Tool by tool, building a home repair shop enables do-it-yourself maintenance and saves money.
Doing your own repair work with the proper tools saves money by avoiding labor charges, but it makes money, too, because more time on the road means more revenue.
“You do the work on the weekend when you’re at home,” says one-truck owner-operator Gordon Bow of Oakfield, N.Y. “Then it doesn’t take time out of your driving week to schedule maintenance at a truck stop or dealer.”
Doing repairs yourself also reduces downtime because doing your own oil changes and greasing gives you a chance to look under the truck and find problems before they leave you stranded. More savings accrue when you buy oil, grease and transmission and axle fluids in bulk, paying much less per pound or gallon.
Care taken by a dedicated do-it-yourselfer also deters inspectors, says Bow, who ties wires in place and slips old hose over brake lines so they won’t chafe. “If they see you’ve maintained the truck and tried to keep air hoses and other safety-related parts protected, they’ll spend less time looking for trouble,” Bow says.
Less tangible, but nonetheless real, is the satisfaction to be had from doing your own work, Bow says. “I really enjoy doing it. There’s nothing shameful about being a grease monkey.”
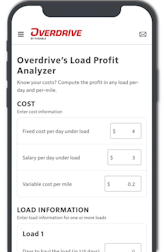
But if your toolbox is empty, where do you start?
Tools aren’t cheap. A simple high-quality pair of angle-nose pliers, for example, will cost you about $49. But if you take care of them, they’ll last for many years and pay you back in unexpected ways.
Earl Evans, a one-truck owner-operator from Canfield, Ohio, advises starting out with hand tools that will help you tighten loose bolts and replace broken or worn parts.
You’ll need both metric and English wrenches of all kinds, Bow points out. “Bolts are half metric and half English sizes on every vehicle.”
Keith Harring began building up his tools early in his career, when he had just two trucks. Today K.L. Harring Transportation is a medium-sized fleet with more than 30 tractors and many more trailers. Its repair shop is run by Tommy Vajdic, who advises starting with open-end wrenches, box wrenches and sockets.
Sockets can be operated by a ratchet wrench, allowing you to rotate a bolt in a confined space without continually pulling the wrench on and off the head. Box wrenches are easier and quicker where you can get over the top of a bolt, but there isn’t room for a socket. You’ll need open-end wrenches where there isn’t room to get over a bolt head.
Sockets have drives that take the form of a square fitting, either as an extension or a part of a ratchet wrench or bar. They are classified by different size drives; you match the size of the drive to the size of the bolt and the amount of torque needed to turn it. Vajdic suggests 5/16-inch, 3/8-inch and 1/2-inch drives. For heavy work, Bow recommends 3/4-inch drive sockets or impact wrenches. If you graduate to the heaviest chassis work, you’ll need sockets with a 7/8-inch drive, Vajdic says.
Getting some universal sockets is a good idea, Bow says. They incorporate a U-joint to help you work around corners.
Necessary hand tools also include standard and needle-nose pliers, vise grips, Allen wrenches and filter band wrenches. Small wrenches will handle fuel filters, larger ones the big combination full flow and bypass oil filters. Make sure to get a good set of screwdrivers of various sizes with standard, Phillips and Torx heads, Bow says. Screwdrivers will help you replace incandescent and LED lamps, which will help keep inspectors off your back, Harring says.
Torque wrenches are critical for certain component work, for example replacing water pumps, where correct bolt torque helps gaskets to seal. Harring’s shop has both 75- and 250-pounds-feet torque wrenches. The larger size, which can cost $230 to $275, is needed for major engine work, such as head gasket replacement.
Compressed air power will help you do the big jobs when a number of large bolts need loosening and tightening. Evans recommends a 5-hp air compressor with a rating of 16 cubic feet per minute and a 60- to 80-gallon storage tank, the same size Harring used in his early days. Such compressors typically sell for $600 to $700.
Bow spec’d his Detroit Diesel 14-liter Series 60 with a two-cylinder, 27-cfm airbrake compressor that allows him to use air tools on the road with the engine idling at 1,100 rpm.
Like many owner-operators, Harring started his do-it-yourself career by changing his own oil. Changing oil, changing filters -fuel, coolant and oil – and greasing make up the most basic maintenance. This is when you’ll use those filter band wrenches, but you’ll also need to add drain pans and some sort of used oil storage.
Evans suggests a 4- to 7-quart pan for the coolant filter and a 5-gallon galvanized drum for draining transmission and axle lubes. For coolant, he uses a plastic pan rather than metal because coolant is often drained and held while replacing a heater core or water pump. The plastic pan won’t rust, helping guarantee the coolant will stay clean. Evans recommends keeping containers upside down and covered when not in use.
He drains his oil into a large pan on rollers, easily moved under the engine. You’ll need one of 50- to 60-quart capacity for a 14- to 16-liter engine. Evans installed a Fumoto quick-open drain valve onto his Caterpillar engine. It accepts a hose so the hot oil can safely be channeled into the drain pan.
Disposing of oil is an issue because you’ll need to pick it up. Such businesses prefer larger quantities, so a smart move would be to do what Evans did and get a 250-gallon waste oil tank. At that quantity, businesses may even take it away without charging you. Evans’ drain pan is sealed so he can use air pressure to force the oil into his storage tank.
Bow, Evans and Harring all buy their oil in 55-gallon drums. The oil costs much less per quart, and there’s little waste. Draining 10 or 11 one-gallon containers, on the other hand, leaves a measurable amount of oil in each bottle, Bow says.
You’ll need a pump driven by a rotating crank. Harring’s shop uses an air-powered pump to ease the delivery of those 50-plus quarts to the sump. Evans uses a $22 five-gallon “bucket pump,” complete with delivery hose, to get gearbox and axle lubes from their containers into the truck.
Doing your own greasing requires a heavy-duty grease gun for the standard zerk fittings to provide enough pressure. One of the larger hand-held units will hold enough No. 2 to prevent reloading too often. Hand grease guns easily can be filled very gradually, so that you feel increasing pressure when the reservoir gets full.
Bow prefers his air-powered unit that fits on top of a drum. He recommends having a hand free to guide the grease supply hose and fitting and hold them in place. Air power also saves a lot of elbow grease, Bow says.
Bow also uses wheel chocks while greasing the driveshaft so he can put the truck in neutral. Removing any torque eases the job of getting grease to penetrate all the bearings in each cross.
Are you likely to expand from simple replacement of fluids and filters into things like exhaust system work or replacing small components? Transferring a pulley from a worn-out generator to a replacement might mean you’ll need a place to rest the unit, or even hold it, as you work. This means you need a solid workbench at least 6 feet long, Evans says.
Steel workbenches that size typically sell for about $450. Add a substantial vise, securely mounted to one end, to hold whatever you’re working on. Drop lamps or fluorescent tubes with long cords will help you see and reduce eye fatigue.
Evans uses air-powered impact wrenches for his own exhaust work, since those parts tend to rust.
Truckers who are good with procedures that require a number of exact steps in the right order may want to set their overheads. Besides the right manuals from your engine dealer, you’ll need a set of feeler gauges for the valves and a special injector height gauge or inch-pounds torque wrench for setting injectors. Add a pry bar that will allow you to bar the engine over and sit it at six different crankshaft positions. Bow sets his every 100,000 miles, but the job is so precise he gets help from a friend, a former technician.
Many owner-operators do their own basic electrical work. Bow, for example, recently experienced reduced cranking power. A test of his batteries after disconnecting them revealed the problem was a thin film on all the connections in the battery circuit. Only carefully cleaning and refastening the connections solved the problem. This would have cost a lot if he had hired a professional.
For electrical work, Bow recommends a good battery tester, as well as small wrenches and emery cloths, for disassembling and cleaning up connections. A battery terminal brush can be had for about $26. Get a basic electrical tester such as a multimeter or digital voltmeter to measure voltage and current flow. Use solder and shrink tube connectors to make wiring repairs, Evans says, because today’s road de-icers will make short work of anything less.
Bow strongly recommends a hand-held computer compatible with your engine’s electronic control module. It’ll tell you what’s wrong when used to download stored failure codes. If the engine develops trouble while you’re on the road, this will make any emergency call faster and more effective.
Take advantage of any diagnostic or maintenance software your engine or truck manufacturer offers, Harring advises. This normally costs little or nothing, and the information can easily be downloaded to your PC with an inexpensive connector harness.
And remember to keep receipts for anything you buy. Tools are tax-deductible, and so is a shop if it is built specifically for the purpose of truck maintenance and parking, says Russell Fullingim with Truckers Financial Service in Bloomington, Calif.
Whether you stick with simple tasks or become your own full-service shop, acquiring the right tools is a step toward saving money and spending more road time actually on the road.
BE CAREFUL, SAFE WHEN MOUNTING TIRES
Fleet owner Keith Harring learned long ago that installing and rotating his own tires saved a lot of money. Tommy Vajdic and Gordon Bow both do theirs and use impact wrenches to do the tough job of removing wheel lugs. Air-powered impact wrenches range from $500 for a 1/4-inch to $1,500 for a 1-inch.
You can’t remove the wheels until the truck is safely supported up in the air on something as solid as granite. You need four 12,000-pound jack stands and a floor jack rated at 18,000 to 20,000 pounds, one that uses hydraulic fluid to multiply the force put on the handle. These cost as much as $2,700 new, but Earl Evans has found you can floor jacks for as little as $300 to $500 at auction when repair shops or trucking companies shut down.
Tire beads are easily damaged if pried onto the rim without spreading out the prying force. You don’t need a tire machine, but you do need the proper tools, what Bow calls “tire spoons” because of the way they look. A typical set can be had for $475. You will also need a bead-seating tool, which is a small air tank and valve. The tank is filled from your shop air compressor and used to force a blast of air into any tire that’s reluctant to pop onto the rim.
The old exploding-ether trick is one Bow refuses to risk life and limb on. Tire makers universally caution that such treatment does casing damage that puts your life at risk later.
Special tools for cradling single or even dual Class 8 tire/wheel combinations are also essential for avoiding injury.
To go further in this direction, you’ll need the super-large socket wrenches, pullers and installers needed to repack and properly torque wheel bearings and replace their seals. This work is extremely exacting, but experts such as Evans and Bow do it all the time, making frequent bearing maintenance inexpensive. This attention to detail saves money on replacement bearings and seals and makes losing a wheel just about impossible.
If you specify low maintenance hubs and want to replace sealed cartridge bearing units, you need to graduate to torque multipliers and higher-rated torque wrenches to install their special, high-torque retaining nuts.