Regular tire pressure maintenance results in longer casing life and better fuel economy.
Would you replace an expensive shoe just because it had a worn heel or sole, or get a shoemaker to resole it and replace the heel? The same thinking applies to tires, says Harvey Brodsky, managing director of the Tire Retread Information Bureau. Like a high-quality shoe, tire casings are designed for a far longer life than the original tread, Brodsky says.
What’s the biggest reason to use retreads? Your tire costs are second only to your fuel costs, and retreading substantially cuts those costs. While a new tire will cost more than $400, a retread costs only $150, Brodsky says.
Of course, everyone has heard retread failure horror stories. Proper retreading is no simple matter, so occasionally things go wrong, especially if the job was done by one of the few “bums” in the business that Brodsky admits still exist. However, there is one simple key to avoiding retread failure, or indeed tire failure in general: the casing.
The most common myth about retreads is that roadside “alligators” are tread sections a retreader failed to attach securely. In fact, independent surveys confirm that most rubber pieces left on the road are casing failures, not tread failures, and they are as likely to come from new tires as from retreads.
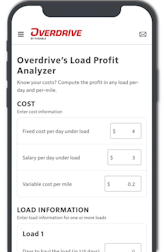
The vast majority of these tire shreds contain wire, which retreaders don’t insert in the first place, says Brad Reiners, marketing communications manager at Bandag. That wire is part of the original tire maker’s casing, the inner portion that supports the load and that the tread is attached to. If you can see wire protruding, it’s a casing failure.
New tires and retreads are identical in structure. The original tire manufacturer builds up the casing out of many rubber compounds and then attaches the tread. Much the same thing occurs in “pre-cure” retreading, in which a previously molded tread section is installed on a tire casing. The only visible difference is a small seam where the new tread meets the casing. A casing that has been kept in proper condition nearly eliminates many of the causes of retreaded tire failure.
How do you care for casings? Proper inflation is by far the main thing. Underinflation and its close cousin, overloading, account for the lion’s share of tire abuse.
While thumping a tire may tell you whether it’s absolutely flat, it cannot accurately read the pressure. “It’s almost like pounding on the hood to see if your engine needs oil,” Brodsky says. “Use a gauge and check the tires when they’re cold so you get the most accurate reading.”
Running a tire even 10 to 15 pounds too low will greatly increase the flexing and heating of the casing as you drive. A tire that’s 20 pounds underinflated has been subjected to so much stress it should be removed and inspected, says Goodyear’s Pat Demianenko, North American retread business development manager. Overloading causes similar damage because it also increases the flexing of the casing.
Inflation is critical because air gives the tire its strength. Air is elastic, efficiently absorbing road shocks and rolling effects so that little heat is generated. Reduce that air pressure, and the tire flexes, generating a great deal of internal friction because rubber is far less malleable than air.
Both new and retreaded tires are put together by “vulcanization,” which uses heat to fuse the parts together with rubber-based adhesives. Vulcanization occurs at 280 to 300 degrees; run a tire when it is underinflated or overloaded, and its highway temperature approaches the vulcanization temperature. This can reverse the process that put it together, so that the tire comes apart.
The heat doesn’t affect only the vulcanized parts. Severe overheating causes the steel cords to lose their strength, too, so they begin to move out of their proper relationship to one another. The extreme result is the broken cords sprouting from alligators. The flexing has heated and softened the wire until it broke apart, as a coat hanger bent back and forth eventually will snap. And this is not easily done with the high-quality, flexible wire used to construct casings, so an alligator on the roadside likely is a relic of a severely abused tire.
If inflation maintenance is driving you batty, look at a tire inflation system. Many will pay for themselves in less than two years because of savings in emergency calls, the manufacturers say.
They also save fuel. Al Cohn of Pressure Systems International, which makes the Meritor Tire Inflation System, reports that fuel economy drops by 1 percent if pressure is 10 percent low, 2 percent if 20 percent low, and more than 4 percent if 30 percent low.
Tire casings also can be injured by running mismatched tires in dual positions. The tire with the larger diameter ends up overloaded, while the smaller one eventually experiences scrubbing of the tread. When both tires overheat, energy and gobs of fuel are wasted.
Significant misalignment, a critical issue on 18-wheelers because of the length of the trailer, often has a similar effect because the tread actually scrubs sideways, Brodsky says.
A helpful way to preserve a casing is to make sure the tread never wears too thin – below 4/32 on steers and 2/32 on the other tires. This also will keep DOT inspectors happy. Several tire experts, however, advocate retreading well before reaching those limits. Demianenko thinks observing at least 3/32 as an overall limit pays off in added casing protection.
One obvious reason a little extra rubber goes a long way is that the typical puncture is caused by objects, such as carpet tacks, that would never reach the casing if the tread were thick enough. Preventing punctures not only eliminates leaks but protects the casing from the damage that would occur from running underinflated until the leak was detected.
If the casing is penetrated, you still can save it most of the time – if you take it to the right tire repair shop that won’t just plug it and call it done. A high-quality repair means the tire is removed from the wheel and repaired with a vulcanizing process that seals the inner liner. Plugs just seal in moisture; they often result in rusted cords and catastrophic failure. “I’m dead set against plugs,” Brodsky says. “Fix the casing from the inside.”
A high-quality casing, properly maintained and properly repaired as needed, is good for two more cycles after its first life. Retreads are legal on steer tires, though it’s more common to run virgin tires there and then retread them at other positions. Drive tires often will be retreaded once or even twice, then switched to the trailer for one more cycle.
Take care of the casing and pick the right retreader, and you’ll greatly enhance your chances of cutting tire costs to the bone without risking an expensive and dangerous failure.
TAILOR RETREADS TO YOUR APPLICATION
As a group, retreads have one advantage over new tires other than cost. The pre-cure process, in which tread is molded by itself and later vulcanized to the tire, has enabled the creation of a bonanza of new tread designs you can get only on retreads.
In fact, you can select among application-specific tread designs that last longer because they are ideally configured for certain uses. “Choosing the ideal tread pattern – rib-or lug-type tread design – depends on the type of operation and traction requirements, as well as other similar factors,” says Glenn Stockstill of Michelin.
This is one area that separates responsible retreaders from the others, says Harvey Brodsky of the Tire Retread Information Bureau. “Don’t just let them pick up your tires,” he says. “Spend time with the retreader so you can learn something about tread design and you can tell them about how you use your vehicles. Deal only with people who know what you are doing in your operation.”
A Bandag dealer, for example, “will look at wear, appearance, snow or mud starting traction, ice or wet stopping traction, and fuel efficiency needs to identify an application-specific tread suitable for your needs,” spokesman Brad Reiners says.
On trailers, tread pattern is less of a concern. Trailer tires often are on the last of three cycles, which means they receive a thinner tread anyway. This minimizes friction and heat on the casing, which is older by the time it gets back there.