Hitting the road
Feedback on the latest heavy-duty power plants shows some positive signs as new technology tackles 2010 emissions standards.
By John Baxter
Selective catalytic reduction, used by all but one heavy-duty engine manufacturer to meet the 2010 emissions standards, opened up a whole new area of technology and maintenance.
SCR is a diesel designer’s dream. It kills oxides of nitrogen outside the engine, which allows for lower levels of exhaust gas recirculation, reducing engine stress. Because the additional NOx in the exhaust eats up soot, it means less regeneration of the soot collected in the diesel particulate filter.
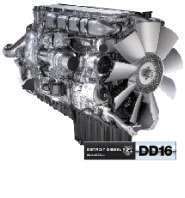
Still, an additional system on the truck adds cost, weight and the responsibility for the driver to refill a diesel exhaust fluid tank so the SCR system can work. These facts are constantly stressed by Navistar, which has taken the bold step of meeting the new standards with a combination of basic engine technology changes, including higher levels of EGR, and applying emissions credits the company has with the U.S. Environmental Protection Agency.
Following is a look at early reports on the new engines from manufacturers and their customers.
Detroit Diesel
Customers with Detroit Diesel’s 2010 engines are getting a net 3 percent improvement in fuel cost, says Amanda Phillips, director of component marketing and communications for Daimler Trucks North America. The new engines actually average a 5 percent improvement, but fleets typically spend 2 percent of what their fuel bill is on DEF. The net difference in cost could improve, she says, because “diesel fuel will go up, while DEF is not likely to.”
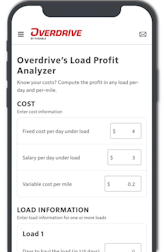
She says the 2010 Detroit Diesel engines idle more quietly than previous designs. At the same time, 2010 versions of the engine are more fuel efficient than earlier ones mainly because the DPF needs active regeneration only at about 3,000 miles, versus 300 for 2009-spec engines.
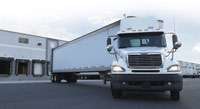
Mike Hasinec, vice president of maintenance systems and support for Penske Truck Leasing, says customers have seen miles per gallon improve 3 percent to 7 percent in Penske’s Freightliner Cascadias and medium-duty trucks running 2010 engines. “And there have been no maintenance issues. The percentage of DEF required has ranged from 1.5 to 3 percent of fuel usage. As the DEF does not cost too much, our customers have seen an improvement in their bottom line.”
Oil analysis reports have shown no major changes, Hasinec says.
“The drivers like the throttle response, and have seen less need for forced manual regenerations,” he says.
The 50,000-mile oil change interval that is standard with the DD15 and its sister engines because of finer filtration will remain, says Phillips. “We are seeing positive results and have no concern that we need to adopt earlier changes.”
Matt Hein, co-owner of Tri-Hi Transportation, running DD15 engines in Freightliner Cascadias, sees on-road DPF regenerations occurring at 2,500-3,000 miles versus 400 on 2007 equipment. He has figured fuel economy gains and subtracted DEF costs, and sees a net reduction in cost of $4,500 to $5,000 per truck per year.
Daniel Scherer, fleet maintenance manager at Meijer, Inc. says his Cascadias equipped with DD13s are delivering about 12 percent better fuel economy than the trucks they replaced.
Steve Duley, vice president of purchasing at Schneider National, says its Cascadias powered by the 2010 DD15 have accumulated 500,000 miles, with more than 200,000 on one, without maintenance issues. Fuel economy beats that of their trucks with earlier engine technologies.
Mike Jeffress, vice president of maintenance of Maverick Transportation, says his company has had no issues with drivers not being able to operate the truck normally because of frozen DEF, in spite of having a cold winter in Michigan. The fleet runs DD15s in Cascadias.
Cummins
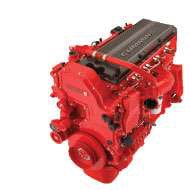
Cummins has given the ISX a new injection system. Both the familiar 15-liter ISX and the 11.9-liter version, available in August, sport the XPI (extreme pressure injection) common-rail injection system. Its ultra-high-pressure injection pump delivers a continuously regulated supply of the juice to a rail. This large pipe supplies each of the six injection nozzles with fuel at whatever pressure is needed, even below 1,100 rpm.
Cummins’ Steve Charlton, director of heavy-duty engineering, says of the new system: “You can dial in the pressure for the next combustion event, or create a five-piece event to help with emissions. That means you can use pilot injection to reduce noise. You can also increase the exhaust temperature to keep the SCR catalyst working or to help regenerate the DPF.” He says the system can create 35,000 psi or more.
Since XPI provides high-pressure fuel without unit injectors, the 2010 ISX engines no longer need the second camshaft that used to operate them. This helps the engine run quieter.
Customers say their drivers are happy with the overall performance, from startup to full bore down the highway, says Lou Wenzler, Cummins on-highway market communications director. Road testing a SmartPower 425-hp ISX that jumps from 1,450 lb.-ft. torque to 1,650 in the top two gears, one driver refused to believe the engine was only a 425, Wenzler says.
Charlton says the ISX engines also have a greatly enhanced EGR cooler that does a much better job of turbulating the exhaust and coolant as they pass through, enhancing its cooling capabilities, and thus reducing engine stress. And Charlton says the engine is tuned so the sweet spot is considerably larger.
Fleets commonly see a 0.3 mpg improvement, which is 5 percent better than last year’s engines, say Wenzler and Jim Kelly, senior vice president of heavy-duty marketing.
Ray Redmon, maintenance manager of Calex of Pittston, Pa., says his fleet runs Volvos with 2007-spec ISX engines rated at 450 hp. He’s looking forward to purchasing some 2010 ISX-powered trucks this year because he believes the lower levels of EGR should reduce the occasional oil filter plugging of his current engines. To virtually end such trouble, even on 2007 engines, Wenzler says Cummins Filtration has slightly altered the volumes of oil flowing through full flow and bypass sections of their filter.
Navistar
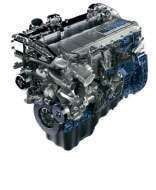
With its MaxxForce 11- and 13-liter engines, Navistar has seen fuel economy improve 1 percent to 3 percent in its 2010 models, says Tim Shick, director of business and product strategy at Navistar Engine Group. This is due to improvements in chassis integration with the International trucks, adoption of a clutched air compressor and, in the case of the ProStar, excellent aerodynamics.
Also, oil analysis reports on the new engines have been as good as those on previous engines, Shick says.
He notes that competitors’ engines are also using EGR – in their case, to supplement SCR. “The MaxxForce 11- and 13-liter engines are using advanced EGR as an alternative to SCR,” he says. “Our EGR rate will go from 25 to 30 percent for ’07-’09 engines to 30 to 35 percent for 2010.”
The MaxxForce 13 engine has ratings from 410-475 hp, the 11-liter from 330 to 390 hp. Because EGR rates increase with power level, he says, Navistar increased the size of its cooling package and EGR cooler to shed more exhaust heat this year. And, engines have been shifted back a bit in the chassis to improve underhood airflow.
“Exhaust leaves the engine at 500 to 800 deg. F., but the EGR cooler can take it down to 200 deg. F. or less,” he says.
Because EGR engines must run cooler than SCR engines to meet the NOx standard, Shick says, shedding more heat outside the engine does not stress internal parts. “For example, the oil cooler is no larger,” he says.
For 2010, Navistar moved the main charge air cooler to the front of the radiator, while retaining the inter-stage cooler between turbos, to improve charge-air cooling. Two other changes will improve reliability: Twin wastegated turbos will replace a variable geometry design; and exhaust flow will be controlled with an improved EGR valve that uses stepper motors to move it in both directions, rather than a spring for closing.
Combustion improvements, such as adding a proprietary double piston bowl and increasing fuel pressures from 25,000-26,000 psi to 31,000-32,000 psi, enabled Navistar to reach its goal of maintaining maintenance intervals and getting engine efficiency back to where it was in spite of ingesting more exhaust.
Navistar has said it will introduce the MaxxForce 15 by the end of this year. The engine will use the cylinder block and internal parts of the Caterpillar C15 with no modifications.
Mack
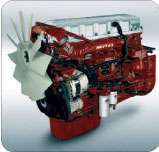
Dave McKenna, Mack powertrain products marketing manager, says the 2010 MP engines “have a reduced EGR flow rate, just about down to 2002 levels. This means the engine breathes a little better.” Better breathing saves fuel. The engine will also employ “multiple injection events,” he adds, which minimizes the use of DEF and reduces engine noise.
“The high injection pressures that were available previously allow us to produce less soot.” This is augmented, he adds, by the use of SCR aftertreatment so the NOx is reduced after the exhaust leaves both the engine and the DPF, allowing the system to “passively oxidize 99 percent of the soot in the DPF.”
For example, the infrequent use of the active regeneration system led one driver to tell Mack representatives he was happy with the truck because he had never seen a warning light or one indicating active regeneration from the DPF system.
The engine has a Borg-Warner magnetic fan drive, which also helps save fuel. Reduced EGR means less heat to carry away, although Mack has kept the same cooling package used in the previous design. The combination of an oversize radiator, less heat rejection, and a fan drive that modulates rather than coming on full blast as soon as it is needed, requires less power to drive the engine fan. Drivers will also no longer feel it when the fan engages or disengages.
McKenna claims typical fuel savings in the range of 5 percent “in the same drive cycle with the same horsepower,” with one vocational fleet seeing a change from 6.5 mpg to 7 mpg. These fuel savings are further improved for those who opt for the Econoboost system that discourages unnecessary downshifting by increasing the torque only when it’s needed for hill climbing.
Reliability of the new SCR components has been no surprise, McKenna says, “because of the way the basic system had been tried out previously in Europe.”
No changes in recommended maintenance intervals have occurred. McKenna says that with engine heat and pressure stresses down and the probability that lower EGR means less oil soot, Mack will continue to study data to see if a change is merited.
Volvo
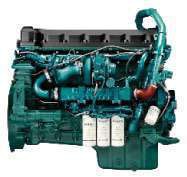
Watkins Shepard Trucking, which hauls commodities to both coasts from Montana, tested Volvo’s SCR prototype engine. The fleet has had no problems with SCR or DEF supply, says one of its drivers, Michael Halpin.
“The trucks we are driving are about as responsive as a truck could be, are getting great fuel mileage for a 16-liter engine, and the reliability, comfort, and functionality are about as good as it gets,” he says.
Bill Parry of Giant Eagle, a supermarket chain, says the company has been running five pre-production SCR trucks from Volvo since 2007. “Volvo initially shipped us DEF, but we soon found a local supplier and buy it in 250-gallon totes. We’ve found that SCR is no different from any other new technology. There seems to be a lot of smart engineering that has gone into the system. When you look at the exhaust pipe, it is amazingly clean, and the drivers think the response (of the engine) is better.”
Ed Saxman, Volvo’s drivetrain product manager, says, “Some of our competitors are introducing new, common-rail injection systems with 2010. Our injection system is pretty much as it was in ’07. We had a 35,000 psi system even then.
“We’ve seen about a 5 percent increase in fuel economy. It comes from reduced EGR combined with other things. The most important of those is our ‘no regen solution.’”
Volvos do without regeneration under virtually all on-road driving conditions, Saxman says, for several reasons.
Volvo’s 2007 engine redesign allowed it to tolerate higher levels of EGR. The injection system was improved, in part to allow increased injection pressures and generate less soot. It was also re-programmed to allow multiple injections for each power cycle, which helps control both soot and NOx.
Fortunately, NOx in the exhaust helps the passive regeneration of soot in the DPF. With SCR to get rid of that pollutant at the end of the process, it’s practical to allow the engine to produce some NOx and send it into the DPF. So, a three-part strategy resulted: One, an engine that produces minimal soot; two, control of the combustion to give the correct ratio between soot and NOx in the exhaust headed for the DPF; and, three, control of exhaust temperature to keep it hot enough to regenerate the DPF without adding fuel with the doser in the DPF.
Paccar
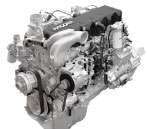
The MX engine, using SCR, is not on the road yet but has been extensively tested. The engine will displace 12.9 liters, use compacted graphite iron for both the block and cylinder head, and the maximum rating will be 485 hp with 1,650 lb.-ft. of torque, according to marketing materials. Mounting the gear train on the rear of the engine, and designing the mounting system so the oil pan “floats,” will minimize noise and vibration.
Paccar says an unusual “fractured cap” design for the bearing caps allows greater strength in the engine’s bottom end and longer torque and power curves.
The engine will have the camshaft located high in the block and driving unit injector pumps. These electronically controlled pumps will provide 36,000 psi injection pressures through high-pressure piping to electronically controlled injection valves located in the head. Improvements in such piping, plus the engine computer’s ability to coordinate the valves on the pumps with the opening and closing of the injectors electronically, allows a high-performance injection system of unusually simple design. n