Step 1
It’s not just the rubber that meets the road that keeps you rolling, mile after mile.
Tires aren’t the only rubber that goes endlessly round and round every minute of every trip. The belts under your hood are also running, and, like your tires, if they aren’t properly maintained you might suddenly find yourself parked on an interstate shoulder.
And while you’re checking that belt rubber, inspect its close relative the hose pipe, another piece of rubber that shouldn’t come between you and the road.
How to replace belts and hoses
Drive belts are used to allow the engine crankshaft to turn the cooling fan, alternator and air conditioner compressor. Belts provide a quiet and inexpensive way to carry the drive from the crankshaft to any of these accessories.
The traditional way to install and tension belts was to provide pivot or sliding mounts held in place with mounting bolts and nuts. These systems are still used on many vehicles. For this type of mounting, adjusting belts to the proper tension when installing them, and keeping them at the right tension, is the most critical secret to long life.
Many manufacturers use automatic tensioners to eliminate the need to inspect and retension belts periodically. These also often make the job of belt replacement much simpler. But they have a few maintenance issues of their own, making the traditional belt tensioning systems desirable to truckers who don’t mind checking and adjusting tension occasionally.
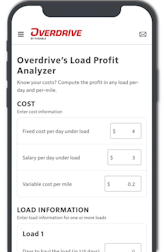
Note: Before working on belts, always make sure the ignition is switched off and keys are removed from the cab.
To find out about the best belt maintenance and replacement practices, we went to see Jim Sayre, Sr., dealer principal, Jim Aloia, service manager, and Jim Bernstiel, technician, of G.L Sayre International/Peterbilt of Conshohocken, Pa.
Replacing belts with standard mounts
The vehicle we worked on was a Peterbilt 379 tri-axle dump truck, powered by a Caterpillar C-15. This engine uses a conventional belt tensioning system. A set of two matched belts drives a four-groove fan hub off the crankshaft, using the back two grooves on the hub. This hub, in turn, drives the alternator and A/C compressor via a set of two matched belts using its front two grooves.
The alternator provides tensioning for itself and the A/C compressor via a bolted, hinge-type mount at its bottom and a threaded rod at the top. The fan hub is mounted to the front of the block on a sliding mount retained by four bolts. A bolt accessible from above allows the sliding hub mount to be moved downward and upward so you can remove, replace and tension belts.
- Loosen the bolts that hold the alternator in place. First put wrenches on either end of the pivot bolt and nut at bottom, using a ratchet and socket on the nut at the front, and take the tension off this mount. Next put a box wrench on the bolt and nut that fasten the link between the threaded tensioning rod and the top of the alternator and loosen them.
- Put a box wrench onto the locking nut at the top of the threaded adjusting rod and loosen it. Once that nut is loose, use an open-end wrench to loosen the nut on the adjusting rod located just below the link to the alternator to loosen it and reduce belt tension. Once tension has dropped enough, you can loosen the nut the rest of the way with your fingers. Turn it till there is plenty of room to remove the drive belts for the A/C and alternator.
- It is now possible to remove these belts from the pulleys. Work them around the fan and remove them from the engine compartment.
Step 4
- 4. There are four bolts fastening the sliding hub mount to the front of the block. First, loosen all four with a box wrench. Next, locate the tension-adjusting bolt, accessible from above the front of the engine. Then put a socket wrench on that and use a ratchet drive to turn counter-clockwise and remove all tension from the fan hub drive belts. Finally, remove the bolt from the front of the engine that fastens down a clip to keep the airline to the fan clutch away from the belts, for working room.
5. Maneuver the belts into a low position on the fan hub, out of the grooves. This sometimes allows you to get them off the crankshaft pulley and around the big balancer on the crankshaft. Unfortunately, on some applications they aren’t long enough. You then need to work blind between the front of the fan and radiator and remove five or six nuts on studs that fasten the fan to the hub. Once the nuts are removed, you can easily slide the fan off the hub, leaving it right behind the radiator, while you sneak the belts out between the fan and the hub.
6. Inspect the belts. Look for cracks on either the outside band or on the inside where the belt rides in the pulley groove. If the belt has been slipping, it will have a glazed appearance and the sides will feel smooth. It should be replaced because it will not be able to drive the accessory without slipping. If the belt is oil-soaked, it should also be replaced because oil causes rubber to deteriorate. In the case of serpentine belts, check for the same kinds of cracks and glazing, and also for fraying that starts at the outside edges and works its way toward the center. Any set of two or three belts must be replaced with a matched set. Running mismatched belts will place excessive stress on the shorter belt and cause it to fail. Also, try the new belts in all the grooves to make sure they ride with the outer diameter just at the top of the groove. Worn grooves allow the belt’s bottom to ride against the bottom of the groove. V-belts need to ride so the V-angled surfaces support the belt, or they will slip. Replace worn pulleys. It’s also smart to look from both sides to make sure all the pulley grooves for each set of belts are lined up with one another. Misalignment results from loose bolts, use of the wrong replacement parts or damaged mounts or accessories.
7. To replace the belts, first work the fan drive belts around or behind the fan and then onto the crankshaft pulley (rear two grooves). If the fan has been removed, relocate it on its studs and install and tighten the fastening nuts, holding the fan by the blades to keep it in position during tightening.
8. Work these belts into position on the rear two grooves of the fan hub. Make sure the belts are not crossed over – so one is in the rear groove on both crankshaft and fan hub, and the other is in the forward groove on the crank and second groove on the fan hub. Then tighten the tensioning bolt for the hub mount. When the belts are snug, tighten the four mounting bolts. Then check the belt tension, preferably with a gauge. To use the gauge, grab it as shown and pull the T toward your palm. Then position the gauge around a belt strand so the gauge body’s two aluminum prongs rest along the outside diameter of the belt and the black hook clears the inside. Release the T and read the gauge along the ridge located on the T handle. The tension for this belt is in the green area – OK for a new belt. Experienced techs can check tension with a thumb. Belts should have good, springy tension but not be tight like a piano wire, says technician Jim Bernsteil. Make brand new ones slightly snugger because they loosen during the first hour of operation.
9. Work the accessory drive belts into the front grooves of the fan hub and the grooves on the A/C compressor and alternator. Make sure they don’t cross over one another. Tighten the lower nut on the alternator-adjusting rod till the belts are snug. Now tighten the locking nut (the upper nut on the adjusting rod), the nut and bolt attaching the link to the alternator and the alternator pivot bolt and nut. Check the belt tension as described above and readjust the tension if necessary. It’s always smart to tighten all bolts before the tension check as this slightly moves things around.
Step 1
Replacing an Automatically-Tensioned Serpentine Belt
This Class 7 International dump truck used by the Pennsylvania Dept. of Transportation is powered by an International DT-466. This type belt is called a “serpentine,” after the way a snake squiggles through the grass, because it zig-zags around several pulleys. Always take note of how the belt is routed before removing it. The serpentine belt drives the water pump, located below the tensioner, and an alternator and fan, located above it, directly off the crankshaft pulley. Note that the grooved inside diameter rides on the crank pulley and accessory pulleys for traction, but that the back of the belt rides against the tensioner pulley.
- Lift out fasteners and remove splash shield from the side of the engine compartment.
- Insert a 1/2-inch socket drive installed onto a breaker bar into the square hole in the tensioner. Now pull the handle downward to rotate the tensioner toward you till the belt is quite loose. Hold the tensioner in this position with one hand (or get someone to hold it for you). Then slide the belt off the alternator pulley and finally release the tensioner and remove the socket drive from it.
- Now remove the belt from all the pulleys. On most trucks, the belt can be removed at this point. On this vehicle, the crankshaft drives a hydraulic pump, and its driveshaft is in the way. If working on a vehicle like this, remove the bolts that attach the U-joint flange for the driveshaft to the crank pulley, slide the shaft forward and remove the belt by passing it between the pulley and the driveshaft.
- To install the new belt, work it around the crankshaft, water pump, alternator and fan pulleys. Then rotate the tensioner with the socket drive as in Step 2. Finally, position the outside diameter of the belt in the tensioner groove and then gradually release the tensioner. Reconnect the driveshaft to the crank pulley.