The good news for 2007 engines is that maintenance and fuel costs will be affected only minimally, according to engine makers. With more time to do field testing than
for the 2002 engines, they are also confident that reliability won’t be a problem.
Achieving the huge step in lowered emissions, however, even with the help of new low-sulfur fuel, will mean a significant price increase. It also puts tremendous demands on the technology, with turbo boost pressures as high as 70 psi, says Steve Egleston, engineering leader for Flexfab, a hose manufacturer.
“The 2007 engines will run hotter, use more boost pressure, and have oil vapor and corrosive EGR gases introduced into the intake air,” Egleston says. “This means we have had to rethink the materials we use for these critical hoses.” But an exotic lining, reinforcement of the bellows and new construction methods have enabled Flexfab to do its part for the new engines, Egleston says.
Engine makers are doing much more than that to meet the stringent standards. All engines made starting Jan. 1, 2007, must drop particulate emissions to .01 grams per horsepower-hour, a tenth of present levels. At the same time, engine makers must cut nitrogen oxide in half, to 1.2 grams per horsepower-hour. In addition, any crankcase emissions will be considered part of the NOx output.
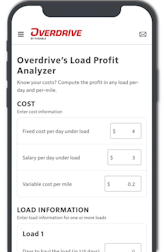
REDUCING PARTICULATE
The only way to cut particulate to required levels is to add a diesel particulate filter. This device will sit where the muffler is now and also will reduce noise levels. Its job is to collect the unburned soot and hydrocarbon particles and hold them in place until they burn off. Since diesel exhaust normally contains plenty of oxygen and heat, this will be easily done in over-the road applications.
There are three DPF challenges. The first is that diesel exhaust cools under light load because the airflow through the engine does not drop as much as the flow of fuel. Burning the accumulated soot and hydrocarbons when the engine isn’t working hard enough will require periodic heating of the exhaust. Getting the fuel to ignite and burn safely and cleanly is a minor challenge.
The second challenge is that sulfur itself is a source of particulate, and it can readily poison the DPF, too. The petroleum industry will be lowering the sulfur in diesel fuel from its present 500 parts per million to 15 ppm or less. Regulations require that 80 percent of diesel fuel be available as this ultra-low sulfur diesel by 2007.
The third DPF challenge is that exhausted ash collected in the DPF won’t burn off no matter how hot it gets. Ash is composed mainly of additives that get into the exhaust via the oil the engine consumes. The primary ingredient is the total base number additive that combats acidity in the oil. This issue will be partially dealt with through a new oil standard, tentatively called PC-10. This oil will provide adequate TBN protection with a strictly limited amount of ash. The ash that does accumulate will have to be removed through a maintenance operation.
REDUCING NOX
For the most part, NOx will be reduced via the exhaust gas recirculation designs of all 2002 engines except Caterpillar. This means more EGR for Cummins, Detroit Diesel, Volvo, Mack and, very likely, the new Class 8 engines from International. Increased EGR means higher cylinder pressures and increased heat rejection.
Hardware remains very similar for Cummins and Detroit, although Detroit mentions an “enhanced” Series 60 without giving details. Detroit will also introduce a new engine that will be available only in Freightliners and will be built in four different displacements. A 14.8-liter version will be the first. It reportedly may include some exotic new hardware.
In the case of Volvo and Mack, a new engine line will be produced. Because of higher levels of EGR, the pulse EGR system Volvo used on the VED-12 will be replaced by a variable geometry turbocharger. These engines will provide better throttle response, says Tony Greszler, vice president of Volvo Powertrain.
Caterpillar will continue its basic hardware and ACERT technology, though with tuning changes to further lower NOx. The only basic NOx-related change will be clean gas induction. Bob Keene, customer satisfaction manager at Caterpillar Engine Division, says CGI differs from EGR. For example, because ACERT technology means less NOx in the combustion chamber, the volume of recirculated exhaust will be negligible, Keene says. Also, Caterpillar will draw post-DPF exhaust, meaning the lion’s share of soot will already be removed.
MAINTENANCE REQUIREMENTS
The biggest maintenance issues will be the time and cost of getting a truck or engine dealer to clean the DPF. Not only will the DPF, reportedly weighing as much as 300 pounds, require special handling equipment, but its cleaning will need to be done in a sophisticated vacuum chamber.
The Environmental Protection Agency mandates that the filter must go at least 150,000 miles before it needs cleaning. Manufacturers believe that in typical over-the-road driving, it’s likely to go much farther. Cummins’ Cyndi Nigh says units in linehaul service should “require service only once every four to five years.” The filters will be designed to last the life of the vehicle.
The Cummins ECM will monitor the performance of its Fleetguard DPF, and prognostics will indicate service intervals via the RoadRelay or Insite systems. This is likely to be an integral function of all onboard diagnostics anyway, since filters that are clogged with ash will increase engine backpressure, which interferes with airflow through the engine.
Cleaning will take one to two hours, and the labor charge will probably be the bulk of the cost. If your dealer’s hourly labor rate is $90, you’ll probably get out the door for $150 to $200, including a small fee for disposing of the ash. But the whole matter will likely be handled “when you come in for periodic maintenance,” Keene says. For those desiring quicker service, many outlets may offer exchange programs, simply switching your filter with one that has been cleaned.
The next potential maintenance issue is the closed crankcase system. Keene says the Caterpillar system “will be integral, with the gases passing through the DPF,” so DPF maintenance will take care of the crankcase system.
Cummins engines will use a simple filter manufactured by Fleetguard that will require annual replacement. At Volvo, “We don’t have any regular maintenance planned for the crankcase ventilation system,” Greszler says.
Another issue is lubricity of the fuel. Scrubbing out the sulfur removes some parts of the fuel that serve as lubricants for the injectors. Additives that improve fuel lubricity are abundant. Greszler reports that a lubricity requirement has been included in American Society for Testing and Materials specifications for the new fuel. This means that lubricity additives will be put in by the fuel suppliers, Cummins and Volvo say.
The manufacturers have already done a lot of fleet testing using the new low-sulfur fuel and the new lower-ash oils and have begun to determine change intervals. The reduced sulfur content helps reduce the need for TBN because crankcase acid is created when sulfur combines with oxygen. In most cases, drain intervals are expected to be the same as with current models or better, spokesmen say.
Nigh says 2007 engine longevity should be as good as ever. Stable architecture assures customers that the engine they are operating today will be the same basic engine in 2007 with the addition of exhaust aftertreatment. Cummins officials also are optimistic about having had more time to integrate their engines with truck systems than in 2002.
Volvo’s new engine is designed for higher cylinder pressures and will offer “enhanced durability,” Greszler says. The Series 60 design has also been “enhanced” in unspecified ways.
“With ACERT, Caterpillar is likely to have the lowest heat rejection of all the engine manufacturers,” Keene says. That would tend to help engine life and may also help reliability in other areas, for example the underhood hoses.
“We are already building 2007 C13 and C15 engines on the production line,” Keene says. “We are building and shipping a large quantity in the next two months.”
FUEL COST AND ENERGY
Manufacturers say their 2007 engines will be about as efficient as they are today. But fuel that is more highly refined to eliminate the sulfur will cost as little as 3 cents per gallon more, according to an old EPA estimate, or much more, according to others.
Fuel that has been so refined also will be less dense and will have a 1 percent to 3 percent reduction in energy. Most observers are optimistic that as refiners perfect the process, the drop in energy content will be small. Fuel use will likely increase just enough to compensate for the decrease in energy content.
Detroit Diesel’s communications manager, Liane Bilicki, says the new fuel “will offer close to the level of fuel efficiency we see in our current products.”
Volvo’s Greszler says, “We are working to maintain at least comparable fuel efficiency between current and 2007 engines, but this is predicated upon having fuels with comparable BTU content.”
Since most trucks on the road will have to buy low-sulfur fuel, drivers of older trucks will use it, too. They will likely experience a similar slight increase in fuel consumption, helping make the post-2007 vehicles competitive.
Engine makers believe they will be competitive in performance and reliability as well. With more lead time for research and development than pre-2002, and with hundreds of engines being fleet-tested, they expect a smooth product introduction in 16 months.
HOW MUCH EXTRA COST?
Engine makers decline to give even rough estimates about the cost of the 2007 engines and their accompanying diesel particulate filters.
Rainer Schmueckle, then-president of Freightliner, estimated in late 2004 that the 2007 engine changes would add $4,500 to $6,000 to the cost of 2004 engines.
A truck dealer who declined to be identified, but who is familiar with retrofitting particulate filters, projects new engine costs at $8,000 to $10,000. Other reports also have listed estimates as high as $10,000.