A classic cabover design with this International Transtar, made from 1968-78.
In the 1970s, it seemed as if everybody wanted to drive a truck, wear a cowboy hat and gab in a new language on the CB. But wanting to be a truck driver in the ’70s didn’t make much sense if you wanted a comfortable life. The cab-over-engine (or COE) design was still king, and the driver was a pawn in an uncomfortable chess game he had little influence on.
But in 1980 things began to change. Rules that had kept freight rates artificially high were loosened substantially by the Motor Carrier Act. Along with the reduction in rules, the federal overall length laws were changed. The COE design had resulted from the need to shorten the cab to increase trailers’ cubic capacity and payload when overall length was regulated. Now only the trailer length had to meet a standard, and it had increased, too. This paved the way for a future in which dozens of other changes would make the truck driver feel like a king of the road.
Past
Larry Strawhorn started his career at Mack Trucks, Inc., in 1965 and was, up until 2002, the vice president of engineering at the American Trucking Associations. He notes a prime force in the evolution of truck design – the carriers that were regulated up until 1980 are now often staffed by Teamsters Union drivers, while most newer carriers are not. “The formerly regulated carriers have to pay the drivers quite well,” says Strawhorn, “while [many of today’s carriers] attract drivers by buying fancy trucks.”
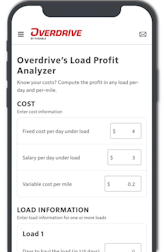
There was a time, Strawhorn says, when the engine air intake was put inside the cab to reduce dust. Drivers had to listen to the intake noise as well as put up with the drafts and dust this brought into the cab.
But the ride revolution was soon under way. Air suspensions would give way to air cabs and seats. Rob Swim, director of dealer marketing at International Truck and Engine, recalls, “When I first started selling trucks, there would be a simple, vinyl-covered bench seat or two seats attached via tubing right onto the floor.”
Swim recalls driving one COE with a seven-speed transmission and an old 6-71 two-stroke Detroit Diesel, which produced a high-pitched roar. The truck’s sound insulation was so poor, his ears were actually hurting by the time he got out of the truck. Because of the old COE’s engine doghouse between the seats, he felt like his right foot was on fire.
Drivers were also irritated by the need to tilt the cab to work on the truck. “Since they lived in the truck, they felt like you were tilting their house 90 degrees,” Swim says. In those days, he told himself, “I’m sure glad I’m a salesman and not a driver.”
Fuel was constantly increasing in price in those days, and many segments of the interstate highway system were reaching completion, raising average cruise speed. The potential for aerodynamics to save fuel became paramount for many truck designers. One such person was Larry Orr, who became chief engineer of PACCAR in the early 1980s. According to Kenworth Trucks: the First 75 Years, by Doug Siefkes, Orr had begun to do wind-tunnel research into aero design with Tim Kangas, PACCAR’s assistant director of R&D, before 1980. They used truck models made of wood and wax. Initial tests were conducted on a COE model. “It proved the whole idea of aerodynamics and fuel economy,” Orr says.
By the time this design was ready, however, Orr had decided that “the rules had changed and conventionals were the future.” The next result, after another year, was the T600, which had a sloped hood, lowered bumpers, sleek fenders, side skirts, roof fairings – the “most important single feature” in terms of aerodynamics, says Ed Saxman, Volvo’s drivetrain product manager – and an air cleaner that had been moved under the hood. A set-back front axle that carried more weight allowed for longer, smoother riding springs.
Present
The longer springs put on many trucks have produced more comfortable, lower frequency ride vibrations, says Saxman. The springs change thickness throughout their lengths, which kills other forms of vibration, too. And their slower movements also dampen out the natural vibration of imperfectly balanced tires, which had been transmitted to the cab by earlier spring designs.
A sharper turning radius was another design innovation that saw full use in the T600. Dubbed “The Anteater” by many drivers, the T600’s fuel economy proved out, and the design has survived with continuous refinement through the present T660.
At the same time, in 1989 an International Trucks aerodynamics expert named Gene Olson reported to Owner Operator magazine that cabovers could be just as aerodynamic as conventionals. International made COEs like the 9700 for some time after that, and they all had the rounded corners and other features Olson described as necessary to keep the flow of air “attached,” running smoothly against the surfaces rather than being bounced outward.
Peterbilt in 1988 introduced its radical 372 COE, often regarded as the most aerodynamic truck ever built. The vehicle featured a rounded front and a two-piece windshield that curved back vertically and on both sides. It had a visor that stood out from the roof and allowed airflow behind it to minimize sun glare without blocking air movement. It also had a front cover that opened at the bottom, allowing access to most minor maintenance items without tilting the cab.
Peterbilt Chief Engineer Landon Sproull says the 372 was derived from the 322 that preceded it. Many drivers disliked the radical, rounded look of the 372, but the model was visible in significant numbers on the roads in the late ’80s and early ’90s. Sproull and Scott Pearson, Peterbilt’s assistant general manager of sales and marketing, claim the real reason for its demise in 1993 was the increasing popularity of conventionals.
Still, Sproull points out that if you look at any late-model aerodynamic Peterbilt with the hood open, you’ll immediately notice that “a lot was learned in designing the 372. You’ll see quite a bit of similarity in the styling cues, like bigger radiuses, and the roof fairing across the windshield.”
Of course, when you add the effect of powertrain improvements to aerodynamics, you end up with a radically different driving experience from what truckers had in the ’70s. Most trucks would struggle to hold cruise speed in 1977, but today there is a generous supply of reserve horsepower. A 65-70 mph cruise can be maintained with less than half the available power in most rigs, meaning drivers can cruise right up long grades and only rarely have to downshift except in mountainous country.
In recent years, automated transmissions that shift perfectly and faster than the best “gear jammer” have attracted many women and less-skilled male drivers. With the kind of power trucks have now, and the improvements in ride comfort and noise level, today’s trucker rides in high cotton compared to his or her predecessors, even with a manual gearbox.
Future
You ain’t seen nothin’ yet. One change sure to come is “brake by wire,” or EBS – the Electronic Braking System. EBS sends signals that feed air instantly to the brake chambers, speeding and helping to equalize braking action. It will come when proved as reliable as present brakes and approved by the Department of Transportation.
Another change will be hybrid drivetrains, which major component makers are working on, and not just for trash trucks. Storing energy in batteries every time you touch the brakes and using it to help you accelerate and climb hills will save a lot of fuel. It will also improve performance, especially when starting on a steep grade. Giving a powerful electric motor the job of moving you out on steep hills will eliminate the shudder and cab rocking you are used to today – and give longer life to the clutch.
There will also be a revolution in diesel combustion and engine energy recovery. Systems that alter Rudolph Diesel’s basic idea will soon be in production to save fuel and reduce emissions under cruise conditions. Today’s diesels always inject the fuel right when it’s needed – with the piston right near the top of the stroke. A new concept, PCCI (“premixed-charge compression ignition”), advances the injection timing so all the fuel goes in well before the burning starts. Compression is reduced by causing the intake valve to close later, which keeps the mixture from igniting too early. Giving the fuel and air more time to mix this way cuts both NOx and soot and helps fuel economy.
Other refinements likely to come include more twin turbochargers running in series, electrically assisted turbos that will supply needed airflow instantly, sensors that measure cylinder conditions directly and optimize all the conditions continuously through feedback, and electrically driven accessories that take less energy to run. One scheme may even recover the energy from the recirculated exhaust, which is now thrown away, to run an extra turbine whose output would be returned to the crankshaft. With all these changes, diesel engine efficiency could rise from 42 percent today to as high as 55 percent.
One major worry is traffic, on the increase and already clogging much of the system. Al Koenig, past president and chair of the American Truck Historical Society, decries the fact that we stopped expanding the Interstate system and so often hear of federal fuel-tax dollars going to airports and mass transit. He calls the present environment “a lot of people out of touch with reality,” and recommends the political involvement of truckers as the only possible solution.
One thing that might help is ITS (Intelligent Transportation System) technology, being developed in part under the Department of Transportation’s Vehicle Integration Initiative. ITS systems could control access to busy roads to prevent clogging, reroute traffic around trouble spots, and might even be developed to control individual vehicles on major highways to prevent the bad driving habits that cause the accidents that so often leave drivers frustrated and late.
Jakes Make Big Impact on Market
Like everything else on the truck, engine brakes have come a long way since 1977. Paul Pare, director of marketing at Jacobs Manufacturing, says that in 1960 when Jakes were first introduced, they grabbed only about 10 percent of the market. Today, it’s more like 90 percent.
The original designs were all aftermarket. But Jacobs and the engine manufacturers have worked more and more closely together to integrate the design over the years. Pare reminds us that the engine brake has traditionally been limited by the design of the engine itself, which is built to produce power, not braking. Through progressive integration, Jacobs engineers have been able to make the best of the situation. Custom-designing Jakes for different manufacturers has reduced the weight from the original 60-65 pounds for separate housings that incorporate the Jake’s power and slave cylinders to 18-20 pounds for an integrated design offered by one manufacturer. The traditional design actuates each cylinder’s braking action off another cylinder’s cam, or, in a few cases, the same cylinder’s cam, at a point in the cycle that is very effective, but not quite ideal. The new design is integrated into its own rocker, with its own cam lobe for actuation at the very best point in the cycle.
Late-model Jake Brakes talk to the engine ECM. This allows them to give improved performance by adjusting the variable geometry turbo, says Ron Carbone, a Jacobs engineer. This integration also allows three power levels to be produced.
All this, says Pare, “enhances not just safety, but also cost. You get a high return on investment with a late-model Jake Brake because of reduced brake lining and drum wear, and increased truck productivity. Today’s engine brakes make it possible to safely go both up and down hills at the same speed.”