Previously in this series: Liquid-bulk tanker niche presents both rare and common challenges for owner-ops
Most trucking segments don’t have to worry about regular trailer washouts. Reefer haulers certainly do when moving various food products. Yet it's a feature of liquid bulk tank work that, when dealing with hazmat chemicals, can feel like a complicated bug for many owner-operators. Nearly 1 in every 10 tanker-hauling readers responding to Overdrive’s recent survey indicated washouts presented their biggest business challenge.
“Time is only one thing,” said independent owner-operator Jeff Tomlinson in comments submitted directly to the survey. The “cost of wash and getting it into the rate is always a project.”
Having the trailer sealed after delivery for repeat deliveries of the same product helps cut down on time and money spent on washouts, Tomlinson said, but “the customer that requires a wash after every delivery, even loads from same shipper to same customer, even two loads a day, has made life tough. It eats up serious hours. It's difficult to bill for the wash, but paying a driver to wait for the trailer kills any company profits.”
McCaughey leases this 2018 Freightliner Coronado glider to Dana Transport, hauling chemicals around the U.S.
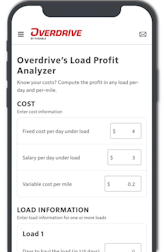
It's not only time pressure that's a task for independents, noted one-truck Tristate Haulers owner-operator Fred Stair. With chemicals, “you have to make sure when you reload, if you’re not doing the same product, that they’re … wash compatible," he said. "So just in case there’s any kind of remnants embedded in the steel, it won’t [react] negatively to the new chemical that you’re going to put in there.”
Time and cost, both, are a factor for owner-operator Stair, too. Chemical washouts occur at "special facilities," he said, "so that’s time-consuming. It’s a cost. Some of these tank washes can be upwards of $500” or more, “depending on the product.”
If you’re primarily pulling brokered freight, negotiate the cost of a washout with your rate. When Bessie Liquids small fleet owner Paul Midgett works with brokers, he often quotes the linehaul rate plus surcharge plus “actual washout,” he said, to ensure he can get paid for the full cost. In his direct contracts with chemical companies, he said, industry standard applies: washes get reimbursed to the carrier.
Yet reimbursement doesn’t cover the time spent waiting. “If you’re lucky, it’d be an hour, two hours,” Midgett said, yet “it’s very typical it could be half a day.”
Again, the time -- as with hard cost -- depends on the chemicals involved. “There’s a process they have to go through,” Midgett said. “Just about everything has got to be a caustic wash, then you’ve got to dry it.” Certain products, he said, “if you had half a dozen drops of water” still in the tanker, “it’ll change the color of the complete load.”
One product he’s hauled is typically a tan color, but even a few drops of water will change the color to burnt orange. It doesn’t actually affect the product, he said, because the end user is going to add water to the product in a sprayer anyway. Problem is the receiver doesn’t know just how diluted the product really is, so it can get rejected.
For example, say you haul a load of herbicide, then plan to load a fungicide or pesticide. If there’s cross-contamination, “you’re gonna kill the best corn that farmer’s ever had, and he’s been farming since 1932, and you’re gonna pay a huge price for that corn,” Midgett said. Segregating equipment for particular products can help guard against such disastrous possibilities. For Midgett, the practice is his form of insurance. With plenty available equipment, he never puts herbicide in the same trailers the company uses to haul fungicide or pesticide.
A one-truck, one-trailer operation has to ensure as best as they can the washout facility does a thorough job to prevent such cross-contamination.
[Related: Finding your niche haul: The tradeoffs and triumphs of freight specialization]
The big slosh: A learning curve for new tank haulers
Keith (left) and Zach Bauer haul milk and related products as part of their Pennsylvania-based Z&K Bauer Transport. Keith runs in the 1996 Kenworth W900L shown here, while Zach pulls with the 2008 Peterbilt 389 glider.Lawson Rudisill
Coming into tanking anew, owner-operators will just about have to relearn how to drive the truck-trailer combo.
Unlike most freight that sits solid, secured to a flatbed or in a van, this freight moves. Sudden take-off or hard braking can get whatever liquid is in the tank behind you sloshing, even jerking the truck around. Take a turn too sharp and get the liquid moving too much to one side, there’s a good chance you’re rolling over.
“There is no such thing as just a wreck in our world. It’s a catastrophic affair if there is one. If it breaks the tanker, you’ve got a huge mess.”
--Small fleet owner Paul Midgett, in Part 1 of this feature
Fred Stair likened it to having a half-empty bottle of water and putting it on its side and tilting it back and forth -- “that’s the same thing as inside the chemical tank,” or any other liquid tank. “If you accelerate too fast, chemical’s gonna go back, and it’s gonna come forward in a vengeance and hit the truck, so if you’re not timing your shifting quite right, you could do some damage to your truck if it’s a manual,” he said. “And also stopping takes a lot of … you have to have a little more finesse on that, as well, when you stop because, again, it’s very unforgiving when you make the wrong move.”
In instances where you may have to stop short in traffic, “it feels like someone rear-ended you,” Stair added. “That’s how hard and forceful it hits the truck."
Keith Bauer, who owns milk-hauling Z&K Bauer Transport with his son, Zach, echoed that sentiment. Slamming on the brakes “can push you through a red light,” he said. “The rollover rate on this stuff is horrible. … It’s constantly moving all the time, so it can be a challenge.”
In their food-grade operation, noted Zach Bauer, tanks don't have baffles like a lot of fuel or chemical trailers have, “so you have 46 feet for that liquid to get moving back and forth and side to side, and so it kind of demands some of the best people to do it safely.”
Shifting itself might instigate the big slosh, he added. "When you shift and go to a higher or lower gear, and then your liquid slops, if you’re in the wrong gear high or low, it’s going to mess your day up." He urges new operators to take it slow, give it "time to learn how to move with it, shift with it and lean with it and everything else.” -- Lawson Rudisill contributed to this report
Access more feature reporting around a bevy of trucking niches via Overdrive's Niche Hauls archive.