Belts and hoses that fail can sideline your truck when you least expect it. Carrying spares can save time and money when one of these critical parts fails on the road. Even better, take the time to periodically inspect them for signs of wear and replace any weak links before they become a problem.
Cooling system leaks are among the most frequent maintenance problems. Coolant hoses can develop leaks from abrasion, punctures, loose clamps and an improper fit between the fitting and the hose. A hose should fit snugly over the mating tube. During inspection, squeeze the hose along its length to detect cracking, softness and wear spots. Hoses that are cracked, swollen or dried instead of resilient should be replaced, advises the Technology and Maintenance Council.
Most hoses are manufactured with woven reinforcement in the walls for strength and rigidity. They are sized by their inside diameter. Standard-quality coolant hose is made of black rubber EPDM hose. Silicone hose is more expensive but is tougher and lasts longer in high-heat applications, providing higher temperature tolerances than EPDM hose, and it does not dry out or crack as quickly.
When replacing hoses, lubricate the ends and fittings with water or a solution of water and mild liquid soap. To avoid an adverse chemical reaction and deterioration of the hose, do not lubricate with ethylene glycol, propylene glycol or any petroleum-based products. Silicone-based oils should not be used with EPDM hose, says TMC.
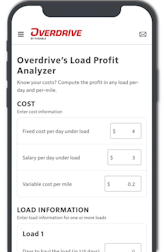
Gates Rubber Co., a major supplier of belts, clamps and hoses, recommends checking coolant hoses when the system is flushed or whenever servicing of the radiator or water pump is required. Hoses showing obvious signs of wear and those more than 4 years old should be replaced, Gates advises. Since EPDM hoses tend to bond to metals, removal of coolant hoses from fittings must be done carefully. Avoid forcing or prying a hose to prevent damaging the fitting. Gates recommends slitting the hose lengthwise at the fitting to loosen it for removal.
During four years of testing on fleet vehicles, Gates engineers traced the cause of most coolant hose failure to an electrochemical attack on the rubber compound in the hose. Known as electrochemical degradation, the condition occurs because the hose, coolant, and engine and radiator fittings form a galvanic cell, like a battery. The chemical reaction causes the formation of microcracks in the hose tube, allowing the coolant to attack and weaken the hose reinforcement, Gates reports.
To check a coolant hose for the effects of ECD, the company recommends that you squeeze the hose near the clamps or connectors. If the hose feels soft or mushy, chances are good that the hose has been attacked by ECD and should be replaced. There should be no difference in the feel between the middle and ends of the hose. Upper radiator hoses and heater hoses tend to fail first because that is where the temperatures are the hottest.
According to Gates, it is not uncommon to find hose failures due to electrochemical damage in vehicles driven fewer than 25,000 miles. The timely replacement of a coolant hose can prevent a roadside breakdown, as well as damage to the engine. When replacing a hose, Gates recommends also replacing the hose clamps. While clamps are typically made with stainless steel bands that resist corrosion and damage, they are secured by carbon steel screws, which can fatigue and lose strength.
Gates manufactures Green Stripe hose, which provides a longer service life than a standard EPDM hose and is more durable than silicone hose, the company says. The product also resists the permeation of water molecules through the hose wall better, enabling the cooling system to maintain its coolant concentration longer.
Pay Attention to Clamps
Hose clamps represent another weak link in the cooling system. Clamps are designed to provide either a constant tension or a constant diameter. Constant-tension clamps include worm-drive, post-type screw and wire-type screw designs. Spring-type clamps provide a constant diameter and include spring band, spring-loaded T-bolt and convoluted spring-band designs. Polymeric bands, made of heat-sensitive plastic material that can contract and expand with temperature changes, are also used to secure hoses to fittings.
According to Gates, heavy-duty cooling system clamps should be able to provide compression load sufficient enough to be transmitted from the surface of the hose through the wall to create a sealing load at the hose/stem interface throughout the operating temperature range. Leaks commonly develop when the coolant is cold, requiring tightening of the clamp. Ideally, a clamp should provide a higher compression load at low temperatures so that cold leaks are avoided.
Gates engineers evaluated a variety of types of metal and polymeric clamps and determined that polymeric bands can outperform metal clamps in maintaining cooling system integrity throughout the operating temperature range. The plastic bands are also better than metal clamps in distribution of compression load and protection against overtightening.
Gates offers its PowerGrip SB clamp made of a heat-sensitive thermoplastic material that is installed with a standard heat gun and never needs tightening, the company says. Used with both silicone and black rubber hoses, the polymeric clamp helps eliminate cold leaks by adjusting with temperature changes to maintain the proper sealing force on the hose during the engine’s operating cycles.
For a clamp to perform at its optimal level, it should be installed at the manufacturer’s recommended installation torque, advises ABA of America, a manufacturer of clamps. Insufficient clamping force allows fluid seepage between the joint and the hose I.D., increasing the risk of blow-off. ABA’s product line includes heavy-duty worm-drive clamps with nonperforated, smooth bands and rounded edges to minimize hose damage.
Norma Products, manufacturer of NormaClamp constant-tension band clamps, recently introduced a high-torque hose clamp that provides 30 percent more clamping force and withstands higher installation force than conventional worm-drive clamps. Available in 25 millimeter to 152 millimeter, the clamp is 12 millimeters wide and has a smooth inner surface to minimize friction with the hose during installation.
Clampco offers torque-bolt band clamps with smooth surfaces and uniform radial clamping force. The T-bolt clamp was designed to resist vibration, corrosion, temperature extremes, high pressure and frequent release and tightening cycles.
Belts Lose Flexibility
V-belts and multi-ribbed belts are used to drive accessories by the wedging action of the belt in pulley grooves. Belts have high-tensile cords embedded in a synthetic rubber core for strength. The core consists of a lower supporting cushion of stiff rubber to form the belt’s compression zone. An upper or tension zone incorporates a softer material to better handle the continuous flexing of the belt as it turns around the pulleys.
Belts lose flexibility over time and become brittle, cracking along the ribs and eventually breaking apart. Excessive heat caused by improper installation or pulley incompatibility is a leading cause of belt failure, according to Gates Rubber Company, designer of the first V-belt and the world’s largest manufacturer of V-belts, timing belts and V-ribbed belts.
Belts should be checked regularly for fraying, splitting and cracking. Belt tension should also be checked with a tension gauge. Loose belts tend to slip in the pulleys, creating heat that can shorten a belt’s service life and cause premature bearing failure. Belts should be tensioned according to the manufacturer’s recommendations. A new belt should be tensioned to the highest value, then run in for 10 minutes and retensioned at the midpoint of the tension range, says Gates.
Some Caterpillar engines are equipped with dual alternator belts. Always check both belts for correct tension, the manufacturer advises. Engines equipped with serpentine or poly-V belts have automatic belt tensioners and do not require a belt tension inspection, but they should be checked for uneven or eroded under-cord ribs, which cause the belt to lose its gripping power.
To inspect a belt, twist it so that you can see the sidewalls and bottom to check for glazing (shiny sidewalls) caused by friction created when a loose belt slips in the pulleys or by oil or grease in the pulleys. The belt should also be checked for ply separation. Using belt dressing, which can cause a belt to fall apart in layers, is not recommended.
During installation, belts should not be forced onto the pulleys because the tensile cords can be damaged, shortening service life. Instead, the drive take-up should be released completely, then tightened. Two belts in a matched set should both be changed, even if only one appears to be worn. This practice assures that the belts remain matched throughout their service life, observes Gates.
Belt/pulley incompatibility can result from a mismatch in pulley size and pulley spacing. A size mismatch can occur when an engine component, such as an alternator, is replaced with a new one that comes with a different sized pulley. A pulley-spacing mismatch can occur even in a new engine when an optional component, such as a heavy-duty alternator with slightly different spacing than the original design, is installed.
According to Gates, to the untrained eye, two 3/8-inch belts can be installed side by side on seemingly compatible pulleys, but not until a belt fails prematurely or flips out of the drive, is the incompatibility noticed. When replacing a belt or installing a new component, check for pulley compatibility, says the company. Pulleys should be inspected for excessive play or wobble, signs of a failed bearing.
Worn sheaves can also cause premature belt failure. The grooves should be checked with a sheave gauge to determine the extent of wear. Oil or grease should be cleaned out to avoid belt slippage and early deterioration of the belt. Any rust, burrs or foreign objects in the groove should also be removed to prevent premature belt wear. Belts should also be checked for cuts and small, irregular cracks, signs that the belt should be replaced.
Gates offers the Green Stripe PowerBand belt, a joined V-belt which replaces two single belts. It provides more stability and shock load absorption than two single belts can provide, the company says. To help signal incompatibility, the belt will not seat properly in pulleys of different sizes or in two-groove pulleys with different spacing.
Goodyear Engineered Products manufactures hoses and belts in the Hi-Miler line. The belts feature molded-cog construction to improve flexibility and maintain tensile cord support. The design of the cogs provides air circulation to prevent heat buildup in the cushion section, says Goodyear.
Hi-Miler heater hose and straight radiator hose costs about 60 percent less than silicone hose and can go from engine overhaul to engine overhaul without replacement, says Goodyear. The tube and cover are made with a heat-resistant synthetic rubber and reinforced for excellent burst strength, the company notes.
Flexfab Inc. manufactures DuraGuard silicone radiator and heater hoses for heavy-duty trucks. Thermopol Inc. offers a silicone hose with a bonded metallic heat deflector for installations that run hose close to high-temperature surfaces. The custom-formed heat shields can be made to cover specific hose sections or the entire outer surface, shielding the hose from temperatures up to 1,300 degrees F, the company says.