Keeping regular records on tires – date and mileage at installation, and then tread depths at mileage increments – gives you information to help assess the best tires for your application.
Not long ago the main specification guiding owner-operators through tire purchases was wear: The longer the tire lasted, the better it was. But the price of fuel, which is affecting most everything in trucking, also is changing the way tires are spec’ed. Now rolling resistance – or its lack – is a major specification because it translates to higher fuel mileage.
Major tire makers have responded with products to meet owner-operators’ needs for longer wear and higher fuel mileage. However, the two characteristics work against each other. Tires with the highest fuel mileage sacrifice wear and vice versa. So tire makers have products that offer longer wear or higher fuel mileage – or a compromise of both.
Of course, other factors affect wear and mileage: proper maintenance, tire quality and match of application to specs.
“When fuel costs continue to rise, the percentage reduction of fuel costs by using low rolling resistance tires increases,” says Michael Burroughes, Michelin America’s product manager. “You can buy tires that are optimized for wear, and an owner-operator who takes care of his tires can get about 400,000 miles out of them. If he buys tires optimized for fuel, he’s going to get 250,000 or 300,000 miles, and he sacrifices that wear. But when he factors in the savings from fuel, he actually comes out ahead.”
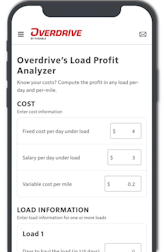
Burroughes acknowledges that most owner-operators are skeptical of this reasoning, but not carriers. Large fleets usually opt for low rolling resistance tires, even to the point of using rib (steer) tires on drive wheels, he says. “Even though they get significantly fewer miles of wear, their savings in fuel more than pays for the additional tires.”
“Owner-operators need to consider removal miles, durability, retreadability, tread design for the application, rolling resistance, and maybe warranty,” says Bridgestone/Firestone engineer Greg McDonald.
A buyer can’t compare products by judging the chemical compounds that go into each brand, because each tire maker keeps that information confidential. Instead, thorough individual record-keeping is necessary, experts say.
“Without numbers that show how the tires are performing, you don’t have enough to make an educated choice,” McDonald says. “Record the date and mileage when the tires go on. Record tread depths at set mileage increments, and then compare them with other sets you’ve had. Did they do better or worse?”
In other words, think in terms of cost per mile. “You might pay more at acquisition,” Burroughes says, “but the payback costs out.”
Drive tires are most important for fuel economy, and tread depth is a major factor in evaluating wear and resistance, says Clif Armstrong, Continental’s commercial division sales and marketing director. “If fuel efficiency is not your main priority, then I’d offer a 30/32-inch tread depth. By virtue of it being deeper, it will get worse fuel economy but longer original miles.”
The lower fuel economy occurs because deeper tread squirms more. “Squirm relates to friction, and that causes roll resistance,” Armstrong says.
Tread depth also serves as a unit for measuring wear, commonly in terms of miles per 32nd of an inch. As a rule of thumb, expect 15,000 miles for every 32nd of an inch.
Advances in tread design have reduced wear and rolling resistance. For example, a closed-shoulder tire, on which the tread is separated from the sidewall by a continuous rib or shoulder, offers decreased traction but better fuel mileage and less rolling resistance because of decreased abrasion.
Michelin uses a decoupling groove, a slit around the tire at the edges of the tread, says Joe O’Connor of Michelin’s Fleet Services Division. “It decouples the tread from the sidewall at the shoulder, minimizing the transfer of dynamic forces from the sidewall to the tread, thus helping to prevent irregular wear,” he says.
Even the shape and direction of a tire’s sipes, the tiny slits in the tread, make a difference. O’Connor says Michelin’s “directional siping technology” and “matrix siping” reduce abrasion and wear and simultaneously increase traction.
“It’s very difficult to put sipes into drive tires because of the driving forces on them,” O’Connor says. “They tend to get chewed up. But this three-dimensional (matrix) sipe allowed us to put this technology in a drive without reducing durability.”
Another tread innovation is Continental’s Visual Alignment Indicator. “We cut six to eight tiny grooves at different depths on our steer and trailer tires,” Armstrong says. “In the very early stages of tire life, the owner-operator can walk by the tire and see if the right side is wearing faster than the left.”
When replacing tires, staying with the same size is wise. “The diameter of the tire is already calculated into the drive train and engine management systems,” McDonald says. “But if you’re spec’ing a brand new truck, you could spec any tire size suitable for the loads you’re carrying.”
“A larger tire will put you at higher speeds than what your speedometer says, and a smaller tire will give you lower readings,” O’Connor says. “Ultimately, you’ll affect the efficiency of the engine.”
Mixing brands is OK. “When it says the size of the tire on the sidewall, all of those are basically the same from brand to brand,” McDonald says. “That way if you get a flat, you can just slap any same-sized new tire on.”
In some ways most truck tires are very alike. “The vast majority – 95 percent – of all the tires that are on the road today are steel-body radial ply tires,” Armstrong says. Yet the specs of these products differ in enough ways to pay off for owner-operators who make informed choices.
“All the major tire OEMs are building great tires,” Armstrong says. “It’s down to fine-tuning your tire choice for specific applications. Look at the benefits of each tire at each position. Look at the depth, tread design and rubber properties, and get the best tire you can within your comfort zone.”
WEAR VS. RESISTANCE: WHAT’S MOST ECONOMICAL?
While longest-wear tires outlast comparable decreased rolling resistance tires, DRR models can save money over time because of their slight advantages with fuel economy and price.
The largest fleets, having crunched the numbers on thousands of trucks, go for DRR tires, says Al Cohn, Goodyear technical marketing manager. But an owner-operator should keep his own records and see whether one type really pays off in his operation.
“With two different drivers and the same truck, load, and route, you’ll get two different wear rates because of variations in driving styles,” Cohn says. Route, terrain, weight, speed, application, trailer axle alignment and truck configuration also affect tire wear, he says.
How much loss of tread you tolerate before changing tires also can affect the comparison. The tread depth on LW tires generally is 30/32 of an inch, Cohn says. Most owner-operators will keep the tires until they’re at 8/32 if they intend to retread it. That comes to 22/32 inches of wear, or about 330,000 miles.
Conversely, tread depth on DRR tires might be 26/32 of an inch. Driven to 8/32 of an inch, DRR tires are good for about 18/32 inches of wear, or about 270,000 miles.
Using those tire life expectations, a one-tenth mile per gallon edge for DRR, and pricing on typical Goodyear LW ($595) and DRR ($562) products, this example shows how the two tires might compare when tire cost per mile and fuel cost per mile are combined.
LONGEST WEAR
330,000 miles