Retreads give worn-out tires a new lease on life – and save you money.
After fuel, tires are an owner-operator’s highest expense. Retreading lets you reuse the good parts of the tire instead of buying all new, saving about half the cost of new tires.
Like your engine, tires have some parts that wear a lot faster than others. The tread takes the most punishment – both continued rolling and rubbing along the road, and punctures from nails and screws. The casing, when properly cared for, can outlast the tread by two to three times because it’s isolated from the road by the tread.
The goal of retreading is to rebuild the tire, removing the tread from the casing and replacing it, much as a cylinder liner is knocked out and replaced. The new tread is securely bonded to the tire through a process called “vulcanizing.” The original tire was fused together, using heat, out of vulcanized raw rubber in the same way. Vulcanizing makes the rubber stronger and harder, like heat-treating metal, and fuses the parts together, like welding. When the job is done right, the retreaded tire’s structure is virtually identical to that of a new tire.
The three processes
There are two basic methods of retreading, mold cure and pre-cure. In mold cure, raw strip rubber is applied to the casing, and the assembly is then inserted into a heated mold, where the strip rubber is vulcanized and the tread pattern molded into the added rubber. In pre-cure, a cushion gum adhesive layer of uncured, raw rubber is applied to the tire. A strip of pre-cured, molded tread is then applied, and the assembly is cured inside an envelope in a pressurized mold to bond the new tread to the casing. Bandag, Inc. has been well known for the pre-cure process for many years, but Goodyear and others also produce many pre-cured retreads.
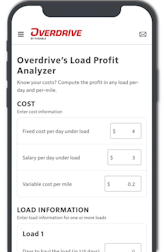
A variety of pre-cure is the Goodyear Unicircle process, which produces jointless pre-cured treads formed into a circle of exactly the right diameter for fitting around the casing.
Mold cure is a well-established process, but it requires the retreading plant to provide the tread pattern in the form of mold “segments” that have the tread pattern in reverse cast into them. The segments form a circle inside the mold press when they close around the casing and strip rubber (A). Typically, the number of mold cure tread styles available is limited because of their cost, even though the segments in a mold can be changed in a lengthy operation.
Pre-cure provides a great number of tread styles because the treads are mass-produced in a large, central plant. Pre-cured tread naturally has a seam where the two ends of the pre-cured tread segment meet and are carefully fitted and then vulcanized together. Properly done, the seam is problem-free. But Goodyear’s seamless Unicircle design eliminates any potential trouble with the seam and makes the resulting product a little easier to balance.
We toured the Wingfoot Commercial Tire Systems retreading and repair plant in Westminster, Md., not far from Baltimore. Bob Bohn, production director and Paul Muckle, satellite manager, walked us through the entire retreading process.
- Casing Inspection
Casing maintenance, including keeping the tire properly inflated and doing all repairs properly, are critical to making retreading work. One of the keys to having an effective retreading program in any operation is caring for the casing so you can take a known good one back for retreading and save the cost of purchasing another.At the retreading plant, the first step is casing inspection. Improved inspection techniques are one of the keys to a great improvement in retreaded tires over the years.
Here, (B) the inspector is getting ready to inspect the casing. He mounts it on a machine that rotates it and allows him to look inside. The machine also tests the tire much the way you’d test electrical insulation. It drapes small chains across the inner tread and energizes them with high voltage (C). Because rubber is an excellent insulator, there is no noise until the chains encounter a small hole in the structure, often containing a nail. The technician then hears a buzzing noise and can locate where the puncture is immediately. He removes the nail and marks the damage for later repair.
He also inspects the casing visually with a bright fluorescent light.
All such repairs are made in a way that seals off the inner liner of the tire, so moisture in the inflation air cannot seep into the casing and rust the cords, or separate the casing’s structural cords with the pressure. Except for a temporary repair just to get you home, it’s vitally important that all tire repairs be done this way – with the tire removed from the wheel and sealed from inside. This is one of the most important keys to preserving the casing for use in retreading.
Patches (D) of different sizes are vulcanized to the inner liner of the tire in order to seal it effectively.
Many retreaders have even more sophisticated inspection systems. Bandag touts its 7400 Insight system that provides a “shearographic” inspection. This uses laser technology and varying vacuum pressures to stress the casing structure and make sure it’s still strong and defect free.
Bohn says Goodyear has its own entirely automated system now in use in many locations.
- Tread removal
Bad casings are discarded. Once a reusable casing is found to be in ideal condition, the next step is to remove the old tread. This is accomplished by using an abrasive wheel to cut the tire down to size, called “buffing.” At this facility, the process is completely automated.The tire type is input into the computer (E), which has data on the exact dimension the tire must be buffed down to in order to reach the outside of the casing. This removes the old tread to within 3/32 of the tire belts(F). The surface is then textured with a grinding wheel. The type of abrasive wheel used produces exactly the right texture, termed RM83, ideal for the new tread vulcanizing process. Technicians can check the texture by comparing it with various examples(G).
- Applying cushion gum or strip rubber
A special machine then applies layers of cushion gum to the casing, if the tire is to get pre-cured tread (H). This is raw rubber which, when subjected to heat, fuses to the inside of the pre-cured tread and the outside of the casing.If the tire will be mold cured, it receives raw strip rubber that is carefully wound around the casing to produce an even layer of sufficient thickness to form a tread (I).
- Applying the tread
In pre-cure, the tread is then carefully located on the outside of the casing. (J) Here, a Unicircle pre-cured tread is being slightly expanded and then located onto the casing. Laser light is used to center the tread so it’s right on the money.Another type of machine applies the standard pre-cured tread (K).
- Curing the tread
Mold curing is done at 300 degrees F. for one hour, with 200 psi pressure in the casing in order to force the tire outward and into the mold segments.Pre-cured tires are cured 23 at a time inside this curing chamber (L). They are placed inside rubber envelopes. Pressure inside each envelope is held at 70 psi with a separate air line to each envelope. This is called EPS or “Envelope Pressurization System.” There is 85 psi in the chamber. The chamber is held at exactly 260 degrees F., using high-pressure steam inside pipes and an air circulating blower to make sure the temperature is even.
Technicians can watch the pressure inside each envelope to make sure it is correct. The temperature inside the chamber is recorded throughout the curing period of three hours to make sure the tires are perfectly cured (M).
- Final inspection
After all this, the finished product receives a careful look-see to make sure the tread is properly aligned and defect-free. The sidewall, inner liner and the appearance of the cushion gum layer will be checked. An inspector can see right away if the curing envelope leaked because the gum will be wrinkled or have bubbles in it. It should be smooth.The precision with which this seam was formed shows what kind of work a quality retread plant can produce (N). The final product gets a label verifying the work done and helps guarantee that it will be returned to the proper customer (O).
Typical tread and rotation patterns
Steer tires are not normally retreaded, and running retreaded steers is prohibited in most jurisdictions. Worn steers receive either a lug tread and become drives, or a simple grooved tread for trailer tires. The lugs allow the drive tires to produce greater forward traction, while the grooved trailer tread has less rolling resistance.
Most of the time, the first re-use of the casing will be for drive tires. The second use goes onto the trailer because trailer tires do not endure either the torque of driving the truck down the road or the twisting forces a steer tire is subjected to.
The secrets to getting good retreads include effective pre-trip maintenance and inspections, as described in the sidebar, and getting proper repairs done from the inside out. The other half of the equation is taking your casings to a large scale retreading plant like this one. A retreading plant should be equipped with the kind of precision machinery we’ve shown here and staffed by highly trained technicians who can control every step of the process in an exact manner.
Early Warning
Pretrip inspections help preserve tire casings for retreading
The most cost-effective retread program depends upon successful reuse of tire casings. The most important key to preserving casings is pretrip inspections.
Bandag, Inc. provides some suggestions on their CD called “No Detours.” It’s important to remember that, with any truck tire, air pressure actually carries the load, not the tire itself. The tire just contains the pressure.
Since the tire structure cannot support the load without sufficient air pressure, it flexes excessively when underinflated. Underinflated tires generate damaging heat, running as much as 5 degrees F. warmer than normal for each 2 psi drop from the proper rating. A tire rated to run 110 psi and holding only 90 psi because of a small leak might run more than 50 degrees F. above the proper temperature, enough to blow the tire apart. Smaller deficiencies in pressure can still reduce mileage and ruin the casing, resulting in an early trip to the scrap pile. Proper pressure also maximizes fuel economy.
“With a modern, radial tire, it’s impossible to determine if a tire is properly inflated by striking it with any kind of heavy object,” Bandag says. “You need to use a good tire gauge.” Gauges need to be checked for proper calibration and replaced occasionally.
- Check the pressure and bring up to the proper pressure. If any tire is found to be 20 psi below its rating, it should be considered flat and removed, inspected and, if necessary, repaired before use. This will prevent tread separation and possible destruction of the tire, along with an unsafe operating condition.
- Inspect the tire as well as you can for any injuries or foreign objects in the tread. If you find a foreign object that is causing leakage, make sure to have the tire removed and repaired properly from inside.
- Check tread depth. It must be 4/32 inch for steer tires and 2/32 inch on drive and trailer tires. Note that many fleets place more stringent limitations on tread depth. Frequently, retreading a tire with 3/32 inch or more of tread life left will improve the chances that a casing will be reusable.
- Inspect also for irregular wear. This can be cured by proper steering and axle alignment. Irregular wear causes the tread depth to drop below acceptable limits prematurely.
- Inspect the sidewalls for cracking or a rupture, which is indicated by a bulge. Get such a tire repaired because this condition frequently leads to a run flat condition and complete destruction of the casing.
For More Information:
Bandag, Inc.
(800) 523-6366 prompt 6
www.bandag.com
Tire Retread Information Bureau
(888) 473-8732
www.retread.org
Wingfoot Commercial Tire Systems Inc.
(800) 643-7330
www.wingfootct.com