Most engine manufacturers say 2010 will be like turning the clock back to the good old days
In 2002, diesels came with exhaust gas recirculation for the first time.
EGR put more stress on the engine, causing occasional failures of items like head gaskets and making the cooling system work a lot harder. EGR technology meant additional components like EGR valves and coolers and variable-geometry turbochargers that would occasionally fail. And it put a significant damper on fuel economy. Fuel usage increased because backpressure was needed in the exhaust system to drive exhaust back into the engine.
By 2006, the bugs with failed EGR valves and coolers and VG turbos were mostly a thing of the past. Engineers had even strengthened major internal parts to help guarantee durability. They recalibrated the ECM to meet the emissions standard while optimizing fuel economy. Thus, as 2007 approached, engines were running more reliably and had regained some of the lost fuel economy.
But 2007 brought increased levels of EGR to meet a still-lower NOx (oxides of nitrogen) standard and gave us the diesel particulate filter, or DPF, to meet a required significant drop in particulate from levels that already were very low. Lower-sulfur fuel, provided to cut particulate and preserve the DPF, together with the improved CJ-4 engine oil, meant better engine durability but more costly fuel and oil. In spite of increased EGR, engine-tuning tricks yielded fuel economy that was comparable with 2006 in most highway operations. But when the truck spends a lot of time under light load, a lot of fuel is used to regenerate the DPF. Also, at infrequent intervals, ash needs to be cleaned out of the DPF. All in all, not a pretty picture.
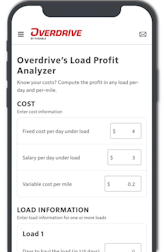
So what will 2010 bring? According to experts from most of the engine manufacturers, a breath of fresh air. It will be a lot like turning the clock back to the days before EGR became a factor.
SCR + less EGR = better engines
In 2010, the NOx standard will be an extremely low 0.2 grams per horsepower-hour, about 1/10 of what was allowed in 2004. Meeting this standard is difficult because low NOx is a diesel engine’s toughest emissions challenge. Diesels thrive on heat because it helps burn soot. Reducing NOx in the engine means making an engine that loves to run hot run cooler.
Until now, NOx has been reduced in the cylinder by re-circulating more and more cooled exhaust. Exhaust absorbs a lot of heat from the fuel as it burns, but it also adds heat, soot and acids to the engine and makes it work under greater pressure. Fortunately, there is an ace-in-the-hole called SCR, or selective catalytic reduction. The technology has long been used in power plants and factories to kill the NOx produced in big boilers. Fortunately, it’s practical to adapt it to a heavy-truck diesel.
This requires an SCR catalyst, a device about the size of a DPF and closely resembling an automotive catalytic converter in construction, together with a storage tank, pump, nozzle and microprocessor. A commodity rapidly becoming available at truckstops called DEF, or Diesel Exhaust Fluid, will be pumped into the SCR catalyst at a rate matching the engine’s NOx output. When heated in the catalyst, a chemical called “urea” is formed from the DEF and, as Ed Saxman, product manager for Volvo Powertrain, tells us, “Urea and NOx becomes nitrogen and water. That’s how SCR after-treatment works.”
SCR is so effective it will be quite practical for the 2010 engines themselves to emit more NOx than in 2007. This means the engine design rules will change in a positive direction for engine manufacturers implementing SCR. “Why are we going to use SCR to kill NOx? Because everything else the engine makes can be reduced by making combustion more efficient,” Saxman says. “By adding SCR to EGR, we can meet the standard so handily that we can actually back off the EGR from EPA ’07 levels.”
Gary Parsons, global OEM and industry liason manager at Chevron Oronite Co., LLC, believes the transition to SCR could somewhat resemble the adoption of the catalytic converter in the car market in 1975 because “using SCR increases the number of degrees of freedom in what engine designers can do.” One example of this, he says, is the fact that having some NOx in the engine exhaust actually helps reduce the need to burn fuel to regenerate the DPF.
Naturally, with DEF having to be pumped in on a continuous basis, it’s a commodity like fuel that must be replaced frequently and will cost truck fleets money – about as much per gallon as diesel fuel. Since minimizing the amount of DEF to the predicted 2-5 percent of the amount of fuel will help control the cost of operation, the engine makers will continue with technology that minimizes the NOx coming out of the engine. There will still be EGR, EGR valves, EGR coolers and variable geometry turbos, except in the unusual case of the Detroit Diesel DD15 series of engines (the DD13, -15 and -16 use a turbo-compounding turbine that drives the crankshaft to develop the exhaust system backpressure that forces the exhaust back in, rather than a VG turbo). Exotic fuel-injection systems that divide the traditional single shot of fuel going into several separate shots to reduce NOx also will continue, and Cummins will adopt the XPI common-rail injection system to allow this on their engines for the first time in 2010.
The big difference in 2010 will be that all the exhaust-handling devices won’t be working so hard, and neither will the engine. This will allow the engine to be tuned for fuel economy more effectively than it has been for some time. The end result will be lower running costs, even including the DEF, some engine makers say.
Part of the fuel savings will come from reduced DPF regeneration. With less EGR, there will be less engine-out soot, and the slight increase of NOx in engine exhaust will help burn off soot trapped in the DPF. In fact, Volvo claims that in most operations, their vehicles will see no active regeneration of the DEF. We may eventually see longer oil-change intervals, too, though the engine makers won’t allow that until they have a lot of experience with the engines.
What drivers need to know
The critical task for drivers will be remembering to refill the DEF tank. It looks as if truckstops will have DEF – finding it won’t be the challenge. But DEF won’t necessarily run out at the same time as fuel. Its consumption is highly variable.
Most engine makers are shooting for a system that carries enough DEF to last through two fuel fill-ups, an interval the EPA requested. But there may be times when the fluid lasts much longer and vice versa.
Drivers will receive a warning light when the DEF tank gets low, but if the fluid runs out, the truck will power down and eventually stop running. So drivers need to refill the DEF tank on a regular basis.
THE EGR PATH
Navistar is going to tough it out and will meet the standard in the cylinder, initially using credits earned over the years to allow them to run at 0.5 grams of NOx. Tim Shick, director of marketing for the engine group, says they will continue to recalibrate their MaxxForce 2010 engines to fully meet the standard by the time their credits run out.
Navistar does not like asking the driver and fleet to manage the DEF supply, dislikes the additional 250-500 lbs. of the SCR system and is concerned about the possibility of high DEF prices. The company firmly believes a sophisticated EGR system with more sophisticated engine calibrations, combined with improvements to their common-rail injection system and other design features like the combustion chamber in the piston, is the best way to proceed.
“Maintenance and related problems would go up without high-pressure common-rail,” Shick says. So the operating pressures and other characteristics of their common-rail injection system will be significantly upgraded. Such changes can control the amount of soot getting into the oil, as well as engine-pressure stresses, even with higher levels of EGR. Navistar’s approach could end up being a big success.
Some of the Best Engines Ever
Just about all the engines for 2010 will be slightly different from the 2007 models – and better. In a world of truck diesels that have seen challenges with increasing maintenance and a drop in fuel economy with EGR, there will be some improvements in areas such as fuel economy and durability. This will happen in spite of the stringent new NOx standard.
Cummins’ big internal engine change for the ISX will be the XPI common-rail fuel-injection system. The dual overhead-cam unit-injector arrangement will go away. While the ingeniously simple injector used through 2009 could only inject the fuel in a single shot each time the engine fired, the XPI system has an electric valve that allows fuel to be injected in as many separate shots as needed. A small “pilot” shot of fuel will go in early in compression before normal combustion can happen, warming the highly compressed air by the time normal injection starts. This makes the fuel ignite more smoothly, killing NOx and making the engine quieter for the driver. It also helps minimize the work the DPF will need to do.
A second advantage of the XPI system is that it provides maximum fuel pressure for injection even at low RPM. Unit injectors perform at their best near the top of the engine’s operating range. This gave the engine’s designers opportunities to improve the engine’s performance and fuel economy and reduce internal stresses.
Cummins’ Steve Charlton, vice president, heavy duty engineering, says the combination of SCR and the XPI fuel system means 2010 Cummins heavy-duty diesels will have a much larger fuel economy “sweet spot.” This means less-skilled drivers who don’t shift at exactly the right time can still get good fuel economy.
With the XPI fuel system, the large camshaft that drove the injectors will be eliminated, along with some of the gears in the gear-train. The new single overhead-cam engine will be lighter, and the lighter gear-train also will help make it quieter. The 2010 ISX engines will carry horsepower ratings from 400-600 hp, developing from 1450-2050 lb.-ft. of torque.
Cummins also will introduce an 11.9-liter version of the ISX that will replace the ISM with an engine patterned after the ISX. This engine will have camshaft drive gears at the rear of the crankshaft near the flywheel, making it even quieter than the ISX. Its power ratings will range from 310-425 hp, and it will produce 1150-1650 lb.-ft. of torque.
According to the company, “Cummins is on track to exceed our field-test mileage target for both heavy-duty and mid-range products. Our testing includes a variety of test cycles with various load factors, light- to heavy-duty cycles and various terrains and climates. Results from our field-testing have exceeded our expectations. In addition, the Cummins 2010 engines have exceeded our customers’ expectations in terms of performance and fuel economy.”
Detroit Diesel and its parent company, Daimler AG, have developed the advanced DD15 engine, as well as 13- and 16-liter versions of the design. The Detroit Diesel Series 60 will disappear in favor of this engine.
These engines will have ACRS, the amplified common-rail fuel-injection system. Like all common-rail systems, it can produce maximum fuel pressures even at the lowest operating RPM, improving performance and reducing emissions. The design incorporates a hydraulic piston for each injector that increases the fuel pressure from about 13,000 psi to more than 30,000 psi. This way, the lines that carry fuel around the engine can run at a manageable pressure. This system can control the rate at which the fuel goes in during each firing cycle in a way that minimizes the need for fuel-consuming DPF regeneration and the amount of DEF consumed.
The DD15 and DD16 engines use a turbo-compounding turbine that captures some of the exhaust energy that is normally lost, driving the crankshaft through a gear-train. This is a more efficient way to provide the exhaust system back