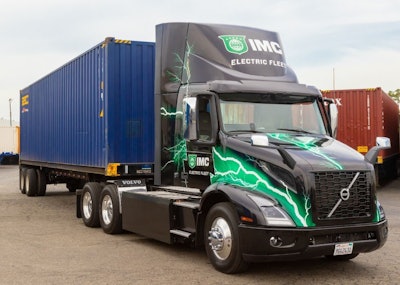
If it feels like everything you read about on-the-ground, real-world implementation of electric-drive Class 8 trucks stems from an operation working the ports in California, that's no accident. The California Air Resources Board's "Advanced Clean Fleets" regulation's most aggressive deadline requires fleets with trucks working the state's ports to register those units with CARB before the end of this year. As of the beginning of 2024, CARB mandates any new truck added to the registry for port work be a so-called "zero emissions" unit (ZEV).
Most of what qualifies and is available today is in the solely battery electric realm, though sizable port drayage provider IMC and its Pacific Drayage Services unit out West has ordered 20 Nikola hydrogen fuel cell-electric trucks that would fit the bill, too, with potentially more than twice the range. Yet, speaking in September, IMC President Jim Gillis hadn't seen a single order deliver as yet.
He said he knew of other fleets sitting on big battery electric orders themselves with no clear timetable for the rigs' delivery.
"Who knows, right? I think we’ll get two or three" this quarter at least, he hoped for those hydrogen trucks.
Uncertainty about how CARB's drayage reg plays out on the ground is high for other reasons, too. The California Trucking Association recently filed suit in federal court taking aim at the ACF broadly, alleging state overreach and violations of both the Clean Air Act and the Federal Aviation Administration Authorization Act, which prohibits state regulation from impacting various aspects of interstate operations inside and outside the state's borders. Whether the district court might act to enjoin CARB from enforcing the fast-approaching dray-registry deadline is unknown.
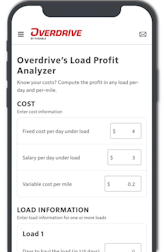
Regardless, fleets of all sizes have simply moved ahead, whether dipping their toes into battery electric with a few trucks or, like IMC, doing that but also placing big diesel orders in efforts to beat the end-of-year deadline for new diesel units in the registry. Sensing huge opportunity with a fast ZEV transition in the ports, too, other companies have jumped into the game on the charging-infrastructure side, as detailed in the previous part of this series in conversation with the Forum Mobility startup.
If there's anywhere a Class 8 electric tractor has the potential to excel, it's short-run port drayage. CARB itself notes its ACF rule specifically seeks to speed along a transition to ZEVs with in-use-trucks regulations for fleets "well suited for electrification," while placing later deadlines on vehicle manufacturers' sales. Yet early adopters of battery electrics struggle to balance the need for sometimes lengthy charging time during a workday with the need for production -- and adequate driver pay.
[Related: CARB's aggressive ZEV deadline backfiring at the ports?]
Electric juice worth the squeeze in drayage?
ACT Research Vice President Steve Tam said his company has performed "three rounds of multiclient studies working on what kind of adoption of electric trucks we're going to see," he said. Fleets and owner-operators "tend to be cost-driven" -- specifically, total-cost-of-ownership driven -- when it comes to equipment decision-making.
For Class 8 battery electric trucks, Tam and company through those analyses found just two operational niches where total cost of ownership is generally better for an electric unit versus a traditional diesel powered truck. One was refuse hauling, mostly done in straight trucks with refuse bodies. The other? Port drayage with electric tractors.
On the front lines of battery electric adoption, it's not as simple as plug in, charge up and go, though.
Ariel Ramos, operator with IMC in one of the company's six Volvo VNR Electric tractors doing container drays daily from Los Angeles-area ports, detailed a variety of kinks he's been working through with IMC's Southern California team.
His days at work for the company at once "haven't changed much," he said. "If I have a very good day, I’ll do probably six moves," picking either a loaded or empty container from the port, and hauling "to the customers or to the yard," or another location within fairly close range.
"The farthest that we go," Ramos said, is to a customer approximately 50-55 miles distant from the port in Rancho Cucamonga, a 100-plus-mile round trip that might find Ramos utilizing a charging complex of the WattEV company at the Long Beach port to top off. The WattEV station, which opened this year, provides a bonus over another port-adjacent charging facility that Ramos said was capable of just about 13% charge in an hour, extending downtime within his day.
Ariel Ramos, pictured, did note a drawback of using port facilities for a charge is the necessity of being bobtail when you go into them. There have been times he's had to coordinate a drop location for a container with dispatch, for instance, just so he could get the VNR onto a charger. (At this link, catch an IMC video on Instagram of Ramos walking viewers through some of the details of his electric VNR on a company charger at their facility in Compton, California.)IMC
The company's invested in "battery on-board" charging equipment at its facility in Compton, California, Gillis said. Given the nature of those chargers, Ramos said his rig can pick up an initial 20%-40% of its full charge capacity in just an hour plugged in. The rate of charge drops off fast thereafter, though. "To get it fully charged," it can take between four and eight hours, he added, depending on what's left in the battery when he hits the yard at the end of a shift.
Gillis noted traditionally his dray operators are slip-seating their trucks in shifts, yet Ramos said that's not the case for the battery-electric he's in today, given the long charge times off-shift. And topping off mid-shift is a requirement on those good days he mentioned, with 6 moves of around 50 miles roundtrip, generally speaking, well more than exhausting the truck's range.
Ramos, paid hourly, doesn't sweat the added downtime much, yet Gillis emphasizes the drawbacks for drivers. In addition to that hourly rate, there's a production-related incentive on top of that in the pay package. Drivers are "losing production there" with all the charge time, he said. "It's something internally we're working on" to address -- just how to account for lost production in the pay structure.
[Related: Intermodal haulers fight off 'system collapse' at ports; Niche hauls]
Production-wise, the longer run to Rancho Cucamonga and back drains battery to the extent that it cuts a few hours of production time out of Ramos' typical shift, he said. Staying purely local, though, and using the quick initial-charge capabilities at the Compton yard, "that's where it's most efficient on my battery" and where he's able to produce to the fullest extent.
It's a different game, certainly, than filling up on diesel and watching the needle slowly move toward the empty mark. He points to subtle differences in power use. On a recent run to out to Rancho there was a big wreck that tied up traffic for miles and miles on the route there. Whereas normally that run at highway speeds might exhaust 40% worth of the battery's charge, this creeper run took forever, of course, but only took 20% of the battery to do it.
Knock on wood, he hasn't run fully out of power yet, he said. "I have a good dispatcher and we have good communication -- I try to talk to him when I’m running out." He's only triggered the vehicle's low-fuel warning once, he said, coming back into the yard with just 15% of power. "That’s about as far as I have dropped it."
[Related: A look at 'Topsy', Edison Motors' new diesel-electric vocational hybrid prototype]
E-trucks' performance characteristics: Sound, acceleration, wear
The second-generation Volvo VNR Electric Ramos works with "has the same features on the truck" as the prior diesel he was in, generally speaking. It's fully capable of "the same work."
The difference? If he's at a red light, his ability to accelerate in the flow of traffic is better. "If you want to pass another truck or change lanes" and need a boost of acceleration, "you can feel the difference," he said. There's "more power with the electric truck. But overall, as a professional, you've got to be careful with accelerating."
Volume and vibration, too, is considerably reduced in-cab compared to a diesel. Outside, too. Ramos now brings additional urgency to closely watching for foot traffic around the port sites where he picks up -- engaged dock workers may well not hear him approach the way they would with a diesel.
A worker at a load site recently mistook his engine for being off, for instance, as he sat waiting to unload.
Gillis noted all six of IMC's electric-truck drivers' experience in-cab has "been nothing but positive," as Ramos suggested.
"Fit and finish is pretty good" in the Volvos, Gillis said, and the VNR electric is "a good-driving truck -- anybody can get in these and drive them."
Yet there have been tradeoffs. "We've seen tremendous wear and tear on the super singles we run to save weight," Gillis said, noting he felt it had to be a result of added torque capability of the electric motor.
Maintenance-wise, too, IMC has seen a "couple of recalls" Gillis noted. "I'm concerned about the battery recalls" in particular with respect to safety-related issues. He pointed to a dramatic report of an electric rig that tangled with a locomotive in Carson, California. The battery burned for a couple of days before firefighters in the town could fully contain it. Overdrive readers are familiar with a somewhat similar, long-burning battery fire reported at the Nikola electric-truck maker's headquarters, ultimately prompting a recall.
[Related: It's official: Nikola truck fires prompt battery-electric recalls]
"The more you see that," Gillis predicted, "you’ll start to see some backlash with the insurance companies. When you first talk to these OEMs about buying electric, they all say return-on-investment is six years down the road.There's a bigger up-front cost, but over time they have less wear and tear, fewer moving parts." Given all the considerations, Gillis believe it "too early in the game to believe that to be true."
In a previous part of this series looking closely at the short-term drawbacks and tradeoffs, and long-term promise, of electric-drive trucks, Gillis put himself in the shoes of an owner-operator weighing costs and benefits, and concluded, "I’m not going to go buy these trucks off the shelves" in their present form.
From an operator's perspective, Ramos concurred, noting the production tradeoffs with so much time spent on a charger particularly. Whether or not you own the truck, in fact, "if you’re getting paid for production," common for owner-operators inside and out of drayage, "it’s not worth it for them," he said. "I have a couple of owner-operator friends that are paid for production." The time consumed for them searching for a station, or sitting on a charger, he feels would be simply "not worth it."
For a company operator like himself, staying strictly local, though, and paid for time worked, "you’re good to go," he said.
Read next: Known unknown: How the used market will develop for Class 8 electric trucks