The excess capacity of Mark Jacobs’ Carrier Transicold X-2 is well-suited to the tight temperature requirements imposed by shippers.
“Temperature controlled” doesn’t always mean “frozen.” Owner-operator Mark Jacobs of Eighty Four, Pa., for example, hauls both frozen foods and high-sugar foods that must be kept at 55 degrees, such as chocolate and the sprinkles that top off ice-cream cones. Jacobs therefore appreciates the sophistication — and fuel savings – of his Carrier Transicold X-2 refrigerated trailer, which knows just when to go into start-stop mode to keep his load cool, and communicates any problems via a plain-English display.
Jacobs therefore appreciates the sophistication – and fuel savings – of his Carrier Transicold X-2 refrigerated trailer, which knows just when to go into start-stop mode to keep his load cool, and communicates any problems via a plain-English display.
As fuel costs climb, refrigeration-unit and reefer-van manufacturers haven’t been standing still. Diesel units are becoming more efficient and, in many cases, are being replaced or supplemented by electric motors. Redesigned cooling systems and improved materials mean just enough energy is used, but no more. New technology in both cooling units and vans can help you control costs not only by saving fuel, but by reducing maintenance, downtime and weight.
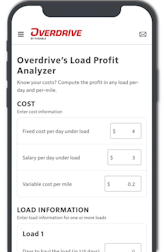
“Thermo King is constantly engaged in research and development aimed at improving efficiency and performance,” says Jerry Duppler, the company’s product manager for trailers.
One change to hit the market in recent years is direct injection. All recent reefer models use this more efficient type of combustion chamber that reduces air motion in the cylinder, thus reducing heat and energy loss to the cooling system.
On its Vector 1800 MT unit, Carrier Transicold now offers Deltek hybrid technology, says Ignacio Aguerrevere, director of marketing and product development. The mechanical connection between the engine and compressor and fans is replaced by wires. The engine drives a 460-volt, 3-phase, 60-hertz generator. The compressor has a self-contained electric motor within its crankcase, making it a “semi-hermetic” design. This eliminates the shaft seal required by mechanically driven compressors, a significant source of refrigerant leaks.
The electric power also drives the evaporator and condenser fans via low-maintenance electric motors.
The high voltage, three-phase current minimizes the amperage draw and complexity of the compressor and fan motors, which makes them more reliable while minimizing energy consumption. Cargo heating is accomplished via electric resistance bars powered by the generator. The charge in the system is reduced by almost half.
The chief advantage of the design is reduced maintenance, Aguerrevere says. The design eliminates belts, gearboxes, axles, fan clutches, several hot gas and defrost solenoid valves, defrost dampers and vibration-absorbing connections.
While there’s no fuel saving directly associated with electric drive when running on diesel power, shutting the diesel off at the set point is more practical because the unit allows more precise temperature control. It’s also possible to heat one part of the van and simultaneously cool another part, while still maximizing engine off time.
Another significant advantage is the superior performance of electric heat when hauling products such as milk and lettuce that must not freeze in the extreme cold of the northern U.S. and Canada, Aguerrevere says. Conventional reefers heat with the hot refrigerant gas produced by the compressor. The gas simply bypasses the condenser and flows directly to the evaporator through separate valves and piping. Because the gas is never cooled or liquefied, and never undergoes the pressure drop that normally occurs in the expansion valve, it heats the trailer interior.
But hot gas bypass systems lose their ability to provide heat “just when you need it most” – in the coldest weather, because the compressor and lines are chilled by the frigid outside air, says Bill Maddox, product manager of special applications for Carrier Transicold. Also, belts can crack in extreme cold even when they are in good condition.
The unit plugs into shore power and operates at 460 volts with the diesel shut down when parked and loaded. This reduces costs, since power derived from the electric grid costs little more than half that generated by a diesel. While 460-volt power is not available everywhere, many warehouses are wired for it. The high voltage maximizes the cooling per kilowatt-hour of electricity consumed. Where emissions laws are a concern, as in California, this is an ideal way to provide refrigeration.
Thermo King also makes units that can switch to electric drive when appropriate. “The advantage of electric operation is the ability to reduce emissions and noise while operating the refrigeration unit when stationary, typically at a loading dock or distribution center,” Duppler says.
Thermo King prefers the simplicity of a direct shaft drive because there is little loss of energy in driving the compressor this way, Duppler says. “During mobile operation, the refrigeration unit compressor is driven directly by the unit diesel engine,” Duppler says. “When stationary with shore power available, an electric motor drives the compressor directly. A clutch isolates the electric motor from the diesel engine.”
The company still makes diesel-only units, of course, and they are preferred “by long-haul and truckload fleets where the majority of operation is mobile and the extra weight of electric standby components is not desirable,” Duppler says.
Carrier has focused on another fuel-saving change: increasing the range of operating conditions when conventional units can run in stop-start mode. When the trailer interior must be kept within a narrow temperature range, the traditional approach has been continuous engine operation. When the set point is reached, engine rpm is reduced, and the compressor is “unloaded” to reduce its capacity. This means solenoid valves bypass several of the six cylinders to reduce the amount of refrigerant compressed. Cooling continues, but at a reduced rate.
Continuous engine operation with compressor unloading ensures stable cargo temperatures when there is a large difference between the desired box temperature and ambient conditions. But when ambient and box temperatures are close together, start-stop operation gives more than adequate temperature control. Stop-start operation uses less fuel because, when running at reduced capacity, the engine and compressor generate a lot of unnecessary friction. It’s like using an idling truck engine rather than the smaller APU engine to handle the hotel load in the cab.
Carrier’s Advanced Microprocessor considers the ambient temperature when deciding whether to go into stop-start mode and uses that mode whenever conditions are appropriate.
Thermo King’s Smart Reefer SR-2 microprocessor control allows the box to be controlled by stabilizing the temperature of either the air returning from the box to the evaporator or the discharge air being circulated into the box. It displays messages in English, Spanish and 20 other languages.
The refrigerant cycle is very sensitive to design changes. A condenser redesign that adds surface to improve cooling, or improves the flow of refrigerant gas through the narrow tubes, could create a noticeable drop in compressor head pressure. This would translate into significant fuel savings.
“Specific circumstances can make it advantageous for a buyer to retrofit existing trailers with a new refrigeration unit,” Duppler says. “Thermo King dealers have the information and training to help their customers evaluate this option and make the right decision.”
CLEARING THE AIR
Because chlorine causes depletion of the ozone layer, the former chlorofluorocarbon (“CFC”) refrigerants such as R12 and R-502 are being replaced by hydrofluorocarbon (“HFC”) refrigerants such as R-404A.
“CFC refrigerants are available for service in decreasing quantities during the phase-out period, with corresponding increases in cost,” says Jerry Duppler of Thermo King. Fortunately, “Most people have already traded in units designed for CFCs,” says Bill Maddox of Carrier Transicold.
Refrigerants aren’t the only reefer pollution being regulated, however. The particulates generated by the units’ engines also are a concern. The California Air Resources Board will require all refrigeration units entering the state and built in 2001 or earlier to comply with strict particulate standards by Dec. 31, 2008.
Thermo King offers a reefer-specific diesel particulate filter that cuts particulate by 50 percent and meets the California standard. The kit includes insulation, controls, and a backpressure gauge. Thermo King dealers also offer Tier II CARB-compliant engine retrofits for existing units.
TAKE YOUR TEMPERATURE BEFORE YOU SPEC
Reefer capacity and insulation specifying is “always a balancing act, based on what you haul,” says Jerry Richardson, product specialist at Wabash National. Will it be frozen or just chilled? With deep-frozen food such as ice cream at minus 20 degrees Fahrenheit, you probably will want 3-inch to 4-inch insulation in the floor and ceiling.
But will you always have a dry freight backhaul? Under those conditions, if less insulation means increased cube or weight capacity, you might actually make more money with a trailer that allows you to carry more on the way home.
Wabash even offers custom insulation packages. Above all, “Know the capabilities of the trailer and reefer unit,” Richardson says.
A big consideration in spec’ing a reefer unit is excess capacity. If you run long hours on the highway and load and unload only at the end of a run, you won’t need it unless shippers demand tight temperature control during loading and unloading. But if you’re making frequent stops and have rollup and side doors that “are open a lot, you had better have more cooling capacity,” Richardson says. “You’ll need both a bigger cooling unit and better insulation.”
Besides all the hot, humid air entering while the doors are open, these types of doors are “not as good thermally” even when closed, Richardson says.
Richardson suggests specifying a durable, thermoplastic trailer liner because “like a Corvette bumper,” it will withstand those inevitable forklift impacts.
When damage does occur, fix it right away. Otherwise, water gets into the insulation and forms a very potent heat transfer medium, destroying the insulation’s ability to protect the cargo and minimize fuel consumption. For the same reason, Richardson suggests carefully controlling pressure washers and working from front to rear, so ship-type lapping of the trailer skin won’t allow water in.
Quality construction also minimizes heat gain. “We build the entire trailer shell as a unit, and then add the foam,” says Craig Bennett, senior vice president of sales and marketing at Utility Trailer Manufacturing. “This allows much better sealing than fabricating the walls, roof and floor separately,” he says.