Running a 500-hp diesel engine to generate cab and sleeper heat is like whittling with a chainsaw. It can be done, but not without a lot of excess noise and energy.
The most efficient truckers have long relied on auxiliary heaters to keep them warm during downtime, cutting emissions and saving money in the process. The fuel consumption of today’s heaters is a fraction of that used by heavy diesels.
“Our D1LC burns two-hundredths of a gallon per hour when set on low,” says Ray Lawrence, president of Espar of Michigan.
Part of this efficiency results from a greater use of electronics, which enable auxiliary heaters to operate on multiple output levels instead of merely switching on and off. Electronics also provide diagnostic capabilities that improve and expedite servicing.
Espar Heater Systems, based in Mississauga, Ontario, is one of three main heater brands. The other two are Proheat, based in Vancouver, British Columbia, and Webasto Thermosystems, based in Lapeer, Mich. All are reporting strong sales this year, despite the dismal condition of the new truck market.
“Green technology is a good seller nowadays,” says Scott Winton, Proheat’s sales and marketing manager. “Communities and neighborhoods are getting testier about the exhaust of vehicles left idling for long periods.”
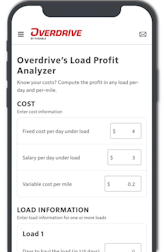
Webasto marketing director Sandra Jones agrees, saying the federal government is putting pressure on states to lower emissions, and idling trucks are popular targets of those efforts. Pollution issues aside, she says, the biggest selling point of heaters is their contribution to fuel savings.
That was the driving factor at Genmar Transportation in Little Falls, Minn., when its management recently ordered 50 Espar heaters from Interstate Detroit Diesel in Superior, Wis. Dave Waltman, Genmar’s shop foreman, says the initial results look good. “We’ve seen a big drop in the idling time of trucks with heaters,” he says. “And we picked up a half-mile per gallon on them.” Genmar runs 165 trucks. Waltman says auxiliary heaters will be installed in all new units as they’re brought into the fleet.
The following steps apply to an Espar D1LC Compact heater. The job is fairly straightforward and doesn’t require specialized tools. The heater kits come with all necessary mounting hardware, but some people will want plastic loom (gator skin) and extra nylon ties to further protect and secure the wiring harnesses. Shop time is six to eight hours.
The job
1. Unpack the kit. Arrange parts according to their function: fuel, electrical, air, etc. Grouping the hardware will help you visualize the tasks and ensure that all necessary bits are present.
2. Choose a mounting location. The D1LC should be mounted in an enclosed area. On trucks with sleepers, the units are typically bolted inside a cargo box under the bed. Ideally, a heater should be accessible from the ground so it can be easily installed and serviced. It should also be within 6 feet of its fuel supply. The space from which inlet air is drawn should be odor-free. This may mean finding a new home for your oil jugs, shop rags or laundry basket.
3. Bore holes. Use the kit’s templates and a center punch to mark the locations of required holes: ductwork, combustion air and wiring harness. Before drilling, put the heater in the location where you intend to mount it, just to make sure there is clearance between your intended drilling and any hidden electrical components or structural elements. Remove the heater and cut the holes with a drill and appropriately sized hole-saw bits.
4. Assemble heater, fuel pump. Attach the heater to its mounting bracket, exhaust and air-intake tubes, wiring harness and any covers that would be inaccessible after installation. Following the manufacturer’s instructions, connect the fuel pump and hoses. Don’t install either component yet.
5. Blow loose shavings away from holes as you drill.
5. Mount fuel pick-up pipe. Look for an unused mounting plate or threaded opening on top of your fuel tank. If one is not available, clean off an area and mark it for drilling, using the kit’s template. Smear grease on an appropriately sized drill bit and bore a guide hole. (Grease helps keep shavings from dropping into the tank.) Repeat the process with a hole saw, boring in at a slight angle. Stop drilling before the center is completely separated from the tank. Use a small screwdriver to pry up the loose side of this newly formed slug, then grab it with pliers and wiggle until the remaining slice of metal is detached.
Measure the distance from the hole to the bottom of the tank. Cut the pick-up pipe so it will reach within 2 inches of the tank’s bottom when installed. Mount the pipe with the hardware provided, but be careful to avoid dropping any parts into the fuel tank.
6. Mount heater and combustion tubes. Place the heater over the large hole in the floor of the mounting location, threading the intake and exhaust tubes through the opening. Once the unit is properly positioned, anchor it with the self-tapping screws provided in the kit. Insert a rubber grommet into the small hole used for wiring, then poke the harnesses from the heater through the opening.
Secure the flexible exhaust pipe to several solid supports under the sleeper, spacing the mounting clamps evenly. Make sure the pipe is kept away from any heat-sensitive materials, such as plastic or rubber. The end of the pipe should be tipped slightly downward and extend just beyond the sleeper’s rear exterior wall. Repeat the process with the intake tube, routing it away from the exhaust. Its open end should be turned downward to minimize the introduction of water and airborne debris. It, too, should be secured with several clamps.
7. Route the ductwork. You’ll likely need to install two air ducts: a heat outlet and an inlet where air is sucked in for heating. Ideally, both should be inside the cab or sleeper. Depending on your installation, you can, however, draw air from the cargo box housing the heater, as long as the space is clean and odorless. Heaters with a cargo box inlet require just one air duct, the outlet.
Espar provides ample amounts of flexible duct tubing with its heaters. You should trim this material to fit your installation. The tubing connects to a vent, or heat deflector, on the outlet side and a flange on the inlet side. Each must be mounted in an appropriately sized hole, which is best cut with a drill and hole-saw bit. Once you’ve routed the duct tubing – taking care to avoid sharp edges and potential crushing – secure it to a nearby wall with plastic or nylon ties (provided in the kit).
8. Use dielectric grease on all wire connections.
8. Connect fuel system. Mount the fuel pump on a support under the sleeper floor near the heater, but at least 3 inches from the exhaust tube. Route one hose to the bottom of the heater and the other to the pick-up tube on the fuel tank. Allow some slack in the pick-up tube’s hose to accommodate movement in the cab suspension. Make sure all hose connections are tightly butted together and sealed with clamps. Secure the hose with nylon ties. Apply dielectric grease to the fuel pump’s wire connections, then plug them into the main harness coming from the heater.
9. Mount thermostat. Connect the thermostat’s wiring harness to the heater’s main harness and route the loose end to the spot where the thermostat will be mounted. Secure the wiring at close intervals throughout its length, by strapping it with nylon ties or tucking it behind the sleeper’s upholstery.
Climate control panels often have enough room for a thermostat, but they might have underlying electrical components that would be damaged by drilling. Make sure your chosen area is free of obstacles, then remove the thermostat’s front cover and hold the box in place while marking the necessary holes with an awl or drill bit. Once the holes are made, you might need to loosen the mounting surface enough to reach behind and poke the thermostat’s wires through.
Attach the wires to the thermostat according to the manufacturer’s instructions. Fasten the box to the mounting surface and snap the front cover into place.
10. Connect to battery power. Route the power wiring harness from the heater’s main harness to the battery box. Use plenty of nylon ties or plastic loom to secure and protect the wiring from movement and chafing. Follow the manufacturer’s instructions for connecting the lead and ground wires to the battery set. A 25-amp fuse must be installed on the positive wire. Firmly crimp all connections and coat them with a battery terminal sealer.
11. Start the heater. Check all connections for tightness. Switch on the thermostat. The fuel pump should emit a quiet clicking sound, and the heater fan should spool up. Don’t be surprised if the unit fails to start, however. It might need to be cycled on and off a few times to pull up enough fuel. If it doesn’t fire up, switch off the control box after 30 or 40 seconds and let the unit go through its cool-down mode. Repeat after five minutes.
An auxiliary heater normally requires little maintenance, but it’s important to inspect the unit periodically and keep the mounting enclosure clean. It also suffers from lack of use. Running a heater once or twice a month through the warm season will prevent many problems during the first cold snap.