There is a pause when you ride in a loaded tanker that is braking, and it comes with a sense of anticipation. It’s a delay that can make some rookies nervous. You roll to a halt and wait. You know it’s coming. The load surges forward and hits the front of the tank. It thumps and urges the tractor forward against its applied brakes.
An inexperienced driver might easily forget to keep the brakes applied, says Steve Tuschen, whose Joe Tuschen Trucking company hauls milk out of Sun Prairie, Wisc.
Fluids surge at different rates. If you’ve got a thick milkshake back there it might roll up on you like a slow ocean swell. But thin gasoline can surge forward like a huge surfer’s wave in Hawaii’s ‘Banzai Pipeline.’
The tank industry comprises about 8 percent of the entire trucking industry. Whether hauling food grade, chemicals, gasoline, or any of the many liquid bulk commodities our society requires, a tank line exists under more regulatory pressure, more scrutiny of all kinds, than most other types of carriers.
Hauling a tank is a specialized task. Some trailers, for example, have baffles, some have walled compartments, but many are simply long hollow tubes. These “clean bore” or “shotgun” trailers are generally made from stainless steel. One factor that makes them difficult to pull is that they can seldom be filled to capacity. There is a certain amount of surge that must be controlled, especially when starting and stopping.
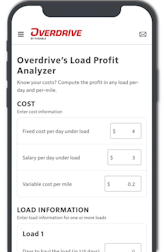
On a ride from Tallahassee, Fla., to Pensacola, Fla., to delivery in Murray, Ky., veteran McKenzie Tank Lines driver Ernie Sellers makes it look easy. But from the start of this 1,165-mile run, the effect of 5,000 gallons of liquid amines in a 7,200-gallon tank is a significant factor in how he drives. Sellers says he seldom pulls tanks with baffles or compartments, since they are mostly used for gasoline and other petroleum products generally taken care of by local drivers. “Baffles and compartments are hard to clean,” Sellers says. “When they’re not needed, they don’t get put in.”
Sellers knows his tanker dos and don’ts. He started pulling tanks for Tallahasee-based McKenzie Tank Lines in 1978, and with very few exceptions, every trip has been aboard a Mack. “On average, I run 2,500 miles a week, local and long. I get home maybe twice a week,” he says. “They keep me busy.”
Tuschen says milk tanks are straight tubes like the majority of McKenzie’s tanks. “Milk turns to butter when it churns. Baffles would turn the milk to butter quicker.” Running 378 Pete quads, Tuschen can load almost 52,000 pounds in a quad if he loads to the top.
There are no baffles in this McKenzie tanker. These long hollow tube trailers are known as ‘clean bore’ or ‘shotgun’ tankers.
There is no need to worry about expansion with milk, a significant factor with some liquids, according to Greg Faulconer, vice president of Dairy Farmers of America, who echoes Sellers comments about baffles. DFA hauls milk, vinegar and various juices in its operations and often carries 50,000 pounds of product. Milk weighs 8.6 pounds per gallon, making a full load in the range of 5,800 gallons. DFA’s tanks have a capacity of 6,000 to 6,800 gallons, leaving plenty of outage and plenty of room for surge to develop.
There are no baffles in DFA’s tanks. According to Faulconer, DFA would lose its Grade A certification to haul milk if the tanks had baffles, but the problem is not surge-related. “Baffles allow for the build up of bacteria,” he says. “They’re too hard to clean.” Cleanliness and product integrity are more important concerns than controlling surge, and both are driver responsibilities.
To minimize the “slosh factor” of a liquid load, Lamar Simpson, McKenzie’s driver training coordinator, emphasizes the need for smooth shifting, long following distances and braking far in advance of the stop. But there is little even the smoothest shifting and brake application can do to prevent 5,000 gallons from sliding against the forward bulkhead when starting and stopping. “Every product is a little different,” says Sellers. “Some are thick, but that doesn’t mean they weigh more. We have some product weighing 16 pounds a gallon. It’s not the weight, though. Thick liquids move slower but they still surge.”
Sellers has never driven anything other than tankers. That experience shows. This trip is a smooth ride even though he is behind the wheel of a truck he has never driven before. McKenzie had put him in a new Mack CX, a “smart truck” equipped with plenty of technology. Sellers’ regular truck has an Mack 6-speed, but this IVI (Intelligent Vehicle Initiative) truck has an Eaton 10-speed. Sellers is pleased with his new ride but believes “fewer gears are better when you’re hauling tanks.” For that reason alone he misses his old truck. “About the only time more gears are better hauling tanks is in the mountains,” he says. True to this philosophy, Sellers nearly always starts out in third gear, saving shifts to keep the load as stable as possible.
In some ways hauling tanks is as sensitive a driving task as hauling swinging meat, an enterprise of mythologically unnerving proportions. A liquid’s surge and side-to-side movement has much the same effect on stability as sides of beef hung from the roof. A freight hauler might also experience the same sensation as surge if he has ever been under a wagon with pin slap, except that pin slap is a sudden, sometimes noisy affair while surge is nearly silent and difficult to predict until a driver has gotten used to the particular product he is hauling.
There is a technique to hauling tanks. Downshifting is different because using the transmission as a brake is not effective. Simpson recommends smooth brake application to bring the load to the front, then keeping it there by minimizing shifts and selecting the right gear for the speed of travel. On the trip to Kentucky, Sellers constantly demonstrates the effectiveness of these techniques.
Even backing up a tank is a different experience. “Tanks don’t have straight sides a driver can watch,” says Simpson. The tank looks very small and does not run true to the wheels of the tractor, its body being set in and difficult to follow. Sellers says he often backs up to get into position to be off-loaded. There are no loading docks in his workday, but there are plenty of skinny alleys.
At McKenzie, drivers get training in a wide range of fundamentals. Drivers are taught how to calculate the weight of each product, and to calculate gross weight and insure bridge law compliance.
Beyond knowing maximum gross and axle weights, drivers must be conversant with trailers, what trailer numbers signify, tank gauge tables (called a strapping sheet) to measure outage, and know how to calculate from this information how much product can be loaded. Every tank is individually calibrated, so the driver must identify the trailer by serial number. A common scenario requires the driver to load 46,000 pounds of product specified by the customer. A driver may be required to compute how many gallons can be loaded, outage, and gross weight. Sometimes the driver must calculate based on dome lid height or the specific gravity of the product. Specific gravity is often listed on the MSDS. The weight of water, 8.3 pounds per gallon times the specific gravity, will give pounds per gallon. Outage is significant. It is “the air space from the top of the dome collar down to the top of the product,” according to the manual. Few tanks are ever fully loaded since many products expand. At least 5 percent outage must be left for poison-by-inhalation liquids and 1 percent for all other liquid hazardous materials to allow for the expansion of warming product.
If products can expand, they can also leak, ‘weep,’ or be left in the tank as ‘heels.’
Expansion is not a problem as long as provision is made for its occurrence. Leaks on the other hand mean that the product and its package have both been compromised and must be contained immediately. Tanks have safety features, called pressure relief valves, which allow for the escape of excess pressure and in some cases permit the exit of a small amount of product. In addition, weep holes are required by regulation. They are often used in the void (the space between tank compartments) to allow small amounts of product to exit.
A heel is product that is left in the tank after unloading. According to Richard Healy, McKenzie’s vice president of safety, heels are not a problem if the tank is used in a dedicated operation since the same product will be going into the tank at next loading. Nevertheless, even dedicated tanks with heels of more than 10 gallons require investigation. If a tank needs to be cleaned, the limit for a heel is reduced to three gallons.
In Murray, Sellers ends the loaded portion of this trip. Doing dedicated runs often means a great deal of deadhead, a circumstance McKenzie works hard to avoid with its non-dedicated tanks. But a dedicated tank cannot be reloaded except by the customer to whom the product was delivered. While drivers at McKenzie get less per mile for deadhead, their hourly rates for loading and unloading add significantly to paychecks. Sellers says he likes his work and is fairly compensated. He averages about $40,000 per year, a figure many OTR drivers who get home much less often than Sellers might envy.
Sellers closely inspects his glad hand and pigtail.
Security Increases for Tanker Drivers
Security has tightened in every corner of the bulk liquid and hazardous materials hauling industry. Richard Healy, McKenzie Tank Lines vice president of safety, says, “Roadside inspections have increased from two to three per week in our fleet to six to 10 a day.”
Agnes Shafer, vice president of communications at Dairy Farmers of America, notes, “Food quality and food safety is always of critical importance to DFA’s trasnsport team. Last year’s terrorist concerns and the anthrax scare gave the ongoing security discussions even more relevance. DFA, like other dairy and food organizations, reviewed its policies and added even more measures of security.” DFA has instituted a chain of custody procedure. All milk tanks are now sealed except when being loaded and unloaded and seals are numbered to provide a chain of custody.
In future, smart trailers connected to onboard computers through power line technology or electronic braking systems will be able to monitor and transmit product information like temperature and pressure to a central location. It is now possible with the addition of software to shut down a truck compromised by a security breach or prevent it from entering certain unsafe areas, according to Charles Groeller at Mack.
McKenzie plans to outfit its fleet with auto inflation tire systems and accident triggered battery disconnect systems to increase on-road safety.