A Unique Solution
Navistar’s MaxxForce Big Bore’s non-SCR approach to 2010 emissions offers strong fuel economy and performance.
Navistar impressed the market with the 2008 introduction of its 11- and 13-liter MaxxForce Big Bore engines, featuring common-rail injection and a compacted graphite iron block. The 15-liter engine was introduced this year. The truck and engine maker drew attention again when it declared it would use advanced exhaust gas recirculation rather than selective catalytic reduction to meet the extremely low 0.2 grams/hp/hr NOx standard for 2010.
No other competitors followed suit.
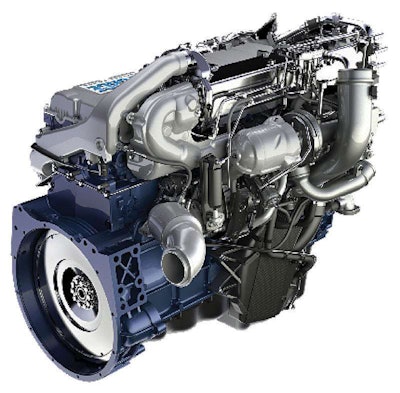
Navistar’s Tim Shick says the Big Bore’s air and fuel handling systems, such as on this 15-liter model, “help deliver peak torque at 1,000 rpm versus a typical 1,200 rpm for competitors.”
Part of the recipe is Navistar’s ability to burn credits from the U.S. Environmental Protection Agency so that its 2010 engine, which reduces NOx to about 0.5 grams/hp/hour, gets EPA certification, while further development work proceeds. The result, the engine maker says, is an engine that delivers fuel economy that equals its 2008 version because of injection and air handling system developments. Add to that the freedom of not having to add diesel exhaust fluid and the combination of a 12.4-liter block and no SCR catalyst or DEF tank, and the engine’s ability to enhance operational ease and payload capacity is clear.
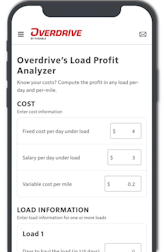
Navistar says the CGI cylinder block itself, the only one in the Class 8 industry at the engine’s introduction (the Paccar MX also uses the material), is vital for making such an engine quiet, fuel-efficient and durable. “This incredibly strong platform handles the loads that deliver the best combustion and dampens vibration and noise,” says Tim Shick, director of marketing for MaxxForce engines. “It carries the load without weighing you down.”
Tim Coffren, vice president of management and maintenance at Hirschbach Motor Lines, says the trucks in his refrigerated fleet with the 2010 MaxxForce Big Bore engines have been getting nearly 7 mpg.
“The engine has been solid,” he says. “We have had no issues.” Drivers have made positive comments about the gradeabilty, he adds, but “can’t hear the engine, and need to rely on the tach” when they shift, Coffren says. “The engine delivers maximum torque really quickly. They need to retrain themselves and feel as if they just got out of truck driving school.” Because the torque shows up very early, “they are forced to use progressive shifting. Those who are patient and learn to drive it properly can get all the acceleration they need,” he says.
Because CGI is so strong, castings “don’t have to be as thick and heavy in order to achieve the desired durability required for a heavy-duty diesel,” Shick says. “This results in up to 500 pounds of weight savings over traditional big bore engines cast from gray iron – which can translate to greater payload and bigger payback.” Pronounced ribbing in the crankcase helps the engine to run quietly, and other design features include what Shick describes as “fewer electrical connections within the controls,” which makes for easier accessibility.
Another element is the engine’s “redesigned combustion bowl, which combines with the higher fuel injection pressure to break the fuel up into a finer mist spread more evenly inside the cylinder, resulting in a more complete and cleaner burn,” Shick says. “That means more power to the wheels and less soot out the exhaust.”
The engine’s most unusual design feature is in the air handling and fuel systems. It combines twin series turbochargers with something unique – an interstage cooler that uses engine coolant at well below operating temperature to remove compression heat produced by the primary turbocharger. This “increases air density to maintain peak power as speeds increase,” Shick says. “The smaller, primary turbo responds quickly for immediate takeoff at low engine speeds, and the larger, secondary turbo provides peak power at higher speeds and on steep grades.”
Another major key to MaxxForce Big Bore performance is “its advanced fuel system, which
features injection pressures of 2,200 bar (approximately 32,000 psi) for precise fuel dosing, injection timing and optimal combustion,” Shick says. “The results: better fuel efficiency, quieter operation and in-cylinder reduction of emissions.” Since this is a common-rail fuel system, those extreme pressures are available even at low engine rpm.
Several 2010 revisions ease maintenance. A Spinner centrifugal oil filter has been added, increasing change intervals from 25,000 miles to 40,000 miles for vehicles getting 6.5 mpg. The secondary charge air cooler that cools the intake air after the second turbo has been moved to the front of the radiator. This not only improves the cooling of highly compressed air, but clears the way for easy removal of the cam cover when it’s time to set the overheads. And moving the doser used for DPF regeneration to where it’s protected from heat has eliminated coking and the need for periodic cleaning.
MaxxForce Big Bore
Configuration: Inline 6-cylinder diesel, four valves per cylinder, overhead camshaft actuated, integral engine brake
Displacement: 12.4 liters, 758 cubic inches
Bore and stroke: 4.96 by 6.54 in.
Compression ratio: 17:1
Aspiration: Dual, staged turbochargers, interstage cooler and air-to-air charge cooling
HP ratings: 410, 430, 475
Torque ratings: 1,450, 1,550, 1,700, plus 1,750 multi-torque
Dry weight: 2,400 lbs.
Oil pan capacity: 42 qt.
Service intervals:
Oil, oil filter change/Spinner cleaning interval: 40,000 miles
Fuel filter: 25,000 miles/12 months
Coolant: 600,000 miles/6 years