Preventive maintenance can be expensive, but neglect is even more costly. Systematic PM saves you money in the long run by reducing the chances of equipment failure on the road and reducing time lost to repairs. It also helps reduce the severity of failures if they do occur. Some industry estimates say preventive maintenance can cut breakdown costs in half, and a properly maintained engine will last much longer and use less fuel.
Nearly all owner-operators change their oil often and/or use oil analysis to determine precisely when to change if at more distant intervals. Also important is using quality oil and filters, as well as timely coolant servicing (including system flushing), because these practices will help an engine last longer. Using synthetic transmission and axle lubricants and changing at required intervals also will help extend component life.
Don’t neglect other less-familiar practices. Adjusting the overheads after break-in and then at the required infrequent intervals saves fuel, reduces oil sooting and wear, and is likely to prolong the life of both valves and injectors. Replacing injectors before combustion gets too dirty also will prolong life.
Using quality fuel filters will, in turn, prolong injector life. Various long-life antifreeze options, such as extended life coolants and coolant filters that add supplemental coolant additives on a controlled basis, should be considered even though the initial cost may be higher.
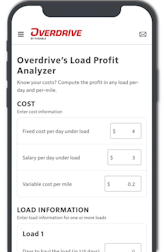
A simple maintenance plan that doesn’t require technical skills and special equipment will include tires, engine oil, wipers, lights, filters, coolant and belts/hoses. A more technical PM will include brakes, drive axles, wheel seals, transmission, batteries, exhaust, driveline, suspension, steering, clutch and engine. For post-2007 model years, too, it will include the diesel aftertreatment system.
An ounce of prevention
Become familiar with every inch of your truck and know which components can fail and under what circumstances. While many a successful owner-operator has started out their career in trucking in a shop working on diesels, you don’t have to be a mechanic, but you should be familiar with a truck’s mechanical operation and how systems interact.
Manufacturers recommend a standard PM schedule for every model. The Technology & Maintenance Council of the American Trucking Associations also provides PM guidelines for tractors and trailers. Follow these schedules diligently, and you’ll head off a lot of trouble.
Daily pre- and post-trip inspections should be a routine part of your day, and can help identify problems before they become emergency situations. A leaking differential should be repaired before the lubricant loss causes component failure. Early warning signs found by engine or driveline component oil analysis can alert you to serious problems before costly troubles occur. If you have a truck with more than 300,000 miles, consider running a dynamometer test once a year.
Always look for common problems such as seal leaks, loose bolts, chafed wires and hoses, improper adjustments and worn, broken or missing parts. If you cannot recognize these problems, have a qualified technician inspect your rig every six months or even more frequently. Overdrive 2024 Trucker of the Year Alan Kitzhaber, for instance, long stuck to a between-every-oil-change schedule for a detailed inspection with his preferred shop. (He successfully operated his 1995 Kenworth T600 for a whopping 4 million miles-plus with maintenance diligence.)
An alternative is having lubrication service done at a dealer or truck stop where experienced technicians will look for problems as they work.
The same can be said for maintaining a trailer. For a dry van, check the suspension during pre- and post-trip inspections, perform a pre-load adjustment and annual inspection on the bearings, check the brake lines regularly, and check tire inflation and wear regularly. Also replace the work scuff liner to protect the trailer walls, check the roof during pre- and post-trip inspections for holes and leaks, inspect the threshold plate often, and inspect the floor to spot weak spots or small holes.
Watch your batteries. Winter weather often is blamed for battery failures, but damage caused by hot weather often is the primary culprit. Battery wear can go undetected for months, but routine checks can head off potential failures.
Lead acid batteries have a higher discharge rate in elevated temperatures, shortening service life. To counter this, many operators running trucks with auxiliary power units have migrated to absorbed glass mat batteries, which are not susceptible to electrolyte loss like lead acid batteries.
Solar panels are a cost-savings option to help power auxiliary climate control and in-cab power systems that reduce the need to idle, and to reduce some stress long-term on the alternator. New Lithium Iron Phosphate or Lithium ion battery configurations, too, show promise in this area, particularly in configurations to power auxiliary air-conditioning in the warmer months.
[Related: Stay ahead of the inspectors with maintenance topics in Overdrive]
Keep engine coolant clean and strong. While today’s trucks don’t leak coolant as much as older trucks, coolant still degrades over time. As coolant’s protective additives become depleted, its corrosion-fighting properties are diminished.
Also, if undiluted coolant and coolants of different types are continuously topped off with water, it can degrade the fluid’s freeze and boil protection. Today’s coolants can reach 600,000 miles, with many warrantied up to a million miles.
Saving for maintenance
Every good PM schedule begins with establishing a maintenance escrow savings account. An industry standard for maintenance escrow savings is based on a time-proven formula, though in the inflationary environment of the last few years a smart owner-operator will set aside even more:
Maintaining brakes
It’s no surprise that violations for problems with a truck's brakes are among the most cited by roadside inspectors, given their constant wear and critical safety role. Pre- and post-trip inspections are key for identifying issues before violations occur.
Obvious red flags include rust streaks, air leaks, oil stains, air lines rubbing on crossmembers or frame rails, bad or missing gladhand seals and brake components that are worn, missing, broken or loose. Look at components such as air chambers that may be corroded or rusted. Also check the air system for contamination or water, slack adjusters, brackets and air lines that may be hanging low.
The best ways to keep slack adjusters maintained are to grease them regularly, making routine visual inspections and operational checks, and avoiding manual adjustment for automatic adjusters.
Manually adjusting automatic slack adjusters (ASAs) can harm the longevity of the unit. The National Transportation Safety Board has even condemned the practice of manually adjusting ASAs. ASAs typically only need to be manually adjusted at installation or when a brake job is performed. ASAs are designed such that they “automatically” compensate for brake wear as it occurs.
[Related: An assist for avoiding brake adjustment violations]
Brake experts note, however, that they adjust with full brake applications, whereas it’s possible with routine driving to only apply the brakes with 10%-20% air applications under normal conditions. Without full brake applications, the ASAs are not compensating for the wear and opening the operator up to brake problems and adjustment violations.
Use the low-air alarm test during your pre-trip inspections to get those full applications. Build air to 120 psi, then repeatedly apply the brakes, bringing pressure down to set off the alarm. Brake experts recommend six full brake applications with at least 90 psi as part of a pre-trip. You may need to rebuild air in the system to get those full applications.
Also listen for leaks by building pressure in the air system while keeping the parking brakes applied, then walking around the truck listening for leaks. When doing this, look at your air gauges to make sure the compressor is building correctly, and make sure none of the warning lamps are illuminated on your dash.
Finally, inspect the pad thickness visually, measure caliper position with a ruler, and inspect rotors for cracks every four to six months. Catching any of these issues during your inspections can eliminate accelerated wear, brake damage and damage to other components.
Read next: Effective PM starts when you buy the truck: How to deal with dealer service