Federal regulations mandate brake wear specifications. For example, air disc brakes must have 1⁄16 of an inch of lining; air drum brakes must have 1⁄4 of an inch. Some types of failures can cause a spring brake to stick on. If the air chamber that retracts a (parking) spring brake fails, it’s a simple procedure to install a caging bolt to manually force the brake to disengage. Carry one along.
PREVENTIVE MEASURES
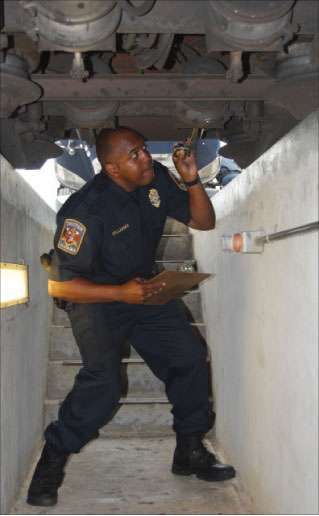
• During preventive maintenance on older vehicles, have a certified mechanic check brake chamber springs. This requires special tools and training.
• Check brake stroke during each preventive maintenance, when you swap trailers and before driving in mountains.
• Determine maximum brake stroke for your slack adjusters in your owner’s manual or in criteria published by the Commercial Vehicle Safety Alliance. Wearing gloves, pull hard on each slack. If any move more than is allowed, on manual slacks tighten the 3⁄8-inch adjusting screw. If an automatic slack adjuster fails to adjust, do it manually, following manufacturer’s instructions.
• With auto slacks, promptly investigate any failure to adjust. Often, wear in brake system parts, not the slack, is the problem. Otherwise, replace or rebuild the adjuster.
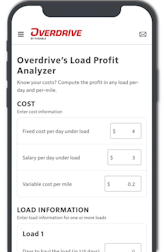
• Replace all worn parts, not just linings, when doing a brake job. Always use original equipment relay valves or replacement valves certified to provide identical pressure. Replace chambers and other parts with those of the same size and length.
• On long grades, apply 10-30 psi to slow the vehicle, and then release in a continuous cycle. Steady pressure can result in a runaway.
• During inspections, check your brake system for leaks. Make sure low-air alarms and the compressor work properly.
• Make sure trailer brake hoses are at least a foot off the ground. n