It’s critical to lube the bearing before installation. The hub should be carefully mounted on the axle to avoid damage to the new seal.
At the current rate of improvement in wheel-end systems, it won’t be long before wheel seals are among the most durable parts of a truck, offering longevity comparable to that of Huck bolts and ashtrays.
A scant five years ago, seal manufacturers were rightly proud that they’d doubled the life expectancy of their products, moving the average from roughly 150,000 miles in the 1970s to nearly 300,000 miles. But nobody’s bragging about that lofty achievement these days. Now the goal – heck, the norm – for better quality seals is 400,000 miles or more. The source of this ever-upward spiral? To quote an old slogan from industrial giant DuPont: “Better things for better living through chemistry.”
Today’s seal materials, with trade names like Viton and Vamac, could easily be confused with brands of anabolic steroids or perhaps the characters of a Star Wars episode. Actually, they’re the latest in a string of exotic substances designed to ignore the high temperature at the end of a working axle.
“Heat’s the enemy of wheel seals, especially those made from standard nitrile rubber,” says John Butler, senior field engineer for Federal Mogul. “At 250 degrees, they crack, break the static band and leave.”
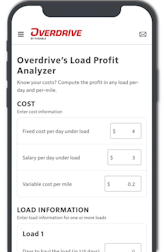
Under normal operating conditions, clean lubricant will keep internal heat levels from rising too high. The real danger is during the first few miles of a trip, before the lube warms and starts flowing freely enough to coat the seal’s lip. This problem is especially common in non-drive hubs filled with semi-fluid grease, an increasingly popular product.
“During a dry start-up, the temperature on a seal lip can easily spike well above 175 degrees,” says Leslie Kern, senior heavy-duty product manager for Chicago Rawhide. “Seals must be built to withstand this sort of continuous abuse.” To do that, manufacturers are constantly looking for new and more durable plastic and rubber compounds. Much of the latest crop comes in the form of HNBR (hydrogenated nitrile) or polyacrylate.
Despite the wizardry of chemists, however, things still occasionally go wrong, and seals fail prematurely. Alan Dick, a product manager at Stemco, contends that the single biggest cause of such trouble is incorrect installation. Too often, he says, mechanics – both professional and backyard – will attempt the job without proper tools (seal drivers), resulting in components that are damaged or mounted slightly cockeyed. Other contributors to seal failure include incorrect bearing tension, faulty bearings or cups; inadequate, contaminated or non-compatible lubricant; or excessive brake heat.
Below are the steps for replacing an oil-bath wheel seal on a Class 8 vehicle axle. More product-specific information is available from each manufacturer. One extremely helpful guide is a Chicago Rawhide publication, Wheel End Systems. Service shop time for these jobs is typically rated at just less than two hours.
THE FIX
- REMOVE WHEEL AND DRUM. Secure the truck with wheel chocks on a flat surface. Raise the wheel end off the floor and brace the axle with a heavy-duty jack stand. Release the brakes and back off the slack adjuster. Do not use an impact wrench for this task. ArvinMeritor adjusters have a locking pawl device that must be pried out or removed before they can be backed off. Unbolt and remove the wheel. Use a large hammer to loosen the corroded bond between the drum and hub, then slide the drum off the brake shoes and place it on the floor, wide side down.
TOOLBOX
3/4-inch socket set
1/2-inch socket set
Torque wrench
Hub sockets
Seal driver
Combination wrenches
Assorted screwdrivers
Assorted pliers
Sledgehammer
Jack stands
Ball peen hammer
Crow’s foot pry bar
Cleaning brushes
Emery cloth
Shop towels
Cleaning solvent
Silicone sealant
Lubricant
FOR MORE INFO
Chicago-Rawhide
(800) 882-0008
Dana
(800) 826-4357
Federal-Mogul
(248) 354-7700
National SKF Automotive
(888) 753-2000
Stemco
(800) 527-8492
Triseal
(800) 910-7325