevronTexaco
(925) 842-1000
www.chevrontexaco.com
Modine Manufacturing
(262) 636-1200
www.modine.com
Peterbilt Motors Co.
(940) 591-4000
www.peterbilt.com
Mack Trucks, Inc.
(610) 709-3011
www.macktrucks.com
Caterpillar Engine Div.
(309) 675-1000
www.caterpillar.com
Detroit Diesel Corp.
(313) 592-5000
www.detroitdiesel.com
Fleetguard
(615) 367-0040
www.fleetguard.com
The Penray Companies
(800) 322-2143
www.pennray.com
Amalgatech
(602) 252-0280
www.amalgatech.com
Recochem
(905) 791-1788
www.recochem.com