Inspect, adjust and replace
Proper attention to belts will save you from the wasted time and expense of a road call
V-belts need two forms of maintenance: They need to be kept at the correct tension, and they need to be inspected and replaced before they fail. Adjusting tension will extend belt life.
Belts are tensioned two different ways. The standard system is designed so the position of one of the driven accessories can be shifted with a rotatable bolt, to increase or decrease tension. Newer systems use an automatic tensioner and roller that bears on the back side of the belt. It rotates on a pivot that has an internal spring and dampener.
To manually check the tension of belts without an automatic tensioner
Figure 2For standard, rigid mounting systems, the best way to check belt tension is with a tension gauge. However, with experience, you can effectively check with your thumb. Depress the belt with the maximum force you can comfortably exert (see figure 1 above). You should not be able to depress the belt more than its thickness in a short span like 1 foot or less, or more than twice its thickness in a span of 2 feet or more.
Using a tension gauge:
1. Look at the gauge dial and make sure it is calibrated in pounds (figure 2, next page). Then look up the required tension in pounds in a guide that comes with the gauge, or in your owner’s manual.
Figure 32. Position the gauge with the face toward you. Depress the knob on the gauge and then assemble it around one strand of the belt, with the two stationary prongs on the inside of the V and the movable one on the outside surface. Release the knob to obtain the reading (figure 3).
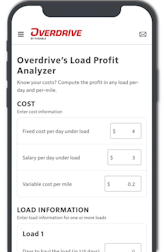
To adjust the tension
1. Loosen the mounting bolts for the alternator, air-conditioning compressor or fan hub. Typically, there is a hinge bolt on one side of the accessory that has a nut on one end, and a simple bolt in a slotted mount on the other side. You’ll have to use a wrench on either end of the hinge bolt.
Figure 42. Turn the adjusting bolt clockwise to increase tension or counter-clockwise to reduce it. Once tension is to specification, tighten the mounts and recheck.
3. If necessary, repeat steps 1 and 2 to compensate for any change.
Recheck any new belt after 3,000 miles.
To check tension with an automatic tensioner
1. Start the engine, raise the hood and get as close as you safely can to the belt tensioner. Any howling sound could mean the device’s roller bearing is worn and should be replaced. Shut the engine down, and remove the keys from the cab.
Figure 52. Depress the outside of the belt with your thumb as shown above. If there’s a problem, you’ll feel a significant loss of tension.
3. There’s a tension marker line on the tensioner and two more on the block. Make sure the single line stays between the other two. Note which way the tensioner rotates to tighten the belt. In the setup shown (figure 4), it would be counter-clockwise.
4. Rotate the tensioner away from the back of the belt using a square socket drive and long handle, unhook the belt, and then slowly rotate the device back and forth between its zero tension position and the maximum. If you feel any roughness, the device’s pivot bearing is worn and should be replaced.
Figure 65. To replace the belt, first note the routing of the belt around the crankshaft, various accessories and the tensioner (figure 5). Draw a diagram if the routing is complicated. Use the socket drive to rotate the tensioner away from the backside of the belt, to reduce tension to the point where the belt can be pulled out of the groove in the tensioner’s pulley, and pull it out. Then, rotate the socket drive so the tensioner will return to its neutral position. Finally, remove the belt from around the remaining pulleys.
6. To put in the new belt, first route the belt around the crankshaft and accessory pullies. Then rotate the tensioner in the direction away from the normal location of the belt, and route the belt next to the tensioner pulley (figure 6). Finally, allow the socket drive to rotate to allow the tensioner to restore tension and then remove it from the tensioner. Check you’ve gotten the correct belt by ensuring that the mark on the tensioner is between the two on the block.
Belt maintenance
Job difficulty on a scale of 1-10: 5
Tools required:
• For standard, rigid mounting systems: Appropriate box wrenches. Ideally, a belt tension gauge.
• For automatic tensioners: A long socket drive handle and socket wrenches of appropriate size.
Note: Always turn the engine off and remove the keys from the cab before working on belts.
Big Rig Basics Tip DIY to save
Randy Roberts runs six cattle hauling rigs out of Winchester, Ohio. He maintains his belts in several ways. When his trucks come to their home base, he opens the hood and looks underneath. He eyeballs belts for fraying or cracks. For standard mounting systems, he checks tension by feel in the standard way. For automatic tensioners, he puts a wrench on the tensioner and rotates it in the direction that loosens the belt. This will tell him right away if the tensioner is getting weak.
Several of his drivers carry extra belts and use standard tools to replace them on the road. This can save a lot of money on road calls and is probably the best tip of all. He also has the trucks inspected regularly at East Earl Truck Repair in East Earl, Pa. Their mechanics inspect belts and make repairs and adjustments to the belts, mounts and tensioning mechanisms as necessary.
Standard vs. automatic belt tensioner systems
When purchasing a new or used truck, you will have to choose between a standard, adjustable accessory mounting system and an automatic tensioner system.
Traditionally, belts were adjusted as an accessory was rotated, typically with the square head of a socket drive. The accessory, such as an alternator, would be mounted on a hinge at the bottom and a slotted lever at the top. Once the hinge bolt and upper bolt were loosened, the belts could be properly tensioned.
An improvement to this system came with “pad-mounted” accessories, where the alternator, power steering pump or AC compressor was bolted at four points and held tightly to the block, killing damaging vibrations. Pad mounts definitely trump a mount where the accessory rotates to adjust the belt, so smart operators always look for pad mounting systems.
The next development was the automatic tensioner, a natural outgrowth of pad mounting systems that called for some sort of movable tensioning pulley. Automatic tensioners use “serpentine” type belts rather than traditional v-belts. They are flat on the outside with grooves for friction on the inside. The tensioner typically works by putting pressure on the outside of the belt and normally has a wheel with a flat outer surface.
An automatic tensioner is normally preferable to a standard, traditional belt tensioning system. New belts installed to the right tension and then checked shortly after and readjusted as necessary will normally run for some time and need only an occasional inspection and adjustment. However, the automatic tensioner just about eliminates such maintenance, as it will adjust to compensate for all but the most extreme level of wear, meaning a nearly maintenance-free belt system for the life of a belt.
The only disadvantage of the automatic tensioner systems is that the tensioner will eventually wear out. While normally simple to replace, operators need to know how to inspect them and can expect an associated parts cost ($100-$200) that does not apply to the traditional, simple systems unless vibration damages one of the brackets.