“You can’t have too much horsepower” is a universal truth in the trucking business. Truckers like big, powerful engines. But an important link between all that engine power and the drive wheels is the drivetrain, including clutch, transmission and other components. Without proper maintenance these vital components can fail, and then those 600 horses you’ve got under the hood won’t mean a thing.
Drivetrain basics
At the front of the drivetrain is the clutch. It’s designed to slip so you can get a smooth start. The clutch pressure plate uses heavy springs, and is bolted to the engine flywheel and turns along with it. The driven discs are made of metal, with ceramic or organic facings designed, like brake linings, to slip smoothly and handle high heat without undue wear. When the driver releases the clutch pedal, the pressure plate (and with twin-disc clutches an additional metal plate between the two driven discs) traps the clutch-driven discs between the flywheel and pressure plate. With a skilled driver, the springs soon cause the driven disc to turn along with the flywheel with no slip.
The transmission sits just behind the clutch and allows the driver to change the ratio between engine and driveshaft/wheel rpm. This lets the engine develop sufficient power regardless of vehicle speed. Modern American heavy truck transmissions all use a twin-countershaft design, which ensures great strength and compact construction. The gears are always meshed with their adjacent gears – that’s why the “constant mesh” moniker is attached to truck transmissions. This protects the gear from shifting errors.
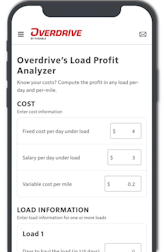
When the driver shifts, he is just sliding one of the shift collars splined to the mainshaft to engage a mainshaft gear. Constant-mesh gearboxes take less effort to shift than synchronized transmissions because the diesel does the work instead of the
driver’s arm.
Most truck transmissions are designed so that in top gear the drive passes through two sets of transmission gears and the output shaft turns faster than the input shaft and engine; this is called running in “overdrive.” A few transmissions use direct drive in top gear: Shift collars link the input, main and output shafts together, and the drive passes straight through using no gears. Overdrive top gear ratios are used because, in this way, the driveshafts turn faster, but the torque carried by the drivetrain is a lot lower. Trucks with conservative engine torque ratings sometimes run axles with ratios around 3.00:1 and direct-drive transmissions to save a bit of fuel while maintaining correct cruise rpm. Over-the-road trucks using overdrive typically run rear axle ratios of 3.55:1-3.90:1.
All four rear wheels receive driving power through the use of tandem drive axles. One driveshaft carries power from the transmission output shaft to the forward differential; a second carries power to the rear differential. Both rear axles reduce the rpm of the wheels as compared with the driveshaft with a ratio from 3.00:1 to as high as 4.50:1, depending upon the application. They also allow one wheel to turn faster than the other when the truck turns, through the differential. An inter-axle differential on the front drive axle allows the two axles to rotate at different speeds due to slightly different tire diameters and the slightly different paths taken by the axles during turns.
Powertrain components must be matched. Don’t order a new truck and try to save money by under-spec’ing a component – for example, ordering a 1,450-pounds-feet transmission with an engine that produces 1,550 pounds-feet. Also, be careful when uprating engine power curves to make sure the components, including their coolers, are up to handling the torque and horsepower.
How to reduce drivetrain wear
Drivers can save clutch and drivetrain wear by starting in the right gear, ideally first gear in a 9-, 13- or 18-speed, and second in a 10-speed, when on a level road carrying a full load. Starting uphill with a load demands at least this gear – and maybe low – on 9s, 13s and 18s, and first on a 10-speed. Using a good low gear tremendously reduces clutch slippage and drivetrain stress because the engine and clutch need to generate a lot less torque and the clutch locks up much sooner.
Transmission gears take a lube that’s different from rear axle lube. Because there are a great number of gear meshes in a transmission, the lube runs hot.
Transmission and axle lubes – knowing the difference
Transmission and axle lubes are very different because they serve two very different components. Transmissions run quite hot because there are four gear meshes – four sets of gears working together to transmit power – almost all the time, and at least three additional meshes created as at least six additional gears roll around together. Axles run much cooler than transmissions because there is normally only one major set of gears in mesh, but they use hypoid gearing, which means the teeth actually slide over one another. Transmission gear teeth tend to roll over one another rather than sliding.
Transmissions use single-weight lubes, while axles can use multi-weights. What’s the difference? Oils occur in various weights or thickness (viscosity). They always get a lot thicker when it’s cold, and thin out when hot. To create oils that flow when cold, yet don’t thin out too much to protect parts when hot, chemists developed VI (viscosity index) improvers. Refiners then combine thin base oils like SAE 10 or 15 with VI improvers to create a multi-viscosity oil like SAE 15W-40. That’s engine oil that’s as thin as a natural or “straight” 15-weight when cold, and as thick as a 40-weight at hot engine operating temperatures.
Transmission lube is a single-weight, high-viscosity lube oil like SAE 50 with an additive package similar to what’s used in engine oil, says Charlie Allen, director of sales and marketing with ZF-Meritor. Single-weight lubes are used because the VI improvers needed to create multi-weight lubes would break down in the high heat, leaving the lube too thin to protect the transmission.
On the other hand, the hypoid gears used in axles require lubes with what are called “EP” or “extreme pressure” additives to separate the sliding gear teeth. Bruce McGlone, senior materials engineer with ArvinMeritor, says the EP additives are made of sulfur and phosphorous. The gears would be subject to extreme wear and even seizing (welding together) without them. Dan Pesce, lubricant liaison between Eaton’s engineering and marketing activities and the lube manufacturers, says the sulfur those EP axle lube additives contain would corrode the copper oil coolers used with transmissions. Because axles don’t create too much heat for viscosity index improvers, they can use multi-viscosity oils.
Obviously, rule No.1 for transmission and axle lubes is: Keep them separate. Make sure all containers stay labeled, never put trans lube in an axle or vice versa, and never mix the two types of lubes together in the same component.
Synthetic versus mineral
Mineral lubes come out of the ground and go in your truck after simple refinement by separating them down to a single viscosity and removing impurities. Synthetic lubes are man-made from special chemicals. Synthetics resist breakdown from heat-induced oxidation very effectively, and they are also more slippery and therefore lubricate better. Because of the stability, when you overhaul a component run on synthetics, says Allen, “The parts are cleaner. There’s just an oily film.” In addition, according to McGlone, synthetics run cooler in axles, which keeps those EP additives stable and allows longer change intervals.
Chevron Lubricants, on the other hand, says that properly formulated mineral oil products can give operators the same benefits as synthetic lubricants. Chevron says tests show its transmission and gear oils offer protection and extended service intervals equal to synthetics.
Many industry sources claim using a full synthetic is the most economical way to operate unless you won’t keep the vehicle for long. While synthetic oil costs much more than mineral oil, it typically needs to be changed only 1/5 as often, but does not cost five times as much. Disposal and downtime costs are also higher for mineral lubes. In addition, extended warranties depend on the use of synthetics, so you gain warranty protection even as you save maintenance dollars.
For Eaton Fuller transmissions and Dana Spicer axles, there are synthetic lubes approved for 500,000-mile change intervals, and highly refined mineral lubes approved for 250,000-mile intervals. There are mineral lubes approved for 60,000-mile intervals for transmissions, and 120,000-mile intervals for axles. These apply to on-highway operation. Different intervals apply when running in off-highway or for severe service.
For Meritor transmissions, you can change synthetic lubes at 500,000 miles or mineral lubes at 50,000. For Meritor axles in line-haul operation, you can change synthetic lubes at 250,000 miles; with synthetics and a pump/filter system, you can extend that interval to 500,000. Mineral lubes must be changed every 100,000 miles. For axles in construction or heavy haul, these intervals drop to: 100,000 miles with synthetic lube and a pump and filter; 50,000 with synthetic alone; and 25,000 with mineral lube.
The manufacturer must specifically approve all lubes. You can go to your owner’s manual and look for specifics, or you can consult the component manufacturer. Compare the manufacturer’s specs to the fluid maker’s specs, or, better yet, find the fluid on a list of approved ones.
Using synthetic lube in transmissions is also easier on drivers, making shifting much easier when starting out on a cold day.
Level checks
Both transmissions and axles need frequent level checks. Fluid level is critical because nearly all transmissions and axles are lubricated by splash – fluid is picked up and distributed by the gears. When the level is low, the gears don’t pick up as much and there’s less liquid on the working surfaces, so wear increases. Having enough fluid also helps cooling, especially in the case of axles.
An ideal interval to check fluid levels is 12,000 miles. The truck should be sitting level with the components cool. Remove the filler plug from the side of the housing. The fluid should be right at the level of the plug – not even slightly below – even though you might be able to reach down with your finger and touch it. Fill the unit all the way up with the same approved fluid that’s already in there. Fluid will normally disappear over hundreds of thousands of miles, but if the level is noticeably down when checking frequently, find and repair leaks. (Transmissions and axles do not use fluid the way engines use oil to lubricate their piston rings.) Fixing leaks keeps the level up where lubrication will be most effective. It’s also smart to check for leaks when walking around the truck on a pre-trip inspection.
Leaks often occur at cooler hoses when they’re chafing, at clamped hose connections when clamps break or loosen up, within the cooler itself, or at driveshaft seals. Also, says Pesce, look at PTOs as they sometimes leak because external brackets aren’t supporting them adequately.
Temperature
Temperature is a major issue with all lubes, but especially with transmission lubes. Many trucks suffer from the absence of a transmission cooler, and the problem can be aggravated by the smooth airflow produced by the aero design of late-model trucks.
Both Eaton Fuller and Meritor recommend a transmission oil cooler for any engine 350 horsepower or higher. Coolers are required for all engines of 399 horsepower and above, and at or above 1,500 pounds-feet of torque for Meritor and 1,550 pounds-feet for Eaton Fuller. Pesce says the transmission oil should ideally run 120 degrees above whatever the outside temperature is, for example, 210 degrees on a 90-degree summer day. Fuller transmissions should not see temperatures over 250 degrees routinely or 300 degrees for short periods. Meritor transmissions should not reach more than 275 degrees even for short periods.
Experts say chassis manufacturers often find out that airflow around the transmission is poor and install a cooler even for engines with low power output. If your vehicle’s gearbox runs too hot and there’s no cooler, one should be installed. If there is a cooler and fluid is still too hot, inspect for debris in, or damage to, the fins of air-cooled coolers. For coolers throwing the heat into engine coolant, flush the engine cooling system if necessary, and then take steps to protect it against corrosion and deposits. Remember that you can get a false high indication if the temperature gauge is out of calibration. If things seem okay mechanically, don’t be shy about having the gauge checked!
Pesce says Dana Spicer axles normally run about 100 degrees over the outside temperature. If they rise much above that level, check for low fluid and replenish if necessary.
Meritor says to stop the vehicle and fix the problem if the temperature rises above 250 degrees.
High axle operating temperature can also be caused by an internal problem like gears set too tight during overhaul, or by hard operation with tires that are mismatched or whose inflation pressures are widely different. Extreme applications may require a pump for the power divider in the forward tandem drive axle.
For more information, contact the following:
ArvinMeritor
Tel. (800) 535-5560
www.arvinmeritor.com
Chevron Lubricants
Tel. (800) 533-6571
www.chevron-lubricants.com
Eaton Fuller
Tel. (800) 826-4357
www.roadranger.com