CSA and YOUR RIG
Now more than ever, you’re responsible for what you drive, including company trailers. Take control of maintenance with robust inspection procedures and self-education to avoid inspection hassles.
“I go over my truck with a fine-tooth comb every day,” says owner-operator Bob Grantham, based in San Antonio, Texas.
That routine is arguably the single biggest thing owner-operators can do to effectively deal with much of the increased maintenance scrutiny under the Federal Motor Carrier Safety Administration’s Compliance, Safety, Accountability program.
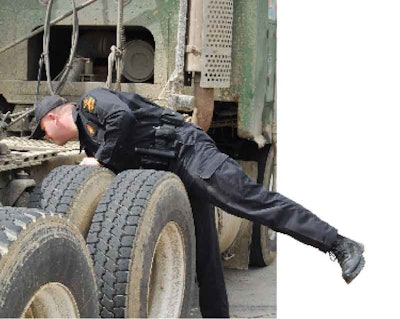
Last month, Part 1 of Overdrive’s guide to dealing with CSA addressed what owner-operators can do to manage the driver-related data that contributes to their own and their leasing carriers’ safety scores. The other side of the coin is what might be the most well-developed of CSA’s Behavior Analysis and Safety Improvement Categories (BASICs): Vehicle Maintenance.
“The vehicle itself is where all the compliance officers have been trained,” says Jay Thompson, president of consulting firm Transportation Business Associates.
From a maintenance perspective, CSA markedly raises the stakes for owner-operators – not just because of the program’s intensity, but because of the level of responsbility it places on drivers. Both the public Carrier Safety Measurement System (SMS) and the private Driver Safety Measurement System (DSMS) reflect accountability for equipment violations, regardless of vehicle ownership.
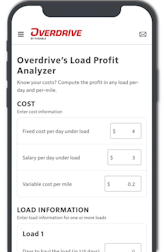
The Vehicle Maintenance BASIC in both ranks carriers and individual drivers on their attention to the nuts and bolts of their rigs. Unlike the SafeStat system that it replaces, which included just out-of-service vehicle violations in its scoring, CSA includes all vehicle violations in near real-time. Scoring is updated monthly.
The lower a carrier’s ranking, the better. With a score above 80 in Vehicle Maintenance, FMCSA could come calling.
Many independent owner-operators are scoring well in the category, as reflected in early SMS results ranking carriers, publicly available since December 2010. The average Vehicle Maintenance score for carriers with up to five trucks was well below the intervention threshold (or “alert” status) and lower than in all four other public BASICs.
Here are key practices to increase the odds that your equipment doesn’t get selected for inspection and that, when it does, it will pass:
Double down on pre- and post-trip inspections.
Performance of the daily vehicle inspections required by federal regulations has degenerated over the years, says adviser Bill McClusky, with owner-operator business services provider ATBS. Too many operators, he says, may hit the ground only one time, if at all, during a pre-trip.
“You need to get underneath and check all the brake mechanisms, air lines going to the trailer, brake travel on the slack adjusters, spring hangers, air bags, checking for all leaks, any loose chassis components,” he says.
“If I had a dollar bill for every inspection I’ve done on this truck, I’d be a rich man,” says Union City, Tenn.-based owner-operator Robert Shumate, leased to Williams Sausage. “In my opinion, you can’t really just look at a truck twice a day and say everything’s OK. I go over the truck early in the morning, check everything out pretty good.”
Throughout the day, Shumate says, he continues to check equipment on his Peterbilt 379. “Say I stop and walk inside at the truck stop. While I’m going in I’m looking underneath the truck to make sure I don’t see anything hanging. When I’m opening the trailer doors to unload, I’m checking out the wheel seals. You’ve got to look at everything, top and bottom, side to side.”
To be completely thorough with your inspections, know equipment regulations. The applicable regulatory parts are 393 and 396 of the Federal Motor Carrier Safety Regulations. Visit fmcsa.dot.gov and search the numbers under “Rules & Regulations,” or revisit your paper copy of the regs.
Haul for a carrier that’s committed to maintenance.
If you’re leased, insist on needed repairs to company equipment as need arises. With CSA in effect, as Shumate suggests, any responsible leasing carrier will want to be on top of it quickly. Though Shumate owns a reefer trailer, he gives the example of a situation he’s seen many times with other carriers. “I pick up a company trailer and let’s say it’s got a bad tire,” he says. “I call the carrier and say ‘Hey, it’s licked, looks like a bathing cap.’ They say, ‘Well, we’ll fix that down the road. It’ll make another trip.’”
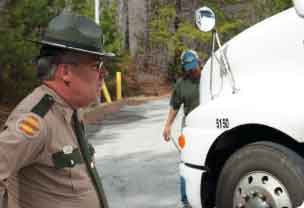
A violation for that tire today might not put Shumate out of service, but it will contribute points to the carrier’s CSA ranking in Vehicle Maintenance. It will stay for three years on Shumate’s employment history.
Jeff Sass, general marketing manager for Paccar Parts, says he thinks fleets will indeed be much more proactive when breakdowns occur, which could mean more assistance for drivers when all manner of roadside equipment issues occur. “If fleets don’t try to be more complete and more careful about their equipment, they’ll be left behind,” he says. “No one’s going to want to take risks with these new regulations – driver or fleet.”
While Sass adds that he expects to see more roadside problems resulting in towing rather than an operator “limping” along to a shop, CSA’s impact hasn’t been fully felt by Peterbilt TruckCare and Kenworth PremierCare, the former of which responds to roughly 50,000 roadside incidents each year.
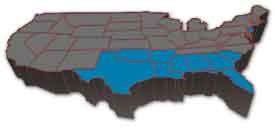
Shumate suggests being a reliable partner in resolving equipment issues. “I’m not going to pull a company trailer onto the yard and do a brake job on it, but if I see lights or an air line I can do, I’ll do that repair. If I make the company money, they’ll help me out.”
Owner-operator Grantham pulls a mix of Greatwide and shipper-owned trailers, hauling on a dedicated account. Greatwide and his shippers, he says, “are very concerned about CSA. When we go out and do a pre-trip, it has to be right, they know it has to be right, and it will be right when we move out of the gate.”
Document all equipment problems as thoroughly as possible on Driver Vehicle Inspection Reports, as well as anything you fix yourself or that the carrier takes care of – or refuses to. Holding onto copies of the reports could mean the difference in whether you’ll be able to successfully challenge a trailer violation on your record in future.

A last recourse in dealing with an unresponsive carrier is to report problems to FMCSA via its whistleblower line. FMCSA can take action if notified of the violation within 60 days of its occurrence. Hotline information is available at “Submit a Safety Violation Complaint” at nccdb.fmcsa.dot.gov. The site directs you to either fill out an online form or file over the phone at (800) 368-7268.
Though Department of Transportation policy dictates confidentiality, no immunity is granted. If company records can trace the trailer to your tractor, you could be opening yourself up for problems.
Assume more control over maintenance.
When your carrier is not fully responsive to company trailer problems you note, one option is to check into pulling your own equipment. If you’re not doing a lot of drop-and-hook, it may be possible to make it work without a hit to your miles and revenue in the short term.
Long-term, once the trailer’s paid for, the higher mileage or percentage pay leasing carriers offer operators with their own trailer could easily add up to a sizable profit boost. And you would command full control of the unit’s maintenance, with confidence that it’s up to spec.
Other steps toward taking responsibility of both trailer and tractor maintenance involve improving your DIY maintenance skills and packing appropriate parts.
Shumate carries extra headlights and taillights with him. Marker lights he’ll buy as needed. Recently, he says, “I had an air line that was starting to irritate me. I went ahead and replaced it. I’d rather do it now than have a DOT officer tell me it’s bad.”
Parts providers are coming to help. Truck-Lite and Grote recently introduced repair kits designed to equip drivers to make easy fixes. “When drivers are doing pre-trip inspections and they find something, they really just want to get down the road and haul their freight and get home,” says Grote National Accounts Manager Mark Blackford.
Keeping such a kit in the cab could well preserve your safety score. The top two (and three of the top 10) most prevalent violations in the Vehicle Maintenance BASIC are for inoperable or missing required lights, according to industry publisher J.J. Keller. Carrying replacement air hoses, belts, reflectors, reflective tape, patch kits for temporary leak repair and/or any other part you could conceivably replace yourself would be ideal to avoid the minor violations that could add up.
Don’t underestimate how much trouble you can avoid by paying attention to the smallest details. Schneider National owner-operator Don Bradley learned this when he was inspected at a New York toll booth.
“The guy actually wrote me a ticket for missing a reflector on the back of my sleeper,” he says. “I thought they were optional, but every truck since 1997 had to have them.”
The problem occurred when Bradley had the sleeper repainted after repairs but didn’t notice the reflectors had not been replaced.
Bradley says that same inspection also noted the “shorty” mudflap hangers he had on his tractor were missing 4 inches of required reflective tape that had worn away. The oversight carried a CSA severity weighting of 3 out of a possible 10 for “no or defective lighting or reflective devices.” By comparison, running a tire beyond the limit of 2⁄32-inch of tread depth, even in the trailer position, contributes at least 8 points to your own or your leasing carrier’s total points.
How to avoid truck inspection
One thing that prompts a truck inspection is independents’ and larger carriers’ Inspection Selection System scores. The formula for those scores was updated with the rollout of the Carrier Safety Measurement System in December. Roadside inspectors use carrier ISS scores to prioritize inspection.
In their outreach to carriers via the Tennessee Alternative Commercial Enforcement Strategies program, Harmon and Hadden focus on what they’re looking at when screening carriers for inspections. If a truck is sitting at a red light across from a patrol officer, Harmon says, “We’re looking at the license plate, for visual equipment violations – is it a clean truck? If a truck is a nasty truck, odds are the driver’s log book is out of line, too.”
In that respect, CSA has changed nothing about who gets inspected, says Transportation Business Associates’ Jay Thompson. Officers “are looking for obvious stuff — a a headlight out will always get you pulled over, even in the daylight if you run with them on for safety.” Thompson adds “anything hanging down, air hoses, wires” to that list.
“Trucks in drayage service on the U.S.-Mexican border are generally much older than the average U.S. fleet,” he says, yet they have the same safety scores as their U.S. counterparts. The reason is the anticipation of inspection, he says, which motivates them to stay on top of maintenance.
In addition to CSA, “The various states’ financial condition has placed them on a hunt for revenue,” says Don Lacy, safety director with Prime. The carrier has been producing DVDs for its largely owner-operator core of drivers on conducting pre-trips in a systematic manner.
Concern over carrier rating disclosures
Plaintiffs in the National Association of Small Trucking Companies et al. v. FMCSA lawsuit are trumpeting the recent settlement with FMCSA as clarifying the question of carrier safety fitness for shippers, brokers and other third parties like factoring companies in freight transactions.
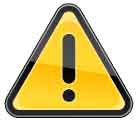
As part of the settlement, the agency agreed to change the “alert” designation for carriers above the intervention threshold in any public BASIC to an exclamation mark symbol. The trucking groups argued the BASIC scores are not intended as summary judgments on carrier safety fitness in any particular operational area. Use of the CSA Safety Measurement System methodology to determine ultimate carrier safety fitness still requires formal rulemaking. In polls of shippers released by MorganStanley prior to the settlement, a majority indicated they would not use a carrier with an “alert” status in any BASIC.
To further clarify the ! status, FMCSA added a disclaimer to data in the SMS that reads in part: “Readers should not draw conclusions about a carrier’s overall safety condition simply based on the data displayed in this system. Unless a motor carrier in the SMS has received an UNSATISFACTORY safety rating pursuant to 49 CFR Part 385, or has otherwise been ordered to discontinue operations by the FMCSA, it is authorized to operate on the nation’s roadways. Motor carrier safety ratings are available at http://www.safer.fmcsa.dot.gov and motor carrier licensing and insurance status are available at http://www.li-public.fmcsa.dot.gov.”
Severity weight for Violation carriers
Tire tread depth less than 2⁄32 of an inch — 8
Stop lamp violations — 6
Brake hose/tubing chaffing and/or kinking — 4
Brake(s) out of adjustment — 4
No proof of annual inspection — 4
No or defective lighting or reflective devices — 3
Oil and/or grease leak — 3
Parts/accessories in unsafe condition — 2
Inoperative required lamp — 2
No/discharged/unsecured fire extinguisher — 2
These base severity weightings are for various equipment violations. The more recent a violation, the heavier it is weighted. For example, violations that occurred less than six months ago in the Carrier SMS are multiplied by three; those between six months and one year ago by two.
DIY tips to keep inspectors at bay
• Tires and brakes
• Lights and electrical systems
• Drivetrain
• Trailers
CSA and insurance rates
“At this point, I don’t think the insurance industry has gotten its arms around the CSA approach,” says 1st Guard Corp. Chairman Ed Campbell. All the same, a move away from the Motor Vehicle Record as the primary data source for owner-operator policy underwriting toward CSA appears likely, if ready access to the data is available, Campbell adds. Compared to driver MVRs, “CSA seems to be driven by greater specificity.” This is perhaps nowhere more true than in its cataloging of all manner of roadside Vehicle Maintenance violations, which have never before been visible to insurance carriers.
For owner-operators with their own authority, this will most likely be the case. “There was information available through SafeStat” on carriers, says Canal Insurance Chief Underwriting Officer Paul Brocklebank. “We used it. But in terms of quantity and specificity, there’s more information available with CSA that we’re able to utilize.”
For leased operators, things are more uncertain.
Mike Miller, Progressive regional marketing director for commercial lines, doesn’t see big changes in underwriting, he says, primarily because “a lot of the driver records are not available for public consumption.” All the same, he adds, “we’d love to one day run the data through to see if there is true predictability” for safety outcomes from on-road behaviors chronicled by CSA.
Gaining access to driver CSA data, whether through the employing/leasing carrier or a third-party service provider like Vigillo, will be key to insurers’ use of the data for pricing. For example, Vigillo now offers a Roadside Resume free of charge to drivers that shows ranking data for drivers and owner-operators with carriers who use their service.
Ultimately, CSA could drive down insurance costs. “I think long-term that this approach to monitoring motor carriers will be more effective in reducing accidents than the old way,” says Wes Brackey, president of Great Plains Casualty. “As the trucking industry continually reduces their accident frequency, it will lower the cost of insurance to the industry.”
Brocklebank thinks CSA may lead to a better-qualified, better-compensated driver pool. As for what that means for insurance, he notes, “with better risk comes better pricing.”
RESOURCES:
1st Guard, 1stguard.com, (800) 995-4827
Canal Insurance, canal-ins.com, (800) 452-6911
Great Plains Casualty, greatplainscasualty.com, (866) 493-2778
Great West Casualty, gwccnet.com, (800) 228-8602
Progressive, progressivecommercial.com, (877) 656-7077
Roemer, insuremyrig.com, (888) 931-1934
Sentry, fortruckersonly.com, (800) 610-4888
Zurich, zurichna.com
James Jaillet contributed to this report.