WTI Transport driver John “Spoon” Witherspoon tightens winch strapping on a load of building materials on-site at GAF-Elk Corp. in Tuscaloosa, Ala., a favored loading site of many drivers on account of its drivers’ lounge, spacious loading area and one particularly crucial factor – average load time at the site in January this year was just 27 minutes.
Flatdeck load securement is one of those perennial Truckers News topics. Since the North American Securement Standard, the NAFTA-mandated harmonization of U.S., Canadian and Mexican securement regulations, began to be deliberated in the early part of this decade, the anticipation and realization of new rules has dominated the headlines. In practice, though, as any experienced flatbedder will tell you, know-how and attention to safe procedures will almost always satisfy the letter of the law.
Whether you’re already hauling flats or are looking for a change, the thing to understand about flatbedding is that you’ll have your hands on much more than just the steering wheel and shifter. Securing the load is the flatbedder’s job. Tarping it, too, says Tulsa, Okla.-based Arrow Trucking driver Erik Walton. “Folks think of tarping as the biggest problem,” he says, because it keeps drivers and owner-operators exposed to the elements for long periods of time in an attempt to get the prettiest, most aerodynamic fit. But Walton takes pride in the job, echoing many flatbedders when he adds, “The way I see it, they make clothes to cover you no matter what you’re working in.”
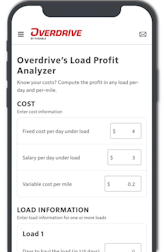
But the toughness and pride that come with a difficult job well done aren’t the flatbedder’s only reward. Delivering on the responsibility for the load is perhaps the best prize. Whatever you’re hauling – a steel coil, finished lumber, pieces of a torn-apart vehicle – it’s your charge. Knowing what it takes to keep it on the trailer and off the road is a must.
Loading
“What the requirements are is a generalization, but it’s hard to haul a generalization,” says independent owner-operator Gil Johnson. The Bristol, Va., native recalls how he learned cargo securement back in 1969, when he was taught by “an old man” at Warren Transport in Waterloo, Iowa. “I was taught then that if you can learn how to tie down rubber-tired equipment, you can learn to haul anything,” he says.
Securing a big John Deere tractor to a 42-foot flatbed was a feat of strength in those days, requiring myriad chains tightened by the lever method. Today’s ratchet binders for chains, along with the increased strength and employment of polyester web strapping, has made a lot of the flatbedder’s work a great deal easier, Johnson says. Years ago, only a frequent lumber hauler might have actual three- or four-inch straps in his toolbox. Two-inch straps with lower breaking strengths were most common. “I remember very vividly up in the north country throwing chains up over a load of lumber,” Johnson says.
Ratchet binders and racheting straps are fast, achieving high tension in very little time (you have to be careful about over-tensioning, though, says Johnson). And slide rails on lightweight aluminum trailers make straps a quicker and more convenient alternative to cumbersome chains on most load shapes.
While the regulations mandate at least two tie-downs in the first 10 feet of a load and one every 10 feet thereafter – in addition to mandating that the sum of the published working load limits of all tie-downs equal at least half the weight of the load – they are intended as minimum requirements. If you’re uncertain of a strap’s WLL, the orange striping down the center of the strap can give you a rough idea. One stripe means the strap has 5,000 lbs. breaking strength per inch. Two stripes – 6,800 lbs. For example, the common four-inch strap with one stripe has a breaking strength of 20,000 lbs. Its working load limit is likely to be about a fourth of that number, or 5,000 lbs.
When in doubt, make certain you’ve far exceeded the minimum. Erik Walton says he spent a good deal of his recent training time memorizing the regulations, but the best piece of advice he got during his three-month on-road training was part of the common sense Johnson stresses. It’s all about driver comfort, he says. “Know your regulations. Know what you have to have on there, but secure it to where you feel comfortable,” he says. On a run from Decatur, Ala., to Houston in January, fully loaded with 47,000 pounds of 30-plus-foot steel tubes, he had 10 heavy four-inch straps securing the load, exceeding both weight and length rules by a large measure.
“The way I look at it,” he says, “you stand back from a load and really look at it, and make sure you’ve secured it from going [in any direction] this way or that way, that way or this way. If you had a big enough hand and you could pick up the trailer and turn it over, would the load go anywhere?”
Steven Booth, an independent owner-operator based in Merrimack, N.H., who transitioned to flatbedding after decades in computer technology, says he agrees in principle with the need for common sense. But he also warns drivers not to take advice from just anybody. “Don’t listen to a bunch of dummies who have no idea what they are talking about,” he says. “Just because someone has been in the business for 30 years does not mean they know the proper way” to secure your load. Booth says you’ve got to train yourself. “I’ve called the FMCSA on multiple occasions and also will pull into a weigh station to ask the DOT for help and advice. Both have been nothing but 100 percent helpful.”
Booth also suggests shippers as great resources. “They’ve seen it done a thousand times,” he says. Booth rolls with “25 straps instead of the normal 12 or so,” he says. Driving and loading mostly at night, sight is a big concern for him, so he will on occasion go with as many as double the required number of straps for peace of mind.
There are situations where common sense might not add up to a legal securement method, though. Owner-operator Bill Mellius, leased to Universal Am-Can, came into the flatbedding business a few years back, just when the new rules were coming into effect in 2004. He tells the story of an 8,000-lb. load that was 26 feet long. “Weight-wise you think two straps,” he says. But length-wise at least four straps is required – two in the first 10 feet to satisfy the front-bracing requirement, then one for every 10 feet or partial thereafter. “I put five,” says Mellius. “You can never over-secure a load. If you don’t feel safe with how you have it secured, don’t move it until you do, or don’t haul it. You’re responsible for the load! If it falls off, it’s your fault, regardless of where you are – [at the] shipper, consignee or on the road.”
And the danger of a spilled load extends not only to highway traffic around you, of course. There’s a reason drivers call a metal coil loaded with its eyes to either side of the trailer a “suicide coil.” Says Walton, “I do this for a job just like anybody else. I’d hate to get killed doing my job.”
Driving
Owner-operator Booth’s prime directive for flatbedders on securement issues has little to do with securement directly. “Drive like the load is not secured at all,” Booth says. Lay off the gas, and do all you can to avoid sharp lateral movements and quick stops. “Movement from the g forces of acceleration is usually not a concern for me,” Booth adds. Drive slow. You’ll save fuel, too.
The federal regulations require all drivers to check the load for securement within the first 50 miles of any trip and every three hours or 150 miles, whichever comes first, thereafter – and every time duty status changes. Prompted by the bumps and vibrations of the road, loads will sometimes shift and settle. As with securing the load, the frequency at which you inspect the load is a matter of comfort. Walton says on particularly worrisome loads he’ll check for shift at every rest area, stopping and tugging all the straps to test their tautness. “I’ll check my distance,” he says, inspecting the length between the front of the load and the front of the trailer, “because I know what I had when I started – from the front to the back. As long as none of that’s changed, down the road we go.”
If you drive at night, visual aids like headlights from cars and other trucks, street lights and emergency flashers should be utilized to help inspect the load. “I will use every opportunity to check my load,” says owner-operator Booth, primarily a nighttime hauler. “Just the simple task of taking a corner provides you with a huge view.” To help ensure safety in low-light situations, again he goes well beyond the securement regulations. “Having sometimes twice the amount of straps or chains gives me peace of mind,” he says.
Veteran owner-operator Johnson recalls well the “good old days,” he says, when there were more flatbeds than cars hauling on the Indiana Toll Road to and from the steel mills on Lake Michigan and elsewhere. He says there’s no substitute for patience in flatbedding, and all drivers would be doing themselves a favor if they just slowed down a bit and took the time to really understand the needs of every load. “Flatbedding is not for people in a hurry,” he says. And though he says he’s heard of great carrier securement schools – he references Landstar’s and CRST Malone’s, particularly – he says there can be no substitute for on-the-road training.
“There’s something about the one-on-one with a guy who’s done it all before,” Johnson says. “That’s the only way you can make it work. You can memorize all this stuff, but if you don’t understand how it actually happens – everything’s on the trailer, everything’s in motion – you won’t get it. Most flatbedders get into some strange stuff. The trick is in being able to think your way through it and make an application of what you’ve learned.”
Rating the Rail
Federal regulations for cargo securement traditionally have been based upon working load limits of tie-downs and trailer anchor points. Four years ago, when the North American Securement Standard (NASS) became the cargo securement law of the land, the new regulations prohibited tie-downs from passing outside the rub rail except in extraordinary circumstances. According to David Lawson, Safety Manager of WTI Transport, drivers prefer to have tie-downs passing underneath the rub rail anyway. Straps that pass underneath the rail wind more directly into the winch roller, permitting more force to be applied to the strap. “Furthermore,” says Lawson, “drivers mainly passed the tie-down over the rail in cases where a section of rub rail was bent in against the side of the trailer. In the case of straps, the driver had to pass the strap over the rail or unwind the entire strap, thread the entire length through the narrow gap between rail and trailer, and then throw the strap over the top of the trailer.” According to Lawson, during a two-year period following the initial implementation of the new regulations, federal regulators discontinued enforcement of the rub rail regulation as an out-of-service violation and then removed it from the regulations completely.
As Lawson explains, FMCSA appeared to be concerned about the strength of aluminum rub rails compared to those on older steel trailers. To address this and other concerns related to trailer anchor points, a new equipment regulation was included in NASS stating that the rating of a tie-down reduces to the rating of an anchor point to which the tie-down is attached if the anchor point is rated lower. “In other words,” says Lawson, “if you attach a 5,000-lb. chain to a 2,000-lb. anchor point, under the regulations the chain becomes a 2,000-lb. chain.”
If your rub rail doesn’t have a specified working load limit, then it is assumed to be zero, Lawson says, thus your straps or chains are rated zero if they’re anchored to it – and you’re not legal. Most drivers and owner-operators prefer anchoring to the under-trailer ledge, if possible. “My trailer is a 2005 model, and the rub rail is reinforced to allow strapping to,” says owner-operator Steve Booth. “But that rub rail is there for a purpose, even though it’s rated to be able to strap to. If you take a corner too sharp and rub up against a wall or pole, that rub rail is there to protect your straps from being torn off. It makes no sense to me to have any part of the strap outside the rail, period.”
Memorable Loads
Every flatbedder has a story about the load that was too tough to tame – or just tough enough. Here are a few examples we’ve found, in the words of the haulers themselves.
A company I was with bought a whole lot of equipment at an auction in Dallas. You pulled into the building, and they loaded all this equipment on the trailer. Greasing, pieces of equipment – a whole bunch of union riggers sitting it on the trailer and that’s it. It was nothing super elaborate, but it was very hard to hold down. You throw your regulation book away then. You wouldn’t know where to start. The more pieces, the more complicated it is to secure.
– Gil Johnson, independent owner-operator, Bristol, Va.
We had one coming from Bedford Heights, Ohio, to Pueblo, Colo. It was two louver dampers for the power plant they’re building in Pueblo. They’re about 20 feet long, so it took up almost the full trailer with two, but they were 10 feet wide, my first permitted load. Because of the shape of it, it was hard to tarp because you’ve got 15 feet of tarp, and then you’ve got an eight-foot flap and you have to figure out how to cover that whole load with that tarp. It gets interesting. We ended up using four tarps, all we had that day.
– Erik Walton, Arrow Trucking company driver, Tulsa, Okla.
My most difficult loads are the crane parts I’ve hauled many times from a local company. These are random-size steel beams and many other odd-sized pieces. I am continually trying to impress on them the angle of my straps or chains. If it were up to them, just the fact that the strap touches the outside of the beam would indicate to them that it’s fine. It’s not. I explain to them over and over that the beam has no downward force being applied to it, and it can slide forward with no problem. They tend to put a smaller beam next to a taller one. I will have them block the smaller one up so it’s just as tall as the one next to it, thereby allowing the strap or chain to exert downward force on both beams.
– Steve Booth, independent owner-operator, Merrimack, N.H.
Strap Manufacturer Celebrates 40th Anniversary
Kinedyne, longtime leader in flatbed and van securement products, celebrates its 40th anniversary in 2008. Since the company’s founding in 1968, the increased use among flatbedders of its core product, the webbing that makes up its durable polyester winch and portable ratchet straps, has driven its success. “Years ago, chains and binders were the mainstay,” says Tony White, company director of sales based at the Prattville, Ala., plant where much of Kinedyne’s catalog is manufactured. “But they evolved into a trailer-mounted winch and a four-inch winch strap – because of how much lighter [straps] were, and how much easier to use.”
Their kindness to cargo helped, too. The typical four-inch Kinedyne winch strap, with a breaking strength of upwards of 20,000 lbs. and a working load limit of 5,000 lbs. or more, can rival the strength of many chains in a flat, non-abrasive package. Furthermore, a brand-new line of webbing, dubbed “Rhino Web,” features a special exterior coating that makes the product more durable in the work-heavy flatbed operation, beating the tensile strength of standard straps after extreme abrasion by 30 percent, White says.
Visit Kinedyne.com for information on products old and new, among the latter including the Saf-T ratchet binder for chains and the Kwik Winder for fast winch-strap rolling.