Filtration maintenance
Fuel filter service will help prevent roadside breakdowns and prolong the life of your injection system
OneToday’s injection systems use tight clearances and operate at ever increasing pressures. This means you need to replace your fuel filters at recommended intervals, or even before, to avoid a breakdown.
Most truck fuel systems have a primary filter on the suction side of the fuel pump and a secondary filter on the pressurized side between the pump and injection system. The primary filter is designed to separate water and larger particles from the fuel, protecting the fuel pump as well as the injectors. The secondary filter can catch fine particles because of the pressure generated by the fuel pump.
TwoReplacement filters must be of the right micron rating, or fineness. Use the OEM filter or one with the correct “cross number” in a parts book that lists filters by engine application.
1. First, service the fuel/water separator — in this case a Davco unit used by many engine manufacturers. Service the unit at the mileage recommended in the service manual, or whenever the fuel level rises to the line.
Three2. Using the narrow portion of the special wrench, loosen the cap at the top of the unit by turning it counterclockwise and then remove it by hand, placing it on a clean rag.
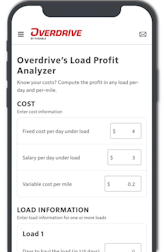
3. With the engine off, place a drain pan below the fuel/water separator, and then open the drain cock and allow the fuel to drain completely. Close the cock snugly.
Four4. Slide the wrench down over the filter until it fits around the large attaching nut at the bottom, and turn the nut counterclockwise until loose. Then turn it off the threads and remove the nut and the large, plastic housing, putting them on a clean rag.
Five5. Gently pull the filter cartridge up and off the seal at its base. Make sure the green seal stays on the filter.
6. Install the new filter and seal onto the nipple at the base, then gently force it downward to make sure it’s fully seated.
7. Lube both new O-rings with a sealer, and then install them into their grooves on the cap and the plastic housing.
Six8. Install the plastic housing with the attaching nut onto the filter base until the housing seats. Then carefully turn the plastic nut until the threads are straight and engage so that it rotates easily. Turn it by hand until it starts to get tight, and complete tightening with the wrench. Tighten it only till snug.
9. Fill the unit to the black ring near the bottom only with filtered fuel.
Seven10. Make sure the spring that forces the filter downward is in place in the bottom of the plastic cap. Then install the cap, turning it gently till it’s straight, the threads catch and it can be turned easily. When it starts to get tight, engage the cap with the semi-circular portion of the special wrench near the handle, and use the wrench to turn it until snug.
Nine11. Now place your drain pan under the spin-on secondary filter. Install a filter wrench over the filter in the proper direction for turning it counterclockwise, and use the wrench to turn it until loose. Once the filter can be turned by hand, remove it and then pour remaining fuel into the drain pan. Make sure the gasket has been removed with the filter.
12. Wipe the filter mounting base with a clean rag.
13. Lubricate the filter O-ring with the silicone O-ring lubricant.
Ten14. Fill the secondary filter with filtered fuel. Pour the fuel through the outside holes only, if you can, to ensure all fuel will be filtered again before it reaches the injectors.
Eleven Fifteen15. Note the instructions on the side of the filter regarding how far to tighten it, normally about one turn. Carefully put the filter straight under the attaching nipple on the mount and rotate it gently until the threads catch and it will turn easily. If it’s hard to turn, loosen it and try again until it’s straight. Once it turns easily, rotate it just until you feel the gasket touch the base and it gets harder to turn. Then rotate it the recommended number of turns, watching the markings on the side. You should be able to tighten it by hand. If necessary, use the band wrench to tighten it gently just to the recommended position.
Sixteen16. Now turn the priming pump plunger counterclockwise to unlock it, and then pump it up and down until resistance increases. Force the plunger back down and rotate it clockwise to lock it down. On engines with an electric priming pump, turn the key on and allow the pump to run until it slows, indicating the system is primed. Repeat if necessary.
17. Start the engine and allow it to idle until the engine runs smoothly, indicating air has been removed from the fuel system.
Big Rig Basics Tip Dehydrate the fuel system
Bob Maddox is the owner of Nick and Dee’s Trucking, a Cummins-powered 13-tractor fleet in Hereford, Texas. “Water freezes at 32 degrees,” Maddox says, “while diesel fuel won’t normally gel until it’s below 20 degrees.” His suggestion is to drain water regularly from your filters to prevent not only injection system damage but freeze-ups in the winter. “Many drivers think they have gelled fuel when a filter clogs, even though the problem may just be water,” he adds. He’s found you get a slush that increases restriction and clogs the filter.
Drain the filter at night, he says, after a day’s run, when modern electronic engines will have heated the fuel in the tank to a warm temperature. Shut the engine off and then turn the key back on if you have an electric priming pump, as do most late model trucks. Then open the drain on the filter and let it drain until you get pure fuel. You should also drain water from your fuel tanks periodically.
He also recommends using some sort of restriction gauge to tell you when your filters are clogged. He uses Cummins’ Road Relay, which sets a code that indicates the filters are clogged, telling him it’s time to change. This prevents you from wasting filters.
Monitor fuel condition with indicators
It’s a smart idea to use a large fuel/water separator with a clear plastic housing to help keep tabs on your fuel’s condition. There are also standard filters that have a dash lamp that indicates water in the fuel/water separator. With separators with clear housings, if there is water in the fuel, it will become obvious that the fuel is cloudy and of a different color from clean fuel. Follow the manufacturer’s instructions on draining out water, which is done with the engine off so you won’t draw water-laden fuel into the injection system. You just need to make sure the fuel you are draining is replaced. Do this by turning the key on and running the electric priming pump or, if a manual pump is used, by operating it after draining each small batch of fuel — about 1 cup.
The Davco-type primary filter used in this article shows when the filter cartridge needs to be replaced. All you need to do is watch the level and replace the cartridge when it reaches the line near the top of the cartridge.
Brian Coomer, service manager, and Kevin Griest, technician, of Cumberland Truck Equipment in Ephrata, Pa., provided help in preparing this article.