Once upon a time, 40 years ago, diesels weren’t turbocharged, trucks weren’t aerodynamic and the cabover was king. Trucks had trouble starting when the temperature dipped below freezing. There were no seat belt or emission standards, 60 mph fully loaded was hard to reach and the average fuel economy was 4 miles per gallon.
Truck technology and design have changed a lot since then, thanks largely to the brilliant but mostly anonymous work of engineers who, bit by bit, changed trucks from inefficient, noisy, balky devices into the smooth, powerful, comfortable vehicles we have today.
“Back in the old days, drivers carried a lot of parts with them,” says Larry Strawhorn, vice president of engineering for the American Trucking Associations. “They’d often be seen by the side of the road changing parts like fuel pumps. With spoke wheels, the tire/rim assembly was a lot lighter than it is now, and you could heft it up onto the spokes with your back. With disc wheels, you’re less likely to see drivers changing their own wheels. The increased reliability of trucks has made life very different for the driver.”
Early technology
Until the 1970s, most trucks were powered by normally aspirated diesels. These engines, without the pressure boost of turbocharging, capitalized on work done by early diesel pioneers to increase output by increasing engine rotating speed. Nearly all were governed at 2,100 rpm. The most popular Cummins model was the NH-220, says Mark Conover, Cummins market manager for owner-operator/high performance fleets.
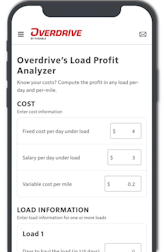
These engines ran at their best near the top of the operating range because rpm made the injection and combustion system work better. Drivers were instructed, above all, to keep the engine from lugging – exactly the opposite of the driving technique encouraged today. The minimum rpm under load was 1,500, and cruise occurred at 1,800 rpm and above. The most popular transmissions were very close-ratio 10- and 13-speeds.
Detroit Diesels of the early ’60s were two-strokes known as the 71-Series, with 71 cubic inches per cylinder. In the era before turbos, this design produced more power in a smaller engine envelope. Because of the relatively small cylinders, eight-cylinder models were popular, and 12 cylinders were available.
In this era, all diesels had hydro-mechanical injection systems that metered, timed and injected the fuel without electronics. Macks and Caterpillars used pump-line-nozzle systems, while Detroit used unit injectors and Cummins the PT pump and injector system. Caterpillar engines had pre-combustion chambers: separate, small chambers connected to the main combustion chamber via a narrow passage to more forcibly mix fuel and air.
In this time of much cheaper fuels, gasoline engines survived in many fleets running shorter hauls, Strawhorn says.
Many conventionals had rounded corners and windshields that tilted to the rear, but they looked a lot more aerodynamic than they were. Trucks needed to conform to overall length standards, so the cabover was king in many fleets because it could legally pull a longer trailer. Many cabovers looked like cigar boxes because of the need to preserve cab room in the short space.
Transmission revolution
In 1962, truck transmissions still had a single mainshaft and countershaft and could carry relatively little torque. With so many cabovers on the road, a major challenge was making the gearbox strong, yet short enough to fit into the chassis. The limiting factor was the need to make the gears wide enough for the teeth to carry the torque. In the early ’60s, significant increases in low-end torque made gearboxes just too big, Conover says.
A bright engineer at Fuller hit upon the idea of spreading out the stresses by making the gearbox wider and shorter and putting a countershaft on either side of the mainshaft. The countershaft gears could be half as thick because two of them carried the load. Even the mainshaft gears could be thinner because the torque was now split between two meshes opposite one another, rather than focused in one location. Mainshaft gears would now float on their teeth between the opposing countershaft gears when not engaged, instead of each needing its own bearing. Floating gears, which could move around during engagement, also reduced shift effort. Fuller introduced this twin countershaft design in 1963.
Late 1980s International 9670 has a roof-mounted air deflector, part of the gradual evolution from boxy to aerodynamic.
A different way of life
Strawhorn, who once drove an International K-model, claims cab ventilation was so poor drivers sometimes drove while standing on the running board and steering through the open door. He also recalls when tires were of bias ply design with cotton cords as reinforcement.
“With trucks running at higher speeds more and more of the time, tires had to change with the times, so now we have steel-belted radials,” Strawhorn says.
“In fact, vehicle and highway design always parallel one another. Today’s highways haven’t changed for a long time, so congestion is building. Now, we’re seeing changes designed for managing crowded situations. We have lots of short, panic stops, so we need front axle brakes to shorten stopping distance. We then installed ABS on the truck to prevent loss of control.”
Another major change, starting with deregulation of the industry in 1980, was the elimination of overall length limits and the limitation of trailer length, Strawhorn recalls. That, in turn, marked the beginning of the end for the cabover.
“Other big changes in the cab include designing the roof structure to support the various air dams required for aerodynamics,” he says. “And a substantial redesign of interior space, partly so the driver has survival room in the event of a crash. This and the mandated use of seatbelts, which came along in the 1980s, have saved a lot of truckers’ lives.
“Even the Mack Bulldog has changed. Lighter fiberglass parts made it possible to make the entire hood a tiltable assembly. Truckers could then get better access to the engine compartment. But Mack had to make the tail and ears of the bulldog less pointy so you could use it as a grab handle when tilting the hood.”
Modern power
Mack was responsible for changes of more significance than making a smoother hood ornament. In the early ’60s, Mack engineers found the turbocharger made it practical to design an injection pump governor that would pump more fuel when the engine was lugging down. Traditional engines would have belched smoke with such a change, but with a properly matched turbo, the extra fuel merely heated up the exhaust, spun the turbo faster and increased power without smoke. The result was the Maxidyne of 1966, a diesel with enough torque rise to allow the use of only five wide gearsplits without power loss after an upshift. Turbos were adopted on all diesels by the ’70s.
While the 5-speed remained a Mack novelty, the industry embraced the torque rise. At the end of the ’70s, the 13-speed was the most popular transmission in the market, but by the mid-1980s wide-ratio 9-speeds were the order of the day in most fleet trucks.
Mack also scooped the industry in 1982 with the introduction of the Econodyne, the first diesel with an air-to-air aftercooler in front of the radiator. Air-to-air increased power while reducing emissions and fuel consumption. The rest of the industry followed suit.
Momentous changes in the industry during the 1980s produced the very different engine we have today. A new era of emissions standards and fuel economy caused Detroit to scrap the two-stroke 92-Series for heavy truck applications, though not until it had sported the first electronically controlled unit injectors ever built. The successor was the Series 60, introduced in 1987. This was an inline six with a 12.7-liter displacement, two-piece articulated cast iron pistons, and an overhead cam and free-breathing valve arrangement.
Caterpillar introduced the 3406A in 1974 but later replaced its pre-combustion chambers with direct injection for better fuel economy. The 1994 3406E gave Cat an overhead cam and electronic unit injectors. Further changes to this series have resulted in the C15 and C16 of today. Cat has led the horsepower race since its inception.
Until 1991, Cummins’ Big Cam I-IV 855 cubic-inch engines were equipped with the cool-water Optimized Aftercooling system, designed to prevent overcooling of intake air, Conover says. Air-to-air was introduced with the N14 in ’91. Cummins’ 1997 Signature 15-liter dual overhead cam engine added a separate injector camshaft, so what had been the injector cam could optimize engine braking, and put Cummins in the 600-hp category. ISX models with lower power ratings followed in 1998, Conover says.
Volvo introduced its overhead cam, unit injector VED-12, 12-liter in late 1993.
Now, nearly all top-of-the-line engines have overhead cams, and all have totally electronic injection system control. Though still using an in-block camshaft, Mack’s E7, introduced in 1991, has the highest swirl combustion chamber in the market, says Mack engineer Wayne Wissinger. This and the E-tech unit injector pumps give it the longest oil change interval in the industry, he says. All domestic engines and the Volvo now have articulated pistons with an iron or steel crown, which handle heat and pressure much better than straight aluminum.
Through most of the ’80s, truckers had difficulty starting their engines after an overnight shutdown at 30 degrees. Now, most will start easily at 10 degrees or colder. Engines automatically idle faster during warmup, eliminating the hand throttle, and an electronic governor allows the driver to release the clutch without touching the throttle pedal. Torque peaks at 1,200 rpm or less and doesn’t die just below the peak, hanging in even below 1,000 rpm. Horsepower and torque have gone through the roof, with 500-plus horsepower engines common. Noise levels are astoundingly low.
Drivetrains
Fuller introduced low inertia in 1987 with the first 18-speed, allowing the driver to preselect split shifts. The 10-speed replaced the nine-speed as the most common fleet transmission during the early ’90s because faster axles were being adopted. But the biggest drivetrain changes of recent times have been the new electronic shifting options.
These use the power of engine and transmission computers and the data links that carry information between drivetrain components to float-shift the truck from gear to gear. Engine throttling breaks torque and then synchronizes engine and transmissions speeds for a perfect, clutchless shift. Gear changes are made by small electrical solenoids working on the shift rails atop the transmission. The latest electronic gearboxes also operate the clutch.
Whether slipping quickly through pre-selected split shifts, operating a light clutch, running effortlessly through the gears with an automated manual transmission, taking a steep hill without a single downshift behind a 600-hp Cat or Cummins, or just cruising with hardly a hint of the traditional diesel knock in their ears, most of today’s drivers know that, by yesterday’s standards, they are thoroughly pampered.
The Mack Model B was a classic, 1950s conventional that lasted in the market until 1968.
In with sleepers, out with cabovers
Ken Self, former president and CEO of Freightliner, recounts the “quick-change engine” tractor design of 1967. His company had developed a cab with plug-in connectors that allowed an engine switch in only 70 minutes. The engine switch worked fine, but the connectors were unreliable, and mechanics frequently eliminated them from the wiring and hoses during repairs.
Manufacturers do a much better job of cab development today than in the 1960s. In the past 20 years, set-back axles allowed for better aerodynamics, especially around the front bumper and wheels, and enhanced the ride by allowing room for longer, taper-leaf springs that react more gently to bumps in the road. They also shortened turning radiuses, even for conventionals. Putting air suspension on most drive axles and many trailers improved the ride even more. Cab sound and thermal insulation took giant leaps forward.
Another big change came in the hoodline, which became far more angled on most highway conventionals. This trend, begun by Kenworth with the T600 in 1985, is reflected in many models, including the Freightliner Century Class, Kenworth T2000, Peterbilt 387, International 2600 Series and Volvo VN. While Peterbilt still makes a few conventionals with long, straight noses, sloped hoods are offered even on traditional models. Mack’s Vision tractor was its 1998 entry into the low-nose tractor market.
Sleepers grew and in the early ’80s were integrated more effectively with the conventional cab. Joe Cacopardo, director of communications at Volvo Trucks, reports that the earliest fully integrated design was the White Integral Sleeper of 1984, introduced three years after Volvo bought White Motor Corp. The goals of integral design included making the cab larger, lighter and freer of structural problems and leaks. Integral design also made the cab assembly longer, allowing for a smoother ride on the cab suspension for the same reason a longer wheelbase improves ride.
A number of valiant efforts were made to save the cabover, including the ultra-aerodynamic Peterbilt 372 of 1989 and the flat-floor 9800 design from International in 1996. Everyone in the industry was astounded when they saw a true cabover with no doghouse, but the 9800 had only a four-year run. The Freightliner Argosy of 1998 even sought to make the climb to the front seats easier with optional motorized stairways that hinged out from the side of the cab. The Argosy is still produced, but in small volume.
The cabover design succumbed to conventionals as fleets did everything they could to attract and retain drivers. It was no secret that drivers preferred a hood or large car because of sleeper access, perceived safety in a crash and appearance. So the cabover has all but died, while the new breed of aerodynamic conventionals is the leading design of the 21st century.