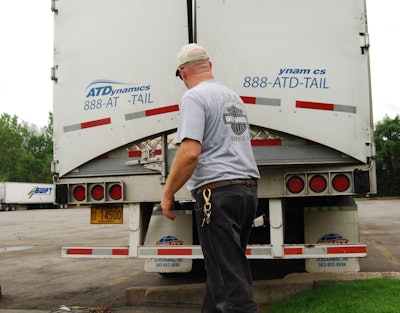
Is a trailer worth the investment? For many owner-operators, yes. And it should take less than four years to earn back that investment, even when buying new equipment. According to Overdrive research, most independent owner-operators already own their own trailers, as do around half of leased owner-operators.
While some leased operators don’t have the pressing need to provide a trailer that most independents do, they often find trailer ownership has significant added earning potential. Leased owner-operators who own their own trailer gross about 6 percent more, or $10,000 annually, than those who don’t. They keep more than half that. Among all owner-operators, trailer ownership brought a $6,000 gain in yearly net income. Even with the additional costs of operating your own trailer, the average added earning potential in flatbed, dry van and reefer segments returns the investment in roughly two or three years.
Some independents own more than one trailer so they can haul van freight one day and flatbed freight the next, and this is not out of the question for leased owner-operators. One big advantage of trailer ownership for many owner-operators is the peace of mind in knowing who’s in charge of maintaining trailer tires, brakes and other equipment. On the other hand, that maintenance is a chore – and an expense – that bobtail-only owners don’t have.
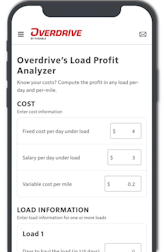
An owner-operator who owns a trailer also has more responsibility for staying loaded, as company drop-and-hook operations are mostly off-limits. Trailer ownership also can carry other responsibilities, such as the cost of plates. But for a leased operator, the real results require consideration of the carrier’s operation and yours. All other factors being equal, many fleets pay owner-operators with their own trailers more than owner-operators hauling company trailers. Trailer ownership also can enable a leased operator to avoid fees passed to owner-operators pulling company trailers.
Some all-owner-operator fleets actually require their leased operators to own trailers. Other fleets, because of liability concerns, are just the opposite, not allowing owner-operators to pull anything but company trailers. Depending on the application, a leased operator can boost line-haul revenue by 5 to 10 percent.
SMART TRAILER SPEC’ING
Factors like maintenance expenses, longevity and handling ease play vital roles in getting what you want in a trailer. You won’t realize low cost per mile if your trailer breaks down, is expensive to maintain or can’t handle your loads well. Knowing definitively what you intend to transport, where you plan to work and how long you intend to keep the equipment will help you balance price with projected maintenance costs. Smart choices will keep your operating costs low and your resale value high.
KNOW YOUR APPLICATION. At spec’ing’s core is understanding your application. Hauling heavy-footprint products like paper rolls requires higher floor ratings. Applications with additional equipment like automotive racks require interior designs that protect the trailer from damage during loading and unloading.
Loading cycles can vary greatly – from weekly to multiple daily loads. The greater the frequency, the faster the equipment wears. Consider your trailer’s versatility, spec’ing the size, model, style and axle and suspension configuration so you can run the trailer in several states, as well as in Canada. If you intend to haul in California, be aware of laws that involve trailers. California is the only state that has an axle spacing law that requires a distance from the kingpin to the rear axle be 40 feet or less. In other states, 43 feet is typical. Spec’ing a sliding axle will give your trailer the versatility to meet standards in California and other states.
Also in California, once engines on refrigerated trailers pass emissions testing, they are in compliance for seven years. Beginning in 2012, engines of 2005 model year and newer must meet ultra-low-emissions standards by seven years after the model year. In 2013, new requirements for fuel-saving aerodynamic equipment on dry vans went into effect for 2010 and older trailers. Already, 2011 and later model-year trailers must be U.S. Environmental Protection Agency SmartWay-approved or equipped with aerodynamic retrofits.
MINIMIZE MAINTENANCE. Spec premium quality for components such as long-life brake linings, wide brakes, long-life wheel ends and seals. Controlling corrosion also will reduce maintenance worries. You’re reducing cost per mile and maintenance costs by spec’ing special coatings that protect trailer parts. Some trailer manufacturers offer galvanizing to protect door frames, hinges and the entire sub-frame.
Spec’ing any system that eliminates wearable parts will minimize maintenance. Hendrickson’s Intraax suspension integrates the axle into the beam with no wearable parts on the axle connections. In reefers, a glass-reinforced thermoplastic liner can reduce maintenance expense and help the trailer maintain excess cooling capacity, reducing operating costs. Similar premium products could include a puncture guard liner to protect the trailer interior against punctures, thermoplastic coating to apply to suspensions and landing gear, and a steel liner with a rigid backing instead of a plywood liner.
REDUCE WEIGHT. Weight reduction helps operators who typically “load out” at 80,000 pounds because it means additional payload. It also helps those who usually “cube out” because every pound saved increases fuel efficiency. Lighter weight usually carries a higher price, but every pound saved on equipment means more potential payload. Furthermore, for every 300 pounds you eliminate, you gain 0.2 percent in fuel efficiency, experts say.
The biggest weight saver is spec’ing aluminum, which also is more corrosion-resistant than steel. You can spec aluminum side posts and roof bows in dry vans. Aluminum can be substituted for steel in cross members that support the floor and for hardwood flooring. Aluminum rims can replace steel disc wheels.
SPEC FOR FUEL SAVINGS The same physics that apply to tractor fuel economy improvements can be applied to the trailer. The more aerodynamic the tractor, the more critical it is for the trailer to play a complementary role in streamlining airflow. Studies have shown that the fuel-economy difference between a typical fleet van and a more aerodynamic trailer is 1 mile per gallon or more. So an owner-operator could
add $10,000 or more to his bottom line in one year by using a trailer with strong aero features. That means the trailer would pay for itself long before it wears out. Aerodynamic devices like side skirts and other belly fairings and tail fairings for box trailers address many aerodynamic problems, including the undercarriage, tandems, the top and sides of the trailer, and the low pressure created behind the trailer. Others, such as gap and nose fairings, improve the aerodynamic efficiency at the front of the trailer.
The other key factors are rolling resistance and mechanical resistance. Design your trailer with the most fuel-efficient low-rolling-resistance tire possible. Incorporate liftable axles so that the only tires on the ground are those needed to carry the weight at any given time. Automatic tire inflation and tire pressure monitoring systems can help you keep optimum pressure in the tires for the load.
To reduce mechanical resistance, more and more operators are employing racing technology by using the MicroBlue polishing and coating process on all bearings, axles and any other component subject to friction. These improvements, along with many others, have shown fuel mileage increases as much as 1 mile per gallon or more over typical trailers.
Many of the aerodynamic devices available for trailers see attention from EPA’s SmartWay Transport Partnership. SmartWay-certified devices can be spec’d when ordering your trailer or acquired separately as add-ons. Furthermore, if you run in California, continued business there may require investment in these devices, as noted earlier.
Optimizing trailer resale value
If you spec your trailer to fit your needs and plan to hold on to it until it wears out, you don’t need to worry about versatility. But spec’ing a trailer too closely to your application will limit its resale potential. A 45-foot trailer will attract fewer buyers and generate less trade-in value than 48-foot or 53-foot models. Consider these other specs:
•Air ride suspension: It will bring more at resale than a mechanical spring system because the trailer will be in better condition and have more versatility in what it can haul.
•Air-assisted pin pull mechanisms: These devices enhance operation and potentially avoid back injuries when repositioning the tandem.
•Automatic docking control: This allows precise positioning as you drop the trailer.
•Deck lock: This device maintains the deck’s height for easier loading and unloading.
•Track width: If you spec the standard track width of 77.5 inches, you could equip the trailer with standard duals or wide-base single tires using 2-inch outset wheels. On the other hand, if you spec an 83.5-inch track using zero outset wheels to accommodate super singles, buyers won’t have the option to use duals.
•Kingpin setting: Spec’ing a standard setting will appeal to more buyers than a customized setting.
•Stability systems: These are gaining in favor as a spec to improve handling, avoid rollovers and increase trailer longevity.
•Automatic tire inflation system: Tire inflation is important to enhancing durability and reducing cost per mile. These systems also help improve cornering and overall handling.