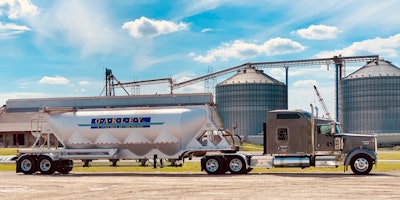
Owner-operators looking for reliable freight in a niche application may find a perfect fit in the dry bulk industry. Buying your own trailer is a much bigger investment than a dry van or most flatbeds, but compensation is often above average. Operation and maintenance of the equipment is easier than it might seem.
Owner-operator Scott Talley of Hohenwald, Tennessee, pulls a pneumatic tank with his 2015 Kenworth W900 Icon for Bruce Oakley Trucking. He hauls salt, catalyst, roofing granules, bleached clay — “anything that’s dry and in powder form,” Talley says. He’s been leased to Oakley for three years.
Dry bulk pay models and rates vary by product, Talley says. Oakley gets paid by the ton for what its drivers haul, though he gets paid by the mile. His runs vary from under 100 miles to 1,000 miles or more.
Because of the variety of freight available, dry bulk work is steady year-round. While Talley declined to cite his compensation, he feels the niche pays more than average.
Dry bulk hauling is generally gentle on trailers, but hauling materials such as salts, sands and gravels can lead to more maintenance. “If you’re hauling a more abrasive material, you will have to replace some valves underneath the trailer” and other small trailer parts, Talley says, but overall it’s “pretty easy on the trailers.”
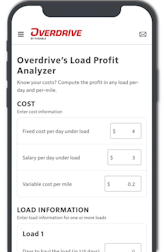
Loading typically takes less than 30 minutes. For an end dump, the biggest concern is keeping the trailer level so it doesn’t turn over, Talley says.
For unload, Talley has a blower on his tractor that pressurizes the pneumatic tank and blows the product out. Tank and line pressures must be monitored so the line doesn’t get plugged, but otherwise, unloading is straightforward, he says. It can take from 90 minutes to eight hours.
“Depending on the product and as long as everything stays dry, it’s pretty easy to clean out,” he says.
Talley pulls a company trailer, but he’s priced new trailers at $60,000 to $70,000 if not more. For an operator looking to buy equipment, “for a tank, you’d have to have a blower, and getting into an end dump, you’d have to have a PTO (power takeoff) and what’s called a wet kit, which is the hydraulic tank that raises the dump bed up,” Talley says. A PTO diverts power from the engine.
Unlike liquid bulk hauling, dry bulk freight rides easy. Once the freight settles in the trailer, “you don’t feel anything move at all,” Talley says.
Many of the refineries and other plants Talley hauls to, built in the 1960s and 1970s, aren’t designed for today’s longer tractor-trailers. “Take your time” in a tight spot, he advises. “We do get into some predicaments.”
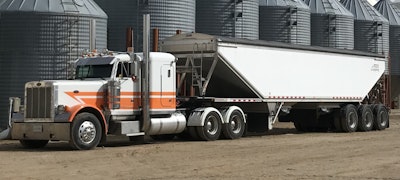
Chad Swan, who runs a grain farm in West-Central Saskatchewan, hauls his own grain, seed and fertilizer with a 2004 Peterbilt 379 and a 2008 Peterbilt. Using a two-hopper trailer, it requires little manual labor, he says. Sometimes he can unload in under 10 minutes.
“For the most part, they empty right out” once you open the chutes, Swan says. “If you get some tough grain or some fertilizer in them, you’ll have to go in and sweep them out, because it can hang up a little bit on the steps.” When switching crops, “you want to make sure you get it all out, and it’s just a matter of sweeping,” which takes five to 10 minutes.
Since Swan operates his own farm, most of his runs are short. From the field to the bin is just 15 miles. In the winter, he has to haul a little further.
Driving on slopes and uneven ground can spell trouble for trailers. You have to know “that weight’s behind you, and you’ve got to take your time, and stop and adjust accordingly,” Swan says.
“I’ve heard of a few different brands having problems with the frames cracking going in and out of fields because you’re going on different slopes, and if you’re loaded, there’s more weight on the axles, and it can be hard on them,” Swan says.
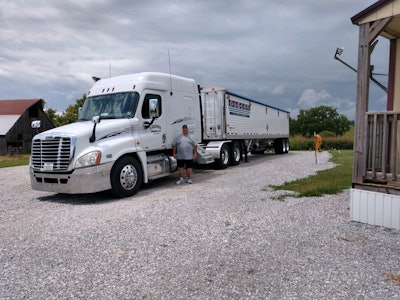
Jerry Dunbar, another Oakley Trucking lessee, hauls mostly different types of smaller, granular grain or powder with his 2011 Freightliner Cascadia and a company 2020 Timpte Super Hopper Bottom trailer.
“It’s not like big chunks that would go in a dump trailer, but it’s not as fine as a powder that would go in a pneumatic trailer,” Dunbar says. He’s priced new hopper bottom trailers at $55,000 to $60,000.
A lot of dry bulk freight pays by the ton, says Dunbar, though he receives a flat rate per mile. He receives bonus pay if he hauls the most weight he can. “Probably the biggest consideration on the hopper bottom is getting your weights right on the front and back hopper while you’re loading so you’re not overloaded and you’re legal,” he says.
Dunbar receives $1.65 for every empty mile, $1.75 for every loaded mile and up to $1.85 if he hauls the maximum weight. He averages his typical per-mile pay at about $1.70 to $1.75 for all miles. On average, he runs 2,200 to 2,800 miles each week.
Another benefit of working with a hopper bottom is the ease of unloading. “When you open the hopper doors, it empties out by gravity,” he says.
Dunbar usually runs from one feed mill or elevator to another, “so you don’t get a lot of off roading or really rough conditions,” he says. He runs throughout a large region from his home near Joplin in Southwest Missouri.
He uses air scales on the tractor and trailer to help load to the maximum legal weight. There’s a lot of “getting on and off scales, because we scale all of the time at the shipper and receiver.”
Dunbar doesn’t have to get in or out of the trailer, because he has an extendable broom that can reach into the trailer when it needs sweeping. He washes the trailers out occasionally, but maintenance is minimal beyond the usual “greasing and checking the brakes and tires.”