Freight that is secure puts the owner-operator at ease, knowing the cargo is safe, his rig is not at risk, and there is no fear of an out-of-service violation from inspectors.
The problem with dry van securement, the Federal Motor Carrier Safety Administration recently ruled, is not that cargo restraining devices – trailer tie-down points, cargo straps, load locks, jack bars, shoring beams and chock blocks – are ineffective. The problem is that truckers use them incorrectly or don’t use enough of them.
Properly secured freight won’t shift, unbalance the trailer and cause an accident. It won’t be damaged in transit and raise liability questions. Freight that is secure puts the owner-operator at ease, knowing the cargo is safe, his rig is not at risk, and there is no fear of an out-of-service violation from inspectors.
“When you leave something in there loose and let it roll around, it can have a lot of impact,” says Rod Ehrlich, chief technology officer with Wabash National Trailer. When freight moves, it builds force and can damage trailer walls. But if it’s immobilized against a bulkhead, the force created by the truck’s movement will have no effect.
Even trailers without the strongest walls withstand up to 18,000 pounds of steady pressure in testing, Ehrlich says. “In all van trailers, that wall is fairly substantial when it comes to load confinement,” he says. “The DOT is well aware of that, and they don’t have a problem with shoring a load against the wall.”
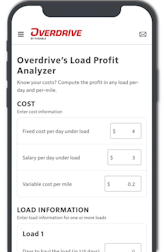
“The load restraint for dry vans is unlike the flatbed system, in which you must have tie-downs to ensure the load does not fall or blow off the trailer,” says Ralph Abato, national sales manager of Ancra Cargo Securing Systems in Cincinnati. “The trailer walls act as containment. All the driver has to do is immobilize the load so it won’t tip, shift or spill.”
Suitable restraints are available for any dry van freight. Straps and some rigid restraints generally work in tandem with tracking attached to interior bulkheads. If the ends of the restraint lock securely into the track, a working load limit can be assigned the restraint. Safe securement requires knowing the limits of the restraints and the weight of the cargo.
Generally, working load limits of straps are a third of breaking strengths. A strap with a 1,500-pound breaking strength will have a working load limit of 500 pounds. When combining restraints such as straps, beams or load locks, make sure the sum of their working load limits is equal to or greater than half the weight of the cargo. For example, four cargo straps each rated at 500 pounds could legally be used to secure no more than 4,000 pounds of freight, according to regulations.
Also, make sure cargo restraints are free of defects. “If it’s a required tie-down and if it has a knot, that’s an out-of-service violation,” says Collin Mooney, director of training programs at the Commercial Vehicle Safety Alliance. “A knot gives it a weak point.”
Here are some common, proven devices for keeping a load in place.
LOAD LOCKS or cargo bars are the most common restraints because they’re inexpensive and versatile. They work on friction created when their rubber “feet” press against the trailer. Most consist of two metal tubes that slide freely, like a telescope, to adjust overall length and a lever-operated ratchet for small adjustments and locking the device into position. Newer models break down into two or three pieces, making storage easier.
Drawbacks: Because trailer walls vary, load locks can’t be strength rated, and they’re generally useful for only very light cargo. Also, some plate trailer walls are designed to flex; load locks just force them apart without providing much securement.
JACK BARS work much the same as load locks, but they are generally square, made of much stronger metal and have much bigger “feet.”
Drawbacks: Not all trailer walls are rigid enough to withstand the increased pressure they create. Also, like load locks, jack bars cannot be strength rated.
TRACKING consists of metal strips riveted to trailer walls. The strips have holes punched through them. Various restraints lock into the holes to create very strong cargo securement that can be strength rated to satisfy inspectors. In sheet and post trailers, tracking can be designed into the vertical side support posts and spaced to buyer’s specs. Tracking comes in three types, defined by the shape of the holes: F, round holes, is the weakest; A, rectangular holes, is medium strength; E, the strongest, is I-shaped holes, oddly enough.
Drawbacks: If not embedded, can decrease interior width up to 11/2 inches.
SHORING bars consist of two telescoping metal tubes with F track fittings on the ends. They can be strength-rated: round tubes to about 500 lbs. and square tubes to about 1,000 lbs.
Drawbacks: Can be hard to stow.
SHORING BEAMS consist of two telescoping, rectangular tubes made of very heavy gauge steel or aluminum with fittings at each end that are usually designed to lock into E tracking. They can be strength rated up to several thousand pounds of freight. Several shoring beams working together can be rated up to several tons.
Drawbacks: Added weight, difficult to stow.
CAPTIVE BEAM SYSTEMS are posts made of heavy gauge steel or aluminum that are attached vertically to trailer walls, in pairs directly across from one another. Matching horizontal beams fit into slots in the vertical beams; they slide up and down the posts and can be locked into place at desired levels. Usually spec’d by customers and installed by trailer OEMs, these can be strength rated and can double the cargo capacity of a trailer. When not in use, the horizontal beams are locked out of the way against the ceiling.
Drawbacks: They’re expensive, add significant weight, and can easily be damaged by forklifts.
LOAD STRAPS are cheap, lightweight, easy to stow and versatile, as they come with hooks or E, A or F track fittings at the ends. They can be strength rated up to thousands of pounds. Simple cam buckles are tightened by pulling on the loose end; stronger ratchet buckles are tightened with a lever that turns a ratcheted spool; and overcenter buckles, the strongest, are secured by two locking levers that fold over the center of the buckle.
Drawbacks: Overly tightening the straps on sharp edges, without edge protectors, can damage cargo.
CHAINS usually have hooks at either end and are typically tightened using a lever-operated metal ratchet. Like straps, chains can be strength rated to several thousand pounds.
Drawbacks: Overly tightening can damage cargo.
TRACK-MOUNTED D RINGS are versatile, inexpensive, light, easily stored, portable tie-down points that can be strength rated. They consist of an F, A or E track fitting and a D ring joined by a few inches of strap. By attaching the fitting to the track, drivers create a secure tie-down point for straps or chains.
Drawbacks: Used properly, none.
BULL RINGS, or floor-mounted pan fittings, can be strength rated up to several thousand pounds. Usually spec’d and OEM-installed, they create permanent, secure tie-down points for straps or chains.
Drawbacks: They can’t be removed.
FRICTION MATS are inexpensive, light and made of specialized rubber sold in 3-foot squares or in bulk on spools. Placed on trailer floors beneath heavy freight such as paper rolls, mats create high friction between freight and floor, thus stabilizing the freight.
Drawbacks: Mats won’t stop freight from tipping.
CHOCK BLOCKS are wood blocks or wedges that are secured to the trailer floor, usually with nails, around freight to keep it from sliding. They are usually used with other restraints to prevent tipping. Inspectors require chock blocks to be free of cracks and splinters and strong enough not to break apart.
Drawbacks: They must be removed after each load, the trailer floor eventually gets riddled with holes, and leftover nails are a menace.
Most cargo restraints come with a warranty and cost less when purchased in bulk. Restraint manufacturers sell spare parts, and repairs are generally simple.
Cargo securement is a leading out-of-service item, Mooney says, and having fewer than the required number of restraints is the most common freight-related violation. Don’t let it happen to you. Make sure you have securement tools on hand, and use enough of them to keep the cargo moving in only one direction – down the road behind you.
UP AGAINST THE WALL
For many owner-operators, load securement starts with the trailer.
“We install horizontal or vertical tracks, captive beam systems, extra vertical posts, D rings or whatever the buyer specs,” says Mark Roush, director of engineering at Vanguard Trailers in Monon, Ind. “The important thing is that everybody’s up front about what’s going to be hauled in the trailer and what its capabilities are. It’s not good to specify a weaker structure to get a better price. Everybody comes out a loser when that happens.”
Most dry vans are either of post construction or plate construction. Plate trailers are made of two high-strength steel skins sandwiching a polyethylene core and are designed to flex. “Don’t equate stiffness with strength,” says Rod Ehrlich of Wabash National Trailer.
However, freight that pushes against trailer walls, such as carpet rolls, will cause plate trailers to bulge and appear “pregnant,” and so will load locks or jack bars that push against trailer walls. “Try putting three load locks in a vertical row in a plate trailer,” says Chuck Cole of Utility Trailer in City of Industry, Calif. “They’ll keep falling out. They would not have much shoring ability. If you haul something that puts a lot of pressure on the walls, you’ll want the post trailer.”
Post trailers have inner plywood and outer aluminum sheets about an inch apart and supporting posts every 24, 16 or 12 inches for strength. “With a post trailer, you’re able to secure any kind of load,” says Craig Bennet of Utility Trailer. “Owner-operators are probably better off going with the post trailer.”
Besides adding rigidity to trailer walls, support posts with built-in tracking allow for a wide variety of cargo restraining devices. “We can make the trailer walls more rigid with optional heavier posts,” Roush says. “If customers know they’ve going to have heavy sidewall load securing, we’ll offer them the deeper post option.”
However, post trailers cost more to operate because their inner plywood walls easily sustain damage and require repairs.
“If you get into it between plywood and a forklift, the plywood loses every time,” Ehrlich says. “That’s happening constantly, and it gets very expensive.” This is why most large fleets have switched from post to plate trailers, he says.
Plate trailers, too, can have tracking installed, “with a hole in between so you can use an S hook in there,” Ehrlich says. But because of their more rigid walls, post trailers better accommodate load locks, jack bars and captive beam systems.
RESOURCES
www.furnishequipment.com – (800) 332-0614
www.kinedyne.com – (800) 848-6057
www.ancra-llc.com – (800) 233-5138
www.saveaload.com – (800) 728-5623