Today’s heavy-duty oil filters have come a long way since the early filters that used wood chips, cornhusks and cotton liners as filtration media. While those materials served the same purpose as the media in modern filters – to trap and hold contaminants picked up by the oil – they were too restrictive to allow all of the oil to flow through. For that reason, only a small portion of the oil could be cleaned at any one time. The rest bypassed the filter and was returned to the sump, hence the name bypass filter. Oil was routinely changed after a few thousand miles.
Those filters served the trucking industry until the early 1950s, when full-flow filters using resin-treated pleated paper media were introduced. Since then filter manufacturers have strived to improve the capacity (ability to hold contaminants) and efficiency (ability to remove smaller particles) while minimizing filter restriction. Bypass filters are used today as secondary filters, pulling in only about 10 percent of the oil, then passing it through to the sump. Full-flow filters are primary filters through which all the oil flows.
Full-flow filters typically trap particles in the 25-to-40 micron range. Bypass filters use finer media and remove smaller particles missed by full-flow filters. They keep oil cleaner longer, extending its service life and enabling longer drain intervals. Dual-flow filters that combine full-flow and bypass filtration are also available. Many lubrication experts feel that both primary and bypass filters are needed to prolong engine life.
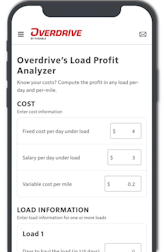
Filters should be changed at every oil drain to avoid becoming plugged or clogged so badly that they become ineffective. Full-flow filters have a bypass valve serving as a pressure-relief, opening when the filter becomes plugged. In that situation, unfiltered oil and debris flow through the engine, resulting in premature wear of engine parts.
Advances in filtration media have enabled the development of extended-service filters. Filter media ranges from inexpensive cellulose (paper) to expensive fiberglass, polyester and other synthetics. Synthetic materials enable filter manufacturers to control the precise size and shape of fibers in the filter to catch smaller particles, improving its efficiency and capacity. Some operators like to change oil filters at the engine manufacturer’s recommendation for normal oil service, even for engines operating on an extended drain schedule.
Baldwin BD103 oil filter features cellulose/synthetic-blend media and a dual-flow design that combines full-flow and bypass elements.
Paper or Synthetic Media?
Oil filters trap particles of soot, debris, wear metals and fuel in the pores of the media as the oil flows through the filter. As the pores fill up, the efficiency of the filter is degraded. A decrease in oil pressure, either suddenly or over time, generally indicates a plugged filter.
The most common type is the spin-on filter. It contains filter media inside a steel canister, which is discarded or recycled after use.
High-quality paper filters meet the requirements of engines operating under normal conditions. Synthetic-media filters are better if you operate in extended heavy-load conditions, frequent stop-and-go service, high or low temperature extremes, or dusty environments. Those extreme conditions produce more combustion by-products that have to be cleaned from the oil, demanding the higher-performance synthetic-media filters to avoid unacceptably short oil-service intervals. Synthetic-media filters are also recommended for extended oil service because of their higher capacity.
The drawback to synthetic glass-media filters is that the media cannot be bent too sharply in forming the filter pleats, or the glass fibers will be broken, according to Baldwin Filters. That limits the surface area that can be built into the filter. Also, glass media typically requires a wire screen lining to keep the glass fibers together, adding cost to the filter.
Baldwin recently introduced a line of severe-service filters which incorporates a blend of cellulose and synthetic material that offers high efficiency and the capacity to extend oil-change intervals. The filter, which Baldwin says outperforms synthetic-media filters, costs more than cellulose filters but less than synthetic-media filters. For trucks operating under extreme conditions, severe-service filters provide extra protection against harmful oil contaminants.
The company also introduced its Vortex line of dual-flow oil filters for Cummins ISM, IXS and Series 600 engines as replacements for the Fleetguard Venturi filter line. The bypass oil flow rate is higher than standard spin-on dual-flow filters, allowing 15 percent of the oil to flow through the bypass media vs. the typical 10 percent. The filter sends all of the filtered oil directly to the engine, not the sump. According to Baldwin, the filters improve engine protection during extended oil-drain intervals, high idling and harsh operating conditions.
The Donaldson Company has developed an innovative new oil filter for Cummins Signature and ISM engines that delivers higher capacity and efficiency than standard filters. Called the P559000, the filter uses Donaldson’s multi-density Synteq filter media, designed to hold more contaminants. The new design has expanded the media surface area in the filter element for more efficient filtration, the company says. The filter cartridge features a wide-mouth outflow for unobstructed oil flow through the filter. The P559000, which can replace Fleetguard Venturi-style filters, enables operators to extend oil-change intervals.
Donaldson also manufactures the Endurance line of long-life, heavy-duty filters, guaranteed to last for 25,000 miles under normal highway conditions when using premium oil (CG-4 specs), Donaldson Endurance air filters and a regular program of oil analysis. With Donaldson authorization, the mileage interval may be extended to 50,000 miles. If a product defect results in engine or equipment failure, Donaldson will cover the cost of repairs.
Mobil Delvac Extended Life filters from Champion Laboratories Inc., enable over-the-road trucks to run up to 60,000 miles when used with Mobil Delvac 1 synthetic oil, the company says. Synthetic media in the filter are designed to provide maximum filtration protection during extended drain intervals. Champion also manufactures Luber-Finer heavy-duty diesel filters.
Fleetguard’s new Centriguard centrifugal oil filtration line features ConeStaC technology – which forces oil through gaps between plastic cone stacks, reducing the distance particles must travel before they are trapped – for improved efficiency. Contaminants of less than 1 to 5 microns are removed by the filter. The filter is ideal both for severe service and for extending oil-change intervals in normal service, the company says.
Cleanable, Reusable Filters
The Nelson Division of Fleetguard/Nelson manufactures the EcoClean line of cleanable and reusable oil filters. Clean-Pro synthetic media improve filtration efficiency and extend oil life up to 200 percent more than conventional full-flow filters, Nelson says. To clean the filter, an air hose is attached to the filter drain valve, and the dirty oil and contaminants are blown out into a container. Once clean, the filter can be reused, offering a service life of up to 250,000 miles through repeated cleanings, according to the company.
Vortex International offers Vortex Cleanable Filters designed to replace standard oil filters in heavy-duty engines. The full-flow filter features a cleanable stainless steel screen element and active filtration, which uses centrifugal force to clean the oil. Angled holes in the filter head create a whirling action, throwing the oil and particulates into the screen. Particles are trapped and forced into a sediment holding area in the bottom of the canister, which is cleaned periodically.
The Vortex filter has been used successfully by Brinks International. The company drains and cleans the filter every 8,000 miles or 300 hours. Brinks trucks have gone more than 125,000 miles on the Vortex filter without an oil change using this process, and oil analysis shows the oil was still well within the allowable base limits, Brinks reports.
T.F. Hudgins Inc. manufactures the Spinner II CS filter, which also uses centrifugal force to clean the oil. The permanent, cleanable filtration system is a direct replacement for spin-on, full-flow filters. The filter incorporates a cleanable stainless steel screen and a fast-spinning (7,500 rpm) centrifuge, which is powered by engine oil pressure. Dirty oil enters the centrifuge bowl, and contaminants are slung onto the inside wall of the bowl, where they accumulate into a dense cake for periodic removal. According to Hudgins, the Spinner system removes smaller particles than any other filter, down to 0.10 micron, and holds up to five times more debris.
The Amsoil Bypass Filtration System removes particles of less than 1 micron in diameter, using a filter element of stacked discs of wood and cotton fiber. Water is also removed, reducing the risk of oil degradation, engine rust and oil contamination. Because the filter removes such small debris from the oil stream, it significantly increases the time oil can be safely left in the engine, Amsoil says.
The Premo Plus Third Generation Filtration System from Advanced Maintenance Technologies removes both solid and liquid contaminants through a patented two-stage evaporation and filtration process. A heating chamber heats oil to 195 degrees to evaporate liquid contaminants and fuel, which pass out through a vent. The Premo Plus is equipped with a sampling valve to draw oil samples for analysis.
The Puradyn bypass oil filtration system does not replace the conventional filtration system; instead it enhances the full-flow filter and works in conjunction with it.
Cleaning vs. Changing Oil
Puradyn Filter Technologies recently introduced its latest bypass oil filtration system with cotton-fiber media that can significantly extend oil-change intervals. It cleans oil contaminants down to 0.25 micron while replacing oil additives through its patented time-release additive package. The filtered oil enters a heated evaporation chamber, where fuel, acid and water are evaporated and vented. An easy-change design allows the filter element to be replaced in a matter of seconds.
Test vehicles using Puradyn filter technology averaged more than 160,000 miles without needing an oil change, the company reports. The element should be changed at the engine manufacturer’s specified drain interval or as oil analysis indicates. The oil does not have to be changed until oil analysis confirms that it is no longer suitable for use.
Vulcan Chemicals, Wichita, Kan., reports that it saved $1,700 per truck last year using the Puradyn bypass oil filtration system in Cummins, Mack and Caterpillar engines in trucks running an average of 120,000 miles a year. Trucks in the fleet have gone up to 616,000 miles without an oil change “by cleaning our oil instead of changing it.”
According to Puradyn, standard full-flow filtration does not meet the trucking industry’s needs for extended oil-drain intervals. “It is clearly understood that to extend equipment life and time between intervals, a high-quality oil and an efficient ultra-fine filtration system are needed,” the company says.
Filtration Solutions offers the FS-2500, a remotely mounted bypass oil filter designed to trap particles as small as 2.78 microns, thanks to a patented, replaceable filter element called a “conical helix.” The filter allows extended oil-change intervals averaging 65,000 miles with petroleum-based oils and 170,000 miles with synthetic oils, the company reports. The 11-by-5-inch unit is mounted on the truck frame or in the engine compartment. James Rawlings, an owner-operator from Dallas, relates that he has saved nearly $13,000 in oil changes since he first put an FS-2500 on a truck in 1995.
Magnetism is the principle used to clean oil in a device called Klear Force from XP3 Corp. It focuses a strong directional magnetic field through the body of an oil filter, turning the interior walls of the filter into a high-strength magnet. Metal particles are attracted and held, reducing excessive wear caused by the particles flowing through the engine oil, the company explains.