The TIREMAXX wheelend, hoses and rotary seal.
One of the oldest trucker tricks in the book is beating on a rig’s tires with a club to look for a flat. A tire that’s leaked to almost empty will show up this way. But most leaks are slow, and the pressure won’t change enough for you to detect anything different until long after both the tire and your fuel economy have suffered. In fact, many tire company experts have challenged truckers to detect tires 10 or 20 psi below correct inflation pressure this way and won the challenge.
You need a tire gauge. Or an automatic tire inflation or low pressure warning system.
Pressure warning systems are cheaper and could be effective if you’re religious about maintenance on your trailer. But a tire inflation system is the hot setup, according to Al Cohn, director of new market development for Pressure Systems International, and Jim Beverly, chief engineer of chassis control systems at Dana Corp. P.S.I. makes the Meritor Tire Inflation System (MTIS), and Dana makes the Spicer Tire Inflation and Monitor System (TIMS).
The big advantage of a tire inflation system is that it keeps a tire that has a typical leak at the proper pressure, minimizing damage, while allowing you to continue rolling down the road to the next service stop.
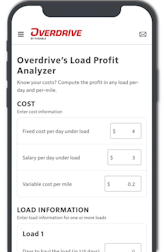
The importance of proper inflation
Running at 90-110 psi, a tire squirms very little, which means it rolls freely, gives good fuel economy and stays cool. Running at 10 or more psi below what it’s designed for actually deprives the tire of the structural strength it needs to support the load. The result is that the rubber flexes violently as you drive, creating friction, overheating the tire and causing serious damage.
Tires are so sensitive to heat because they’re put together at relatively low temperatures. As heat is added, the various rubber parts are “vulcanized” together with powerful adhesives derived from rubber. The process produces an unusually powerful bond, like heat-treating metal engine parts. Tires are vulcanized at temperatures in the range of about 260-300 degrees Fahrenheit.
When a tire overheats, it approaches the temperature at which the vulcanization occurred, and the adhesives soften again and lose their grip. Those road alligators you see are the result of tires getting so hot the bond between tread and casing has been devulcanized.
Justifying the cost
A system costing up to $700 or more before aftermarket installation may sound too expensive to bother with. But inflation system manufacturers argue that you need to better understand the real costs of under-inflation in your operation. True, if you gauge your tires every few days so they remain within a few pounds of their ideal inflation pressure, such a system might be little but a luxury. But not every driver does it, and drivers rarely feel as responsible for the equipment as owners. If you run a small fleet and have a hired driver or two, a system like this could pay for itself in short order. The many financial factors at stake when it comes to tire inflation add up to a lot more money than most realize.
What normally happens when a tire leaks down? Most tires are in sets of duals, and leaky duals are not obvious to the driver the way slightly under-inflated steer tires or wide singles are. A dual tire that’s gotten a large puncture and has been neglected for a few days can leak down to the point at which the other tire is carrying the load alone. Both tires are likely to be damaged, because the inflated tire will carry almost twice its recommended load.
Meanwhile, the leaky tire’s tread scrubs along the road, creating even more heat and direct physical damage. It’s no wonder tires are any trucking operation’s second largest expenditure.
One of the biggest, and least obvious, consequences of low pressure, say both Cohn and Beverly, is tire casing damage. Even if a tire doesn’t get hot enough to cause tread separation, heat, especially over a long period of time, will weaken the casing. The damage may not show up before careful inspection prior to retreading. Every damaged casing reduces the cost savings available through retreading. Even if you don’t retread, used tires with strong casings are worth money.
Another factor, says Cohn, is fuel economy, which drops by 1 percent if pressure is 10 percent low, 2 percent if 20 percent low, and more than 4 percent if 30 percent low. Additional factors include irregular tread wear, which drastically shortens tread life and often creates annoying handling problems.
The biggest costs associated with tire maintenance are those related to roadside service. Reducing the number and cost of service calls alone has enabled many fleets to figure the investment in tire inflation systems has paid for itself in under two years’ time. Add to that the potential costs not only of new tires (because of casing damage) but also unfamiliar vendors’ overcharging and potential DOT fines, and the numbers reach significant totals.
Both Dana and P.S.I.’s inflation systems, and most others, will actually maintain pressure in the tire when it receives a typical puncture.
“The inflation capacity is limited by the air system capacity, but most punctures don’t take all that much air,” Beverly says. “The rubber actually flows back a bit around the nail, and the systems are capable of keeping the pressure up.”
The payback calculator for the Meritor Tire Inflation System (at this site) lets you input costs to show the percent return on investment in the system after two years. Populate the fields by clicking the “Sample” link above the calculator and type over the numbers with your own. In addition to the calculator’s “sample” numbers, at $320 per tire, $160 per service call, 100,000 trailer miles per year and a 10 percent increase in tire life a payback of more than 275 percent is yielded on the original $725 cost of the system plus the $838 cost of installing it in a fleet shop.
Information on the Dana Spicer TIMS system can be accessed by going to the Roadranger website: www.roadranger.com. Under “Products and Solutions” click on “Tire Management,” then click on “Spicer TIMS (Tire Inflation and Monitor System).” There, Dana predicts a $150 savings in fuel, a number based on 6 mpg and $2 per gallon, and mileage data accepted by ATA’s Technology and Maintenance Council for tires underinflated by 10 percent. Other projections include a $320 savings in uptime, another $320 for extended tire life, and a $300 savings per road call for labor alone.
How they work
Tire inflation systems take advantage of the brake system’s high-pressure air. The MTIS is connected to the trailer air tank via a pressure protection valve that, in the event of excessive tire leaks, insures against the brake-system air pressure going below a safe level. All inflation systems include such protection.
The input line from the protection valve is connected to a protective control box mounted on the trailer subframe. The box includes a mechanical pressure regulator that regulates at the pressure specified when you order the system and can be adjusted in the field if necessary.
The box monitors the flow of air into the tires and illuminates a light on the front of the trailer, where the driver can see it in his mirror, if the volume of air needed indicates a leaking tire. A simple network of hoses carries the air to fittings that are tapped into the two axle tubes in the tandem. The tubes themselves are kept pressurized to supply air to the system hardware at both ends.
A different welsh plug and hubcap from what was originally on the axle allow the installation of a “stator.” The stator is a stationary pipe that runs through the plug and hubcap and carries air to a rotating seal at the end of the axle. The rotating seal carries air, via two lines, to each tire in the dual pair. Check valves in each of the two tire air lines keep air loss from one tire from affecting the pressure in the other. The Meritor system can be ordered with a Thermalert system to alert the driver of an overheated wheelend.
The MTIS is unique in some respects, but it shares many basic design characteristics with other systems on the market, including the Hendrickson TIREMAAX system (though it comes only as an integral part of certain Hendrickson trailer suspension systems).
The Dana Spicer TIMS has many similar parts but supplies air pressure through braided steel hoses and a standard hubcap rather than pressurized axles. It has rotary seals inside the spindle at either end of each axle, with a hose to each tire that includes a check valve, but it functions quite differently when it comes to inflating the tires.
Beverly describes it as an “intelligent” system that “uses a processor rather than a simple air pressure regulator.” The processor works via a sensor on a pressure manifold connected to all four tires. It measures the pressure at startup, then every 10 minutes afterward. If any tire has low pressure – and there is plenty of pressure in the air brake system – a solenoid will open and supply inflation air “at a good rate,” according to Beverly. Once the tire has been inflated, the system will be depressurized to maximize the life of the rotary seals.
The Spicer TIMS system can be integrated with Bendix ABS for simplification of components and installation.
One all-important point: Once you get a leak, don’t just rely on the system’s ability to keep the pressure up. Have the tire fixed properly, which includes removing it from the rim and sealing the inner liner, not just plugging it from outside. This is the only way to protect the casing cords from potential rusting, which can ruin the entire casing or may even result in a blowout.
Installation and maintenance
Many of the systems can be installed aftermarket, in addition to being available when purchasing a new trailer. Installation can be performed by any competent shop that works on truck components. It’s usually about an eight-hour process for a competent do-it-yourself mechanic, though it is complex enough that you should not attempt it unless you’ve been working on trucks for some time.
Installation typically involves replacing the welsh plug in the end of the axle with the inflation system plug, drilling holes and tapping various connections, running hoses and wires, and mounting the control box on the trailer subframe and the warning light on the front of the trailer. It’s important in all systems to pressurize the axle to make sure its interior is clean before the plug is installed.
The systems have filters, but air brake systems that have a good, properly maintained air dryer normally supply air that contains few contaminants. Cohn claims the MTIS’s filters virtually never need replacement. Basic mechanical inspections of hoses and connections for damage, and periodic soap-and-water checks of system hoses and connections while pressurized to reveal leaks, are among proper maintenance concerns.
The Spicer TIMS supplies diagnostic trouble codes, somewhat like ABS does, via either blink codes that can be easily read out of the processor, or free laptop computer diagnostic software.
Similar tire inflation systems are also manufactured by Airgo and Vigia. A number of air pressure monitoring systems include Link Manufacturing’s Cat’s Eye, which is simple and makes it easier to inflate both duals, as well as Michelin’s eTire System and Stemco’s BAT RF, which also provides easier inflation access. The last two are mainly intended for large fleet operations and use remote electronic readers.
For More Information:
Airgo Systems
(405) 844-5825
www.tireinflation.com
ArvinMeritor
(248) 435-1000
www.arvinmeritor.com
Dana Commercial Vehicle Systems Group
(800) 826-4357
www.roadranger.com
Hendrickson Trailer Suspension Systems
(866) 743-3247
www.hendrickson-intl.com
Link Manufacturing
(800) 248-3057
www.linkcmp.com
Michelin U.S.
(866) 866-6605
www.michelin-us.com
Pressure Systems International
(210) 222-1926
www.psi-atis.com
Stemco
(800) 527-8492
www.stemco.com
Vigia
(877) 777-2337
www.saferco.com/vigia.asp