Bryon Stoll, who co-owns Suprise Trucking with his wife, Holly, got a bit of a rude awakening recently when two owner-operators leased to the fleet received two separate brake violations written at the same scale in Oklahoma for adjustment issues on two different Suprise trailers.
The first time felt like "a set-up," he said. "There were three roadside mechanics on-site waiting" for somebody to have an issue, "and then they still charge you for the callout fee, even though they’re sitting right there."
The second trailer, within about a couple weeks, had the selfsame adjustment issues, at the same scale. "The funny thing is they had just been DOT’d," not long prior to these pull-ins on I-35 coming into Oklahoma from the north, he said.
Odds are, given the intensifying focus Oklahoma inspectors have put on brakes in recent years (as illustrated on the chart), his Wisconsin-based small fleet is not the only one dealing with the issue.
[Related: Suprise Trucking's long road to resurrection after setbacks for Bryon and Holly Stoll]
Stoll got to thinking about what he could do to assist operators in knowing clearly when adjustment is in order -- and out, of course. He purchased an aftermarket adjustment-check assist device called Brake Safe. The device has been around for a couple decades at this point, said Andy Malion, president of wheel-end safety company Spectra Products in Ontario, Canada. After automatic slack adjusters were mandated in the late 1990s, manufacturers "had to do a visual indication" with their products so an operator could "see the stroke condition."
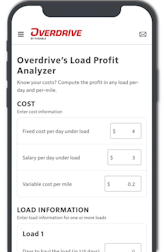
Yet, Malion added, given the rough-and-tumble life of any truck's underside, "you lose visibility into it fairly quickly."
Brake Safe was introduced to help.
"It’s very simple," said Bryon Stoll. "The install is basically just two bolts. The whole kit comes with everything you need for long stroke, short stroke if you have it." The picture here shows the visual indicator on the first reefer trailer on which Stoll has had the device installed. "When it’s set up, those yellow goal posts stay stationary," he added. When brakes are applied, the "little red indicator slides back and forth" with the push rod. "As long as it’s between the two yellow goal posts you’re within regulation."
As is perhaps more apparent from this view, reading stroke compliance visually with the device is a matter of viewing the indicators from the correct angle -- straight on (at a position perpendicular to) the yellow "goalposts" as Stoll put it. As is evident in this picture, those posts are offset from the red indicator itself, which is attached directly to the pushrod.
Costs? Per-axle, Stoll said he paid $78 for each kit (in rare instances investment in an additional component may be needed) -- under $200 total in the vast majority of cases to outfit a single two-axle trailer running drum brakes. "If you know how to turn a wrench," he added, each kit comes with "very good instructions in there – you can go under there and install them yourself," though he's having a tech he uses for routine maintenance add them to all his trailers as they cycle through. (Here's a thanks to that tech, Ben, for taking the pictures here while the first outfitted trailer was in the shop last week.)
Stoll plans to put them on the all three axles of his personal tractor, too, eventually, he said, and some of the owner-operators who run leased to his operation are thinking about doing the same.
[Related: It's prime time for air disc brakes, with nearly 2 in five owner-ops running them on the tractor]
Malion contacted Stoll after the small fleet owner made the executive decision to outfit the entire 10-trailer fleet (reefers and two vans) and put in his fairly sizable order through the LetsTruck.com site.
As Stoll told it, "When he saw such a big order come in, he said, 'I bet somebody got hit at a scale somewhere.' It’s one of those things. I was looking at the product for a long time but I never really had an issue."
Two trailers in two weeks in a row crossing the scale with the same problem ... That'll do it, he said. "You can consider it preventive. Downtime prevention – when you’re talking $200 per trailer to do this, it's a pretty cheap way of making sure everything’s good there." After all, each violation set him back $400 in the brake-adjustment fee from the roadside techs, then "Oklahoma sends you a $250 fine. You're talking, what, $600-$800 by the time you’re done." Not to mention the time lost, as intimated.
[Related: Why it's usually a bad idea to rely on manual adjustment of automatic slack adjusters]
Malion and Stoll both underscored an OTR reality when it comes to automatic slack adjuster maintenance that both felt too many just don't realize. You can download a briefing paper from Spectra Products on the basics of that reality via this link. At the core is that drum bakes' automatic slack adjusters (ASAs) "calibrate with full brake applications" as they wear, Malion said. Yet full brake applications aren't exactly a common feature of OTR driving (anyone who's been cut off recently may beg to differ).
From Malion's briefing paper:
Most drivers usually apply the brakes with 10%-20% air applications under normal driving conditions. ASAs are designed to compensate for wear and adjust with full brake applications to cause the ratchet to roll over to the next peg. As the brakes wear naturally, the ASAs are not compensating for the wear without full brake applications.
Stoll referenced basic checks any driver can and ought to do routinely -- regular readers probably know it already as a way to test the alarm for low air. "When you start the truck," Stoll said, "build to 120 psi. When you’re full of air," repeatedly apply the brakes, "bringing your air tanks down to set off your alarms."
The briefing paper offers a more detailed outline:
Brake experts recommend that as part of the driver's pre-trip inspection the driver should make a minimum of 6 full brake applications with at least 90 psi. ... The pressure may drop after a few full brake applications, so charge the system back to 90 psi or above and complete the last full brake applications. Do not pump the brakes, [rather] apply a full brake application, then release and repeat the procedure. These 6-12 full brake applications should ensure that your ASA is adjusting.
"Most people don’t do that on a daily basis," Stoll wagered, and if they don't, "slack adjusters aren’t being calibrated." They hit the I-35 southbound scale in Oklahoma, "pull in, and they're getting brake adjustment violations. ... Nobody seems to teach drivers how to properly handle automatic slack adjusters. A driver should do that every day."
If the other parts of the ASA and brake system are working, right, then, the Brake Safe indicator should tell you you're good to go. It can also, Malion and Stoll noted, be used as a diagnostic tool when certain parts are in need of attention.
Malion spelled out several ways to read the red indicator's position in such a manner in the video that follows. You can find more via the Spectra website.