Advanced filtration is not a new concept, but it’s getting more attention lately for its ability to extend service intervals, and, soon, to provide added protection against the extra contaminants expected in diesel engines built after October 2002.
Despite their potential benefits, the systems are getting mixed reviews because they’re reportedly often used as substitutes for proper maintenance procedures.
Most of the devices and all of the debate involve technology designed to deep-clean oil. These are bypass filters that route a small portion of the oil flow through extremely narrow passages capable of snagging particles as small as a half-micron. Standard filters, by comparison, catch crud in the 12- to 20-micron range.
Proponents of the systems say cleaner oil lasts longer and does a better job of protecting internal parts against wear. Although such claims seem logical and indisputable, some people say they are also exaggerated and misleading.
Jim Pirie, an application engineer at International, says engine makers require all approved filters to meet a certain cleaning standard, and anything beyond that won’t necessarily result in greater component longevity. “It’s just an additional cost without a lot of benefit,” he says.
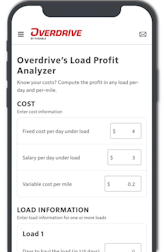
Pirie also takes exception with the promise of greatly extended drain intervals. “Filter manufacturers have encouraged people to push their [drain] limits out further than any engine guy would like to see,” he says, “even further than the threshold for harming an engine.”
Pirie says contamination isn’t the only reason for changing oil. “Over time, the oil’s additive package gets depleted, and the only way to replenish it is with new oil,” he says. “You can’t just dump in a bunch of chemicals and hope for the best.”
Surprisingly, that’s exactly what some vendors have encouraged truckers to do, says Ross Iwamoto, a research scientist at 76 Lubricants. He says aftermarket additives are not a good way to fortify oil. “You can’t possibly hope to match the original additive chemistry of all the oils on the market,” he says.
Additives serve several functions as antifoam and antiwear agents, corrosion inhibitors, detergents and soot dispersants. Iwamoto says soot will become increasingly troublesome late next year, after engine makers introduce exhaust-gas recirculation to achieve federally mandated emissions standards. He predicts soot levels will double, from 5 percent to 10 percent. Oddly, such a jump would affect additives more than filters.
A lot of soot is smaller than 1 micron, so it easily passes through most filters. Dispersants are designed to keep these little bits from clumping together, creating bigger globs and, ultimately, forming sludge. The latest oils, PC-9, are supposed to be able to handle up to 9 percent soot – if their additive packages are in reasonable condition.
With current engines, Iwamoto says, additive packages will go a considerable distance in line-haul operations as long as premium oils and filters are used and regular analysis is done. “We’ve seen quite a few fleets go to 40,000 or 50,000 miles,” he says. “More typically, though, it’s somewhere in the 25,000 to 30,000 mile range. There are some fleets going 80,000 or 100,000 miles, but those are definitely experimental, using special oils. They’re also trading off a little bit on durability.” He says the industry’s average drain interval is about 22,000 miles.
Iwamoto says there are several good filters on the market. “I think fiberglass might have a little better performance than the traditional paper media,” he says. “The centrifugal products also do a good job. They basically work off the density difference between the soot and oil.”
Jim Weaver, general manager of the Spinner II product division of T.F. Hudgins, agrees. Spinner II is a cleanable, reusable centrifugal bypass filter that uses the engine’s oil pressure to spin an internal turbine at roughly 6,000 rpm, creating enough gravitational force to fling particles against the filter’s interior wall.
“The product differs from those using a barrier to screen off foreign matter because it’s not limited in the size of particles it will remove,” Weaver says. “We can actually take out material as small as 0.1 micron.”
Weaver says centrifuge-filtering technology has been around for about 50 years. It is first-fit equipment on 40 brands of engines around the world, including Mack and the industrial models of Caterpillar and Cummins. Spinner II is available through all truck manufacturers’ option books.
“Our product has an advantage over some of the others because it’s reusable,” Weaver says. “Customers never need to replace the filter, just a couple of O-rings. It is also very reliable. There isn’t a heck of a lot that can go wrong with it.”
In March, Fleetguard started competing with Hudgins for centrifugal customers when it introduced its Centriguard system. John Clevenger, a Fleetguard product group manager, says the company didn’t go after this business earlier because there were less expensive ways to achieve the same level of filtration. He says next year’s engines raise the ante.
“We believe multistage filters will be required,” he says. Centriguard provides that with full-flow, bypass and centrifugal areas, all wrapped inside the same can.
Clevenger says aftermarket bypass filters might clean oil well, but many of them don’t meet the minimum flow-rate standards set by engine makers. “Cummins and Detroit Diesel both say [a bypass filter] ought to average 10 percent of the full-flow filter’s volume, which is somewhere between 20 and 30 gallons per minute,” he says. “That means a bypass should handle 2 to 3 gallons in the same time. There are products on the market [whose makers] claim they can filter down to .25 microns. Yet, their flow rates are .05 to .10 gallons per minute. Cummins considers a filter plugged when it’s flowing .03 gpm.”
Furthermore, particles smaller than 2 microns can’t be accurately measured, so it’s hard to understand how some manufacturers can promise to clean below that level. “Technically, every filter catches some sub-micron debris,” Clevenger says.
John Guzek, owner of Energy Enterprises in Green Bay, Wis., has been in the bypass filter business for about 20 years. He markets a technology that was developed to maintain the oil quality of nuclear powered submarines for many months, despite their constant use.
“Submarines can’t dump fluids during a run,” he says, “so they needed a system to keep oil clean for a long time.”
Guzek says his first task in meetings with potential customers is to educate them about the product and its potential. “It is not immediately obvious what this can do for an engine,” he says, “and if you simply follow a manufacturer’s recommendations and believe that’s the best you can get, then you’re kind of locked into a box. This is more out of the box thinking.”
He describes the product as a “depth filter,” a sort of sponge or maze that oil must pass through while circulating. He says the design sets it apart from cartridge filters, “which are more like screen doors: particles either get through or they don’t.” After a few months of use, he says, his product’s performance actually improves because its cellulous media pores become narrower, making it more difficult for oil to penetrate. This restricts more contaminants and, equally important, absorbs more water.
Water, in the form of condensation, is a natural byproduct of engine operation, says Guzek. “When you separate water from oil you’ve reduced the rate of additive package depletion and stopped the formation of sludge, which always contains water,” he says.
Guzek says the combination of deep filtering and water removal gives his system the unique ability to eliminate oil changes in typical class 8 line-haul trucks.
A typical owner-operator spends $550 to $750 a year on oil changes. Many believe this is cheap insurance compared to the cost of major engine repairs. Recommended change intervals vary widely across the industry, and they depend on environmental, mechanical and operating conditions, idle time, and the quality of fuel, oil and filters.
It’s always prudent to consult a truck or engine dealer before investing in a bypass filter or embarking on an extend-drain program. Neglecting to do so could void every warranty within 50 feet of your truck.