Navistar International announced Feb. 22 it has an agreement with EcoMotors International to support development of Eco’s OPOC—opposed piston, opposed cylinder—engine that could produce up to 45 percent better fuel economy than current vehicle engines.
Navistar and EcoMotors officials didn’t comment on when the engine would be ready for production. EcoMotors is a Michigan-based that aims to commercialize the OPOC engine for numerous applications, beginning with the heavy truck market. It is not clear if the agreement gives Navistar exclusive rights to use the engine for heavy duty trucks.
Don Runkle, CEO, EcoMotors International, said, “For customers such as Navistar, this remarkable engine technology represents a competitive advantage that enables not only enhanced environmental sustainability, but also greater profitability. Our engineers are working to effectively rejuvenate the internal combustion engine for the 21st century.”
The engine is constructed of perfectly balanced, two-cylinder, opposed piston units that can be linked together with an electric clutch. When two or more units are incorporated into a vehicle, the clutch can disconnect one of them and allow it to shut off under cruise conditions.
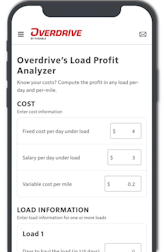
The engine employs an unusual layout consisting of two cylinders located across from one another, each consisting of two pistons that oppose one another and operate in opposite directions. All four pistons operate off separate connecting rods linked to a common crankshaft.
The opposed pistons move toward one another during compression, and back apart during each power stroke. The engine resembles traditional two-stroke designs because there is a power stroke for each crankshaft revolution for each cylinder.
The engine eliminates the cylinder head and all the valve gear as both the exhaust and intake ports are located in the cylinder wall and open and close as the pistons move to uncover them. Its simpler design could reduce production cost substantially. Navistar officials said it would use familiar drivetrain components that would turn faster. This could be possible through use of lighter and smaller drive components.
Since the pistons operate in opposite directions and each operating cylinder has two pistons, the speed at which they move is half that typical in standard engines. This would allow higher rpm’s than in today’s diesels.
The engine uses an electrically driven turbocharger to allow instant boost delivery during acceleration and provide more precise control of boost pressure under all conditions. This virtually eliminates turbo lag and improves low-speed torque by 10 percent or more.
Venture capitalist Vinod Khosla, primary investor in EcoMotors along with Microsoft Corp. co-founder Bill Gates, explained the engine’s combustion and emissions characteristics resemble four-stroke engines more closely than those of two-stroke because of better breathing. Khosla said it can deliver 2-3 times the power density of a standard diesel engine, and produce up to one horsepower per pound.
Eric Tech, president of the Navistar Engine Group, said, “In the finished vehicle, this will yield both better aerodynamics and better packaging efficiency.”