Tread design subtleties, such as the complex zig-zag shape of the blocks as seen on this Michelin XDA Hypersipe retread, can improve traction by doing a better job of expelling water, mud, snow or even stones.
Tire tread patterns aren’t quite as diverse as snowflake, where no two are the same. But tread does differ widely, not only by brand but by wheel position and application. Understanding the reasoning behind each design can help you choose the best tires for the job.
Curtis Decker, national manager of field engineering at Continental Tire North America, says tread must accomplish three things:
- Give traction directionally and laterally.
- Control the tire’s wear rate.
- Control irregular wear.
It must do these while also allowing water, snow, mud and rocks to be expelled. Truck tire treads have a minimum of two circumferential (around the entire tire) grooves at least 10 millimeters wide to prevent aquaplaning. Some tires are better than others at this “due to the angles of the walls of the lugs and the geometric design of the grooves,” says Goodyear Marketing Communications Manager Tim Miller.
Don Baldwin, product marketing manager for Michelin America Truck Tires, notes that tread also “moves materials out of the way to keep a clear path” and “protects the tire casing from damage.” The rubber compound must be specially blended “to resist chipping, cutting and tearing, allowing it to last a long time.”
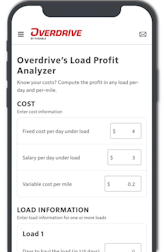
Tread consisting of simple grooves typically is used in long-distance line haul applications to guard against irregular wear and improve fuel economy, says Walt Weller, a vice president for Double Coin Tires.
Zigzag tread is used in local operations, where you need a biting edge for traction. Not only does the reduction in total surface concentrate the weight, but the tendency for the lugs to deflect slightly to one side will concentrate the weight on the outer side of the lug in hard cornering.
One subtlety in tread design is the sipe, a very small space between sections. “The more zigzags you have, the more susceptible the tire is to irregular wear,” Weller says. “Straight grooves with strategic siping in the grooves would be the best type of pattern to reduce irregular wear. Sipes are an additional medium for evacuating water, and also provide more biting edges to provide some additional traction.”
TREAD AND TRACTION
The main reason different wheel positions require different types of tread boils down to circumferential versus lateral traction, says Decker of Continental.
“Circumferential traction is what lug-type tread, used on drive tires, has to provide,” he says. “It can be defined as bite for axle torque. This is especially critical in on/off road applications where the truck may see mud. In general, with a rib tire you’re sacrificing tractive ability for a more beneficial wear rate.
“To get a positive wear rate, you need to keep as much as possible of the tread face on the ground at any point in time, which rib-type tread does better. So, lug-type drive tires give tractive effort, while rib tires give a better wear rate and irregular wear resistance. Rib tires offer more lateral stability, while the strong suit for lug type drives is, of course, tractive effort.”
“Lug tires, of course, provide extra traction in muddy or snowy conditions,” says Goodyear’s Miller. “But drivers like the looks of an aggressive lug design on their drive axle tires even though, for most over-the-road situations, a rib tire would provide adequate traction.”
Drive axle lug tires “may have either an open shoulder or a solid shoulder, with independent blocks in an open pattern,” says Guy Walenga, director of engineering of commercial products and technology at Bridgestone Firestone. “Steers and trailer tires are likely to have more continuous ribs with a solid shoulder. Interestingly, not all tires used on trailers are designed just for trailers.” Some fleets use new steer tires on their trailers.
Michelin’s Baldwin says, “Trailer tires are similar to steer tires in that they are free-rolling and typically ribbed. They must be able to wear evenly under fully loaded or unloaded conditions. That includes the scrubbing action caused when the vehicle is maneuvered.”
Drives must have much deeper tread, says Walenga, because they are constantly under torque, “so the tire is literally buffing itself all the time.”
INSIDE THE MAGIC TRIANGLE
Decker describes the tire designer’s challenge of working within tread’s “magic triangle”: fuel economy, durability and tractive effort. As you move toward any one point, you tend to move away from the other two.
Goodyear’s Miller says treads with high traction use more fuel. “An aggressive tread (higher tread depth) will squirm more,” he says. “Squirming creates heat, which is an indication of energy loss and a higher rolling resistance value than a less aggressive tire. It’s like walking on a soft sand beach compared to a concrete sidewalk.”
In over-the-road trucking, as opposed to pickup and delivery or any driving where the tires scrub a lot, irregular wear is the tire problem that fleet managers lose sleep over. Regular wear is an equal concern, of course. While those vocations with less highway cruising tend to prevent irregular wear by constantly scrubbing the tread smooth with frequent turning and changes in driving surface, trucks that roll straight down the interstate for hours need only a slight alignment problem to create irregular wear that can ruin tires.
Tread wear, both irregular and regular, tends to increase with squirming, as does fuel waste. Trailers run tires with a shallow tread depth and simple ribs because this maximizes the area of rubber on the road while preventing squirming. Low squirm minimizes irregular wear and maximizes fuel economy.
The challenge for the tire buyer is the same as that of the tire designer: optimizing that balance between life, fuel economy and traction. Decker says, for example, “In a high scrub application, you need a deeper drive tire and can’t use a fuel-efficient design.”
Those who run in the North usually prefer an aggressive lug drive to handle snow. Even so, Miller points out, “Several fleets operating on highways in states that do have winter driving conditions have successfully run rib tires on drive positions after gaining drivers’ confidence that traction will not be an issue.”
For those in between, a smart tradeoff might be using a less aggressive tread and then specifying drive axles that not only lock via the interaxle differential, but also wheel-to-wheel.
Balancing fuel efficiency versus tire life is another challenge. Deep tread means a loss in fuel economy and the potential for irregular wear, but deep tread will last longer, provided it wears regularly. Significantly lengthening the life of a tire may well decrease overall costs more than a slight fuel savings.
Walenga says the possible fuel savings aren’t necessarily slight, though. “It can take a lot of tire miles to make up for 1⁄10th of a mile per gallon,” he says. If the fuel savings are there, and the tire’s life can be maintained, then choosing a fuel-efficient design may be smart.
Fortunately, design and technology has helped to minimize such compromises. For example, Decker says Continental’s HDL Echo Plus, which has deep 28⁄32 tread and the company’s most fuel-efficient tread material, achieves a balance between fuel economy and long life.
“The development of new tread compound and casing materials plus the ability to use computer modeling as a design tool have helped engineer tires that optimize performance,” Miller says. “In the recent past, tread compounds that offered low rolling resistance would not wear as well as those that were optimized for long life. This is not true now.”
TREAD DEPTH BY WHEEL POSITION
DRIVE TIRES. Having the deepest treads, these are normally 24⁄32 to 26⁄32 inch. The deepest ones go all the way to 32⁄32, or a full inch.
STEER TIRES. Often 16⁄32 to 19⁄32 inch.
TRAILER TIRES. The shallowest tread, usually 11⁄32 to 16⁄32 inch.
THE HIGHS AND LOWS OF DIAMETER
Many operators run low-profile tires to allow a taller van or higher load while still clearing bridges. Low-profile tires also lower the truck’s center of gravity, helping to avoid rollovers, and they weigh less, increasing payload.
However, those who are accustomed to hauling oversize and over-height loads that route around low bridges anyway often specify taller rubber. Taller tires last longer because they throw a larger contact patch onto the road, while reducing the revolutions per mile. Just make sure you specify a higher axle ratio to compensate for the lower tire rpm and ensure cruise rpm is high enough to handle all that weight.