When ride and handling start to suffer on your truck, chances are good that the problem can be traced to the suspension. Without routine maintenance, the long, hard miles take their toll on suspension parts. Nuts loosen and back off, spring components develop cracks and break, and friction causes excessive wear on unlubricated moving parts.
Suspension problems are the second most common defects cited by roadside inspectors after brakes. Signs of misaligned, shifted, cracked or missing springs; loose or missing shackles and bolts; spring hangers unsecured at the frame; and cracked or loose U-bolts can put your truck out of service in an inspection.
First rule of suspension maintenance: Keep the nuts tight. Clamps, brackets and U-bolts holding the suspension together stretch over time, allowing the nuts to loosen. On new equipment, fasteners should be retightened within the first 1,000 miles. They should be checked again at 10,000- to 15,000-mile intervals and retorqued to the manufacturer’s specifications every 100,000 miles.
Don’t rely on a roadside inspector’s report to learn about the condition of your truck’s suspension. It’s better to get underneath yourself on a regular basis to inspect the springs, shackles, U-bolts, shock absorbers, torque rods, air bags and other parts that wear and fail over time. While you’re at it, take a grease gun and torque wrench with you. A little effort can save you lots of trouble.
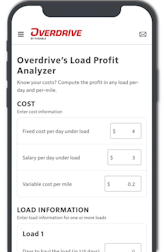
Suspension manufacturers have reduced the amount of maintenance required on their products over the years, but the basic types remain the same: multi-leaf or parabolic taper leaf springs on the front and four-spring, walking beam, multi-spring and air-ride on the rears. Air suspension, the most popular, requires little maintenance except when air lines and air bags develop leaks through punctures or chafing against other parts.
Importance of Lube Job
Keep metal suspension components well lubed to prolong their life and help ensure that your suspension operates at peak performance. Hit every zerk fitting with a grease gun as well as other parts that wear against each other according to the manufacturer’s guidelines. Bronze bushings should be lubricated, but rubber bushings should not, since lubricants can damage them. Keep lubricants away from rubber blocks and other rubber suspension components, too.
Pins and bushings that secure front springs are especially critical and should be lubricated roughly every 15,000 miles for over-the-road equipment. Proper lubrication minimizes friction that can wear out bushings prematurely and damage springs. When replacing bushings, they must be torqued to the manufacturer’s specifications to avoid crushing them by over-torquing. Under-torquing is no good, either. That allows the bushings to move and wear faster than normal.
Hendrickson Truck Suspension Systems offers extended-wear Laser Lube front spring eye bushings. They are designed to solve the three major problems with front bushings: lack of lubrication, contamination by dirt and moisture, and distortion of the bushing’s shape. The bushings are impregnated with graphite for continuous lubrication. Urethane seals at each end prevent contaminants from entering, and a laser-welded seam provides improved dimensional stability.
Horton’s Roller Bushings are designed to provide a smoother ride and improved handling for heavy-duty front suspensions. Dozens of tiny needle bearings create unique grease grooves for maximum lubrication and minimum maintenance, the company says. A ribbed surface makes installing the bushing easier. Horton sells a heavy-duty pin-and-bushing tool for removing and installing Roller Bushings. It also works with standard pins and bushings.
Bronze bushings, used mainly for extra heavy-duty service, have a single zerk fitting. Ball indented bushings in the spring eyes of the Hendrickson RT2 Series have lubrication channels. To properly lube them, the rear of the vehicle should be lifted to relieve the load on the bushings; then, grease should be forced into the channels until it comes out the other end. Severe service applications require more frequent lubrication.
On walking beam suspensions with spring packs, a pair of zerk fittings on the hangers at the spring pins facilitate the job of lubing. The hangers should be closely checked for cracks and excessive rust, signs that they should be replaced. As a general rule, when working on suspensions, do not reuse U-bolts, bolts and huckbolts after removing them. New fasteners – Grade 8 nuts and Grade C U-bolts – should be used.
Hendrickson advises that springs with one or more leaves broken below the No. 2 leaf should be replaced with a new spring assembly of the same part number. The number is stamped on the spring clips. Springs on both sides should be replaced at the same time for even spring deflection.
Right Time to Rebush
A walking beam suspension is designed to let the axles float out sideways as many as three inches during tight turns. Worn center bushings permit even more lateral movement, which causes tires to rub on the suspension frame hangers. Signs of scrubbing appearing on the inside sidewalls of tires mean the center bushings should be replaced to avoid severe tire damage, Hendrickson says.
Select the right bushing material for your application. For standard-duty service, rubber center bushings are recommended and require no maintenance. For more severe service, if the bushings are wearing prematurely, Hendrickson recommends high-confinement rubber bushings, bronze or fully bonded rubber bushings for extended service life.
Rubber load cushions are used instead of leaf springs on the Hendrickson RS Series suspensions. The cushions should be checked for damage and swelling at least once a year. Saddles and frame hangers can cut into the rubber and reduce the effectiveness of the cushions. Replacement cushions are available in a range of hardness ratings for different applications.
Hendrickson’s vocational suspensions use transverse rods to provide lateral support. They keep the axle centered laterally and control axle walkout while cornering. Torque rods keep the axle housing from twisting during braking and accelerating to help maintain optimum driveline angles and absorb leaning and cornering forces. The torque rods should be checked for looseness and badly worn bushings.
Air-ride suspensions use inflatable air bags or air springs – typically two per axle – to absorb road shock. The bag is a rubber/fabric bellows with a column of compressed air, which provides force and supports the load.
Air bags come in variety of sizes and shapes, including single, double and triple convoluted types and reversible sleeve models for different types of applications. Mounting brackets secure the bags to the frame rails ahead of the axles. Each bag supports a trailing arm, which is attached to the frame and allows the axle to move.
The bags are prone to damage and should be inspected regularly. Listen for the characteristic hissing sound to detect air leaking from tears, holes and abrasions, advises Firestone Industrial Products Company, whose Airide air springs are on more than half the vehicles equipped with air suspension. Misalignment can damage a bag as can overextension of the air spring. That can result in the bag pulling away from the metal top plate or from the lower mount.
The style of air spring most commonly found on heavy-duty trucks and trailers is the Firestone 1T or reversible sleeve type, a large diameter air spring that rolls up and down on a piston mounted to the bottom. Identification of the proper replacement assembly requires determining the bellows type, the bead plate and piston type used. You also need to determine if the spring includes an internal bumper, Firestone says.
The 1T style spring is available as a complete assembly, including the piston, or as a service assembly, with bellows and bead plate only. Before buying a service assembly, Firestone advises close inspection of the piston to be reused. A slight imperfection or buildup of corrosion or dirt on the piston can cause a new bellows to wear out prematurely.
Raydan Manufacturing sells Air Link, a retrofit kit to convert spring pack and rubber block suspensions from Hendrickson, Neway Anchorlock International, Ridewell Corp. and other manufacturers into an air-ride suspension. Retrofitting a Hendrickson spring pack, rubber block or solid mount walking beam suspension takes about 20 hours, Raydan says. It entails removing the original suspension, except for the walking beams, and bolting the Air Link to the frame in its place. The retrofit adds two air bags above each walking beam.
According to Raydan, Air Link offers the highest roll stability of any air-ride suspension, rivaling that of spring and rubber block suspensions, while providing a smoother ride.
Shocks Wear Out
Shock absorbers play an important role in the suspension system by dissipating axle rebounds and adding stability to the vehicle. Shocks are designed with a specific service life and should be replaced when they don’t work anymore. When a shock absorber is doing its job, the bottom section feels warmer than the upper section. When in doubt about the condition of the shock absorber, check the resistance by disconnecting it at the bottom bracket and working it with your hand. Oil leaks, excessive rust and deep dents are visible signs that shocks should be replaced.
Hendrickson developed its Hi-Torque shock absorber as part of the integrated Efficient Driveline Geometry (EDGE) system, designed to reduce suspension-related torsional driveline vibration and frame rise during hard braking and accelerating and while traveling over rough road surfaces. An internal rebound spring in the standard 1 3/4-inch bore shock absorber compresses on the extension stroke to resist the rapid extension related to axle windup. Since the compression stroke is not affected, ride is not adversely affected.
The EDGE system includes a zero-delay height control valve that operates within a small deadband – the range of vertical suspension movement in which the system does not react. The system provides faster response to road inputs and maintains the proper height under a wider range of operating conditions than long-delay valves, Hendrickson reports.
The company offers a retrofit height control valve kit that provides twice the airflow of comparably sized valves. That results in quicker response and faster exhaust of air. As a general rule, Hendrickson recommends against adjusting ride height to improve comfort. Changing the height from the factory setting risks inducing a driveline vibration, which can damage pinion bearings and U-joints.
The height control setting should be checked and adjusted after any repair is made to suspension components, Hendrickson says, observing that excessive driveline vibration is a sign that the ride height is incorrect. A high setting forces shock absorbers to travel to their full extension. A low setting results in an uncomfortable ride since the suspension can bump against the axle stop.