Suspension PM
How to keep your air suspension working right for a smooth ride and reduced costs
It is essential to consult the owner’s manual and service manual for your truck or trailer to gather critical information on such items as torque values and service intervals before attempting to inspect or repair any suspension system.
1. Start with the tractor or trailer after sitting overnight, then drive for about two miles. The shocks are the vertical tubes bolted through bushings to the frame at the top and the drive, front or trailer axle at the bottom. Shut the engine down, block the wheels and quickly go around and feel every shock absorber with your hand. Also, view them carefully for any sign of oil leakage.
All should be warm to the touch after having absorbed energy from the moving vehicle as it rides over bumps. Shocks that are nearly at outside temperature or that have any hydraulic leakage should be replaced.
2. Inspect the rubber bushings at the top and bottom of each shock. A minimal amount of cracking is acceptable, but if the bushing is loose, allowing the shock to shift to one side or the other and the bushing to walk out of the tube, replace the shock.
3. Inspect fasteners where they sit against the frame or brackets, looking for rust. Rusty fittings mean a bolt or nut has turned loose, breaking the paint. Loose fasteners must be re-torqued to the manufacturer’s specifications using a torque wrench. Routinely check the torque of all fittings at recommended intervals.
4. Inspect all other bushings — those at the ends of transverse torque rods or the air suspension leaves that hold the axles vertical in relation to the frame. While minimal cracking is acceptable, looseness in bushings will allow these parts to move off center. Loose bushings must be replaced to restore safe suspension function.
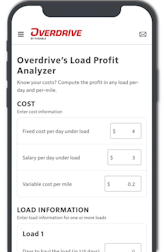
5. Look at your tires. Unusual wear patterns, especially wear on one side or the other, often means worn or misaligned suspension parts. Have the suspension checked with alignment equipment. Suspensions are adjusted at eccentric cams held in position with through-bolts like this one.
6. Don’t weld alignment adjustments, as was done here. Neglect may mean an eventual change in position. But regular maintenance and proper torquing will keep them tight. If they still won’t stay in position, make appropriate repairs. Welding means you can’t align to get safe handling or long tire life.
7. Inspect air bags and all air fittings for leaks. You can use soap and water to locate a small leak — bubbles will make the leak obvious.
8. Inspect leveling valve linkages for loose or worn parts and make repairs as necessary. Check ride height — the distance from the bottom of the frame to the center of the axle — to make sure it is to specification. Improper ride height means poor ride and, with drive axles, damage to driveshaft U-joints. Clean out leveling valve exhaust ports — clogging is the most common cause of valve malfunction.
9. Check the condition of stops designed to support the frame if the air suspension fails. Replace damaged parts, and make sure all bolts are properly torqued.
10. With front axle leaf springs, inspect U-bolts for condition and proper torque. Grease all spring pins (the bushings at the ends that allow the springs to flex) on both leaf springs and air suspension leaves in the manner specified (with weight on or off the wheels). If wheels must be off the ground, suspend the axles on jackstands first.
Thanks to Shane Behmer, service manager, and Brad Galla, technician, at Pennsylvania Truck Centers in Wrightsville, Pa., as well as Jerry Reynolds, national service manager at Hendrickson International, for their help with this story.