Some owner-operators nowadays, enamored with the image first popularized by Southern California’s low-ridin’ community, deflate their trucks’ air suspension so the frame hangs several inches closer to the roadway. Unfortunately for many of these hipsters, the slight alteration in chassis geometry dramatically changes driveline angles. This contributes to rapid component wear, roadside breakdowns and mobile repairs when the U-joint fails prematurely.
“That’s probably one of the biggest problems we see today,” says Tom Sanko, driveline product manager at ArvinMeritor. “It seems like such an innocent thing, but it’s quite destructive.”
The working angle of a U-joint should be no greater than 6 degrees, and the difference in angles between front and rear U-joints on the same driveshaft should not exceed 1 degree, Sanko says. It is possible to lower a suspension and maintain proper U-joint angles, but that’s a chore requiring skills and tools beyond the sets possessed by most do-it-yourselfers. Without modifications (or severe damage), a truck’s U-joint angles will always be correct when the frame’s ride height is within the manufacturer’s specification – something almost anyone can determine with just a tape measure and an owner’s manual.
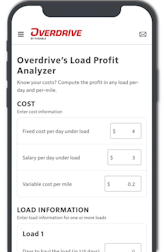
Another big – and easily avoided – problem that dooms many driveline components to an early retirement is inadequate lubrication. Major driveshaft repairs can easily cost more than $1,000; a tube of grease sells for about $2. It’s illogical to spare the latter and risk the former.
But even regular lubrication won’t prevent problems unless it reaches all the critical areas. “I see plenty of cases where people are greasing their U-joints, but they’re not making sure that all cups purge,” says Dave Heinz, a driveline rebuilder at Catco in Burnsville, Minn. “If the cups are too tight, or if there’s some sort of blockage, grease cannot flow into the bearings. That’s when stuff goes bad.” Purging flushes old grease and contaminants from bearing assemblies and indicates that grease is getting to the right places.
To coax reluctant cups to purge, Heinz suggests tapping the driveshaft yoke’s “lug ears” – the metal surrounding the cups – with a hammer while pumping grease. The cups themselves should not be struck. If that approach fails, he says, the U-joint should be slightly loosened and the driveshaft gently agitated. Holding the cups in place with a C-clamp might be necessary during this procedure. If a cup still won’t purge, the U-joint must be replaced.
Some truckers avoid greasing entirely by using maintenance-free components, which cost more on the front end but save time and money during their use. ArvinMeritor’s Rockwell Permalube line, introduced in 1996, has compiled an impressive longevity record, Sanko says. “We don’t really know what the life expectancy is because they just keep going,” he says. “We have samples that approached a million miles, and we pulled them from service just to examine them. Most independents and fleets don’t keep their trucks forever, and that makes it difficult to track [the full life of] these parts.”
Maintenance-free or not, all driveline components should be closely examined at regular service intervals to ensure maximum longevity. These intervals vary from 2,500 miles (off-road and inner-city duty) to 15,000 miles (on highway). Below are the steps for inspecting and greasing a driveline. The replacement instructions apply to Dana’s half-round, and ArvinMeritor’s Easy Service, U-joints.
INSPECTING AND GREASING U-JOINT
A1. SHAKE AND INSPECT. Firmly shake each end of a driveshaft, trying to move it vertically and horizontally. There should be no slack. Carefully check for loose, damaged or missing parts. Also look for signs of cup movement within the retaining hardware. Nearly all these situations would require U-joint replacement. Always shake-test a U-joint before greasing because lubricant will temporarily fill any voids and mask excessive wear.
A2. PROPERLY GREASE. Wipe off each zerk and inject a high-quality (EP-2 grade) grease until it purges from all bearing cups. Grease any slip members fitted with zerks.
REMOVING AND REPLACING U-JOINT
B1. SECURE TRUCK, DRIVESHAFT. Park the truck on a flat surface, set the brakes, chock the wheels, turn off the engine, and put the transmission in neutral. Route nylon utility straps (two per driveshaft) under the shaft being removed and attach their ends to sturdy supports on both sides such as frame rails. This will keep the 70- to 100-pound driveshaft from falling to the floor or onto you.
B2. MARK SHAFT. Use a paint stick or grease pencil to mark the original positions of all shafts, U-joints and yokes. This will greatly help ensure that the parts get reassembled in the proper “phase,” critical for driveline balance and longevity.
B3. UNBOLT DRIVESHAFT. Loosen and remove the four bolts holding each end of the driveshaft in place. In some cases, it’s better to separate the front and rear halves of the shaft at the slip member, leaving the unaffected U-joint in place. The slip area, often covered by a rubber boot, should be well marked to ensure correct reassembly. A pry bar might be necessary to coax the U-joint(s) away from the transmission or differential yoke(s). If a center (or hangar) bearing is involved, unbolt it from the frame. Carefully lower the driveshaft to the floor.
B4. SEPARATE FAULTY U-JOINT FROM DRIVEshaft. Remove the hardware holding the U-joint’s cups in the yoke holes (lug ears). Use a press or puller (available through most truck parts retailers) to dislodge the cups.
B5. CLEAN AND INSPECT PARTS. Wash the newly vacant driveshaft end with a cleaning solution and inspect it for damage: cross-threaded bolt holes or marred yoke surfaces. Polish out small flaws or corrosion with emery cloth or similar material, but avoid removing too much metal. The bores’ measurements must remain exact. Use an alignment bar to check the yoke holes for distortion. The bar should slide through both holes simultaneously. If it doesn’t, the yoke must be replaced at a driveline shop. Also check the slip member. If splines are missing or damaged, or if any permanent lubricant (where applicable) is gone, the driveshaft must be replaced.
B6. INSTALL NEW U-JOINT. Lay the driveshaft on a workbench or in a vise. Poke one of the new U-joint’s trunnions – the part that fits inside a bearing cup – through a yoke hole. If the U-joint has a grease zerk, it should be pointed toward the driveshaft. Look inside one of the bearing cups to ensure that its needle bearings are intact, then slide the cup over the trunnion and into the yoke hole as far as possible. Repeat the procedure on the opposite trunnion. No lubricant should be used on the cups’ outside surface or in yoke holes. Press both cups into place and secure with new retaining hardware.
B7. INSTALL DRIVESHAFT. Under the truck, raise the driveshaft into position, making sure that your marks line up. Attach the separated ends – U-joints and/or slip member – as necessary, using all new hardware (bolts, straps, clamps, etc.). Secure the center bearing if it was loosened or removed earlier. Before fully tightening the U-joint, pump grease into it until all four cups purge. The grease inside new U-joints is for shipping and storage only and is inadequate for actual operation. Finally, torque all bolts to manufacturers’ specs.
TOOLBOX
Combination wrenches
Half-inch socket set
Assorted hammers
Bore alignment bar
Pry bar
Assorted screwdrivers
Snap-ring pliers
Nylon utility straps
Paint stick
Cleaning solvent
Emery cloth
Grease gun
Eye protection
Shop towels
RESOURCES
ArvinMeritor
www.arvinmeritor.com
(888) 725-9355
Dana Spicer
www.dana.com
(419) 866-3900
Federal Mogul
www.federal-mogul.com
(248) 354-7700
Neapco
www.neapco.com
(800) 821-2374
SKF
www.skf.com
(847) 742-7840